Table of Contents
In this article, it is intended to describe the corrosion processes associated with exposed metal structure systems in environments with high relative humidity; causing different deterioration damages, such as cases of corrosion due to differential aeration. In this context, the evaluation and solution of a practical case of differential aeration corrosion in nitrogen cylinders evaluated in a gas extraction platform, which are exposed to a humid and saline environment, is presented.
This phenomenon that consists of the degradation of a material is one of the problems that affects the majority of the equipment, pipes and structures in the oil and gas industry, which over time if not detected in its initial phase could cause the forced exit of some asset, or even more, a process unit and this would be transformed into an economic impact due to loss of production
Before considering this type of corrosion, we will define differential aeration as the difference in the degree of oxygenation, commonly by aeration, which can exist in different contiguous media, associated with the difference in oxygen in media with different degrees of humidity, or drying.
Differential aeration corrosion is an electrochemical corrosive process generated when the alloy is in contact with a polar solvent (water or alcohol) or an electrolyte (salt, acid or alkali dissolved in water), in other words, when a part of a piece metal is in contact with a concentration of oxygen greater than that existing in another area of the same piece. Whether in pipes or equipment, this type of corrosion could be generated where there is a concentration of moisture and a restriction of air flow, such as points of contact with fastening elements (clamps), spaces with confinement, support points with supports. or metal structures, overlapping sections, to mention a few cases.
Generally, metal surfaces are protected with a coating to mitigate the damage mechanism that could originate in the operational environment, however, there is damage to these coatings caused during the installation of some equipment or piping, during inspections, during maintenance work. , blows caused by tools, the degradation of the paint film, among others; which expose the base material to the environment with dew formation allowing localized rust formation to begin. The following image shows the different types of localized damage caused by corrosive by differential aeration in ferrous elements.
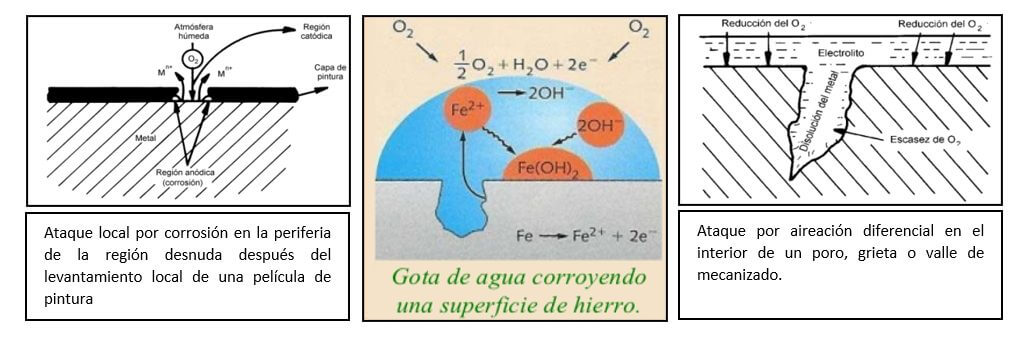
Corrosion study by Differential Aeration
Practical case presented in nitrogen cylinders evaluated in a gas extraction platform, which are exposed to a humid and saline environment, arranged vertically and held with clamp-type elements, although the entire system is exposed to the same environment, the The clamp does not allow the air to move freely in certain sectors, promoting the formation of condensed drops in specific segments, affecting the area where the friction between the clamp and the cylinders occurs. The damage mechanism was presented in the form of grouped pitting. A similar case occurred with some cylinders of the air system on the same platform where their supporting base prevents the air from flowing freely, allowing the concentration of humidity in a sector of the wall (cylindrical casing) and the lower head. For this to happen, the intervention of a section of the alloy is required that behaves as an anode (area that is corroded) and cathode (area of the alloy that is not consumed by the corrosion process), where the environmental conditions allow, presence of different phases of the same alloy or different degrees of aeration of a metal part.
To determine how compromised these assets (Cylinders) were, an evaluation was required according to the standard ISO-9809-1 “Design, construction and testing of seamless steel gas cylinders and tubes” which establishes in its point 7.3 the equation to calculate the minimum guaranteed thickness for cylindrical seamless steel containers taking into account a safety factor in percentage according to customer requirements and also considering what is established in the ISO-6406 “Seamless steel gas cylinders: periodic inspection and testing” that determines in its table B.2 the rejection criteria due to corrosion mechanisms in cylinder walls, in the ITEM that applies to pitting, since it was the indication found in the mentioned cases. Taking into account the wall thickness obtained by means of an ultrasound test and the evaluation of the depth of the pits. Based on this, a comparative table is made with the minimum guaranteed thickness (calculated) and the remaining thickness (thickness measured in the pit-free sector adjacent to the area of interest, subtracting the depth of the pit) to determine if the cylinder is act or not to continue the service for which it is intended. Therefore, it is recommended to dimension the damage found and characterized, in order to then take the pertinent actions, be it the application of a protective coating, the restoration of material or the replacement of the cylinder.
conclusion
The importance of detecting the damage caused by corrosion is the analysis of the factors that influence the generation of said condition, for which it is convenient to take corrective actions to mitigate that the assets are again affected.
References
ISO-9809-1 “Design, construction and testing of seamless steel gas cylinders and tubes” ISO-6406 “Seamless steel gas cylinders – Periodic inspection and testing” |