Introducción
The H2S corrosion in the Upstream sector Oil and gas is a critical concern for the energy industry, hence the importance of implementing preventive measures; which are key to guaranteeing the integrity of infrastructure and maintaining security in this fundamental sector for the global economy.
This type of corrosion is a chemical phenomenon that occurs when hydrogen sulfide (H2S) in natural gas or oil reacts with the metal surface of pipes and other structures, causing the formation of cracks, pits, undercuts, holes and other structural damage, which can put the integrity of equipment and facilities at risk. .
In this article, we will explore the technologies of advanced monitoring used to prevent H 2 S corrosion damageWith examples of innovations, we will analyze strategic solutions that improve integrity management and minimize risks in this vital industry, interesting data and success stories regarding the topic will be provided.
H2S corrosion in the Upstream sector: A crucial challenge
H 2 S corrosion can result in the degradation of equipment and pipelines in the oil and gas industry. It is a corrosive gas that, when it comes into contact with metal, can cause significant damage. The effects of corrosion can be costly both in terms of repairs and production downtime.
In the Upstream oil and gas sector, this type of corrosion is one of the main causes of economic losses. Corrosion costs in this sector are estimated to run into billions of dollars annually.
Why is monitoring important?
Continuous corrosion monitoring is essential to prevent and ensure worker safety and asset integrity in the Upstream sector. Below are some advanced technologies used to carry out this monitoring effectively.
Advanced monitoring technologies
To prevent damage caused by H 2 S corrosion, it is necessary to have cutting-edge monitoring technologies that can detect and evaluate the risk of corrosion in real time. These technologies include:
They are a key tool in the fight against hydrogen sulfide corrosion. These devices can detect the presence of this compound in real time and provide accurate data on corrosion conditions in equipment and pipelines. The information collected by these sensors is important for making informed decisions.
2. Remote inspection
Remote inspection technology has revolutionized the way corrosion is assessed in hard-to-reach locations. Unmanned vehicles (drones) and underwater robots allow underwater assets and high-altitude structures to be inspected efficiently and safely.
3. Predictive modeling
Predictive modeling uses advanced algorithms to forecast future corrosion rate based on current conditions. This allows companies to plan preventative maintenance and reduce costs associated with unplanned repairs.
Strategic solutions
- Corrosion resistant materials
The selection of resistant materials is key in the management and mitigation of corrosion. Alloys such as stainless steel and nickel are known for their corrosion resistance and are widely used in industry.
2. Continuous monitoring and scheduled maintenance
Implementing continuous monitoring programs and scheduled maintenance is essential to prevent serious corrosion problems. This involves regular inspection of assets and timely replacement or repair of affected components.
3. Training and awareness
Training and raising awareness of workers about the risks associated with H 2 S corrosion plays a fundamental role in prevention. Education on best safety practices, handling of hazardous substances and failure prevention is essential for upstream. (Figure 1)
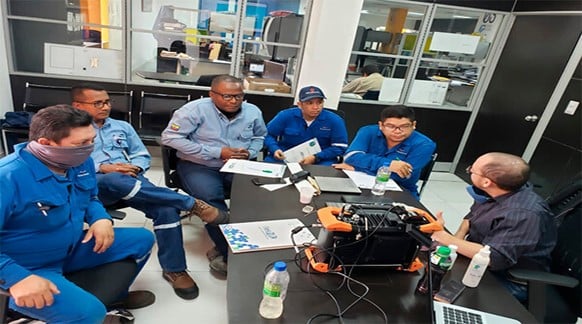
4. Changes in the design of the facilities
Some modifications to facility design can help reduce exposure to H 2 S.
5. Cleaning processes
They help eliminate H 2 S deposits that can promote corrosion.
Current and future innovations for solutions
Currently there are continuous monitoring programs to prevent serious corrosion problems. Below are some programs that use the continuous monitoring methodology against H2S:
- Intelligent Corrosion Monitoring (ICM): This tool uses corrosion sensors to detect and evaluate the risk of corrosion in real time, (Figure. 2).
- Corrosion Monitoring System (CMS): This program uses a combination of corrosion sensors, ultrasonic inspection and x-ray inspection to detect and evaluate the risk of corrosion.
- Corrosion Management System (CMS): It is a management methodology that combines corrosion sensors, ultrasonic inspection, x-ray inspection and data analysis to detect and evaluate the risk of corrosion.
- Technological advancement in the oil and gas industry does not stop. Some of the future innovations include the use of nanotechnology sensors and artificial intelligence systems for even more precise and automated monitoring.
- In the field of inspection, improvements in equipment technology to characterize defects continue to evolve. An example of these is how the Ultrasound method has improved to detect and characterize defects; from the technique used in the USK7 equipment, passing through the TOFD technique, later the PAUT and now the TFM (Total Focusing Method).
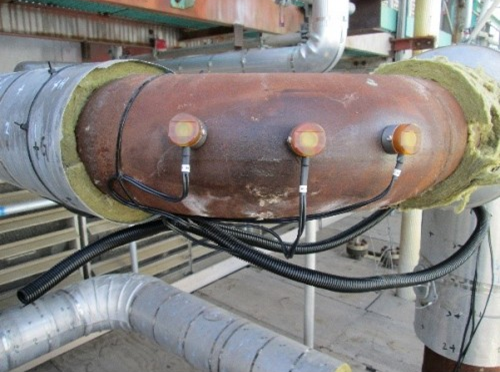
Interesting data
- H 2 S corrosion is one of the main causes of economic losses in the Upstream oil and gas sector. It is estimated that 80% of natural gas leaks in the Upstream sector are caused by corrosion.
- Corrosion costs in this sector are estimated to run into billions of dollars annually. 90% of natural gas pipelines are exposed to H 2 S.
- Advanced monitoring technologies can help detect and assess corrosion risk in real time. 70% of companies in the Upstream sector are using advanced monitoring technologies for corrosion prevention.
- Strategic solutions that can help prevent H2S corrosion include the use of corrosion-resistant materials, changes in facility design, and regular cleaning and maintenance processes.
Success stories
- ExxonMobil
ExxonMobil implemented an advanced H 2 S corrosion monitoring program at its marine production facilities in the Gulf of Mexico. This resulted in a significant reduction in corrosion incidents and an increase in operational efficiency.
- Saudi Aramco
Saudi Aramco, Saudi Arabia’s state oil company, uses predictive modeling technology to predict and prevent corrosion in its oil and gas pipelines, which has led to significant savings.
Conclusions
H 2 S corrosion remains a major challenge in the Upstream oil and gas sector, although advanced monitoring technologies and strategic solutions are improving integrity management and reducing risks.
Investing in these solutions not only protects assets and worker safety, but also contributes to the operational efficiency and sustainability of the industry as a whole. Staying on the cutting edge of these technologies is essential to continued success in the oil and gas sector.
Advanced monitoring technologies can help prevent damage caused by this type of corrosion, but it is important to have a strategic plan that integrates these technologies with other control measures.
Do you want to know more about how to prevent H 2 S corrosion?