Table of Contents
- Introduction
- Titan Features: The Underwater Device
- submarine applications
- What is a submersible like the Titan was?
- What code applies to the manufacture and evaluation of a submersible as a pressure vessel?
- What non-destructive tests are applied to evaluate the conditions of this equipment?
- Inspection and maintenance plans
- Damage mechanisms in a submersible where the hull is made of titanium and carbon fiber like the Titan
Introduction
Oceangate is a company specialized in the exploration and access to remote places in the ocean, with the Titan submersible being one of its main devices that carried out these missions.
For its construction, OceanGate collaborated with specialists from NASA, Boeing and the University of Washington. The submersible has been used in the investigation of several shipwrecks, among which are the Titanic the Lusitania and the Bismarck. In addition, it has played an essential role in exploring life underwater and testing new underwater technologies.
The Titan is lighter and cheaper than any other deep-immersion submersible thanks to the innovative use of modern materials. It has a real-time hull health monitoring (RTM) system, which allows you to evaluate its integrity during each dive. This onboard health analysis monitoring system provides early warning detection for the pilot in plenty of time to stop the descent and safely return to the surface.
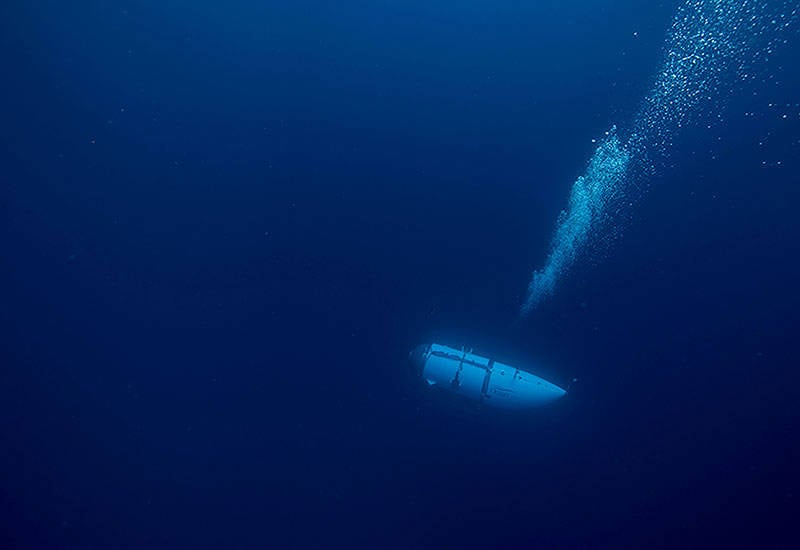
This submarine is equipped with a patented integrated platform for launch and recovery, making it easy to operate in different sea states using a local ship of appropriate size for the project. Its technical specifications are as follows:
Titan Features: The Underwater Device
- Operating depth: Up to 4,000 meters (13,123 feet), which allows exploring marine regions of great scientific and archaeological interest.
- Crewed capacity: For a crew of up to five people, including (1 pilots + 4 crew}, which facilitates real-time investigations and on-site decision-making.
- Resistant structure: Constructed of high resistance materials such as Titanium and carbon fiber to withstand the extreme pressure in the ocean depths.
- Lighting system and cameras: Underwater lights and high-definition cameras that allow a clear and detailed visualization of the underwater environment, which is crucial for exploration and documentation tasks.
- Total dimensions: 670 cm x 280 cm x 250 cm.
- Weight: 10,432 kg, Payload: 685 kg, Speed: 3 knots
- Propulsion: Four Innerspace 1002 electric thrusters
- Life support: 96 hours for 5 crew
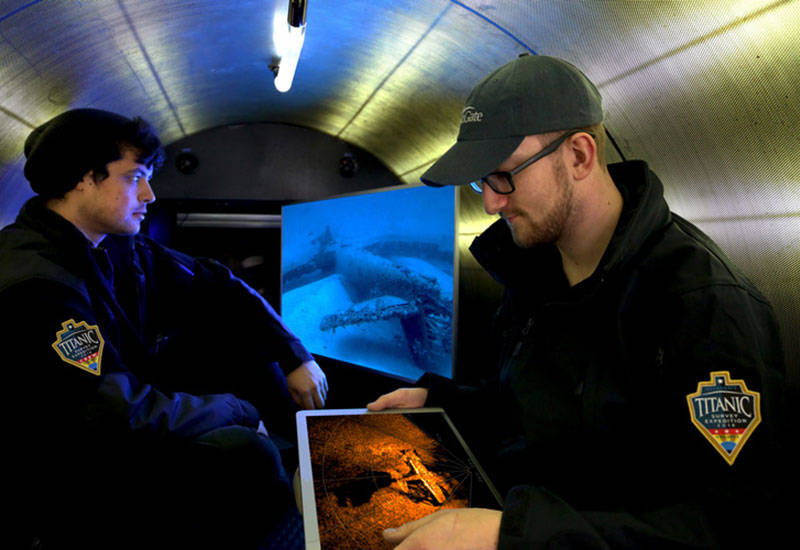
submarine applications
Its main applications include underwater research and exploration, including:
- Shipwreck exploration: Specifically historical shipwrecks, collect data and samples that help to better understand maritime and archaeological history.
- Scientific Studies: Allows scientists and oceanographers to conduct research in the deep ocean, collect water and sediment samples, study marine life, and collect valuable scientific data.
- Filming and documentation missions: They are used in the production of underwater documentaries and films, providing impressive images and recordings of marine life and underwater landscapes.
What is a submersible like the Titan was?
It is considered for its design and manufacture, as a pressure vessel. This is because, when submerged in the water, it is subjected to an external pressure greater than the normal atmospheric pressure at sea level.
When a submersible descends to underwater depths, the water pressure increases due to the water column above it. Hydrostatic pressure increases by approximately 1 atmosphere (equivalent to 1 bar or 14.7 psi) for every 10 meters of depth. This means that, at greater depths, the pressure to which the submersible is exposed increases significantly.
To ensure the safety and structural integrity of the submersible and protect its occupants, design and construction standards must be followed that consider the pressures to which it will be exposed. This includes the use of strong materials and proper manufacturing techniques to withstand external pressure and maintain a safe environment inside the submersible.
In addition, rigorous testing and quality control must be carried out to ensure that the submersible meets design requirements and can withstand the pressures expected during its operation.
What code applies to the manufacture and evaluation of a submersible as a pressure vessel?
The applicable code for the manufacture and evaluation of a submersible as a pressure vessel depends on the country and the specific regulations that govern the construction and operation of this type of equipment. Here are some widely recognized industry codes and standards:
- ASME Boiler and Pressure Vessel Code: This is a widely used code in North America and other countries. It applies to the manufacture and evaluation of pressure vessels, including manned submarines.
- ISO 12215: This international standard provides guidelines for the design, construction and evaluation of marine vessels, including submersible vessels and underwater vehicles.
- ABS (American Bureau of Shipping) Rules for Building and Classing Underwater Vehicles, Systems and Hyperbaric Facilities: These rules establish the requirements for the construction and classification of underwater vehicles, underwater systems and hyperbaric facilities.
- Lloyd’s Register Rules: Lloyd’s Register is a globally recognized classification organization and has specific rules for the construction and classification of manned and unmanned underwater vehicles.
It is important to note that these are just a few examples of the codes and standards used in the industry. The selection of the applicable code may depend on factors such as geographic location, the type of submersible, its size, and its intended use. Companies and organizations that design and manufacture submersibles typically follow relevant codes and standards to ensure the safety, quality, and regulatory compliance of their products.
It is recommended that, when designing and building a submersible, you consult the applicable regulations and codes in the specific region where the operation will take place, and work with engineers and subject matter experts to ensure compliance with safety and quality standards. required.
What non-destructive tests are applied to evaluate the conditions of this equipment?
To evaluate the conditions of a submersible as a pressure vessel, several Non-Destructive Tests (END) are applied, which allow inspecting and detecting possible defects or damage without compromising the integrity of the equipment. Some of the commonly used non-destructive tests are the following:
- Visual test: It is the direct visual inspection of the submarine to detect any signs of damage, corrosion, cracks or visible deformations.
- Liquid Penetrant Test: A liquid penetrant is applied to the surface of the device that penetrates any crack or porosity. Then, a developer is applied that highlights the indications of the penetrating liquid, allowing the detection of surface defects.
- Magnetic particle test: A magnetic field is applied and then powdered magnetic particles are sprayed or scattered. If there are any cracks or defects near the surface, magnetic particles will collect in those areas, allowing their detection.
- Ultrasound test: Ultrasound waves are used to evaluate the internal structure. An ultrasound pulse is emitted and the time it takes to be reflected from the internal interfaces of the equipment is recorded. This provides information about the thickness of the material, the presence of cracks or other internal defects.
- Radiographic testing: Penetrating radiation, such as X-rays or gamma rays, is used to obtain images of internal sections. Denser areas or discontinuities within the material will appear as shadows on the radiographic image.
Inspection and maintenance plans
These plans may vary according to the regulations and standards applicable in each country or industry. However, some general aspects that are considered in inspection and maintenance are the following:
- Periodic Inspections: Regular visual inspections are made to detect signs of damage, corrosion or deformation in the submersible.
- Pressure tests: They are carried out to verify the resistance and tightness of the submersible. This can include hydrostatic testing where the submersible is filled with water or another liquid under pressure and checked for leaks.
- NDT Testing: Periodic non-destructive tests, such as those mentioned above, are performed to detect hidden defects or damage in the submarine.
- Preventive maintenance: Regular maintenance tasks, such as cleaning, lubrication and replacement of worn components, are carried out to ensure the proper functioning of the submersible.
- Inspection and maintenance record: A detailed record is kept of all the inspections carried out, the results obtained and the maintenance actions carried out. This allows for proper condition monitoring and scheduling of future inspections or maintenance tasks.
It is important to note that inspection and maintenance plans may vary depending on the specific application of the submersible and local regulations, so it is always necessary to consult the relevant regulations and standards for each particular case.
Additionally, in the manned submersibles industry, other equipment components must be complemented and tested to ensure compliance with safety standards and their proper functioning. These tests could be:
- Pressure tests: They are scheduled periodically to evaluate the resistance of the submersible at operating depths and ensure that it meets established safety requirements.
- Systems and equipment tests: Tests are carried out on electrical systems, communication systems, backup systems and other equipment to ensure their correct operation and availability in case of emergency.
- Buoyancy and Ballast Control Tests: Tests are carried out to verify the buoyancy, stability and ballast control capabilities of the submersible under different load conditions and depths.
- Instrument maintenance and calibration: Periodic maintenance tasks are carried out, as well as the calibration of the instruments and sensors used on board the submersible.
- Functionality test of the equipment’s propulsion system and engines.
The frequency of these tests and checks may vary and is determined by factors such as regulations, manufacturer’s recommendations, accumulated hours of operation, and the maintenance policy of the company that owns the submersible.
Damage mechanisms in a submersible where the hull is made of titanium and carbon fiber like the Titan
In a titanium and carbon fiber hulled submersible, the damage mechanisms may be similar to conventional metallurgy submersibles, but the use of these materials may provide greater strength and protection against some of these damage mechanisms. Here are some of the common damage mechanisms on a titanium and carbon fiber hulled submersible:
- Collision: Although titanium and carbon fiber are strong materials, a violent collision with underwater objects or with other vessels can cause hull damage such as cracks, deformation or breakage, especially if the force of the impact is significant.
- Structural Fatigue: Although titanium and carbon fiber are strong, lightweight materials, they are still subject to structural fatigue from repeated stress and continuous exposure to the stresses of the underwater environment. Fatigue can cause cracks or failures in the hull structure over time, especially in the areas subjected to the greatest stress, which can lead to implosions in very deep water or water ingress at shallow depths.
- Corrosion: Titanium is known for its excellent resistance to corrosion in marine environments, making it an ideal material for underwater applications. However, galvanic corrosion is possible in areas where titanium connects with other metals or where there is damage to the protective coating. Carbon fiber, meanwhile, is inherently resistant to corrosion.
- Systems and Equipment Failures: Although the titanium and carbon fiber hull provides a solid structure, systems and equipment aboard the sub can fail due to mechanical, electrical, or other problems. These failures may be independent of the hull material and may affect the operability and safety of the submersible.
- Water Infiltration: The titanium and carbon fiber hull should provide an effective barrier against water infiltration. However, problems can arise with joints, seams or non-hull components, which could allow unwanted water ingress into the submersible. It is important to maintain proper maintenance to ensure tightness.
- Explosion or Fire Events: Although titanium and carbon fiber have good resistance to heat and fire, explosion or fire events can occur due to system malfunctions, improper fuel storage, or electrical equipment failure. These events can damage the systems and equipment on board the submersible, regardless of the hull material.
In conclusion, the submersible Titan of the Oceangate company, despite its revolutionary features and its ability to conduct research in the deep ocean, failed to unlock all the secrets of the deep sea, let alone reach its goal of observing the wreckage of the Titanic.
Although its rugged design, manned capability, and camera and lighting system made it possible to explore and document the underwater environment, the Titan faced challenges in terms of the extreme pressure it was exposed to and ultimately imploded. We will have to wait for the investigations that begin from this date to determine for sure the causes of such an unfortunate accident in the depths of the ocean that cost the lives of 5 people.
Own source