Introduction
In the oil industry, pumps play an important role in facilitating the transport of fluids throughout the extraction, refining and transportation processes. In this sense, the API 685 standard establishes fundamental criteria for the selection and operation of these pumps, ensuring their efficiency and safety. Complying with API 685 standards is critical to maintaining smooth and safe operations at all stages of the oil industry1.
The oil industry is a highly complex and demanding sector where efficiency and safety are critical to operational success. The proper selection of these pumps is significant in the efficient and reliable operation of the facility.
Throughout this article, we will explore the importance of pumps in the oil industry and the relevance of the API 685 standard in the selection of these pumps. In addition, we will delve into the criteria established by API 685, analyzing how these criteria contribute to ensure operational efficiency, safety and reliability in pumping systems used in the oil industry.
Importance of pumps in the oil industry
This equipment plays a key role in the refining industry in numerous processes ranging from crude oil extraction to refining and distribution. They are responsible for transporting fluids over long distances and at different heights, thus facilitating the continuous flow of oil and petroleum products along the supply chain.
In the extraction process, pumps are essential for propelling oil from production wells to the surface. Once extracted, the crude oil must be transported through pipelines or tanker trucks to refineries. Here, pumps are needed to move oil through the various refining processes, which include separation, cracking and distillation, among others.
In addition, in the refining phase, the pumps are used to handle a wide range of chemicals and petroleum by-products, such as gasoline, diesel, kerosene, lubricating oils and petrochemicals. They ensure that refined products are efficiently transported to storage tanks or means of transport for domestic and international distribution.
The proper selection of these pumps is significant in the efficient and reliable operation of the facility. The American Petroleum Institute (API) developed the API 685 standard with the goal of providing clear and consistent guidelines to help industry professionals make informed decisions about which type of pump to use in each application.
API 685 standard in the oil industry
API 685, developed by the American Petroleum Institute (API), is a widely recognized standard in the petroleum industry that establishes guidelines and criteria for the selection, design, manufacture, testing, installation, operation and maintenance of centrifugal process pumps for critical applications in the oil, gas and petrochemical industry. This standard is essential to ensure the optimum performance, safety and reliability of pumps used in key oilfield operations such as production, refining and transportation.
API 685 establishes the minimum requirements for sealless centrifugal pumps manufactured for heavy-duty services in the petrochemical and gas industry. This standard is very similar to API 610, only it is the equivalent of a seal-less pump. This standard can only be applied to two different classifications of cantilever pumps: magnetic drive pumps and encapsulated motor pumps. The latter is considered the oil industry standard for seal-less pumps and has been for many years.
History and evolution of the API 685 standard
The API 685 standard has its roots in the oil industry’s efforts to standardize and improve the efficiency of pumps used in critical applications. Over the years, it has undergone several revisions and updates to adapt to technological advances and the changing needs of the industry. Its evolution has been driven by the constant search for more rigorous standards that guarantee safety and efficiency in oilfield operations. Examples of its positive impact include improving pump reliability, reducing operating costs and preventing incidents at key oilfield facilities.
API 685 standards update process
The third edition of the American Petroleum Institute (API) standard “Sealless Centrifugal Pumps for Oil, Petrochemical and Gas Industry Process Services” was published in July 2022. Four areas of particular interest addressed in the API 685 standard update stand out:
- Expanded Introduction: Answers questions raised by the oil and gas community about the common use of API seal-less pumps, providing a more detailed view of their application in the industry.
- Detailed information in the data sheets: The information required to properly complete the API 685 data sheets has been expanded, ensuring that both the purchaser and pump manufacturers accurately address all parameters for the proper selection and scope of supply of seal-less pumps.
- New informative annex: A new informative annex is introduced to address unsealed cantilever multistage pumps, thus extending the scope of the standard to cover this type of configuration.
- It is important to note that the updated API 685 standard includes requirements for both horizontal and vertical single-stage cantilever pumps. These pumps are typically installed in classified environments where hazardous or explosive vapors may be present.
The review process involves the work team considering the relationship between the standard paragraphs within the API standards document (applicable to all equipment) and the specific paragraphs of the API 685 document. This ensures a certain consistency among all rotating equipment. It is important to make the following decisions:
- Modify the API 685 standard to align with certain paragraphs of the API standard.
- Adapt the standard paragraphs to better conform to the standard under review.
- Justify the inapplicability of a standard paragraph to the equipment for which the standard is intended and proceed to eliminate it.
This process ensures that API standards are up to date and relevant to current conditions and technologies, while maintaining high standards.
API 685 centrifugal pumps without seal
API pumps are a specialized class of pumps designed to meet the stringent standards set by the American Petroleum Institute (API) in its standard 685. These pumps are designed for critical applications in the oil and petrochemical industry, where safety, reliability and performance are of paramount importance.
They represent the best technology available for use in refinery and industrial petrochemical applications, and have been designed for use in the hydrocarbon process industry, represent an economical, totally safe solution and are especially suitable for working with the following media: Liquefied Petroleum Gases (LPG): propane, butane, chlorine, ammonia, phosgene, hydrocarbons: olefins (ethylene, propylene, etc.), kerosenes, aromatics, etc.
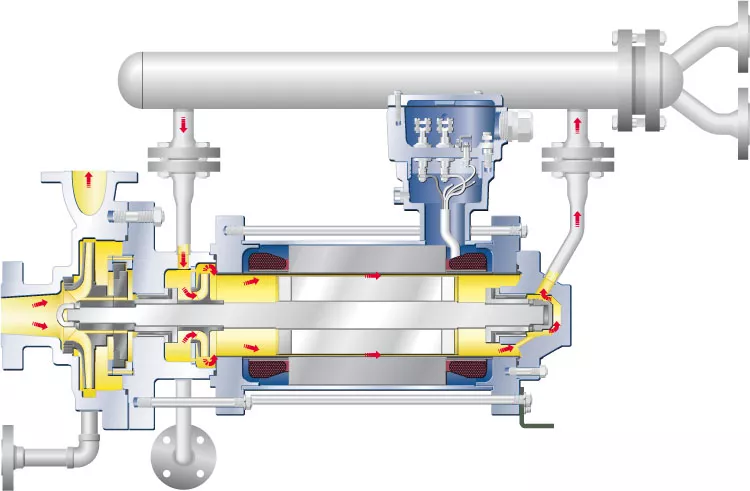
The design of API 685 pumps eliminates the use of mechanical seals, bearings, coupling sleeve and air venting. The result is a safe, simple, quiet, compact pump with a mean time between failures of 10-15 years. The following are some key aspects of these pumps:
- Hermetic design: The distinctive feature of hermetic pumps is their completely hermetic design. This means that the pumped fluid is completely encapsulated inside the pump, without any leakage point to the outside. This hermetic design ensures process safety and reduces the risk of leaks and spills.
- Compliance with API Standard 685: They are designed and manufactured in accordance with the stringent requirements of API Standard 685, which establishes specific criteria for the design, construction, operation and maintenance of high-pressure centrifugal pumps for hydrocarbon services, thus ensuring reliable and safe performance in critical environments.
- Petroleum and Petrochemical Industry Applications: Generally, they are used in a wide range of applications in the petroleum and petrochemical industry, including the transfer of corrosive chemicals, the handling of flammable fluids and the circulation of process fluids in refineries and chemical plants.
- Rugged and durable construction: They are built with high quality, corrosion-resistant materials to ensure long life and reliable performance in harsh environments. In addition, its hermetic design eliminates the need for mechanical seals, thus reducing the possibility of failures and leaks.
- Customized options: They are designed to adapt to the specific needs of each application. This includes a variety of sizes, materials of construction and motor configurations to meet each customer’s unique performance requirements and service conditions.
In order to expand information on the new technologies of encapsulated motor centrifugal pumps, the following video is presented courtesy of: HERMETIC-Pumpen GmbH.
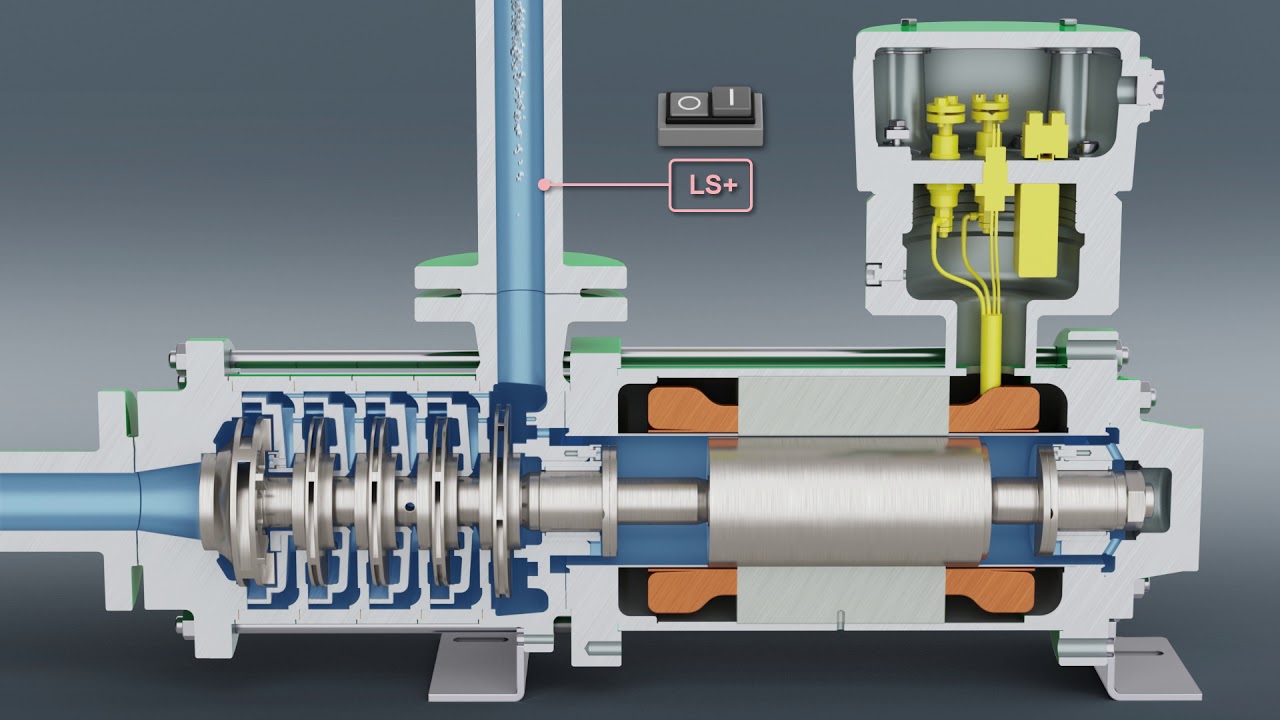
HERMÉTICO | Dispositivos de Bombas con motor encapsulado
Pump selection criteria according to API 685
The following are the most important criteria for the selection of centrifugal pumps:
Conditions of service
The service conditions established by API 685 are fundamental to ensure the optimum performance of pumps in the oil industry. This includes parameters such as temperature, pressure and the type of fluid the pump will handle. For example, centrifugal pumps used in high temperature applications will need special materials and designs to withstand extreme conditions without compromising efficiency.
Design and construction
The API 685 standard establishes strict design and construction requirements to ensure the safety and efficiency of pumps in critical applications. This involves considerations such as structural strength, precise alignment of components, tightness and responsiveness to varying operating conditions. Robust design and high quality construction are essential to avoid premature failure and ensure the long-term reliability of the pumps.
Construction materials
The materials used in the manufacture of pumps are critical to their performance and durability. API 685 specifies recommended materials with emphasis on corrosion and abrasion resistance, especially in aggressive oil industry environments. Materials such as stainless steel, bronze and certain corrosion-resistant alloys are preferred to ensure long service life and reduced maintenance.
Reliability and maintenance
Operational reliability and proper maintenance are key issues addressed by API 685. The standard establishes reliability standards that pumps must meet, as well as recommended maintenance programs to prolong their service life. This may include regular inspections, proper lubrication, vibration monitoring and preventive repairs to prevent failures and maximize the operational availability of the pumps.
Documentation and testing
API 685 also emphasizes the importance of complete documentation and thorough testing during the pump selection and purchase process. This includes detailed documentation of technical specifications, operation and maintenance manuals, as well as performance tests and quality certifications. Rigorous testing ensures that the pumps meet the required quality standards and are ready to face the demanding operating conditions in the oil industry.
Conclusions
Lhe pumps play a key role in the global economy by ensuring a constant and reliable supply of petroleum products. The efficiency and reliability of these pumps are important for maintaining the continuous flow of oil and oil products, which in turn contributes to the efficient operation of the oil industry and energy supply worldwide.
The importance of pumps in the oil industry is fundamental to its operation and to meet the global demand for energy.
References
- API Standard 685 3rd Ed., “Sealless Centrifugal Pumps for Petroleum, Petrochemical, and Gas Industry Process Service,” API, July 2022.
- HERMETIC hermetic pumps API 685.