Table of Contents
- Introduction
- What is a butt joint weld?
- Types of butt weld joints
- Standard butt weld preparation process
- Butt joint welding techniques
- Most common industrial applications of butt joint welding
- Advantages and disadvantages of butt joint welding
- Factors influencing the quality of butt welds
- Conclusions
- References
Introduction
Butt joint welding is one of the best-known metal joining techniques in the metalworking and construction industry. It consists of joining two pieces of metal by aligning their edges and fusing them together to form a solid part. Although this process seems simple in concept, it requires detailed technical knowledge and precise execution to ensure the quality and strength of the joints.
In this article, we will review the various butt welding techniques, their industrial applications, advantages, disadvantages, and the factors that influence the quality of these welds.
What is a butt joint weld?
In butt joint welding, two pieces of metal are aligned and fused together at their ends in the same plane, with no overlap. This creates a continuous joint that is common in structural and pipe fabrication because of its simplicity and efficiency. Edge preparation, by beveling, directly influences the quality of the weld by facilitating a uniform fusion of the filler material.
To achieve a high-quality weld, the edges of the parts must be perfectly aligned and prepared, allowing for uniform fusion of the filler material across the joint. When properly executed, butt joint welding creates a strong, tough joint that is virtually undetectable to the naked eye. It is ideal for applications that require withstanding high loads and demanding conditions.
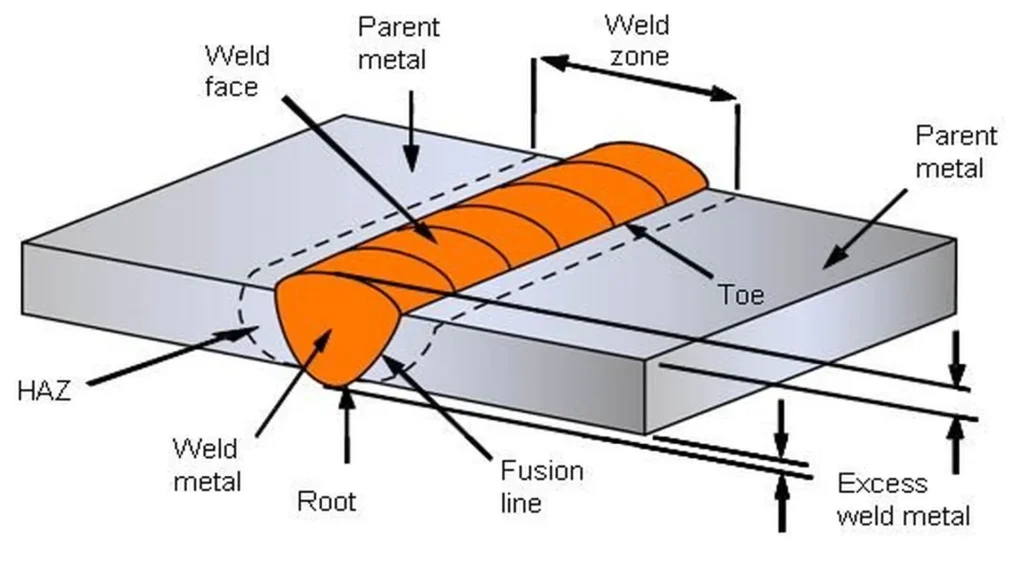
Types of butt weld joints
There are several configurations of butt joints, adapted to different applications. The main variants are described below:
According to bezel shape
- Square butt joint: This is the simplest option, where both edges are perpendicular to the surface of the parts. It is suitable for thin metals and applications with static stresses, but is not ideal for fatigue or impact conditions at low temperatures.
- Single bevel butt joint: One edge is beveled, while the other remains square. This design is suitable for medium thicknesses and allows partial penetration, ideal for parts of different thicknesses; it provides a stronger weld than the square joint.
- Double bevel butt joint: Both edges are beveled. Used for thick materials that require full penetration, providing greater strength on both sides of the joint.
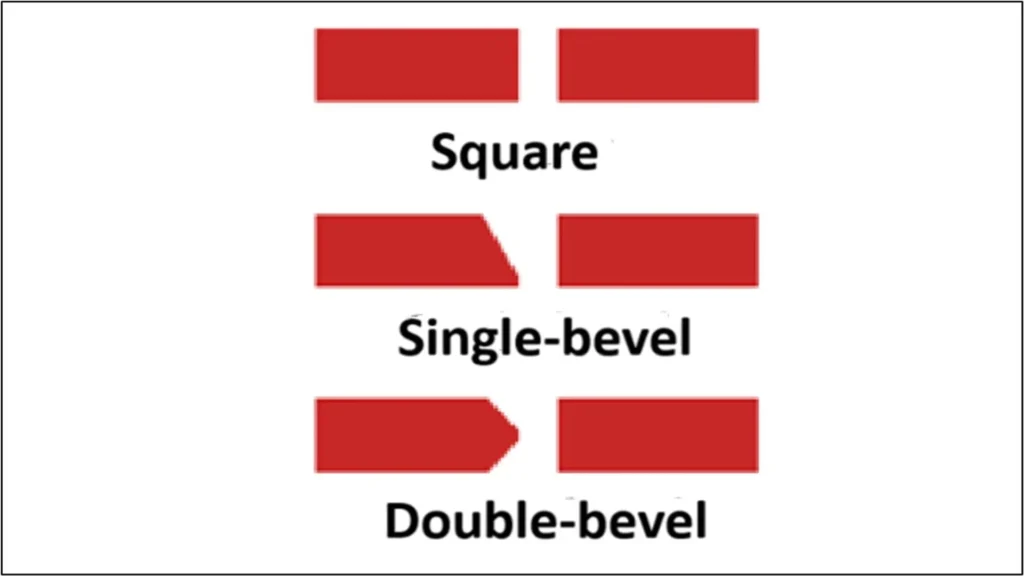
According to the shape of the slot
- Single V: Parts are beveled in a V-shape to facilitate deep weld penetration. It is suitable for materials between 3/8″ and ¾″ thick; these are static load-resistant welds, not recommended for fatigue or impact loads at the root of the weld.
- Double V: Both sides of the joint are beveled, making it ideal for thicknesses greater than ¾” and suitable for all loading conditions. It ensures full penetration but requires alternating weld beads to maintain symmetry and minimize deformation during the process.
- Single U: Used in high-quality welds, this configuration generates less deformation and requires less filler material than V-joints. Ideal for thicknesses between ½“ and ¾”, it is suitable for all loading conditions.
- Double U: This configuration, used for thicker metals, such as ¾” or larger, allows deep penetration with less filler material, making it ideal for heavy-duty applications in extreme conditions.
- Single J: One edge has a J-shaped bevel, which allows good penetration on one side and reduces material cost. It is suitable for moderate-load applications.
- Double J: Both edges have J-shaped bevels, which improves heat penetration and distribution. It is ideal for thicker materials requiring high structural performance.
The choice of the butt joint type depends on several factors such as the thickness of the parts, the material, the welding process used, the required mechanical properties and the applicable standards. One of the main factors in this process is the edge preparation, as it directly influences the strength and quality.

Standard butt weld preparation process
A detailed step-by-step process for the preparation of a butt weld is presented. Compliance with this process ensures a quality weld, with a strong and resistant joint:
- Cleaning: Removes any impurities (rust, grease, paint) from the surfaces to be joined. Manual or mechanical cleaning methods can be used.
- Material verification: Make sure that both the base material and the filler material are compatible and suitable for welding, this includes checking the mechanical and chemical properties.
- Edge preparation (beveling): Performs the necessary beveling on the edges of the parts to facilitate weld penetration.
- Fit and alignment: Place the pieces to be joined with the correct spacing and alignment. Edge spacing depends on the thickness of the sheet.
- Preliminary inspection: Visually check that everything complies with the requirements before starting the welding.
- Welding parameters: Correctly set parameters such as (current, voltage, speed) according to the process and materials.
- Preheating (if applicable): Preheat the parts if necessary to avoid stresses and cracks.
- Welding: Performs welding ensuring good penetration and fusion.
- Controlled cooling: For certain materials, gradual cooling is recommended to avoid internal stresses.
Final Inspection: Visually verify the quality of the weld and perform non-destructive tests (liquid penetrant, ultrasound, radiography) if necessary.
Butt joint welding techniques
Butt joints can be welded by various methods, such as arc welding, friction welding, and high-energy beam welding (e.g. laser or electron beam). These techniques are suitable for different materials and thicknesses, from thin sheets with minimal preparation (square butt joints) to thicker materials that require double beveling for better penetration.
Arc welding
Arc welding methods, such as SMAW, GMAW (MIG) and GTAW (TIG), are the most commonly used butt welding methods. They allow deep penetration and are ideal for joints requiring high strength and durability in different materials.
Friction stir welding
It is commonly used in butt joints. This process generates heat through mechanical friction, causing the materials to fuse without the need for external heat input. It is suitable for thicker materials and for joining dissimilar metals.
High-energy beam welding
Both electron beam welding and laser welding offer exceptional accuracy and localized heating. They are highly efficient and precise, ideal for applications requiring deep penetration joints, minimal deformation, and the risk of thermal damage to the base material.
Explosion welding
This technique is less common for butt joints, but is used to join dissimilar materials such as steel and titanium; in this process, an external pressure generated by a controlled explosion is applied. It is typically used to create corrosion-resistant bimetallic components.
Most common industrial applications of butt joint welding
This type of welding has a variety of industrial applications, among which the following stand out:
- Oil and gas: Used in the construction of offshore platforms, process pipelines, storage tanks, drilling rigs, spheres, and other industrial equipment, which must withstand high pressures and extreme environmental conditions.
- Energy and power: Applied in the manufacture of components such as boilers and turbines, ensuring structural integrity in power and nuclear plants.
- Aeronautics: Used to join aircraft structural components, where the joints must be light, but extremely strong to withstand the stresses of flight.
- Shipbuilding: It is used in the manufacture of ship hulls, internal structures, and on-board piping, where corrosion resistance is essential.
- Automotive industry: Used to manufacture car bodies, chassis, and exhaust systems, where high precision and resistance to vibrations and dynamic loads are required.
- Construction and fabrication: Used in the construction of buildings, bridges, railroads, and industrial machinery, which require welding that withstands high stresses and durability.
Advantages and disadvantages of butt joint welding
Butt joint welding offers several advantages, but it also has some disadvantages compared to other metal joining techniques. A detailed discussion follows:
Advantages
- High structural integrity and durability.
- Adaptability to different materials and thicknesses.
- Speed in production, especially in automated processes.
- Lower cost compared to other more complex techniques.
- Superior aesthetic finish, as it does not always require filler material.
Disadvantages
- It requires careful preparation of the edges, always taking care of the alignment.
- High technical skills are required from the welder and specialized equipment.
- Risk of deformation due to the heat concentrated in the process.
- Thickness limitations, for very thick materials, it is necessary to make multiple passes or use complementary techniques to ensure adequate penetration.
Factors influencing the quality of butt welds
The quality of a butt joint weld is influenced by several factors that must be controlled to ensure a strong, durable, and reliable joint. The following are the main elements that affect the final result:
- Edge preparation: Improper preparation, such as poorly made bevels, contaminated surfaces, or misalignment of parts, can result in poor fusion, increasing the risk of weld defects.
- Unsuitable base materials: The chemical composition and mechanical condition of the base materials affect their weldability. If unsuitable materials or materials with incompatible properties are chosen, weldability and joint strength are affected.
- Selection of the filler material: It must be compatible with the base metal to avoid defects such as cracks, porosity, or lack of fusion. In addition, it must meet the desired mechanical properties, such as corrosion resistance, ductility, and ability to withstand stresses.
- Temperature control: The heat control applied must be precise. Excessive heat can cause deformation or burn the base material, while insufficient temperature does not allow adequate penetration, resulting in a weak weld.
- Welder skill: The skill and experience of the welder are critical to the success of the weld. Technique and precision in handling the equipment ensure uniform penetration and good fusion of the materials.
- Environmental conditions: Factors such as humidity, wind, low temperatures, or contamination can negatively affect the process and bond quality. It is important to control the environment to minimize these impacts.
- Inspection and quality control: The implementation of non-destructive inspections (such as liquid penetrant, radiography, or ultrasound) before, during, and after the process is completed is essential to detect defects such as porosities, cracks, or inclusions that may compromise the strength of the joint.
Conclusions
Butt joint welding is an essential technique in various industries due to its ability to create strong and durable metal joints by fusing the ends of parts together. The welding techniques employed, such as arc, friction, and high-energy beam welding, offer adaptability to different materials and thicknesses and are especially valued for their precision and production efficiency.
Despite requiring high technical skill and specialized equipment, butt welding remains a preferred option due to its high structural integrity, making it an ideal solution for critical applications in sectors such as energy, automotive, and construction.
References
- https://www.mechdaily.com/types-of-welding-joints/
- https://www.twi-global.com/technical-knowledge/faqs/what-is-a-butt-weld