The heavy oil coking process in the oil and gas industry is important to
maximize the production of high-value by-products and to ensure the quality of coke production, but this process has been problematic due to its high environmental impact, particularly sulfur and nitrogen oxide emissions. This process is now subject to strict controls, but remains a significant source of pollution in developing countries.
Technological innovation has made it possible to design more advanced and sustainable methods, such as flexicoquization, a technique that combines the thermal disintegration of hydrocarbons with carbon gasification. Thus, achieving an efficient conversion of heavy fractions into useful products with a lower environmental impact.
This article provides detailed information on the delayed coking and flexicoking processes, the latter representing a breakthrough in coke production and in the reduction of environmental pollutants.
What is coking?
A process in petroleum refining used to convert heavy residues from distillation into higher-value products. This process is based on heating heavy oil residues until they reach their thermal cracking temperature. During this process, the long-chain hydrocarbon molecules are broken down, transforming them into coker gas oil and solid petroleum coke.
What is coke?
Coke is a by-product of crude oil that is generated during the cracking and polymerization processes in the delayed coking unit, either in a crude upgrader or in a refinery. It is the densest component of crude oil, which, when subjected to high temperatures and specific pressures in ovens and drums, is transformed into coke through the polymerization reaction.
The process is carried out in an operating unit called a Coker plant in the more complex refineries, in which the residual tarry material streams from the vacuum and atmospheric distillation units are transformed into high-value products and intermediates. These products include: liquefied petroleum gas, naphtha, diesel, and light and heavy gas oil. All important in different industrial applications.
Delayed coking process in refineries
This process, also known as Delayed Coking, is a process in the petroleum industry designed to maximize the value of heavy residues resulting from distillation units. This thermal cracking process converts these residues into higher value-added products, such as naphtha, liquefied petroleum gas (LPG), gas oils, and fuel gas, while producing residual coke as a by-product. The process consists of heating a heavy hydrocarbon in a furnace at high speed and then sending it to coke drums. Under specific pressure and temperature conditions, the hydrocarbon is thermally cracked, mainly into gas, naphtha, gas oils, and coke.
Description of the delayed coking process
The process begins with the heating of heavy hydrocarbons in a furnace. Once the thermal cracking temperature is reached, the heated stream is sent to the coke drums, where it is subjected to specific pressure and temperature conditions. Here, the hydrocarbon is thermally cracked, fragmenting the hydrocarbon molecules into lighter components such as gas, naphtha, and gas oils, while the coke is deposited in the drum.
The process consists of three stages: feeding, coking, and fractionation. Figure 1, shows the process by means of a flow diagram1.
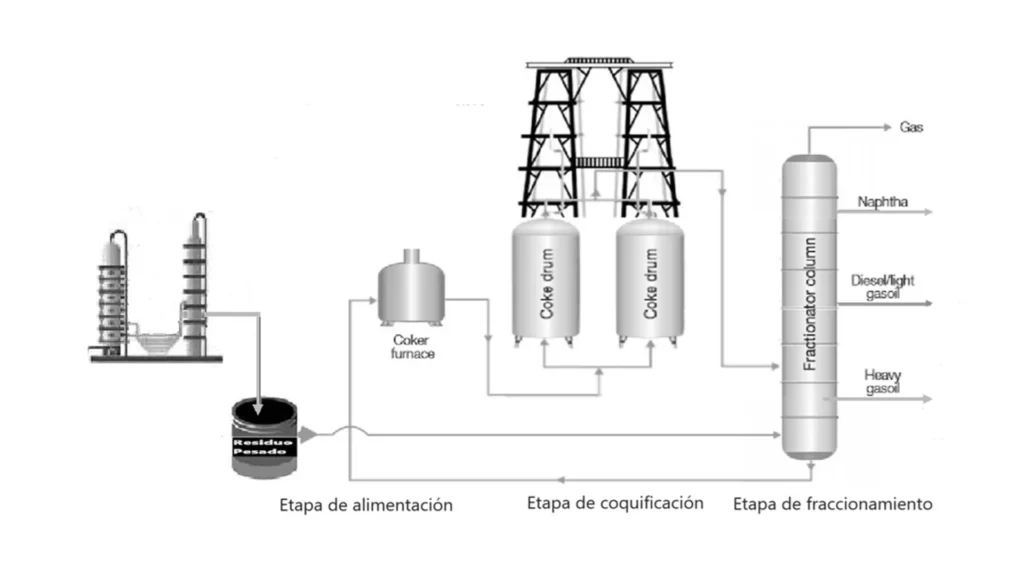
- Feeding stage: This stage focuses on ensuring a continuous supply of fresh charge to the furnaces. The vacuum residue, at a temperature of approximately 650°F and a gravity greater than 7°API, enters the bottom of the fractionating column. Here, it is combined with the fractionator recycle before being pumped to the furnaces. In the ovens, the mixture is rapidly heated to 940 °F, the temperature necessary to initiate coke formation in the drums.
- Coking stage: This section includes the ovens and coke drums. The role of the ovens is crucial, as they provide the heat necessary to start thermal cracking of the residue. To prevent cracking from occurring inside the ovens, which could cause operational blockages, steam is injected into the pipes, accelerating the passage of the residue into the drums. It is in the drums that the cracking reaction is completed and coke is produced by polymerization until the material reaches the ideal temperature in the drums.
- Fractionation stage: In this last stage, the different gas oil fractions are separated according to their boiling point. The vapors coming from the coke drums enter the fractionating column, where they encounter a spray nozzle system that condenses the heavier hydrocarbons. As the vapors rise, they condense according to their boiling temperature, allowing the physical separation of the different hydrocarbon fractions.
Flexicoking process: Advanced technology
The Flexicoking process is an advanced refining technology designed to maximize the conversion of heavy residues into more valuable products, such as liquids, gases, and flexigas. This process is distinguished by its ability to significantly improve efficiency in the utilization of crude residues, minimizing coke generation and producing a low calorific value gas that can be used as fuel in the refinery itself.
This technique significantly reduces waste, maximizing the use of the initial feed and generating high-value liquid products. In addition, it offers flexibility, orienting production towards gaseous or liquid products according to needs and responding to the hydrocarbon industry’s demand for more efficient and sustainable processes.
Flexicoking Process Description
This process incorporates a gasifier that converts part or all of the coke generated in the coker into synthesis gas through a reaction with air and steam. Customer coke particles are recirculated to the reactor to provide the necessary heat. The distilled products are sent to the fractionator, similar to the delayed coking process. The gas produced is cleaned and cooled, resulting in fuel gas usable in the refinery. This process allows the production of fluid coke or the total gasification of the coke to obtain only fuel gas. Figure 2 shows the flow diagram of this process2.
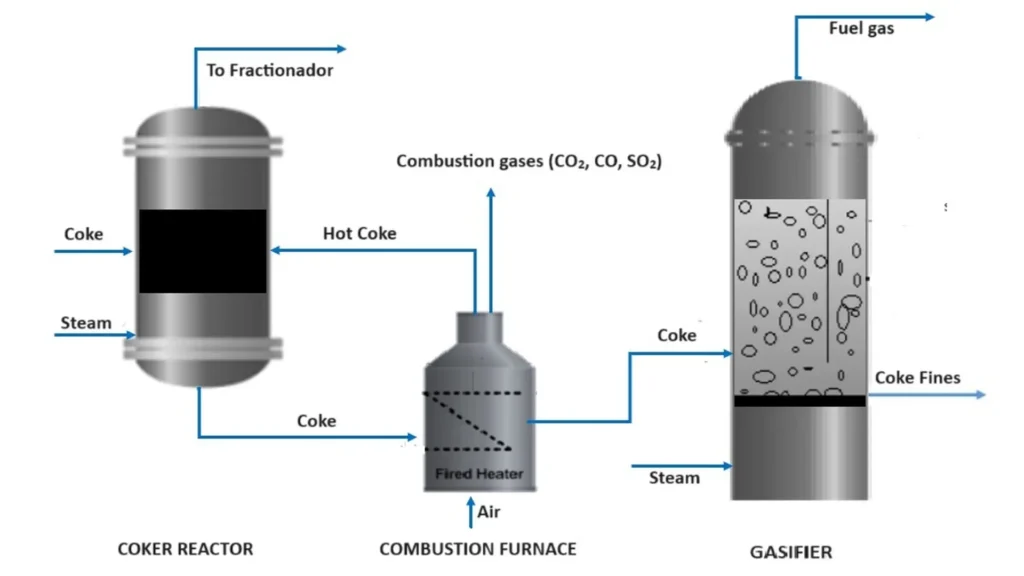
In the reactor, the waste is thermally cracked, generating a wide range of products, including gas and coke. The resulting coke circulates continuously between the reactor and the heater through transfer lines, where it is heated by the gasifying products. This cycle maintains the temperature necessary for the thermal cracking reaction.
Finally, the excess coke is transferred to the gasifier, where it reacts with air and steam to produce flexigas. This gas is then used as an energy source in the refinery, after undergoing particulate removal and desulfurization processes using FLEXSORB technology.
Why is the flexicooking process key in the coking of heavy crude oil?
Coke coking has historically been a process with a high environmental impact, mainly due to the emission of sulfur oxides (SO2) and nitrogen oxides (NOx) from the ovens. In developed countries such as Europe and the United States, only a few coke production plants continue to operate, under strict regulations that control emissions and waste. However, in many developing countries, this process represents a major source of pollution.
Due to the high world demand for coke, a series of stricter regulations have been implemented globally to control pollutant emissions. This is due to the fact that most of the plants lacked fume treatment systems, making it necessary to develop innovative solutions to modernize the coke production processes in order to comply with the regulations.
Under this context comes into play the addition of Flexicoking, an advanced technology that through gas scrubbing systems such as SOLVAir has proven to be highly efficient in the removal of pollutants such as SO2, NOx, and dust. This offers a viable solution to reduce the environmental impact of coking, with high efficiency in the conversion of products, without the need for long interruptions in production.
It is important to note that this technology was developed by Exxon in the 1970s. Combining thermal disintegration of hydrocarbons with carbon gasification and fluidized bed operation, achieving a high conversion of heavy crude fractions into more valuable products with less environmental impact.
The following video shows a detailed overview of the process; as well as, the associated benefits. It also explains how to set up and optimize Flexicoking facilities and how to use this technology to provide a cleaner and more efficient process. Source: ExxonMobil.
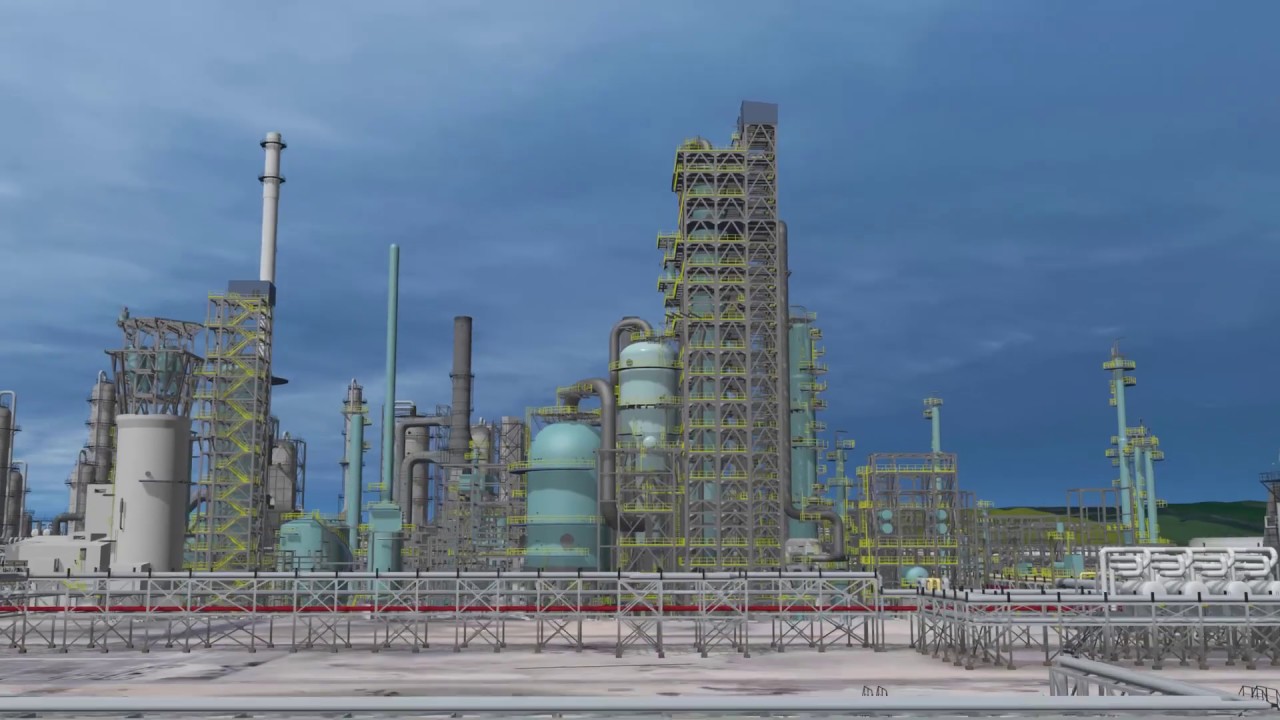
ExxonMobil Flexicoking Technology.
Conclusions
The future of coking coke depends to a large extent on the application of environmentally friendly technologies that preserve the health of mankind. The modernization of plants, the implementation of emission reduction systems, and the shift towards cleaner energy sources are crucial to ensure the viability of this industry in a world increasingly committed to environmental sustainability. The modernization of coke plants and the adoption of new technologies are essential to comply with environmental regulations and ensure the sustainability of this industry in the future.
Flexicoking technology provides an environmentally friendly technological solution for processing waste streams, meeting the growing market demand.
References
- Mendoza, German A; Mendoza Alonso,“ Flexicoking fundamentals and role in the hydrocarbon industry” academiaedu.
- J.P. Wauquier; El Refino del Petróleo; Ediciones Díaz de Santos, S.A, in Spanish, Published: March 18, 2024.