Corrosion is one of the biggest problems at the industrial level, generating innumerable economic losses, due to the deterioration of metallic materials, affecting their physical properties.
In the case of the naval industry, the problem grows exponentially, since the materials are subject to high levels of corrosion due to continuous exposure to seawater, the naturally corrosive electrolyte. Its high salt content makes it behave like a corrosion pile. There are several types of corrosion, but the most common is galvanic or electrochemical. It occurs when two metallic elements of different electrical potential are directly connected to each other with continuity in the presence of an electrolyte (PILA). In this way, an electrochemical process is generated with the creation of an electric current that causes the corrosion of one of the two electrodes: the one that is composed of the “less noble” metal (that is, the one with higher electronegativity, anode) while the another, the cathode, is protected.
The factors that most affect the corrosion of marine vessels are salinity, temperature, oxygen content, chlorides, etc. The area of the ship most affected by corrosion will be the splash zone, since it is intermittently covered by a thin layer of water and is exposed to ambient oxygen.
As ships and platform structures age, they deteriorate through corrosion and fatigue. External deck corrosion has become a major concern for owners and operators.
Marine vessel deck plates and upper shore structures are constantly exposed to a highly corrosive environment (saline medium), not to mention various forms of mechanical actions. These erosion-corrosion mechanisms can weaken or drastically reduce the resistance capacity of the platform.
Also, considering the various forms of mechanical wear that act on them, it is not surprising that the covers need to be regularly repaired or replaced. These erosion corrosion mechanisms are important for structural strength considerations as they can drastically weaken the platform’s bearing capacity and create unexpected shutdowns in vessel/platform operation.
To avoid this type of damage, the most appropriate solutions include:
Total platform replacement.
Some of the conventional solutions to repair or restore the load-bearing capacity of a deck plate are replacement of the existing deck or welding of additional plates. Deck replacement allows the most corroded sections of the deck plates to be removed and replaced and replaced with new steel.
This solution guarantees a completely new platform with no total weight increase in the platform structure, but it is very expensive and time consuming.
In addition, removal of compromised deck plates would expose infrastructure and machinery below deck, which could include equipment from the emergency generator room and engine room. Such unprotected equipment, when exposed to the highly corrosive environment, can sustain significant damage, resulting in extended downtime.
Reinforce damaged covers.
Welding additional plates to reinforce damaged cover plates is generally the most widely used and recognized solution due to its low cost and quick response.
Since new boards can be installed in patches, repairs can be completed faster so platform operations are minimally affected. However, the solder typically forms a bond around the perimeter of the board and the substrate.
The unbonded area can become susceptible to crevice corrosion if the weld is not continuous but intermittent, allowing moisture penetration. Additionally, this solution requires hot work that is not always feasible or permitted in environments with flammable and explosive chemicals, as sparks and hot metal can travel in any direction and cause a potential fire and/or explosion.
Cold Bonding or cold welding.
The cold welding technique can be used to repair the deck plate of ships. This consists of the mechanical and polar union of chemical adhesives with different materials such as metals, plastics and rubbers. Over time these solutions have been improving their capabilities such as adhesion, compression and chemical resistance at different temperatures.
Profits
Cold bonding is used in conjunction with polymeric composites, which today are the most widely used products for this technique since it can offer benefits such as:
- Eliminates the risk of sparks or electrical hazards, will avoid the need for hot work permits.
- It can be applied on site, and is an alternative when traditional cutting and welding are restricted in explosive atmospheres.
- The adhesive used conforms to the irregular shapes of irregular areas, filling the hollow spaces between the surfaces.
- Eliminates the need for in-situ machining, stress relieving, or post-weld heat treatment.
- It is a friendly and ecological technique, it does not cause pollution to the environment.
The reinforcing metal plate and the weakened substrates are the adherent ones. The bonded metal plate reinforces the damaged substrate and restores its mechanical strength. Bonding agent is applied to the underside of the metal plate and weakened substrate before the two surfaces are bonded.
Application methods.
Compound Sandwich: A viscous adhesive product is used and applied against the profile of both surfaces, previously prepared to increase their roughness, allowing the union of both surfaces. then it is pressed firmly to expel the excess material and eliminate the entrapped air, figure 2.
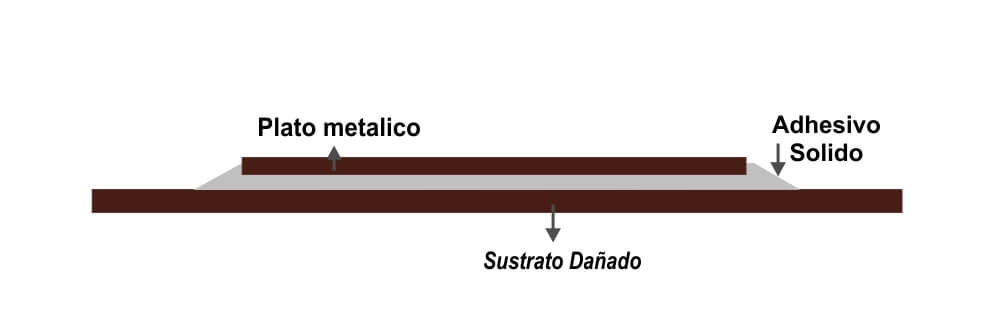
Injection: This method is applied to large surfaces. (eg 1m2 reinforcement plates), it may be necessary to inject fluid material through holes prepared for that purpose, which will ensure full contact between the two surfaces. In this case, a paste is used to seal the edges and the flowable material is injected. This flows from the corners inwards until it begins to exit through the ventilation holes, figure 3).
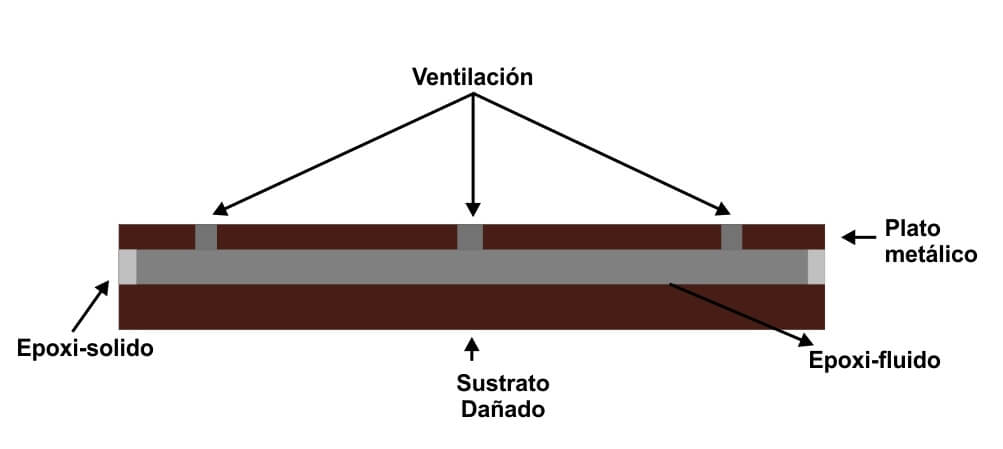
Conclusions
Cold welding is an alternative to heat welding. It is very versatile as it allows equipment or assets to be repaired on site, without heat and in an easy and safe way. Offering the best compromise between cost and performance compared to replacing the deck and welding additional plates to the deck. It is important to know the products for each cold weld, to ensure a use adjusted to the type of repair, with the aim of achieving the greatest resistance and the best finish.
Bibliographic references
- Nguyen, N. (2012). Micromixers: fundamentals, design and manufacturing. Oxford: Elsevier/William Andrew.
- Callister, W.D. (2007). Materials science and engineering: an introduction. New York: John Wiley & Sons.
- Campbell, FC (2007). Advanced composite manufacturing processes. Oxford: Elsevie.
Visit our website to read more articles https://inspenet.com/en/articles/