Introduction
The prevention and mitigation of corrosion are fundamental in the oil industry for the protection of assets and guarantee the useful life of the facilities. Corrosion is a constant damage in all industrial sectors, which generates several problems at an economic, security and asset conservation level, so it is important to understand this phenomenon in order to mitigate it.
Materials science and engineering have developed studies and great efforts for the prevention and inhibition of corrosive processes. The latest generation inhibitors, paints, coatings, including some with sustainable approaches, to cutting-edge monitoring and control systems, offer more efficient and long-lasting solutions for the protection of oil assets.
The new coatings are stronger and designed to withstand extreme corrosive conditions, while real-time corrosion monitoring techniques enable early detection and proactive response to corrosion.
Corrosion as a factor affecting the oil industry
Crude oil and natural gas are highly corrosive in nature, as are many of their derivatives; they commonly carry a variety of high impurity products that are highly corrosive. To mention an example, oil and gas wells and pipelines are environments with high levels of corrosion due to being in the presence of carbon dioxide, hydrogen sulfide and free water, and are also externally affected by the environmental conditions where they are located.
With the passage of time, industrial companies have experienced accidents and risks due to the phenomenon of corrosion, which has revealed the costly nature of its management. However, they have discovered that implementing the best methods to mitigate it can reduce economic expenses by up to approximately 35%, achieving monetary savings and corrective maintenance downtime, generating reliability in the market, safety in general, and care for the environment. atmosphere.
Among the main factors that contribute to the development of corrosion in the oil industry are highly corrosive environments, high temperatures, humidity, presence of corrosive agents in fluids; Improper selection of materials, design, unsuitable protective coatings, lack of maintenance or non-compliance with maintenance programs, among other causes that increase susceptibility to corrosion, also affect.
That is why, today, innovations in corrosion prevention and mitigation have a positive impact on the protection of the assets that make life in the oil industry. When advanced technologies for corrosion control are implemented, from design, manufacturing, installation, operational use and maintenance, favorable results are achieved for oil companies.
Innovations in the corrosion protection market
Protection against corrosion in this industrial sector focuses on the provision and use of anticorrosive systems and technologies to prevent the degradation of the various metals used in their environment. Corrosion is mitigated through the use of inhibitors, special internal or external coatings, cathodic protection, monitoring, inspection and continuous maintenance or cleaning of the structures, as the case may be.
Keeping the assets belonging to the oil industry protected against corrosion increases the availability of the facilities, prevents oxidation and corrosion of the elements, avoids leaks, operational stoppages and minimizes environmental damage, among other benefits generated by advanced protection techniques Here are some emotional ones:
A. Advanced protective coatings: The continuous research in materials has allowed the creation of advanced coatings with relevant anticorrosive properties, such as nanocomposite coatings, high performance, intelligent, ecological, self-repairing and special ceramics: which offer high corrosion resistance, greater durability and long-term protection of metal substrates.
Along with the development of new protective materials, technological innovations have been achieved in coating application techniques, including thermal spray methods, electrochemical deposition, and controlled immersion techniques, which allow precise and uniform application of coatings. maximizing its protective efficacy.
B. Corrosion inhibitors : New chemical compounds have been developed and produced that act as highly effective corrosion inhibitors. These compounds are used in the form of additives or coatings, forming a protective layer on the metal surface and reducing the rate of corrosion.
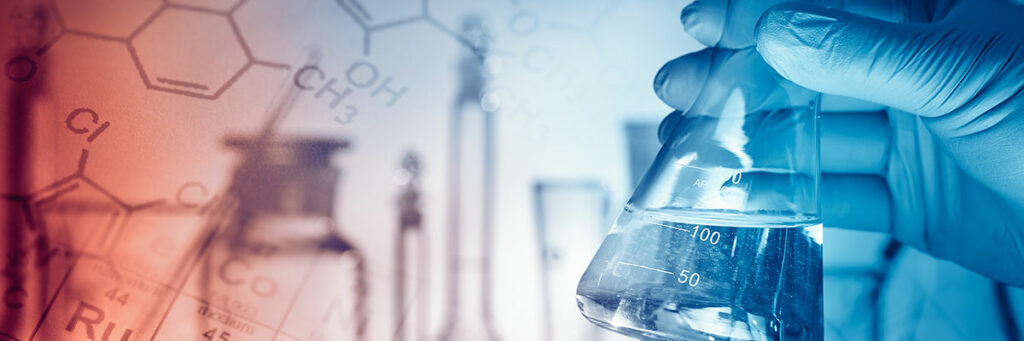
Advances in nanotechnology and intelligent systems have led to the development of autonomous and intelligent corrosion inhibitors. These inhibitors can release anti-corrosion agents in a controlled manner in response to exposed corrosive conditions, improving protection efficiency and reducing the need for frequent interventions1.
C. Corrosion monitoring and control systems: Advances in sensor technology have allowed the creation of devices with greater precision and sensitivity for the early detection of corrosion. These devices monitor changes in conductivity, impedance, or electrochemical potential, providing early warning of the presence of incipient corrosion.
Also, real-time monitoring and data analysis for the prevention of corrosion have had a great contribution in the mitigation and prevention of the corrosive phenomenon, because they allow continuous monitoring of the asset, facilitating decision-making based on data and the implementation of preventive measures before the corrosion process advances.
D. Advanced protection techniques and treatments: Includes cathodic protection where they have developed innovative technologies and an IoT monitoring system. These advances allow precise supervision and protection of the evaluated metallic substrates, avoiding galvanic corrosion.
Also included in this section are high-strength anti-corrosion coatings, enhanced by the development of new resins, polymers and additives that offer superior corrosion protection. These coatings provide an effective barrier between metal and the most aggressive corrosive environments.
E. Digital Solutions for Corrosion and Erosion Monitoring2: The new Plantweb Insight Non-Intrusive Corrosion corrosion monitoring application complements the existing Plantweb Insight line of applications, enabling comprehensive analysis of corrosion and erosion in pipelines. equipment.
If equipped with in-line probes, changes in corrosion risk can be detected in a matter of minutes, allowing sites to take corrective action before damage occurs. The Rosemount 4390 Series of Corrosion and Erosion Transmitters use WirelessHART® for accurate, reliable data and work with in-line probes that measure the corrosive or eroding nature of the fluid to provide early detection of hazards in a facility.
Plantweb Insight Corrosion Applications allow users to access and analyze data from pipe thickness monitoring sensors and online probes from their equipment for advanced real-time analytics to assess risk and impact of corrosion. corrosion and erosion on the asset or plant.
Future prospects for Innovations in corrosion prevention and mitigation
Continuous investment in research is necessary to advance corrosion prevention practices, this includes development of innovative corrosion resistant materials, exploration of new inspection and monitoring techniques, evaluation of the capability of innovative materials and sustainable to meet durability requirements and improve corrosion modeling and prediction. Collaborative efforts between industries, academic institutions and research organizations lead to the development of innovative solutions for the protection of industrial assets.
Research work is being carried out that aims to study the inhibitory effect of benzimidazole derivatives against the corrosion of three different metals (aluminium, copper and mild steel) in an acid solution. The experimental study will be combined with theoretical research using DFT and Monte Carlo simulation methods, to understand how this product can protect three metals against corrosion in the aggressive environment. This study aims to explain the intrinsic properties of molecules (geometry, charges, reactive centers) and can provide important information on the inhibition mechanism 3 .
Innovations in industrial coating techniques continue to evolve as new technologies push the limits of the magnitude of the way industrial assets and equipment can be protected. Trends that contribute to the manufacture, selection and application of coatings are mentioned:
- Artificial Intelligence (AI) and industrial coatings are going hand in hand. Specialized computer software helps coating companies optimize production schedules and product mix for best results. AI speeds duplication of testing and prototyping, while detecting design flaws early on. Intelligent computer vision detects faults, allowing them to be corrected quickly. Analyzes are completed automatically using sensors and smart devices, to improve product quality.
- The collection of data analysis is a result of artificial intelligence to improve the performance of coatings. It is necessary to have robust platforms that collect millions of data points and analyze them correctly to derive ways to improve the coating process. AI makes it possible to collect a wide variety of data, very quickly and in ever-increasing volume. When placed in cloud-based databases, analytics programs process the values and provide us with effective results.
As AI continues to evolve, these software will become less expensive, more robust, and offer even more innovation along with machine learning. This will help the coatings industry determine product life, develop new formulations, and provide synthesis data when placing new products on specific substrates.
- Sustainability – Businesses should aim to conserve energy, reduce waste, mitigate carbon footprints, using renewable materials where possible and minimizing waste. Another aspect that makes industrial coatings ecological is to diversify the products available to companies that need to protect their equipment.
- Nanotechnology continues to advance by leaps and bounds in this sector, some techniques insert metals and ceramics into paint matrices to create UV protection, electrical conduction, better adhesion, color changes, corrosion barriers and self-cleaning properties.
Conclusions
The implementation of innovations in prevention and mitigation of corrosion, are part of the integral strategies in the protection of the assets of the oil industry. The use of advanced paints and coatings, corrosion inhibitors, real-time monitoring systems, and digital solutions have shown valuable results in reducing costs and increasing operational reliability.
Research and development continues to drive progress in this area, with focuses on the application of Artificial Intelligence to optimize processes and improve product quality. Sustainability and nanotechnology are also part of the most outstanding trends for the future of industrial coatings, allowing efficient and environmentally friendly protection.
The commitment to contribute to the mitigation of corrosion in oil assets is mutual, between technological innovation companies and the oil industry. The application of emerging solutions will contribute towards efficient corrosion management. Keeping abreast of trends in this field will ensure continuous improvement and long-term safe operations.
References
- https://tetratec.com/es/blog/corrosion-control-with-treatment-design-additives-and-algorithms/
- https://www.emerson.com/es-es/news/automation/21-03-corrosion-erosion-monitoring
- Nadia Arrousse, Yasmine Fernine, Rajesh Haldharb, Elyor Berdimurodov, Hamza Ichou, Nabil Al-Zaqri, Mohamed Koudad f, Seong-Cheol Kimb, Mustafa Taleb; Environmental Chemical Engineering Journal, Volume 11, Issue 3, June 2023.