Table of Contents
- Introduction
- What is NDT inspection and how does it work?
- Common NDE inspection methods
- Criteria for selecting the appropriate NDE method according to industry type
- Advantages of NDE inspection
- Positive material identification
- NDE inspection implementation strategies
- Development of an NDE inspection program
- Conclusions
- References
Introduction
NDE inspection, also known as Non-Destructive Examination, is a set of techniques used to evaluate the integrity and properties of materials and components without causing damage or requiring disassembly. These methods allow a thorough inspection and measurement of various characteristics, ensuring the preservation of the tested object.
What is NDT inspection and how does it work?
Non-destructive evaluation (sometimes called non-destructive examination or NDE) is the process of using non-invasive procedures to inspect the condition of a material or measure a characteristic of an object without causing damage or disassembly of the asset. Remote visual inspection and most forms of visual inspection are technically different types of NDT. Using a wide variety of technologies, eddy current, fluorescent penetrant, flux leakage, magnetic particle, radiographic, thermographic, and ultrasonic are just a few of the different types of non-destructive evaluation (NDE) used in industry today.
NDE stands for non-destructive examination, while NDT stands for non-destructive testing. We perform an NDE/NDT inspection when it is necessary to examine something for safety, consistency, reliability or other problems without damaging it during the testing process.
This type of testing and inspection can also be used to detect failures or defects during the manufacture of new equipment, as well as to locate, identify, and quantify existing or process-related damage mechanisms.
Sometimes people use both terms interchangeably or lump them together because they are closely related. NDT is the general term for all the different types of tests available, while NDE measurements are more specific and quantitative.
Common NDE inspection methods
NDE inspection can locate flaws and imperfections in surface and subsurface materials. Different tests can analyze different components of a structure and can be applied at any stage of fabrication and construction. Ultimately, any material or product that fails testing due to a flaw or defect must be repaired or replaced to ensure its continued safety and integrity.
Visual inspection
Visual inspection is one of the most common non-destructive inspection methods used in industry. Visual inspection techniques are cost-effective, as they do not require expensive equipment and preparation time.
When performing visual tests, the inspector physically examines the area of interest. However, different tools are used to enhance or complement this inspection, such as borescopes, mirrors, weld and Pitt gauges and illuminators.
Phase array fault detection (PAUT)
This advanced NDE inspection method looks for and finds cracks and flaws. Inspectors also use it to inspect welds, measure thickness and monitor corrosion. Phased array ultrasonic system probes are used to send pulses through the material as a searchlight that highlights the size and location of any existing flaws.
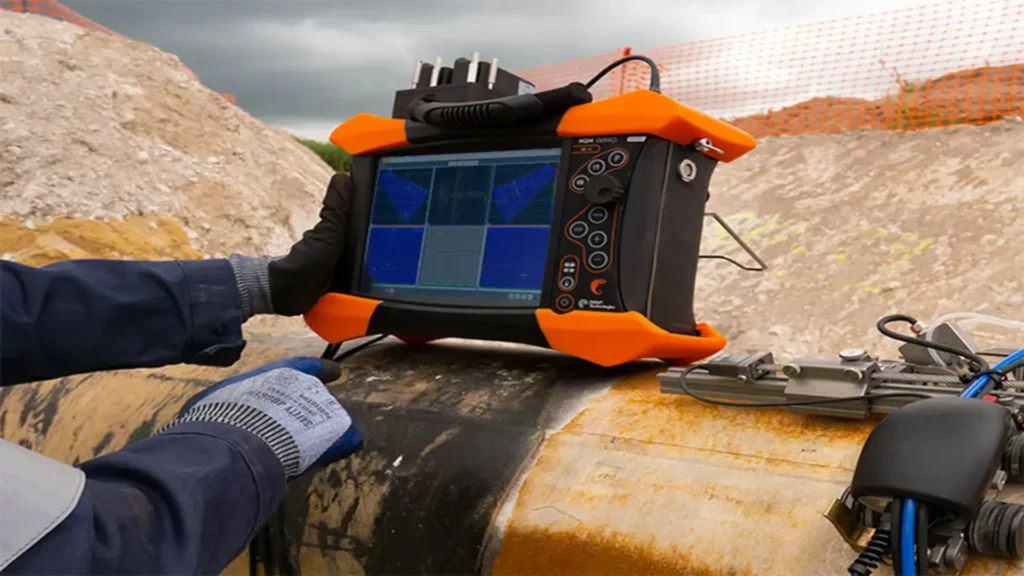
Ultrasonic shear wave flaw detection (UTSW)
Transverse waves have a shorter wavelength and lower velocity than other types of ultrasonic waves. Transverse wave ultrasound allows us to test angled areas to inspect welds and detect anomalies. Like phased-array ultrasound, it can be used to find cracks and defects in new construction or existing process equipment.
Bolt testing
Sometimes it is the little things that can become big dangers if left unchecked. Catastrophic failures have occurred due to poor management of bolted joints. Using advanced bolt inspection and testing techniques, we can evaluate bolts, shafts, and studs without having to remove them to check for corrosion or cracks.
Tube testing
Near field testing (NFT) is used to inspect the inside diameter of pipes. This inspection method is useful if damage is expected to occur on the tube side of the process. Using NFT it is possible to detect corrosion, erosion and pitting on the inside of ferromagnetic tubes.
Eddy current testing (ECT) is a versatile type of NDT inspection method that uses electromagnetic induction. Magnetic currents measure metal thickness, locate corrosion and identify small cracks.
Remote field testing (RFT) allows inspection of the thickness of ferromagnetic tubes. It can be useful to detect wall thinning and areas of corrosion, erosion and pitting on the inside diameter (ID) and outside diameter (OD) of the tubes.
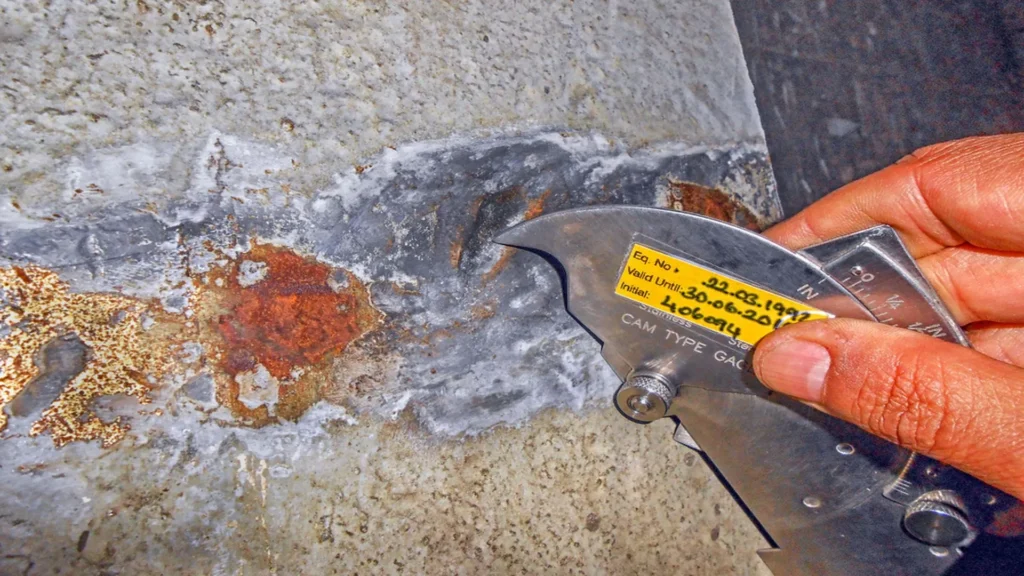
Criteria for selecting the appropriate NDE method according to industry type
NDE inspection is a critical aspect of any industry’s maintenance plans. By hiring qualified experts to determine the condition of your assets, you can ensure their long-term functionality.
Allowing corrosion or mechanical-related damage to accumulate in industrial machinery can decrease efficiency, undermine productivity, cause unplanned downtime, require costly repairs or even harm personnel. Reliable examinations by experienced inspectors like those at International Inspection provide clients with the information they need to maintain the well-being of their assets.
Advantages of NDE inspection
- Non-invasive: NDE techniques allow components to be examined without causing damage or requiring disassembly.
- Cost-effective: By detecting defects early, nondestructive inspection helps avoid costly failures and reduces downtime.
- Safety: Ensures the safety and reliability of critical components, avoiding accidents and improving operational safety.
- Versatility: Applicable to a wide range of materials and industries, from metals and composites to ceramics and plastics.
NDE inspection plays a crucial role in quality assurance, preventive maintenance, and the overall reliability of industrial operations. By leveraging advanced NDE techniques, industries can ensure the longevity and safety of their assets, while optimizing performance and reducing operational risks.
Positive material identification
Identifying the composition of components and materials is crucial in the inspection world. The mechanical integrity of assets depends on the use of the correct materials. Designs are built from calculations related to material strength.
Cracking and corrosion rates can change greatly and put equipment at risk of critical failure and jeopardize facility operations, not to mention lives and environmental impact. Positive material identification will provide a semi-quantitative alloy composition of an asset.
NDE inspection implementation strategies
- Create comprehensive training programs to educate inspectors and engineers on the proper use of NDE technologies.
- Clearly describe the benefits and limitations of different NDE methods from a practitioner’s perspective.
- Establish standardized practices for data collection, analysis, and defect visualization to ensure consistency.
- Include non-destructive testing services in regular inspection contracts or establish on-call contracts for specialized testing.
- Incorporate features in future infrastructure designs that make structures more suitable for nondestructive testing practices.
- Create customized equipment designs and automated inspection processes for complex or repetitive tasks.
- Apply advanced modeling and simulation techniques to improve nondestructive testing capabilities and interpretation.
- Integrate basic non-destructive testing measurements as a complement to standard visual inspections for fast field results.
- Employ flowcharts and decision matrices to help identify the most appropriate NDE methods for specific inspection needs.
Development of an NDE inspection program
To develop an effective non-destructive evaluation (NDE) inspection program, you can follow these comprehensive strategies:
Establish a clear framework
- Define objectives: Clearly describe the goals of your NDT program, such as improving safety, ensuring compliance, reducing downtime or improving product quality.
- Scope of inspection: Determine the types of assets and materials to be inspected and the specific NDT methods to be used.
Develop training programs
- Training tools and curricula: Create comprehensive training programs for inspectors and engineers. This should include both theoretical knowledge and hands-on training with NDE equipment.
- Certification: Ensure that all NDE technicians are certified according to relevant standards (e.g. ASNT certification) to maintain high inspection quality.
Implement best practices and standards
- Document the benefits and limitations: Clearly document the benefits and limitations of different NDE methods from a practitioner’s perspective.
- Standardized procedures: Establish standardized practices for data collection, analysis and defect visualization to ensure consistency and reliability of inspections.
Use advanced technology
- State-of-the-art equipment: Invest in advanced NDE technologies and equipment, such as phased-array ultrasound, industrial computed tomography (CT) and laser-based inspection systems.
- Automated systems: Develop and implement automated inspection systems for complex or repetitive tasks to increase efficiency and accuracy.
Perform cost-benefit analysis
- Economic evaluation tools: Develop tools to evaluate the cost-benefit ratio of implementing NDE techniques compared to traditional methods. This helps to justify the investment in NDE technology.
Conclusions
NDE/NDT inspection prevents airplanes from falling out of the sky, vehicles from causing fatal accidents, pipelines from exploding, bridges from collapsing, and refineries from experiencing critical failures.
These strategies can help industries implement NDE inspection techniques more effectively to improve safety, reduce costs, and increase the life of assets and critical components.
By following these strategies, you can develop a robust NDE inspection program that improves safety, reliability, and efficiency in your operations.
References
- https://en.wikipedia.org/wiki/Nondestructive_testing
- https://www.iinspect.com/nondestructive-evaluation/
- https://exoinc.com/blog/what-to-expect-from-your-nde-inspection