Non-Destructive Testing (NDT) methods are used in the industry to assess the integrity and properties of materials or components without damaging the object under investigation. They are a fundamental instrument for the control of quality, safety and reliability of industrial facilities, help their Member States to train personnel in the application of technology and provide the necessary equipment.
Non-destructive tests can be carried out on any type of metallic material, as well as on its welds, its main applications being the construction of pressure vessels, petrochemical plants, power and nuclear power plants, the transport sector (tanks, railways, shipping industry) and civil works (metal structures and bridges).
Most outstanding consequences of not applying NDT
The consequences of not applying these tests in the oil industry can be serious and far-reaching, including:
- Pipeline failures: Difficult to detect corrosion, cracks and other defects, which can lead to pipeline failures and leaks.
- Environmental damage: Leaks in corroded pipelines can cause environmental damage, including soil and water contamination.
- Safety Hazards: Corroded pipelines can pose safety risks to workers and nearby residents.
- Increased Costs: If corrosion is not detected early, it can lead to increased maintenance costs and more frequent repairs.
- Non-compliance with regulations: The oil and gas industry is governed by various regulations, codes and laws, and NDT is often required to comply with these regulations.
Importance of NDTs in the oil industry
Some specific examples that highlight the importance of non-destructive testing (NDT) in the petroleum industry:
Pipelines are critical components of the infrastructure of the oil industry, transporting oil and gas over long distances. Corrosion is a common problem that can weaken pipelines and lead to leaks or failures.
Non-Destructive Testing techniques, such as ultrasonic testing and magnetic particle inspection, can detect corrosion and cracks, allowing timely repair or replacement to maintain the integrity of pipelines and prevent incidents such as oil spills or gas leaks.
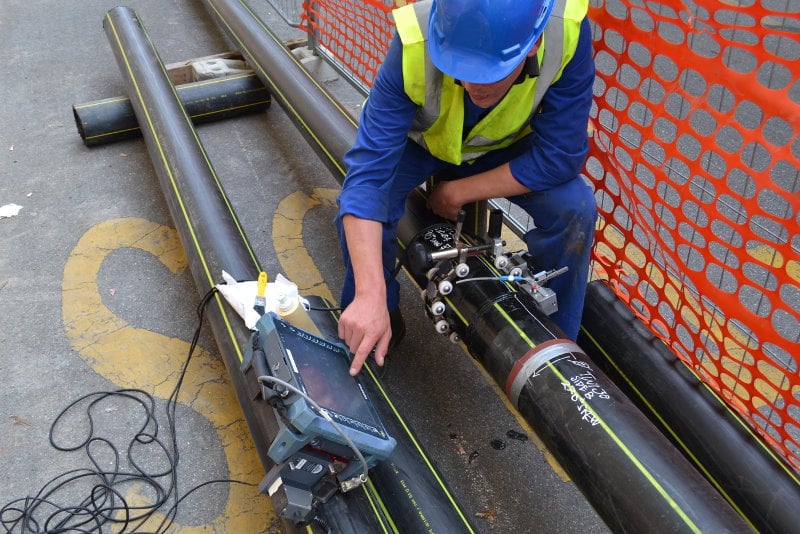
Pressure vessels are used to store and transport volatile substances in the oil industry. They are subjected to high pressure and temperature, so their structural integrity is crucial for safety.
Non-destructive testing methods, such as radiography and ultrasonic testing, can assess the condition of the vessel, identify defects or weaknesses in welds, and ensure compliance with safety regulations.
By detecting problems early, NDT helps prevent catastrophic failures that could lead to explosions or other dangerous incidents.
Oil storage tanks are susceptible to corrosion, especially when exposed to harsh environmental conditions or contain corrosive substances.
Without NDT, undetected failures can compromise the strength of the infrastructure and increase the risk of failure.
Preventing Environmental Damage: Corrosion or other defects in pipelines can lead to leaks and spills, resulting in environmental contamination, including soil and water contamination.
Non-destructive testing plays a vital role in early detection of such defects, allowing timely repair or replacement to prevent environmental damage.
Failure to implement ENDs can lead to significant environmental damage, negatively impacting ecosystems and communities.
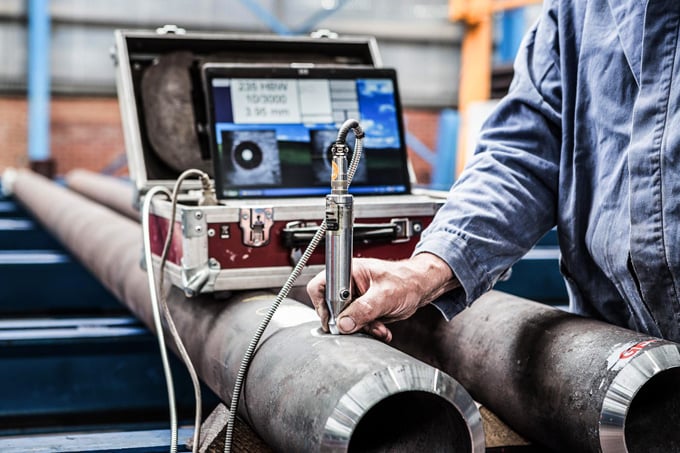
Cases of accidents due to failures and corrosion not detected
Undetected corrosion in oil and gas pipelines has caused several accidents in the past, some accident cases are listed below.
A gas pipeline explosion in San Bruno, California, in 2010 was caused by undetected corrosion and resulted in eight deaths, 58 injuries, and significant property damage.
An oil pipeline owned by the Plains All American Pipeline ruptured in Santa Barbara, California, in 2015, spilling more than 100,000 gallons of crude oil into the ocean. The spill was caused by external corrosion that had not been detected.
An oil pipeline owned by Colonial Pipeline exploded in Shelby County, Alabama, in 2016, killing one worker and injuring several. The explosion was caused by undetected corrosion.
Conclusion
These accidents demonstrate the importance of detecting corrosion in oil and gas pipelines. Using NDT techniques, companies can detect corrosion early and take corrective action to prevent pipeline failure, which can save them significant costs in the long run and prevent accidents that can cause significant property damage, injuries and deaths.
References
Non Destructive Testing for Oil and Gas Industry
https://www.ndt.net/search/docs.php3?id=20786
https://giiesas.com/servicio-ensayo-no-destructivo/
https://semmaq.com/ensayos-no-destructivos/