The professional welder is today an indispensable technical figure. Their role is fundamental in sectors where precision, traceability and structural integrity are non-negotiable. Have you ever wondered why welders with TIG, orbital or nuclear specialization lead the demand in today’s industrial landscape? The answer lies in the combination of recognized certifications, mastery of advanced processes and the ability to operate under international standards.
This article will guide you through the most valued specializations, their regulatory requirements and the impact they have on career, income and job opportunities. In addition, key welder certifications and technical pathways that transform a general operator into a highly skilled professional welder are outlined.
What is a profesional welder?
A professional welder is a qualified metal joining technician who starts his career mastering conventional processes such as SMAW or MIG. Their evolution requires continuous training, recognized welder certifications such as AWS, ASME or ISO, and mastery of advanced techniques such as TIG, laser, orbital or friction stir welding (FSW).
With knowledge of materials, joint preparation, operating parameters and quality control, the professional welder is prepared to perform in strategic sectors where traceability and structural integrity are critical requirements for operational safety.
Qualified or certified? Keys to being a professional
In the welding industry, it is not enough to know how to weld; employers require formal endorsement that the welder is qualified or certified, depending on the type of project.
- Being qualified: demonstrates that the welder can perform a procedure under the supervision of his or her employer, based on standards such as ASME IX, AWS D1.X or ISO 9606.
- Be certified: implies having been evaluated by an external accredited body, such as AWS, TWI or DVS, with international validity.
Certification is indispensable in highly regulated sectors such as nuclear, aerospace or industrial automation.
Welder certifications: The AWS endorsement
The welder certified by the American Welding Society (AWS) demonstrates technical competence under codes such as D1.1 (structural steel), D1.6 (stainless steel) or D17.1 (aeronautical) among many others. This credential, obtained through practical and theoretical examinations, is a global standard for industrial projects.
Obtaining AWS certification validates skills, and increases employability, professional mobility and access to highly complex projects.
Main specializations for welders
The starting point for a welding professional is usually that of a general welder, used in metal-mechanical workshops, light structures and general construction sites. Although this profile is functional and versatile, its field of action tends to be limited to conventional tasks, with few opportunities for growth and low technical evolution.
On the other hand, the welding world offers multiple technical specializations that allow the professional to develop in hierarchical sectors, to obtain higher incomes and to access high-level technological projects. Among the most outstanding specializations are those that require specific manual and technical skills, and those that focus on the mastery of advanced technologies and automation.
Specializations by process and skill
These specializations demand high manual dexterity, extensive knowledge of materials and the ability to work in complex environments or with very specific quality requirements.
1. TIG Welder (Gas Tungsten Arc Welding): The TIG welder is a specialist in high precision joining of critical materials such as aircraft aluminum, titanium and inconel, where maximum cleanliness, thermal control and uniform finish are required. He uses the GTAW process with argon gas as protection, in sectors such as aerospace, food, pharmaceutical and fine boilermaking, where tolerances are strict and regulatory requirements are high.
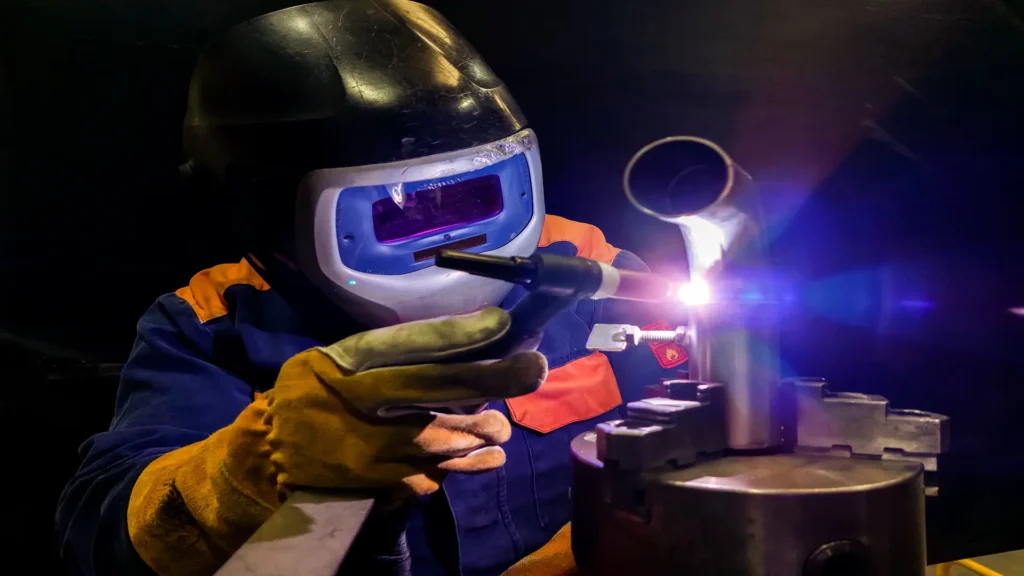
TIG welders must demonstrate consistency in bead quality, torch angle proficiency and thermal control. Their skill is honed with hands-on experience, technical courses and specific welder certifications such as AWS D17.1, ASME IX or ISO 9606-2.
The method is favored for critical joints where defects are not an option, such as aerospace or medical equipment manufacturing, which requires great manual skill and precise control of the arc and filler metal.
2. Pipe welder: The pipe welder is a specialist in the execution of welded joints for fluid conduction systems in operation; he can also work on boilers, honor, towers, exchangers, under certain conditions. His tasks include interpreting drawings, preparing components, identifying materials and applying WPS. He is proficient in positions such as 5G and 6G, and employs processes such as SMAW and GTAW.
Because of his proficiency in a wide variety of alloys and metallic materials, he is in high demand in pipelines, refineries, industrial plants and energy terminals, where compliance with standards such as API 1104, ASME Section IX or ISO 9606-1 is required. He collaborates with inspectors and NDT teams to ensure traceability, technical acceptance and operational continuity of the facilities. It is a career that is lived with vocation, because it tends to work long hours and demanding conditions, with high remuneration.
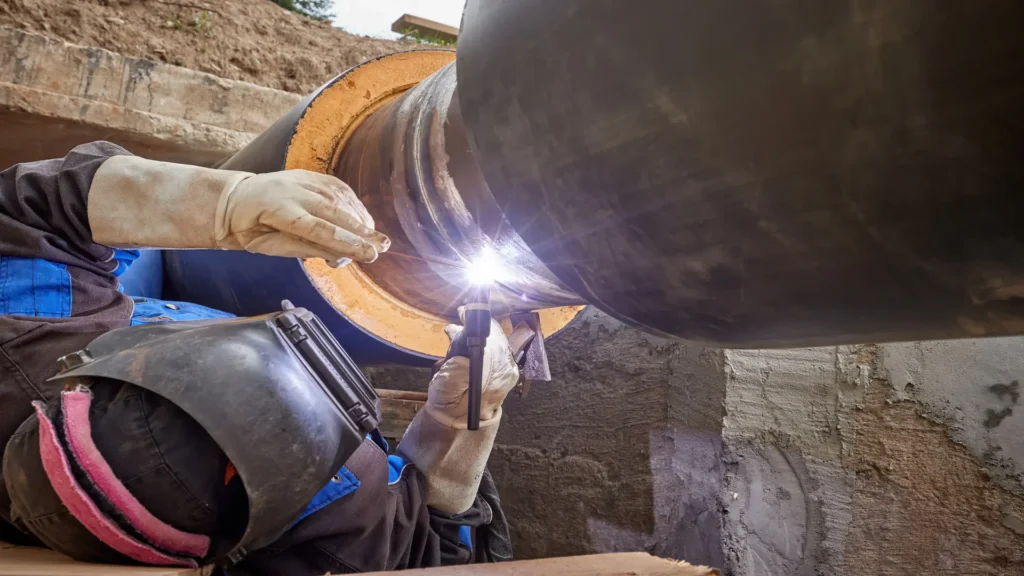
3. Underwater welder (Hyperbaric): This specialist combines structural welding skills with training as a certified commercial diver, endorsed by organizations such as ACDE or IMCA. To practice, they must pass a 6-12 month underwater welding course, physical exams and technical certifications. The work of an underwater welder is carried out in extreme underwater conditions, using processes such as SMAW or GMAW adapted to wet techniques or dry hyperbaric chambers.
He works on marine infrastructure projects, offshore platforms, shipyards and water works, where accuracy, physical strength and compliance with standards such as AWS D3.6M, IMCA or ISO 15618-1 are required. The financial trade-off is often high due to the technical complexity, operational risk and shortage of certified professionals.
4. Nuclear Welder: Nuclear welding requires welders specialized in joining components subjected to extreme conditions inside nuclear facilities. They master processes such as GTAW (TIG) and SMAW, applied on materials such as stainless steels, inconel and other superalloys. They work in pressurized systems, recirculation lines, containment or heat exchangers, where structural reliability is critical.
They operate under strict approved procedures according to standards such as ASME Section III, ASME IX, ISO 9606-1 and regulatory specifications from entities such as the NRC. They must qualify procedures through documented PQR and WPQ, pass radiographic tests and work under radiation safety protocols. Their profile is highly technical and in high demand in nuclear generation, maintenance and decommissioning projects.
5. Aeronautical/Aerospace Welder: The aeronautical or aerospace welder is qualified to join structural and precision components in aircraft, turbines, pressurized systems and space structures. He masters processes such as TIG, friction stir welding (FSW), laser and resistance spot welding, applied on materials such as aircraft aluminum, titanium and superalloys.
Its work requires dimensional accuracy, total cleanliness and compliance with millimeter tolerances. It operates under regulations such as AWS D17.1, NADCAP, FAA and internal standards of manufacturers such as Boeing or Airbus. It performs its functions in controlled areas, such as clean rooms or certified assembly lines, where visual quality, traceability and non-destructive testing are mandatory.
6. Submerged arc welding (SAW): Submerged arc welding (SAW) requires the welder to specialize in an automated or semi-automated process in which the electric arc is generated between a continuous wire and the base material, under a layer of granular flux that protects it from the environment. This process allows a high deposition rate, excellent weld quality and minimal fume emission, making it ideal for extensive and structural work.
The SAW profile masters the adjustment of parameters such as voltage, feed rate, flux flow and feed control in equipment mounted on automatic trolleys or production lines. It is useful in the fabrication of heavy structures, boilers, pressure vessels, wind towers and large pipelines. It operates under standards such as ASME Section IX, AWS A5.17 and ISO 9606-5, with technical requirements in positioning, continuity and penetration.
Process automation reduces the need for manual intervention and improves weld uniformity, making it a strategic profile in industries where efficiency and structural integrity are a priority.
Specializations by technology and automation
These specializations focus on the operation of advanced equipment, programming and integration of automated systems, strategic functions of Industry 4.0.
1. Orbital welder (automated GTAW): This specialist uses automated systems to execute precise circular joints in small diameter pipes, especially in stainless steels. It is indispensable in the pharmaceutical, biotechnology, semiconductor, food and nuclear industries, where repeatability, cleanliness and zero process contamination are required.
The orbital welding professional masters the use of programmable orbital equipment and parameters such as rotation speed, amperage and thermal control. He works in clean rooms or controlled environments, following standards such as ASME BPE, ISO 15614 and qualifications under ISO 9606 or equivalent. Its ability to deliver uniform welds without direct manual intervention makes it a strategic profile in the manufacture of high purity systems.
2. Laser or electron beam welder (LBW/EBW): The laser or electron beam welder performs high-precision joining of metal components using concentrated energy, without direct contact. Its work is considerable in sectors such as automotive, aerospace, microelectronics and medical devices, where deep, clean welds are required, with minimal thermally affected zone.
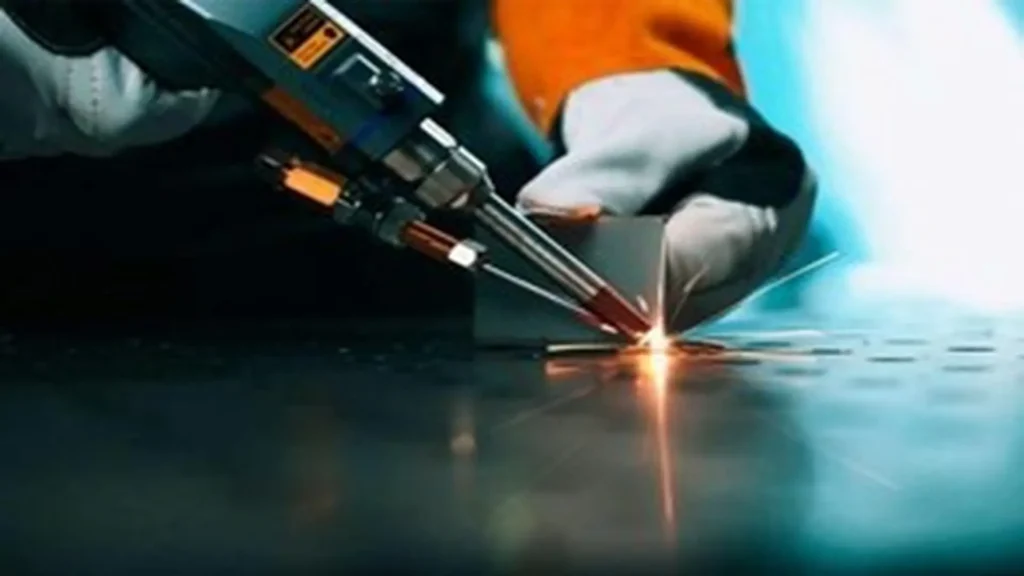
Operates CNC or robotic equipment, and adjusts parameters such as feed rate, beam power and focus. He works with complex materials, including special steels, aluminum and superalloys, under standards such as AWS C7.2, ISO 13919 or ISO 14744. This specialization requires advanced technical expertise, blueprint interpretation and rigorous dimensional quality control.
3. Friction Stir Welding (FSW) Specialist: The Friction Stir Welding (FSW) specialist masters a solid-state joining process, ideal for aluminum alloys, magnesium and dissimilar materials, without the need for fusion or external filler. Its profile is highly valued in the aerospace, naval and railway industries, where continuous welds are required, without solidification defects or thermal distortion.
He operates automated equipment with numerical control, adjusting variables such as axial force, feed and rotation speed. To qualify its procedures, it applies norms such as ISO 25239, ASME Section IX and standards specific to the aeronautical sector. Its work guarantees structural integrity with high energy efficiency and minimum subsequent intervention.
4. Robotic welder and cell integrator (Industry 4.0): This technical profile designs, programs and integrates automated welding cells with technologies such as laser, TIG, GMAW or hybrid, oriented to advanced manufacturing. It is not limited to a specific process, but masters CNC control platforms, artificial vision, intelligent sensors and collaborative robotics in production line.
He works in environments regulated by standards such as ISO 10218, AWS D16.4 and Industry 4.0 protocols, focused on traceability, repeatability and operational efficiency. His role is key in structural assembly lines, where cycle times and digital integration determine industrial competitiveness.
5. Certified Robotic Arc Welder (CRAW): The Certified Robotic Arc Welder (CRAW), a high-value credential awarded by the American Welding Society (AWS), specializes in the operation and optimization of robotic arc welding systems. His expertise extends to key processes such as GMAW and FCAW, pillars of modern manufacturing.
This professional goes beyond the simple execution of automated welding. His role includes programming, calibrating and adjusting critical parameters such as feed rate, arc path and thermal input. This meticulousness is essential to ensure consistent quality on highly repeatable production lines.
The CRAW certification validates its competence to operate in automated cells under rigorous standards such as AWS D16.4 and D1.1, making it an indispensable profile in automotive, aerospace, metalworking and precision manufacturing sectors.
With a three-year term, this certification requires constant renewal with practical updates, ensuring that the welder keeps his or her skills at the technological forefront. This profile uniquely combines technical knowledge in welding, robotics and quality assurance in high-performance production environments.
General or specialized welder?
A general welder executes conventional processes, but today’s market demands specialists capable of adapting to complex regulations and technologies
Advantages of specializing
- Higher pay: Specialized welders (e.g., submarine, nuclear, inspection) earn 15% to 50% more than a general welder.
- High employability: Workforce shortages and booming projects (energy, infrastructure, aerospace) multiply demand.
- Career at technical levels: You can advance to supervisor roles, AWS/CSWIP/CWI inspector or even trainer or consultant.
In contrast, a generalist profile may face
- Income cap: Without certifications or specialization, it is difficult to access critical projects.
- Less mobility: Limited to light work, industrial welding or repairs.
- Less professional growth: No flexibility to take on jobs that require standards or technical precision.
Why specialize?
Better income and stability: According to AWS, the average salary of a general welder is $50,000/year, while nuclear or aerospace welder profiles range from $70,000 to $110,000/year.
Global projection: A certified and specialized welder, with experience in piping, robots or aerospace, can work internationally. Standards (ASME, API, FAA) are shared global standards.
Scalable technical career: The evolution from operator to skilled technician allows for escalation to supervisor, trainer (TWI), CWI/CSWIP inspector or even automation consulting roles.
Impact on a welder’s career
The recommended progression path is usually:
- Apprentice/general welder: proficiency in SMAW, MIG, TIG.
- Pipe welder/specialized production: Proficiency in complicated positions, initial welder certifications.
- Initial certifications: Attainment of AWS D1.1/D1.6, ISO 9606.
- Vertical specialization: Focus on areas such as nuclear, submarine or aerospace.
- Technological specialization: Studies in robotics, AI or additive manufacturing.
- Technical leadership: Promotion to supervisor, CWI/CSWIP inspector, supervisor or trainer roles.
This path allows for articulated development based on technical skills and career aspirations.
Conclusions
Technical specializations allow the professional welder to transcend basic execution and become a highly qualified technical profile. From working in refineries and pipelines as a pipeline welder, to critical interventions under hyperbaric conditions as an underwater welder, certification and regulatory compliance define the standard of excellence.
Having internationally valid welding certifications increases employability, and enables participation in highly complex projects where traceability, accuracy and safety are mandatory. With multiple industrial sectors dominated by automation, energy efficiency and advanced materials, specialization is no longer an option, it is the path to a far-reaching technical career with global projection.
References
- https://www.indeed.com/viewjob?jk=eb275fd9a6a66e6c&tk=1ivq8rlmcg2nt88d&from=serp&vjs=3
- https://primeweld.com/blogs/news/10-best-jobs-for-welders-and-how-to-get-them
- https://es.indeed.com/orientacion-laboral/buscar-trabajo/como-ser-soldador-submarino