Table of Contents
- Nanocomposites: Advanced properties and industrial applications
- Smart metal composites: Transforming the high-tech industry
- Advanced polymer composites for industrial applications
- Sustainable biomaterials: The future of advanced composites
- Carbon fiber composites: Industrial performance optimization
- Additive manufacturing: Revolution in the production of composite materials
- Intelligent design and manufacturing: Computational optimization of composites
- Conclusions
- References
Composite materials have established themselves as essential components in the design of advanced technologies, thanks to their outstanding properties such as high strength-to-weight ratio, excellent corrosion resistance, and remarkable thermal stability. According to recent studies, the global market for composite materials reached $95.6 billion in 2024, with annual growth projections of 7.8% through 2030, driven mainly by demand for lightweight and durable solutions in key sectors.
These materials, consisting of a matrix and a reinforcement, have undergone significant evolution with advances that make them indispensable in multiple industries, particularly in demanding industrial applications. The continuous development of composite materials offers innovative solutions to the challenges associated with performance, durability, and sustainability in increasingly demanding industrial environments.
Nanocomposites: Advanced properties and industrial applications
Nanocomposites represent a revolution in materials science by introducing nanoparticles into the matrix of traditional materials, significantly improving their overall properties. This improvement in durability and thermal stability is especially critical for applications operating under high temperature conditions. This matrix (called dispersing phase or resin), which gives shape to the part, contains a reinforcement, or dispersed phase, based on carbon fibers (whose raw material is polyacrylonitrile). It is an expensive material, with high mechanical properties and lightweight.
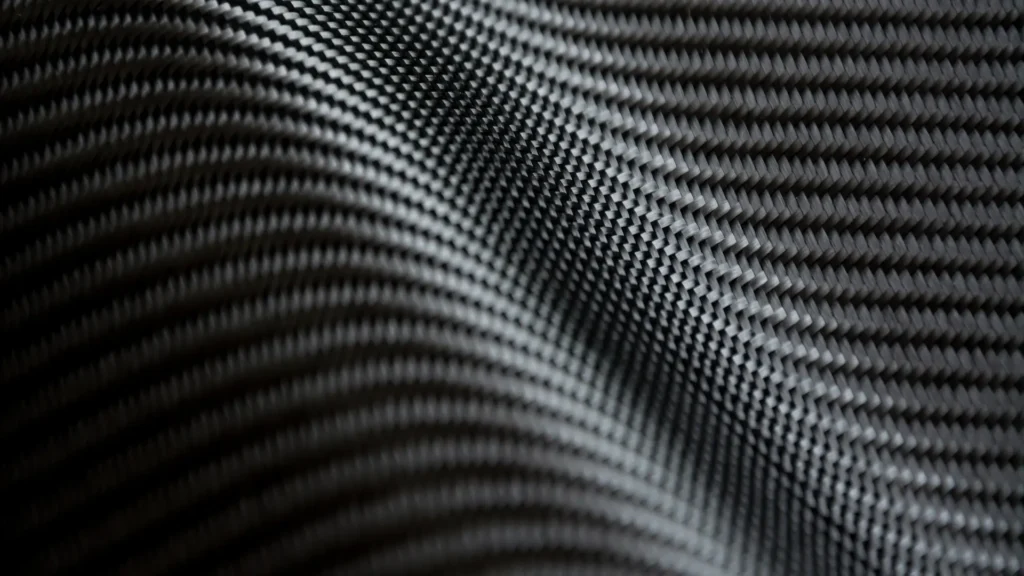
Measurable performance improvements
Recent research shows that the incorporation of graphene nanoparticles can increase tensile strength by up to 45% and thermal conductivity by more than 60% compared to conventional polymer matrices. These performance increases have enabled nanocomposites to penetrate markets previously dominated by traditional metals and alloys.
Self-healing capabilities
Among the most promising innovations are materials with self-healing capabilities, where functionalized nanoparticles release repair agents in the event of microscopic damage, ensuring unprecedented durability and reliability. Laboratory tests have confirmed that these systems can recover up to 85% of the original strength after suffering microfractures, significantly extending the useful life of the components.
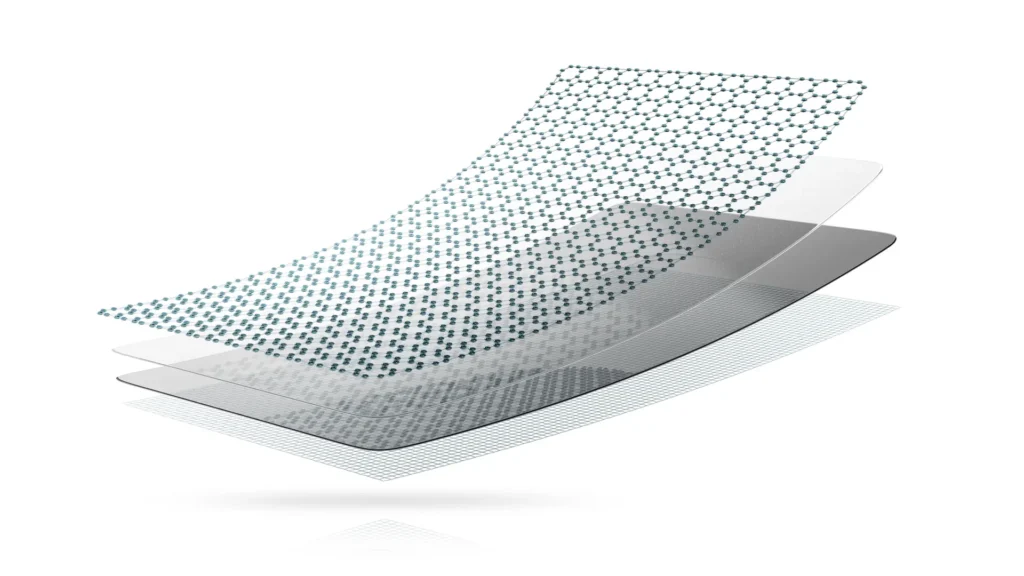
Advanced electronics applications
Improved electrical conductivity makes these composite materials uniquely suited for applications in high-frequency electronics and energy storage devices. Polymer matrix nanocomposites with carbon nanotubes are revolutionizing solid-state battery design, offering energy densities 30% higher than conventional solutions.
Smart metal composites: Transforming the high-tech industry
Smart metallic composites represent a revolutionary milestone in materials science, incorporating shape-memory alloys or polymers into advanced metallic matrices. These cutting-edge materials can modify their structural configuration in response to external stimuli such as thermal variations or mechanical stresses, making them ideal candidates for adaptive technologies in demanding industrial environments.
Shape Memory Alloys (SMA)
Shape memory alloys stand out for their ability to “remember” their original configuration after being deformed, returning to their initial state by thermal activation. This unique behavior, based on transitions in the crystalline structure of the material, has found fundamental applications in:
- Aerospace: Implementation in adaptive airfoils and transformable wing structures that optimize performance in different flight conditions.
- Biomedicine: Alloys such as Nitinol (Ni-Ti) are used in medical devices such as vascular stents and orthodontic wires, facilitating minimally invasive procedures.
- Advanced robotics: In the emerging field of soft robotics, SMAs enable actuators to replicate precise biomechanical movements, improving the operational fluidity and precision of robotic systems.
High-precision magnetostrictive compounds
Magnetostrictive materials respond to magnetic fields by altering their physical dimensions. Compounds such as Terfenol-D (an alloy of terbium, dysprosium, and iron) undergo controlled expansion or contraction in the presence of calibrated magnetic fields, a characteristic that makes them optimal for:
- Underwater sonar systems: Convert magnetic energy into mechanical vibrations with high energy efficiency.
- Industrial energy harvesting: Capture vibrations or mechanical movements in industrial environments, transforming them into usable electricity.
- Nanometer precision actuators: Used in the alignment of optical instruments and space telescopes where extremely precise adjustments are required.
Advanced piezoelectric composite materials
Piezoelectric metallic composite materials generate electrical potential when subjected to mechanical deformation, making them essential components for:
- Industrial structural monitoring: Vibration sensors and accelerometers that transform vibrations into electrical signals for monitoring and predictive control of equipment.
- Energy harvesting systems: Harnessing of ambient mechanical energy to generate electricity in autonomous, low-consumption devices.
- Industrial acoustic technology: High efficiency transducers in sonar systems, industrial microphones and non-destructive testing equipment.
Thermoelectric compounds for energy recovery
Thermoelectric materials transform thermal differentials directly into electrical potential, providing solutions for:
- Waste heat recovery: Energy recovery in industrial processes and vehicle exhaust systems, improving overall energy efficiency.
- Space exploration: Radioisotope thermoelectric generators (RTGs) that convert heat from radioactive materials into reliable electricity for deep space missions.
- Compressorless cooling systems: Peltier cooling technologies for precision electronics and medical applications.
Magnetic Shape Memory Alloys (MSMA)
These advanced materials, a specialized variant of SMAs, modify their configuration under the influence of magnetic fields controlled by rotating their crystalline structure. Their main applications include:
- Ultraprecise positioning devices: Nanometer control for semiconductor and microelectronic component manufacturing.
- Biomedical instrumentation: Precise manipulators for minimally invasive surgical procedures.
- Fast-response actuators: Industrial systems requiring high-frequency, high-precision operating cycles.
Advanced polymer composites for industrial applications
Polymer composites have radically transformed various industries thanks to their exceptional flexibility and ability to establish strong interfaces with reinforcing materials. Recent advances in polymeric matrices have significantly optimized the interfacial adhesion between fibers and matrix, a key factor in ensuring structural integrity under extreme conditions of mechanical loading and thermal stress.
High-performance polymeric matrices
Innovations in thermosetting polymers and thermoplastics have substantially improved critical properties:
- 40% increase in tensile strength compared to previous generations.
- 65% improvement in impact resistance, crucial for components subjected to dynamic loads.
- Reduced moisture absorption to below 0.5%, extending service life in humid environments.
Chemical and environmental resistance
The integration of advanced hydrophobic polymers has minimized the degradative effects caused by exposure to aggressive chemical agents, ensuring optimum performance in:
- Transportation infrastructures exposed to variable environmental conditions.
- Manufacturing equipment in contact with corrosive fluids.
- Robotic components operating in harsh industrial environments.
Emerging applications 2025
Polymer composites are penetrating sectors traditionally dominated by metals:
- Energy storage systems with improved thermal efficiency.
- Structural components for next-generation electric vehicles.
- Sterilizable medical equipment with integrated antimicrobial properties.
Sustainable biomaterials: The future of advanced composites
In response to the growing demand for more sustainable solutions, composite biomaterials have gained strategic relevance in multiple industrial sectors. These innovative composites, which integrate fibers or particles of natural origin with eco-compatible matrices, offer an exceptional strength-to-weight ratio, as well as advanced properties such as resistance to corrosion and ultraviolet radiation.
Quantified sustainability
The latest life cycle analyses show that composite biomaterials can reduce the carbon footprint by up to 60% compared to conventional petroleum-based composites. This significant reduction in environmental impact does not compromise technical performance, as the latest generations of biocomposites achieve mechanical properties comparable to their traditional synthetic alternatives.
Innovations in functional biocomposites
The development of biomaterials has evolved considerably, incorporating:
- Flame retardant additives of natural origin that comply with the most stringent regulations.
- Thermally stable matrices that tolerate operating temperatures in excess of 200°C.
- Controlled biodegradable systems with predictable shelf life and sustainable end-of-cycle.
High-tech industrial applications
Composite biomaterials are transforming key sectors:
- Automotive industry: Interior panels with improved sound absorption and reduced weight.
- Renewable energy: Components for wind turbines with reduced environmental footprint.
- Sustainable construction: Structural elements with carbon-neutral certification.
Carbon fiber composites: Industrial performance optimization
Carbon fiber reinforced polymers (CFRP) continue to expand their presence in strategic sectors such as automotive, aerospace, and power generation, where the optimal combination of structural strength and weight reduction is critical. These advanced materials stand out for their exceptional impact resistance and superior thermal conductivity, essential characteristics for components subjected to extreme thermal conditions.
Optimized thermal conductivity
The most recent developments in carbon fiber composites have succeeded in increasing thermal conductivity up to 15 W/mK, significantly exceeding the 0.3 W/mK typical of conventional polymers. This substantial improvement allows:
- Efficient heat dissipation in high power electronic components.
- Reduction of thermal fatigue risk in aerospace structures.
- Optimization of heat transfer in industrial heat exchangers.
Specific industrial applications
CFRPs are redefining performance standards in multiple sectors:
Energy industry
- Wind turbine blades with increased aerodynamic efficiency and extended service life.
- High-pressure hydrogen storage vessels with optimized safety factor.
- Experimental fusion reactor components with superior dimensional stability.
Aerospace sector
- Commercial aircraft primary structures with 30% weight reduction.
- Satellite components with thermal stability in extreme orbital conditions.
- Thermal protection systems for atmospheric re-entry vehicles.
High-end automotive industry
- Safety cells for competition vehicles with calibrated energy absorption.
- Structural components for premium electric cars with increased autonomy.
- High-pressure hydrogen storage systems for sustainable mobility.
Additive manufacturing: Revolution in the production of composite materials
Traditional methods of manufacturing composite structures present significant limitations in terms of geometric complexity, production time, and structural uniformity. Additive manufacturing (3D printing) has emerged as a transformative solution by enabling the controlled layer-by-layer deposition of composite materials, facilitating the creation of complex, customized geometries with unprecedented precision.
Technological advances 2024-2025
Additive manufacturing technologies for composites have undergone substantial advances:
- 3D printing with continuous fiber: Systems that integrate continuous filaments of carbon, glass or aramid fiber during the deposition process, achieving increases in strength of up to 10 times with respect to unreinforced polymers.
- Stereolithography composite manufacturing (SLA): Photopolymeric resins loaded with functional nanoparticles that make it possible to obtain parts with adapted electromagnetic, thermal or mechanical properties.
- Multi-material hybrid systems: Advanced platforms that combine extrusion of reinforced thermoplastics with controlled deposition of conductive materials, enabling the creation of integrated smart components.
Structural optimization and defect reduction
Additive manufacturing solves critical challenges in composite production:
- Reduction of internal porosity to less than 1%, improving structural integrity.
- Topological optimization that minimizes material required while maximizing strength.
- Precise control of fiber orientation to support specific load paths.
Industrial success stories
The implementation of additive manufacturing for composites has demonstrated tangible benefits:
- Aerospace industry: 40% reduction in development time for satellite components.
- Medical sector: Personalized implants with improved biocompatibility and optimized mechanical properties.
- Industrial automation: 35% reduction in robotic end-effector weight with increased rigidity.
Intelligent design and manufacturing: Computational optimization of composites
Efficient utilization of advanced composite materials depends critically on design and manufacturing methodologies based on computational simulation. Advanced tools such as finite element analysis (FEA) and machine learning algorithms are redefining optimization processes for highly complex composite structures.
Multiscale simulation and digital twins
Multiscale simulation approaches allow modeling the behavior of composite materials from the nanoscale to the macrostructure, providing:
- Accurate predictions of stress distribution at fiber-matrix interfaces.
- Detailed analysis of progressive failure mechanisms under complex loads.
- Optimization of lamination sequences for specific performance requirements.
Digital twin implementation for composite manufacturing processes has demonstrated 25% reductions in scrap rates and 15% improvements in structural uniformity.
Generative design for composite structures
Generative design techniques, powered by evolutionary algorithms and neural networks, are expanding the horizon of possibilities:
- Automatic identification of optimal structural configurations that maximize stiffness while minimizing weight.
- Creation of biomimetic structures that emulate natural organization principles.
- Optimization of fiber trajectories adapted to specific stress states.
These computational advances have made it possible to reduce the material required in structural components by up to 40% while maintaining or improving their mechanical properties.
Artificial Intelligence in manufacturing processes
AI integration in advanced composites production lines is transforming the industry:
- Artificial vision systems that detect microscopic defects in real time.
- Predictive algorithms that optimize curing parameters to minimize residual stresses.
- Continuous quality monitoring through integrated sensors and data analysis.
Conclusions
The integration of smart composite materials—such as nanocomposites, functional metals, and piezoelectric elements—is redefining advanced structural design by enabling components with self-diagnostic capabilities, real-time monitoring, and adaptive response to external conditions. This significantly enhances the safety, reliability, and operational efficiency of complex industrial systems.
Sustainability is becoming a core pillar in the evolution of composite materials, guiding research and development toward recyclable solutions based on thermoplastic matrices and biobased materials. These combine environmental efficiency with high mechanical performance, contributing to carbon footprint reduction in high-demand technological applications.
Advances in additive manufacturing, combined with collaborative digital platforms, are democratizing access to next-generation composite technologies by enabling localized production, structural design optimization, and on-demand manufacturing. This strengthens industrial resilience and accelerates innovation across strategic sectors such as aerospace, energy, automotive, and defense.
References
- https://www.researchgate.net/publication/379802182_Nanomaterials_for_advanced_energy_applications_Recent_advancements_and_future_trends
- https://www.compositesworld.com/news/tecniplas-manufactures-composite-scrubber-for-treatment-of-biogas
- https://pubmed.ncbi.nlm.nih.gov/21062250/
- https://www.mdpi.com/2079-4991/5/4/1690