The oil and gas industry, with its complexity and dynamism, demands robust practices to ensure safe and efficient operations. In this context, comprehensive API inspection represents a fundamental pillar for asset management and maintenance of industrial facilities.
In this extensive article, we will discuss the crucial operational and security benefits that these comprehensive API inspections provide, from contextualizing them as the best way to understand the scope of the context, through their key steps, to preparing for future challenges.
Contextualization of the comprehensive API inspection
The history of API regulations dates back to the founding of the American Petroleum Institute (API) in 1919. From its earliest days, the API set out to establish standards for the oil and gas industry, recognizing the critical need to ensure safety, efficiency and reliability in a constantly evolving sector.
Over the decades, API regulations have undergone significant evolution, adapting to technological changes, lessons learned from industrial incidents, and the demands of an ever-growing industry.
In its early days, the API focused on basic safety and quality standards for equipment and operations. Over time, it expanded to address industry-specific challenges such as the inspection of pipelines, pressure vessels, and storage tanks. The increasing complexity of industrial operations and the need for uniform standards drove the constant evolution of API regulations into the comprehensive framework we know today.
Current relevance of comprehensive inspections in a dynamic industrial environment
In the current context of the oil and gas industry, characterized by technological advances, changes in energy priorities and greater environmental awareness, comprehensive inspections under the API regulations acquire even greater relevance.
Comprehensive inspections are essential to evaluate and ensure the integrity of critical equipment, resulting in safe and efficient operation. In a dynamic industrial environment, where innovation and efficiency are imperative, these inspections provide a roadmap for proactive asset management, helping facilities stay at the forefront of best practices and emerging technologies.
From this perspective, equipment inspectors must prepare to professionally take on this challenge; since they enter as protagonists in this script, so that the expected results are in accordance with the requirements of the standard and the client in question.
Key steps in a comprehensive API inspection
The API inspection process includes three stages: planning, execution and analysis.
Planning
- Scope identification: Clear definition of the equipment and systems to be inspected under API regulations.
- Document review: Evaluation of historical records, plans and relevant documentation to understand operational history and carry out effective planning.
- Programming and resources: Establishment of a schedule of inspections, allocation of resources and coordination with maintenance teams.
Execution
- Visual and non-destructive inspection: Visual evaluation of equipment followed by non-destructive testing as necessary.
- Sampling and analysis: Collection of samples for material analysis and laboratory testing.
- Detailed record: Comprehensive documentation of findings, measurements and any anomalies detected.
Analysis of results
- Condition Assessment: Interpretation of inspection results to determine the current condition of the equipment.
- Prioritization of actions: Classification of findings according to their severity and prioritization of corrective actions.
- Inspection report: Preparation of a detailed report that includes recommendations, actions taken and long-term projections.
Comprehensive inspection under API regulations involves deep and continuous interaction between various experts. Interdisciplinary work is essential to address the complexity of industrial facilities. Below are the main actors:
- Mechanical engineers: Provide knowledge of the structural integrity of pressure vessels and mechanical equipment.
- Process Engineers: Understand flows and processes, identifying critical areas in pipelines and associated systems.
- Corrosion inspectors: Specialized in the identification and evaluation of corrosion, especially relevant in storage tanks.
- Non-Destructive Testing (NDT) Technicians: They perform specific tests to evaluate the integrity of materials without damaging the equipment.
- Health and safety professionals: Ensure that inspection activities are carried out safely and in accordance with safety regulations.
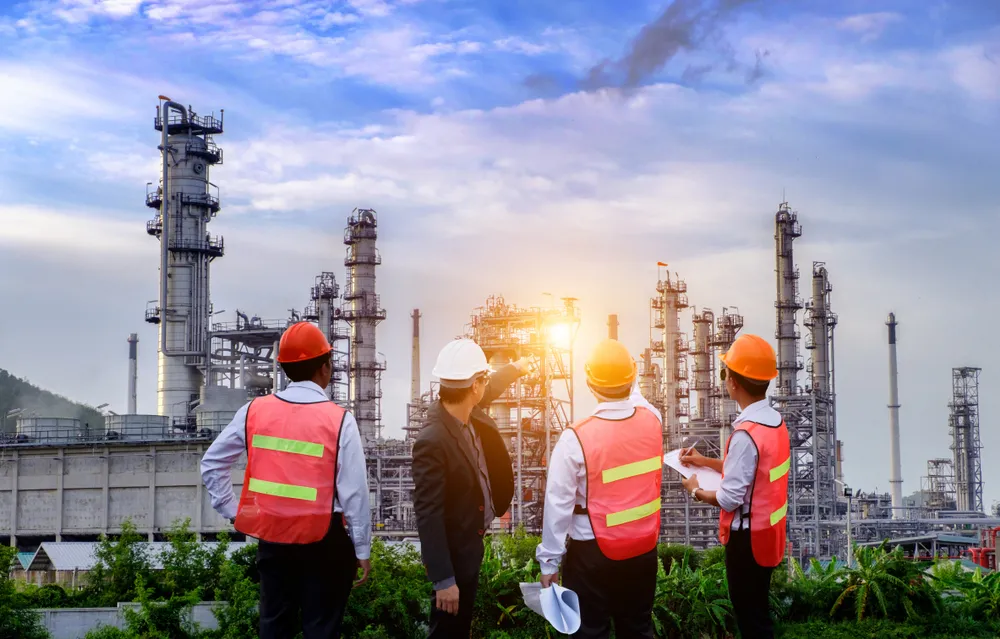
The collaboration between these professionals ensures a comprehensive evaluation of the facilities, addressing mechanical, chemical and safety aspects. Comprehensive inspection under API regulations is, therefore, a team effort where synergy between disciplines guarantees reliable and effective results.
Operational and security benefits
Operational safety is an undisputed priority in the oil and gas industry, and comprehensive API inspections play a crucial role in improving and strengthening this fundamental aspect.
The operational and safety benefits derived from early identification of risks during the inspection process are explored below.
- Wear and corrosion detection: Comprehensive inspections allow early identification of wear and corrosion in critical equipment such as pipes and pressure vessels . This early detection is essential to prevent catastrophic failures that could compromise worker safety and the integrity of the facility.
- Structural Defect Assessment: Thorough inspection against API standards, such as API 510 for pressure vessels, highlights the importance of assessing structural defects. The preventive identification of cracks, deformations or any other structural defect directly contributes to avoiding operational risk situations.
- Pipeline vulnerability analysis: Inspections according to API 570 allow detailed analysis of pipes, identifying vulnerabilities such as loss of thickness, internal and external corrosion. This information is essential to mitigate risks of leaks and possible explosions, safeguarding the safety of personnel and the environment.
- Prevention of leaks and spills: Early detection of possible leak points in storage tanks, supported by regulations such as API 653, is essential to prevent unplanned spills. Anticipating these problems contributes directly to operational safety and the minimization of environmental impacts.
- Mechanical Integrity Management: Rigorous assessment of mechanical integrity, as set out in API regulations, enables proactive asset management. Early identification of possible mechanical failures guarantees safe and continuous operation of equipment, avoiding accidents and unscheduled stops.
- Optimization of emergency protocols: The information derived from comprehensive inspections contributes to the optimization of emergency response protocols. Anticipating possible risk scenarios allows for effective preparation, improving response capacity in the event of critical situations.
- Improved safety culture: Regular implementation of comprehensive API inspections fosters a strong safety culture. Constant awareness of the importance of inspection and attention to detail in risk identification contribute to a safer and more aware work environment.
In summary, the operational and safety benefits derived from comprehensive inspections under API regulations are fundamental to the safeguarding of human life, the protection of the environment and the safe continuity of industrial operations. Early risk identification translates directly into proactive hazard mitigation, promoting a safe and efficient operating environment.
Confidence and preparation for the future
Taking as a fundamental reference the information collected during these inspections; A solid foundation is established for preparation for future challenges:
- Strategic Planning: Detailed information collected during comprehensive inspections provides a holistic view of the facility’s operational health. This information becomes a key asset for long-term strategic planning, allowing the company to anticipate and address future challenges.
- Innovation and adaptability: Early identification of trends or areas of improvement during comprehensive inspections facilitates continuous innovation and adaptation to changes in the industry. Companies that use the information collected can anticipate new technologies, regulations or market demands, maintaining a competitive advantage.
- Sustainable regulatory compliance: Information generated during comprehensive inspections enables sustainable regulatory compliance over time. By staying aware of changing regulations and continually adjusting operations accordingly, the company prepares for future regulatory challenges.
- Efficient asset management: Asset condition information collected during comprehensive inspections supports more effective management. Maintenance planning and informed decisions on repair, replacement or upgrade become critical to prolonging asset life and efficient resource management.
Taken together, the continued commitment to comprehensive inspections not only builds trust with various stakeholders, but also establishes a solid foundation for preparation for future challenges. The information collected becomes a strategic asset that drives informed decision making and long-term sustainability of industrial operations.
Conclusions
Comprehensive inspections under API regulations are not simply a regulatory obligation, but a strategic pillar for sustainable success in the oil and gas industry.
The adoption of these practices by companies not only guarantees their compliance with rigorous standards, but also builds a path towards a future where safety, efficiency and sustainability converge in an unbreakable synergy.
Let’s start this transformation today!
References
Own source