As the IoT and corrosion monitoring expands in different sectors, its role in preventing this phenomenon becomes more and more relevant. In today’s digital age, the Internet of Things (IoT) has revolutionized the way we interact with the world around us. This concept refers to the interconnection of everyday devices through the internet, allowing them to communicate and share data with each other.
Corrosion is a natural and costly phenomenon that affects various materials, from metals to civil structures. It is particularly problematic in industries such as oil and petrochemicals, where exposure to corrosive environments can cause significant damage to equipment and pipelines, compromising asset integrity and operational safety.
Traditionally, corrosion monitoring has been based on periodic and manual techniques, which implies limited and reactive supervision. However, thanks to IoT, it is now possible to obtain a constant and detailed view of the state of assets, allowing early detection of corrosion and, consequently, more efficient management of resources and a reduction in associated costs.
The key to real-time corrosion monitoring lies in the collection and transmission of accurate and reliable data. This is where the IoT shows its true potential. Through specialized sensors, it is possible to capture information on relevant variables, such as temperature, humidity, pressure and concentration of corrosive substances. These sensors are strategically installed on the assets to be monitored and communicate with a central platform through wireless connections, such as Wi-Fi or Bluetooth.
Profits
The transmission of data in real time allows experts to access up-to-date information on the condition of the assets, which provides the opportunity to take proactive measures to prevent and mitigate the effects of corrosion. In addition, the IoT’s ability to analyze large volumes of data in real time enables the identification of patterns and the generation of early warnings in the event of significant changes in corrosion conditions.
This provides a competitive advantage to the affected industries, while ensuring greater safety and efficiency in their operations.
A highlight of the application of IoT in corrosion monitoring is its ability to improve decision making and maintenance planning. By having real-time data, managers can assess asset performance, identify trends, and plan maintenance interventions more accurately and efficiently. This allows you to avoid unplanned outages, optimize downtime and minimize associated costs.
Another important benefit of IoT in corrosion management is the possibility to implement predictive maintenance strategies. By continuously analyzing data in real time, machine learning algorithms can detect patterns and anomalies in corrosion behavior.
These predictive systems make it possible to predict the useful life of assets and determine the optimal time to carry out preventive maintenance activities. This further reduces operating costs, while ensuring the integrity and durability of the assets.
In addition to early detection and prevention of corrosion, the IoT also offers innovative solutions for continuous monitoring of the effectiveness of anti-corrosion coatings. Coatings are a key protective barrier used to prevent corrosion on different metal surfaces. However, over time, they can degrade and lose effectiveness.
By installing corrosion sensors in the coating, it is possible to monitor its status in real time, detect possible failures or areas of wear, and schedule maintenance or repair activities in a timely manner.
It is important to highlight that the successful implementation of IoT in corrosion monitoring requires a robust and secure infrastructure. Reliable connectivity, data protection and cybersecurity are fundamental aspects to guarantee the integrity and confidentiality of the information collected. Companies must invest in robust systems and security protocols to prevent any potential vulnerability.
Applied Examples: IoT and Corrosion Monitoring
Here are some examples of how IoT is being used for real-time corrosion monitoring:
- Sensors in oil and gas pipelines: In the oil industry, corrosion sensors are installed in pipelines to continuously monitor wall thickness and detect signs of corrosion. These sensors are connected to an IoT network that transmits the data in real time to a central platform, where experts can analyze the information and take preventive measures.
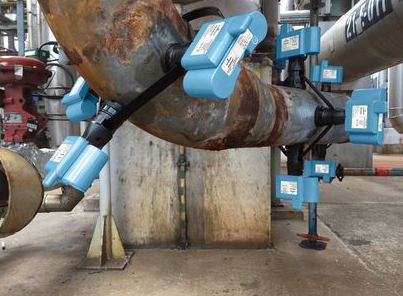
Wireless corrosion monitoring in pipelines
- Corrosion monitoring in marine structures: In structures such as oil rigs and docks, corrosion sensors are used that are strategically placed in areas exposed to salt water and other corrosive environments. These sensors transmit information about corrosion rate and coating quality via IoT, allowing constant monitoring and immediate response to any change in conditions.
- IoT technology can monitor and regulate the operation of offshore wind power turbines . It is a challenge to integrate these turbines so that they all work in these hard-to-reach places in the sea. The key to achieving this could be hidden in the latest advances in information and communication technologies, such as the Internet of Things.
- Monitoring Corrosion in Storage Tanks: Storage tanks used in the petrochemical industry can be subject to corrosion due to exposure to aggressive chemicals. IoT is used to install corrosion sensors on tank walls, allowing corrosion to be monitored in real time and preventative or maintenance measures to be taken when necessary.
- Corrosion monitoring on bridges and civil structures: Corrosion is a common threat to civil structures, such as bridges and buildings. The IoT is used to install corrosion sensors on these structures, which continuously monitor corrosion levels and alert to potential problems. This allows engineers and infrastructure managers to take timely measures to prevent further damage and ensure the safety of structures.
- Corrosion monitoring in industrial piping systems: The petrochemical and chemical industries often have complex piping systems that are exposed to corrosive substances. IoT is used to install corrosion sensors at critical points in pipelines, enabling constant monitoring of corrosion status and early detection of problems. This helps prevent leaks and costly damage to piping systems.
These are just a few examples of how the IoT is being used for real-time monitoring of corrosion in various industrial sectors. Thanks to the ability to collect and transmit data in real time, the IoT is significantly improving the way corrosion is addressed, enabling more efficient and proactive asset management.
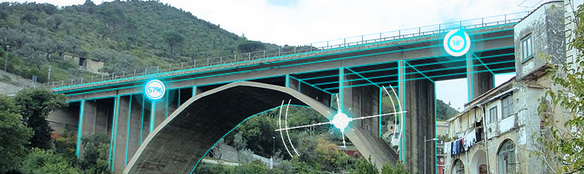
Companies that apply IoT-based systems in corrosion monitoring
Next, I will mention some outstanding companies in this field:
- Aegion Corporation: Aegion is a leading provider of infrastructure protection and rehabilitation services, including IoT-based corrosion monitoring systems. They offer integral solutions for the detection and prevention of corrosion in sectors such as oil and gas, water and energy.
- Corrpro Companies Inc.: Corrpro is a company specialized in cathodic protection and corrosion monitoring. They use IoT technology to implement real-time monitoring systems that help prevent and mitigate the effects of corrosion in different industries, including oil, gas, chemical, and water.
- Honeywell International Inc.: Honeywell is a global company that provides technology solutions in various industries, including IoT-based corrosion monitoring. Their approach includes the installation of corrosion sensors and the transmission of data through their IoT platform for constant monitoring and early detection of corrosion.
- Emerson Electric Co.: Emerson is a technology and services company that provides solutions for various industrial sectors, including corrosion monitoring. Through their industrial automation division, they offer IoT-based real-time monitoring solutions, using sensors and data analysis platforms for corrosion detection and prevention.
- OSIsoft LLC: OSIsoft is a company specialized in managing industrial data in real time. They offer software solutions and services for IoT-based corrosion monitoring, enabling companies to collect, analyze and visualize corrosion-related data for more effective asset management and informed decision-making.
These are just some of the companies that are using IoT-based systems for corrosion monitoring. The field of IoT is constantly evolving, and more and more companies are adopting these technologies to improve corrosion management and ensure the integrity of their assets.
Limitations
While IoT-based systems for real-time corrosion monitoring offer numerous benefits, there are also some limitations worth mentioning. Some of the common limitations are:
- Cost: The implementation of IoT-based real-time monitoring systems can involve a significant investment. Sensor installation, connectivity infrastructure, data platform and maintenance require considerable financial resources. This can be an obstacle for some businesses, especially those with limited budgets.
- Power and battery life: Sensors used in IoT corrosion monitoring systems require power supply. Depending on the location and environmental conditions, it can be challenging to provide a constant power source for the sensors. Additionally, battery life may be limited, which may require frequent battery replacement and additional maintenance.
- Connectivity and range: Real-time data transmission requires reliable and stable connectivity. In complex or remote industrial environments, such as offshore platforms or hard-to-reach areas, network coverage can be challenging. This can affect the ability to consistently transmit real-time data and affect the quality and reliability of corrosion monitoring.
- Cybersecurity: Data protection and the security of IoT systems are critical concerns. The transmission of data in real time over wireless networks can pose cybersecurity risks. Systems must implement strong security measures, such as data encryption and authentication, to protect collected information from potential attacks or intrusions.
- Maintenance and Calibration: Sensors used in IoT corrosion monitoring systems require regular maintenance and calibration to ensure accurate measurements. This involves proper management of the sensors, including periodic calibration, replacement of faulty sensors, and ensuring that the data collected is reliable and accurate.
- It is important to keep these limitations in mind when implementing IoT-based corrosion monitoring systems. Despite these challenges, the potential benefits of real-time monitoring and early detection of corrosion often outweigh the limitations, enabling more efficient asset management and reduced costs associated with corrosion.
Conclusions
The Internet of Things is playing a fundamental role in real-time monitoring of corrosion. Thanks to the ability to constantly collect and transmit data, this tool allows a more efficient and proactive management of assets, preventing and detecting corrosion. This not only reduces operating costs and security risks, but also improves maintenance planning and extends asset life.
The IoT represents a promising alternative for the oil and petrochemical industries, providing an innovative technological solution to face the challenges of corrosion in an increasingly connected and digitized environment.
Sources: