Table of Contents
- What is powder coating?
- How does powder coating work?
- Working principle of powder coating
- Batch systems: Features and benefits
- Powder coating process: Automation and control
- Intelligent data management for inspection and control
- Inspection and quality control technologies
- Energy optimization and sustainability
- The future of powder coating: AI and digitization
- Conclusions
- References
Powder coating has established itself as one of the most efficient, clean and sustainable techniques for the protection of metallic and industrial surfaces. Its ability to generate durable coatings, without the use of solvents and with low waste, makes it a mainstay of modern manufacturing processes.
Widely used in the automotive, appliance and infrastructure sectors, this process provides high corrosion resistance, excellent durability and consistent finishes. Batch systems in particular are ideal for small to medium production volumes, offering flexibility in part handling and finishing.
This article provides an expanded and updated look at what powder coating is, how it works, and how automation and control are transforming batch systems to meet today’s demands for quality, efficiency, and sustainability.
What is powder coating?
Is a dry finishing process that involves the application of finely ground particles of thermoplastic or thermosetting resins, together with pigments and additives, to a conductive surface, usually metallic. These particles are electrostatically charged and adhere to the part, which is then thermally cured to form a solid, uniform and resistant film.
Unlike liquid coatings, this process does not require solvents, which drastically reduces volatile organic compound (VOC) emissions, improves material transfer efficiency (up to 98%) and allows for the recovery of unbonded powder.
A batch powder coating system involves a set of equipment and processes designed to apply and cure on parts that are processed in single batches or small production volumes.
How does powder coating work?
The principle of operation is based on the electrostatic application of powders which, when negatively charged, adhere to grounded surfaces. The process involves five key steps:
- Surface preparation: Chemical or mechanical cleaning to ensure adhesion.
Powder application: With automatic or manual electrostatic guns. - Deposition: Powder forms a continuous layer.
- Thermal curing: Fusion and cross-linking of the resins.
Cooling: Avoids internal stresses in the film - This process is widely used in the automotive industry, household appliances, metal furniture and industrial components.
Working principle of powder coating
Powder coating is based on the application of finely ground particles of polymer resins, pigments, and additives on a metallic substrate. The powder is electrostatically bonded to the surface and subsequently undergoes a thermal curing process for melting and polymerization.
By chemical composition:
- Epoxy: High chemical resistance; limited UV stability.
- Polyester: Excellent weather resistance and flexibility.
- Epoxy-polyester hybrids: Balance between chemical and UV resistance.
- Acrylics and polyurethanes: Premium finishes, high resistance.
Thermal behavior:
- Thermosets: Be chemically cross-linked; irreversible.
Thermoplastics: Melt and can be reprocessed.
The choice of powder type is determined by the technical and environmental requirements of the final application.
Batch systems: Features and benefits
Unlike continuous line systems, batch powder coating systems allow for greater production flexibility. They are ideal for:
- Large parts or complex geometries.
- Custom or low volume production.
- Frequent changes in color or powder type.
These systems include application booths, curing ovens, support racks and ventilation systems. Although they require more handling, their adaptability makes them popular in industries where versatility is key.
The process consists of the following steps:
- Surface preparation: Removal of contaminants by chemical cleaning (degreasing, phosphating, passivation) or mechanical cleaning (sandblasting, sanding).
- Electrostatic charge: An electric charge is manually applied to the powder using an electrostatic gun, which causes it to be attracted to the surface of the grounded part.
- Powder deposition: The adhering particles form a uniform layer, the thickness of which depends on the application and the transfer efficiency of the spray gun.
- Thermal curing: The coated part is placed in an oven where the powder melts and chemically reacts to form a solid, uniform and resistant film.
- Cooling and handling: After curing, the part is cooled before handling or assembly.
This approach is ideal for custom production, large parts or complex geometries that require greater flexibility in application. Want to learn more about batch powder coating systems? Watch this video courtesy of: Global Finishing Solutions.
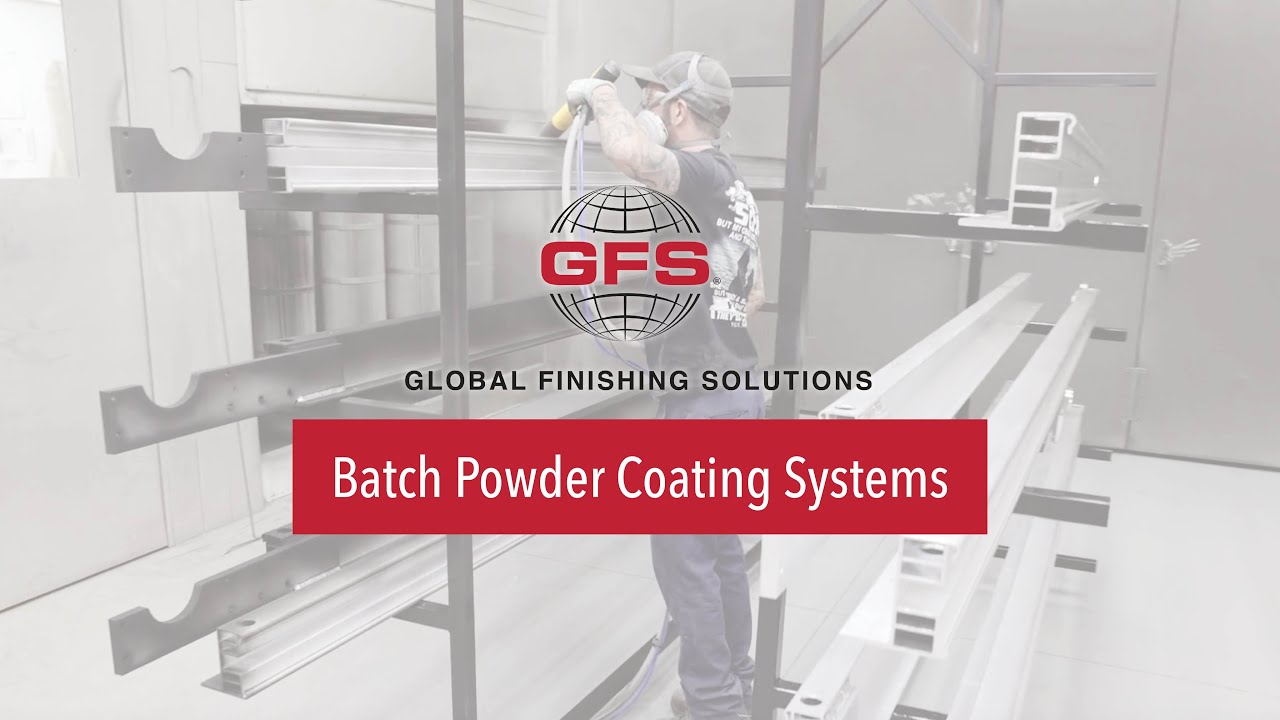
Batch powder coating systems.
Powder coating process: Automation and control
Automation has transformed the efficiency, reproducibility, and traceability in batch systems. Some technologies include:
- Application robots: Ensure uniform coverage and reduce human error.
- Machine vision systems: Detect defects in real time.
- Parameter control software: Manages temperature, voltage, air speed and exposure time.
- Integration with SCADA and MES: Allows traceability and control from the plant to the ERP.stems?
The incorporation of automated technologies in batch powder coating systems allows for improved process efficiency, quality, and repeatability. Some of the most outstanding advantages include:
These types of technological improvements make batch systems highly efficient solutions for industries that require flexibility without compromising the quality of the finish. This method is widely used in the automotive industry, renewable energy, metal furniture and infrastructure, due to its high resistance to corrosion, impact and chemical agents.
The following video shows an automated process of electrostatic application of powder coatings from the beginning to the end of the process. Source: HEBEI HANNA TECHNOLOGY CO., LTD.

Design of an automated powder coating system.
Intelligent data management for inspection and control
Coating inspection generates a large volume of data, from surface preparation to the final evaluation of the applied film. To streamline this process and ensure complete inspection traceability, advanced data management software solutions are being developed that integrate directly with your measurement devices.
This software allows data to be collected, analyzed and organized into structured projects, facilitating the generation of professional reports in real time. Designed to meet the exacting standards of quality inspectors, it offers an intuitive interface that allows you to visualize trends, detect deviations and document compliance with maximum accuracy.
Inspection and quality control technologies
Film thickness control, thermal curing and adhesion are essential for a quality finish. They are used:
- Digital thickness gauges: Based on magnetic induction and eddy currents.
- Thermal cameras: Monitor homogeneity of cure.
- Optical sensors: Evaluate deposition before curing.
- Data traceability systems: Integrate inspection with real-time digital documentation.
Energy optimization and sustainability
Powder coating represents an environmentally friendly alternative to liquid coatings:
- No solvent emissions.
- Recovery of unbonded powder.
- Low energy consumption oven systems (convection, IR, hybrid).
These features align it with the principles of circular economy and low carbon industries.
The future of powder coating: AI and digitization
The use of artificial intelligence and digital twins is revolutionizing surface finishing processes. Highlights include:
- Predictive modeling: anticipate defects and suggest corrections.
- Dynamic adjustment of parameters in real time.
- Digital Twins: Simulate real conditions to optimize results without physical testing.
These tools allow taking the process towards a zero-defect model and high efficiency.
Conclusions
Understanding powder coating and how does powder coating work from a technical perspective allows industries to adopt high efficiency processes with minimal environmental impact. The incorporation of automation and control in batch systems not only increases the quality of the finish, but also strengthens the competitiveness of companies.
The technological evolution of powder coating is a sign of the advance towards sustainable, intelligent and adaptable industrial processes, where quality and traceability become strategic allies for operational excellence.
References
- American Powder Coating Association (APCA). Technical Standards.
- ISO 2178:2016 / ISO 2360:2017 – Thickness measurement of coatings.
- Gema Switzerland GmbH. Powder coating equipment manual.
- ASTM D3359, D1186 – Standards for adhesion and coating thickness.
- European Coatings Journal. Trends in powder coating automation.