Introduction
Atmospheric corrosion does not depend exclusively on the affected asset, since it develops under the influence of corrosive factors or agents present in the atmosphere. These factors are humidity, ambient temperature, wind, salinity, acid gases, suspended particles, among others. Consequently, corrosion in industry is accelerated by the presence of one or more commonly encountered adverse atmospheric conditions.
The interaction of materials with aggressive environments deteriorates structures and components in the oil industry; this increase in corrosion results from the exposure of surfaces to adverse atmospheric conditions which in the presence of air humidity form highly aggressive solutions. These corrosive agents not only increase the corrosion rate through electrochemical reactions on the surfaces, but also degrade the protective coatings designed to protect the materials.
The variation of the parameters of the atmospheric conditions, depending on the operating environment, act directly on the types of corrosion, affecting the useful life and reliability of the assets; therefore, it is important to evaluate their impact in order to apply the most appropriate methods for corrosion control under these conditions.
Classification of atmospheres
Several studies on atmospheric environments, from the point of view of corrosion engineering, have classified these environments according to their aggressiveness towards materials, taking into account the level of contamination and the geographical characteristics present. These zones are classified as follows:
- Rural: Unpolluted environments normally far from industrial sectors.
- Urban: Areas with low aggressive air pollution, usually from surrounding traffic.
- Industrial: Atmospheres with the presence of atmospheric pollution such as sulfur dioxide (SO2) from industrial plants and large volumes of traffic that form acidic condensates.
- Marine: Regions where there are windblown marine aerosols or mists containing chlorides, which pose risks of condensate concentration or evaporation of surface moisture.
Knowledge of the type of atmosphere is essential to specify the criteria to be considered in the selection of protective materials and coatings for the durability and reliability of structures in each specific environment, since atmospheric corrosivity depends on meteorological conditions and chemical parameters.
Influence of atmospheric conditions on corrosion processes.
Atmospheric conditions specifically define the type of atmosphere at a given place and time; while atmospheric corrosion refers to the deterioration process of materials, especially metals, due to their interaction with the surrounding environment; and depends on atmospheric factors such as: humidity, temperature, wind, concentration of pollutants in the air, solar radiation, among others.
It is important to point out that adverse atmospheric conditions do not only influence the corrosion of metals; but they do have a significant incidence mostly in industrialized and marine areas, where they are called industrial atmospheres, or in coastal regions where they are called marine atmospheres.
Characterizing the environmental severity of corrosive atmospheres in industrial environments is so important that it has led to the creation of specific maps that identify corrosion risks in geographic regions. These maps are used as tools to prevent corrosive effects in specific areas, facilitating the selection of corrosion resistant materials and the taking of appropriate protective measures.
Atmospheric conditions in Oil & Gas environments
In the oil sector there are several atmospheric conditions that have a significant impact on external corrosive processes, affecting the integrity and reliability of assets, from exploration and production to transportation, storage and refining. Industrial atmospheres are usually polluted due to high sulfur dioxide contents, this being one of the corrosive agents with the greatest influence on external corrosion processes.
In high-risk environments such as the oil industry, metal degradation creates safety, operational and environmental hazards. The main atmospheric conditions present in this sector are described below:
Humidity
The effect of air humidity on the corrosion of metals depends on the relative humidity. Critical factor favoring electrochemical corrosion in marine and industrial atmospheres. The condensation of moisture on metal surfaces facilitates the formation of electrochemical cells that accelerate the corrosion of metals. In offshore areas, the combination of moisture and salts (chlorides) increases the risk of pitting and crevice corrosion in stainless steel installations under stress.
Temperature
Temperature variations influence the atmospheric corrosion rate of metals. The speed of material deterioration tends to increase with higher temperature, being the most influential factor in oxidation corrosion. In cold environments, for example, the lower solubility of oxygen can reduce the corrosion rate, while in hot climates, corrosion of metals is accelerated due to increased electrochemical activity.
It has been shown that condensation on the metal surface is an important feature of the initial stage of atmospheric corrosion, and temperature changes cause this process. It follows that one of the key factors in the atmospheric corrosion of metals and alloys is the combined effect of temperature and humidity.
Atmospheric pollutants
Very common in oil environments and considerably influential in the corrosion of metals, they occur as noxious gases and solid particles. For example, atmospheres contaminated with high levels of sulfur dioxide (SO2) and nitrogen oxides (NOx) in the presence of moisture transform into strong acids and cause acid corrosion of metal structures.
Acid rains
It is a consequence of polluted atmospheres. Fuel gases react with water and oxygen vapor accelerating the corrosion of metals. There are a number of interactions between different corrosive agents on corrosion rate, some of which are directly associated with acid rains, such as chloride and sulfur dioxide acting on corrosion rate.
Wind speed and direction
Wind influences corrosive processes by transporting salt particles and contaminants to protected areas or areas not directly exposed to them. This generates an increase in the corrosion rate, and develops mostly in areas of difficult access, edges and high points where the particles are embedded and hidden.
Corrosive gases
In the oil industry, exposure to corrosive gases or vapors such asH2S(especially in processes with high sulfide content) can lead to hydrogen sulfide corrosion (acid aqueous). The corrosion of metals by the emission ofH2Svapors is particularly dangerous, causing the hydrogen embrittlement of metals and generating Stress Corrosion Cracking (SCC).
Environmental salinity
Chloride deposition refers to seawater salinity and does not include other possible sources of chloride. The presence of this chemical compound in marine atmospheres, such as offshore platforms or refining plants in coastal areas, accelerates the corrosion of metals. Chloride ions are aggressive, in aqueous media they combine with the hydrogen in water to form hydrochloric acid, damaging the passive oxide layers of metals and promoting pitting corrosion.
Ultraviolet radiation
Prolonged exposure to UV radiation from the sun degrades the protective coatings, exposing the protected material to corrosion. Although UV radiation does not cause corrosion, the degradation of material protection allows corrosion mechanisms to operate freely.
ISO 9223:2012 specifies the main factors affecting atmospheric corrosion of metals and alloys and deals with the complexities that exist between temperature-humidity, sulfur dioxide pollution and air salinity.
It is important to mention that atmospheric environments are a variable that is constantly changing with time and conditions. It is possible to foresee corrosion damage due to the influence of atmospheric corrosivity, but in several cases it is limited to the fact that the environment is a variable with constant changes over time.
Types of corrosion influenced by atmospheric conditions
Corrosion is described as the chemical or electrochemical process by which metals degrade in a specific environment. If the environment is contaminated, it will be more aggressive and accelerates the corrosive process. In the oil industry, the types of corrosion influenced by adverse atmospheric conditions include:
Corrosion of metals by carbon dioxide (CO2) and hydrogen sulphide (H2S), is produced due to gases or vapors that are released and create acidic environments, creating acid rains that affect the external part of the metals in contact, generating pitting and sometimes generalized corrosion; it is common in equipment located downstream from where the gases are emitted, in high points of refineries and in oil wells.
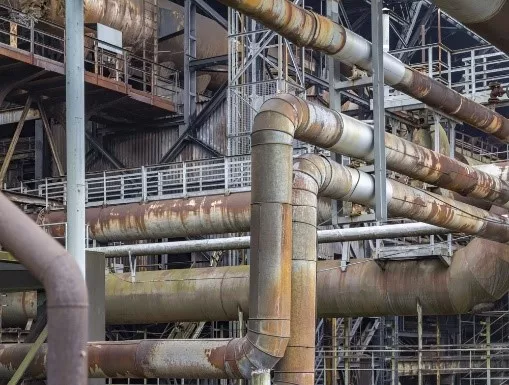
Chloride corrosion, present in infrastructures located in coastal and offshore areas. This phenomenon occurs due to the presence of sea salts, which are deposited on metal surfaces and, when combined with moisture, create a highly corrosive environment. Pitting corrosion is the most frequent and dangerous type of corrosion, occurring because chloride ions penetrate and aggressively damage the metal, even under protective coatings.
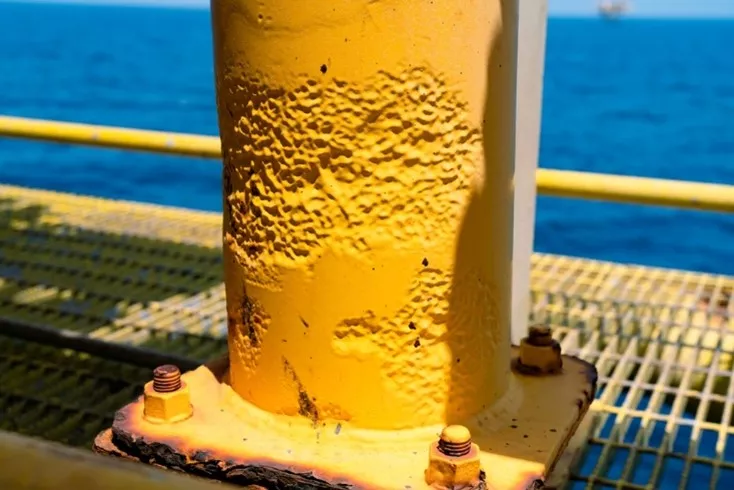
Stress Corrosion Cracking (SCC) is accelerated when the material is exposed to atmospheres with high humidity and presence of chemical contaminants (chlorides and sulfides). The combination of mechanical stress and a specific corrosive environment facilitates this type of corrosion, where cracks propagate at an accelerated rate in the material. Monitoring and control of these environmental conditions are essential to mitigate the risk of SCC.
Galvanic corrosion, which is influenced by environmental conditions, since factors such as humidity, presence of salts and atmospheric contamination increase the electrical conductivity of the environment, facilitating the transfer of electrons between different metals in contact, which accelerates the corrosive process. Galvanic corrosion is more severe in high humidity and saline environments, where these factors act as electrolytes, intensifying the electrochemical reaction between metals.
Corrosion under insulation is affected by temperature fluctuations in operational cycles which, together with the presence of humidity, leads to water condensation under the insulation of pipes and equipment; this creates an environment conducive to electrochemical corrosion, especially in installations with humid and polluted atmospheres.
Microbial corrosion, which is not really a type of corrosion; it is a phenomenon that facilitates the development of other types of corrosion. It mostly affects marine structures by altering surface chemistry and promoting pitting corrosion in environments rich in microorganisms. Sulfate-reducing bacteria and acid-producing bacteria metabolize compounds in the water, producing corrosive by-products such as hydrogen sulfide. This phenomenon affects the integrity of ship hulls, oil platform structures and other marine infrastructure.
The types of corrosion, which are influenced by the adverse atmospheric conditions of a specific operating environment, vary by location and operations, externally affecting structures, pipelines, and associated equipment.
Atmospheric corrosion control strategies
To combat the effects of adverse atmospheric conditions on corrosion processes, the oil industry implements multiple strategies, the use of corrosion resistant alloys, the application of coatings and paints that effectively repel corrosive agents, and the implementation of cathodic protection systems are fundamental practices. In addition, continuous monitoring of environmental conditions and regular inspection of assets can identify signs of deterioration, ensuring timely interventions to mitigate corrosion in the oil industry.
A detailed understanding of how adverse atmospheric conditions specific to each operating environment affect or accelerate corrosive processes in the petroleum industry is critical to the development of effective strategies to predict and control corrosion, thus ensuring asset integrity and reliability.
Conclusion
Atmospheric conditions, such as humidity and temperature, can accelerate or slow down the corrosion of metals used in industry. Controlling these conditions is essential to extend equipment life and ensure operational safety. Strategies such as the use of protective coatings and the selection of appropriate materials are significant in minimizing maintenance costs.
References
Own source