Intelligent maintenance systems can be used to improve existing predictive, preventive and corrective maintenance programs, which provide functional, optimal and efficient support, allowing the implementation of intelligent maintenance systems.
Corrosion is a significant problem in most critical infrastructures, such as bridges, oil and gas pipelines, and marine structures, among others. This phenomenon not only reduces the useful life of the physical structure, but can also lead to catastrophic failures that have serious economic and social consequences. Therefore, it is essential to have effective maintenance early warning programs that help prevent corrosion and maintain the integrity of the structure.
These systems use historical and real-time data to predict any defect in components and equipment, this allows the engineers in charge of these activities to apply preventive and corrective measures before a failure occurs, since, if it occurs, even in a single component can have serious consequences.
Artificial Intelligence and Mechanical Integrity: Corrosion and Erosion Management
Mechanical integrity is a key element of any effective process management program. It involves ensuring that equipment such as pressure drums, piping, pumps, compressors, and instruments are kept in good working order to ensure safe, reliable, and profitable operation. Corrosion and erosion management of piping and process equipment are critical components of mechanical integrity.
Corrosion is the gradual deterioration of materials due to chemical or electrochemical reactions with the environment. It is a natural process that can occur in any process equipment made of metals, alloys, and other materials.
This phenomenon can cause leaks, ruptures, and other failures in pipelines and equipment, creating safety risks, environmental contamination, and loss of production.
Erosion, on the other hand, is the physical wearing away of materials due to mechanical action such as fluid flow, particle impact, and vibration. Erosion can occur in pipelines, valves, pumps, and other equipment exposed to high velocity fluids, abrasive particles, or other adverse conditions.
Erosion can cause thinning, cracking, and other forms of damage, reducing performance, increasing maintenance, and increasing costs.
Therefore, it is essential to have advanced corrosion monitoring and control technologies, as well as continuous training of workers in safety measures, to maximize controls over this phenomenon and minimize the attack of corrosive agents on the prevailing structures.
Artificial intelligence (AI) has the potential to revolutionize the management and prevention of corrosion in vital structures in the industry.
Applications Intelligent maintenance systems in the integrity of assets
Predictive analysis: AI algorithms can analyze vast amounts of data about corrosion in critical infrastructure, such as bridges and oil and gas pipelines. Using machine learning techniques, these applications can identify patterns in data and predict when and where corrosion is most likely to occur.
To manage these phenomena effectively, a comprehensive program must be established that includes the following elements:
Risk assessment: Identify potential corrosion and erosion risks on each piece of equipment and prioritize them based on their severity, probability, and consequences.
Inspection and monitoring: AI applications can be used to inspect and monitor critical infrastructure in real time. For example, drones equipped with cameras and sensors can collect data on corrosion on bridges and pipelines. AI algorithms can analyze this data in real time and alert engineers if signs of corrosion are detected.
Regularly inspect and monitor equipment for any signs of corrosion or erosion, such as leaks, cracks, thinning, or discoloration. Use non-destructive testing (NDT) methods, such as ultrasonic testing, radiography, and eddy current testing, to assess the integrity of the equipment.
By using AI for predictive analytics and real-time monitoring, engineers can better manage and prevent corrosion in the vital structure of facilities, leading to increased safety and lower maintenance costs.
Maintenance and AI – Implement a predictive and preventative maintenance program to address any identified defects and prevent further damage. Use proper repair techniques, such as welding, plating, plating, or replacement, to restore the equipment to its original condition.
Material Selection and Design – Select materials and design equipment that are resistant to corrosion and erosion, such as corrosion resistant alloys (CRA), high strength materials, and erosion resistant coatings. Consider fluid properties, operating conditions, and environmental factors when selecting materials and designing equipment.
Training and Education: Train and educate personnel involved in corrosion and erosion management to understand the risks, inspection and monitoring techniques, maintenance and repair methods, and design criteria and material selection.
A well-designed erosion and corrosion management program can help reduce the risk of equipment failure, improve safety and environmental protection, and improve process plant reliability and profitability.
How do corrosion monitoring and control systems work if they are used with artificial intelligence applied to the oil and gas industry?
Corrosion monitoring and control systems that incorporate artificial intelligence (AI) in the oil and gas industry work by using advanced algorithms to process large amounts of data collected from various sources, including sensors, inspection reports, and logs. maintenance histories. These systems analyze the data and use machine learning techniques to identify patterns, correlations, and anomalies that can indicate potential weld and corrosion problems.
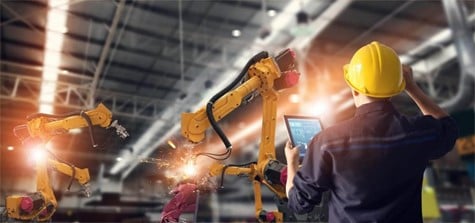
AI algorithms can predict when and where corrosion is likely to occur, allowing operators to take preventative action before corrosion becomes a major problem. The systems can also use real-time data from sensors and other sources to detect and alert operators to potential corrosion problems as they occur, enabling faster and more effective responses to mitigate the problem.
Techniques and technologies to maximize the benefits of AI in corrosion prevention
To maximize the benefits of AI in corrosion prevention, several new techniques and technologies are being developed and implemented. Here are some examples:
Internet of Things (IoT): IoT devices such as sensors and smart meters can collect real-time data on environmental and operational conditions, which can be analyzed by AI algorithms to predict corrosion risks.
The Internet of Things, or IoT, is a system of interrelated computing devices, mechanical and digital machines, objects, animals, or people that have unique identifiers (UIDs) and the ability to transfer data over a network without the need for a person to another. human or person-to-computer interaction.
Advanced Analysis – Advanced analysis techniques such as machine learning and deep learning can analyze large amounts of data to identify patterns and anomalies in corrosion risk factors. This can allow for more accurate and reliable predictions of potential corrosion problems.
Remote monitoring: Remote monitoring technologies such as drones, unmanned aerial vehicles (UAVs), and sensor-equipped robots can collect data in hard-to-reach or dangerous infrastructure areas. This data can be analyzed using AI algorithms to identify potential corrosion issues.
3D Printing – 3D printing can be used to create custom parts and components with specialized coatings and materials to prevent corrosion in specific applications.
By leveraging these new techniques and technologies, the benefits of AI in corrosion prevention can be maximized, allowing for more accurate and reliable predictions of potential corrosion problems, faster and more effective responses to corrosion problems, and cost of repair. reduced maintenance.
How and in what way can AI help to identify the most suitable materials for different applications and corrosive environments?
AI can help identify the most suitable materials for different applications and corrosive environments by using machine learning algorithms to analyze vast amounts of data on material properties, environmental conditions, and corrosion risk factors. This can enable more accurate and reliable predictions of material performance and corrosion resistance, and help identify the most suitable materials for specific applications and environments. Furthermore, AI can assist in the detection and monitoring of this phenomenon by automatically detecting corrosion and coating breakdown, replacing costly and time-consuming close-up visual inspections.
The benefits of using AI for corrosion detection include increased security, reduced access costs, objective classification, and integration with digital asset management systems.
AI algorithms can automatically detect corrosion and coating breakdown, replacing costly and time-consuming close-up visual inspections. This can enable more efficient and effective inspection tools, leveraging AI algorithms to increase efficiency in corrosion detection and monitoring. Likewise, AI can provide more accurate and reliable predictions of potential corrosion problems, enabling more proactive and effective corrosion prevention and maintenance strategies.
AI can also estimate a range of corrosion rates for a given family of materials in a specified range of environments without running experiments, which can save time and resources.
Can machine learning models be trained to identify patterns that indicate failures in robots or automated systems?
Yes, machine learning models can be trained to identify patterns that indicate failures in robots or automated systems. Machine learning algorithms can analyze vast amounts of data about system performance, environmental conditions, and other factors to identify patterns and anomalies that may indicate potential failure or malfunction.
By training machine learning models on historical data, it is possible to develop predictive models that can identify potential failures before they occur, enabling more proactive maintenance and repair strategies.
Additionally, explainable machine learning techniques can provide insight into the underlying causes of failures, allowing for more effective troubleshooting. However, it is important to carefully evaluate the advantages and limitations of different machine learning methods to predict failures in industrial robots and automated systems.
Limitations of AI in corrosion detection include the need for high-quality data to train machine learning algorithms, the potential for false positives and false negatives, and the inability to detect certain types of corrosion that require specialized equipment or techniques.
Likewise, AI algorithms may not be able to detect corrosion in hard-to-reach areas or complex geometries, which may require additional inspection methods.
Also, the cost of implementing AI-based corrosion detection systems may be prohibitive for some organizations, and there may be concerns about the reliability and accuracy of AI-based systems compared to traditional inspection methods. Therefore, it is important to carefully evaluate the benefits and limitations of AI-based corrosion detection systems before implementing them in real-world applications.