Table of Contents
- CUI detection methods
- Mechanisms and factors of Corrosion Under Insulation
- Standards (NACE SP0198-2010), applications and limitations
- Advances in formulations: Aerogel technology
- Anticorrosive coatings: Innovations and applications
- Technical recommendations
- Conclusions
- References
- Frequently asked questions (FAQs) on corrosion under insulation
Corrosion under insulation (CUI) represents one of the most significant challenges to the integrity of industrial equipment. This insidious phenomenon compromises the operational safety and service life of pipelines, storage tanks and other critical components in industrial environments. Effective CUI management requires a comprehensive approach that combines proper material selection, appropriate coating systems, advanced inspection techniques and structured preventive maintenance programs.
Protective coatings have undergone a radical transformation in recent years, driven by advances in nanotechnology, smart materials and self-repairing systems. The U.S. nano-coatings market reached $1.8 billion in 2024, projected to grow at a 16.1% CAGR through 2034, reflecting the increasing demand for advanced protective solutions.
The evolution of protective coatings and the development of self-healing materials mark a considerable transformation in surface engineering. These technologies offer increased durability, and optimize operating and environmental costs by reducing the frequency of maintenance.
CUI detection methods
Accurate detection of corrosion under insulation is critical to mitigate its devastating effects. The following are the most common methods used in the industry to identify and evaluate the presence of CUI:
- “Brute Force” method: This traditional approach involves the physical removal of insulation to visually inspect the condition of the metal substrate. Although effective, it is costly and disruptive to operations.
- Conventional and Non-Conventional Radiography: Conventional radiography provides detailed images of the internal condition of equipment, while non-conventional techniques such as advanced digital radiography offer better resolution and speed of inspection.
- Pulsed Eddy Current: Used to detect changes in metal thickness and possible areas of corrosion without the need to remove insulation, pulsed eddy currents are ideal for fast and accurate inspections.
- Guided Wave Ultrasonics: This technique allows the condition of large areas of piping and equipment to be evaluated without removing the insulation, using ultrasonic waves that travel along the internal surface of the equipment.
Each method has advantages and limitations that must be considered depending on the specific characteristics of the industrial environment and inspection requirements.
Mechanisms and factors of Corrosion Under Insulation
Corrosion under insulation (CUI) is the result of multiple interrelated factors that compromise the integrity of industrial equipment. The following explores the main mechanisms and factors that contribute to CUI:
- Moisture and contaminant infiltration:
- Thermal insulation can be permeable to moisture, allowing water and contaminants to penetrate to the metal surface. The presence of chlorides, sulfates, and other corrosive agents accelerates the corrosion process, especially in harsh industrial environments.
- Defects in insulation and sealing:
- Imperfections such as cracks, discontinuities, and failures in sealing systems facilitate the retention of moisture near the metal surface.
- These defects can result from improper installation, deterioration of insulation over time or damage during operations.
- Thermal cycling and condensation:
- Repeated temperature changes can cause condensation within the insulation, creating a moist environment conducive to corrosion.
- Material expansion and contraction cycles can further aggravate the penetration of corrosive agents.
- Material compatibility:
- Improper choice of materials for insulation and protective coatings can exacerbate corrosion.
- It is important to select materials that are compatible with the operating environment and capable of resisting the moisture and chemicals present.
Each of these factors plays a critical role in the formation and propagation of corrosion under insulation, underscoring the importance of effective detection and mitigation strategies.
Standards (NACE SP0198-2010), applications and limitations
The industry has developed specific regulations to address corrosion under insulation (CUI) and establish best practices for its prevention and control. One of the most recognized standards is NACE SP0198-2010, entitled “Control of corrosion under thermal insulation and fireproofing materials: a systems approach”. The main aspects of this standard are highlighted below:
- Systemic approach: The NACE SP0198-2010 standard adopts a comprehensive approach to CUI management, considering not only the selection of protective coatings, but also periodic inspection, risk assessment and maintenance planning.
- Technology update: Reflects the most recent advances in nondestructive inspection (NDT) technology and methodologies, ensuring that recommended practices are aligned with industry innovations.
- Coating guidelines: Provides clear guidelines for the selection and application of suitable protective coatings under thermal insulation conditions, ensuring effective corrosion protection.
- Global applicability: Although initially developed for the petroleum and petrochemical industry, the NACE SP0198-2010 standard has been widely adopted in other industrial sectors facing similar challenges with CUI.
This standard plays a key role in promoting safe and effective practices to mitigate the risks associated with corrosion under insulation, ensuring the structural and operational integrity of industrial equipment.
Efficiency in insulation systems: ASTM Protocols
Conventional protocols employ standardized ASTM methodologies to quantify thermal performance, expressed by the coefficient of thermal conductivity (“k” value). Two fundamental standards define the evaluation parameters: Primary evaluation protocols include:
- ASTM C-177 (Method C177-97)
Application: steady-state heat flow measurements
Equipment: protected hot plate apparatus
Function: Determination of thermal transmission properties by control of thermal gradients
- ASTM C-518 (Method C518-98)
Application: characterization of steady-state thermal properties
Equipment: heat flow meter
Advantage: Faster results compared to C-177
Techniques in insulating coatings: Limitations
ASTM C-177 protocol requires specimens 25.4-50.8 mm thick. This specification presents significant challenges for insulating coatings:
- Economic limitation: Achieving 25.4 mm implies approximately 50 consecutive applications of 0.50 mm.
- Technical feasibility: Multi-layer application processes exponentially increase operating costs.
- Industrial feasibility: Application of thicknesses greater than 25.4 mm is economically unfeasible.
Specific applications and limitations
Insulating coatings demonstrate proven efficacy in:
- Thermal radiation mitigation: radiant heat transfer control.
- Personnel protection: thermal barriers for occupational safety.
However, their mass implementation is restricted by inherent application limitations at high thicknesses.
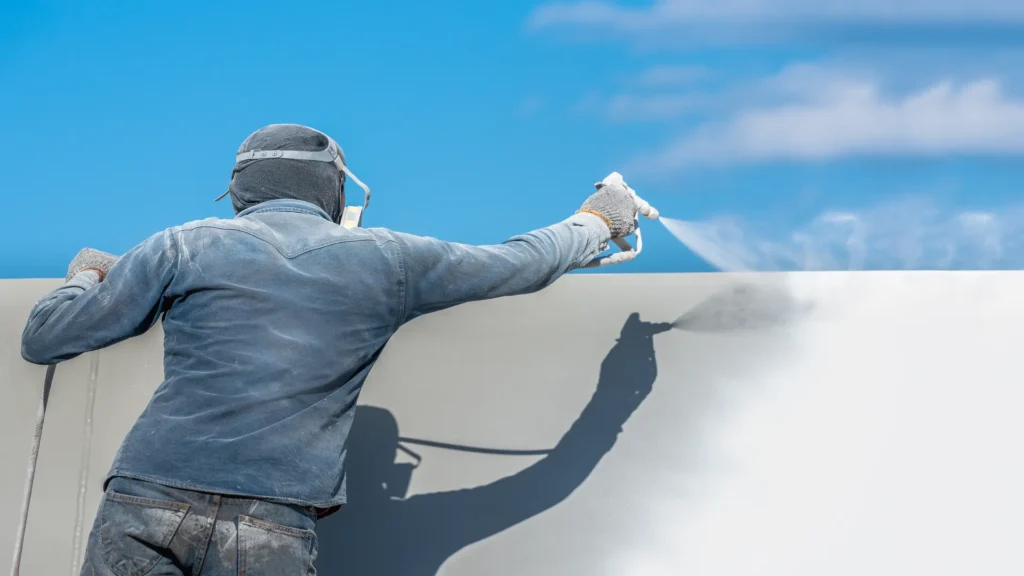
Advances in formulations: Aerogel technology
Aerogels have emerged as one of the most promising technologies in the development of advanced anticorrosion coatings, thanks to their nanoporous structure, low density, high surface area and exceptional thermal properties. Originally developed for aerospace and thermal insulation applications, their incorporation into functional coatings has marked a milestone in the protection of metals exposed to harsh environments, especially in sectors such as oil and gas, marine infrastructure and power generation.
In the field of corrosion protection, silica aerogels and metal oxides (such as TiO₂ or Al₂O₃) are being used as additives or matrices for organic-inorganic hybrid coatings. Their main function in these formulations is to create a highly tortuous physical barrier, which hinders the passage of water, oxygen and corrosive agents to the metal substrate. This property significantly reduces the permeability of the coating without compromising its flexibility and adhesion.
In addition, aerogels can be chemically functionalized to improve their compatibility with epoxy, polyurethane or siloxane resins, achieving a homogeneous dispersion that enhances the durability of the coating. Their inclusion also allows the development of thinner and lighter coatings, maintaining excellent anticorrosion efficiency and, in many cases, providing additional properties such as thermal resistance, hydrophobic properties or even self-repair capacity when integrated with microcapsules or smart inhibitors.
Current research is focused on optimizing the mechanical stability of aerogels, overcoming challenges in their industrial scalability and reducing production costs. However, commercial prototypes and field studies have already demonstrated significant improvements in the lifetime of coatings subjected to salt spray, thermal cycling and exposure to marine environments.
Aerogel technology represents, therefore, a substantial evolution in next-generation anticorrosion formulations, offering more sustainable, efficient solutions adapted to the extreme requirements of modern industry. Among its most outstanding features are the following:
- Material innovation: Recent developments incorporate aerogels as the main insulating matrix.
- Technical definition: Ultra-lightweight synthetic porous materials derived from gels, where the liquid component has been replaced by gas without significant structural collapse
- Characteristic properties: Density: Extremely low (typically <0.1 g/cm³), Thermal conductivity: Exceptionally low values (<0.020 W/m-K), Porosity: Nano-porous structure with >90% air content
- Operational advantages: Superior thermal efficiency: Thermal conductivities comparable to conventional systems at lower thicknesses. Improved applicability: Significant reduction of required thicknesses. Economic feasibility: Fewer applications needed to achieve target thermal performance.
Anticorrosive coatings: Innovations and applications
Nowadays, protective coatings play an essential role in the preservation of infrastructures, machinery and industrial components against corrosion, mechanical wear and aggressive environmental factors.
At the same time, advances in the technology of self-repairing materials are revolutionizing maintenance systems by introducing intelligent solutions that autonomously extend the service life of materials.
This section explores the most relevant types of protective coatings used in industry and presents the latest innovations in self-healing systems, highlighting their applications and benefits within sectors such as aerospace, energy, construction and electronics.
1. Protective coatings: Function and classification: Industrial protective coatings are systems applied on metallic, ceramic or polymeric surfaces to prevent their deterioration. These coatings can be classified as follows:
- Metallic coatings:
- Galvanized: Zinc coating applied to steel for corrosion protection.
- Chromium plating and nickel plating: Improve aesthetics, surface hardness and chemical resistance.
- Organic coatings:
- Epoxy and polyurethane paints: Resistant to abrasion and chemical products.
- Powder coatings: Excellent mechanical properties and aesthetic finish.
- Ceramic coatings
- Used in turbines, engines and high temperature environments for their thermal and abrasive resistance.
- Polymeric coatings
- Materials such as PTFE (Teflon) or silicone offer non-stick and low friction properties.
2. Innovations in self-repairing materials: Intelligent self-repairing materials represent a key innovation to reduce maintenance costs and improve structural reliability. These systems are capable of automatically detecting, reacting to and repairing minor damage.
- Micro-capsule polymers
- Contain repair agents that are released when a crack occurs.
- Widely used in self-repairing anti-corrosion coatings.
- Polymers with reversible bonds
- Incorporate dynamic chemical bonds that allow multiple repairs by external stimuli (temperature, light or pH).
- Self-repairing metals
- Experimental stage. Some metals can close microcracks by atomic diffusion under specific conditions.
- Integrated iIntelligent systems
- Embedded sensors that detect failures and activate self-healing mechanisms.
- Applications in aerospace, defense and offshore structures.
3. Current industrial applications
- Marine infrastructures: Self-repairing coatings to combat saltwater corrosion.
- Aerospace industry: Composite materials with sensors that detect and repair micro-fractures.
- Electronics and consumer electronics: Coatings for displays with self-healing thermal properties.
As research progresses, self-repairing systems are expected to become more widely integrated into critical sectors such as transportation, renewable energy and advanced manufacturing. Adopting these innovative solutions will be key to building more resilient, sustainable and efficient infrastructures in the future.
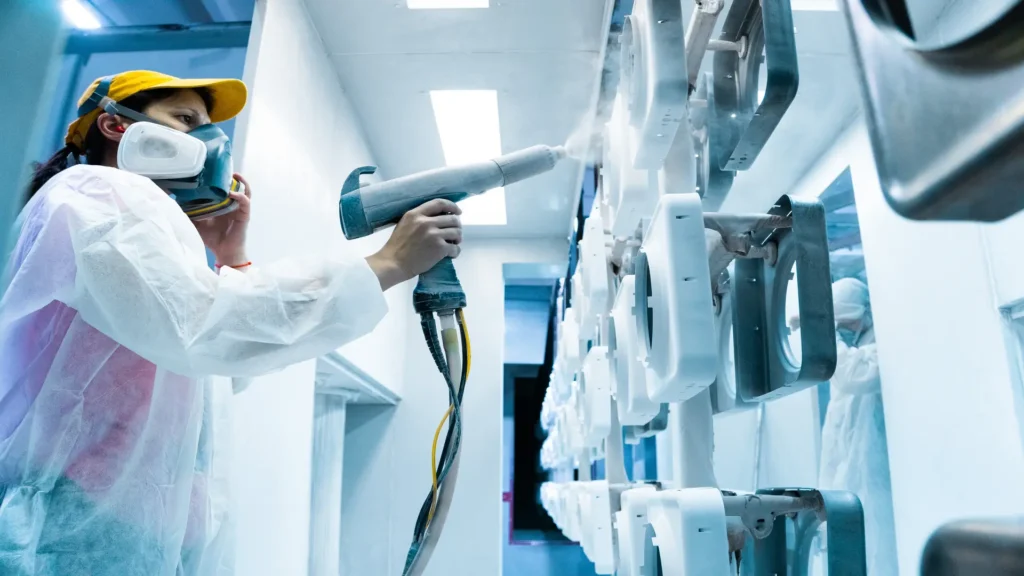
Technical recommendations
- Implement RBI (Risk-Based Inspection): RBI methodologies can be used effectively to mitigate the risk of CUI.
- Optimize inspection regimes: Optimize inspection regimes for more effective detection of CUI.
- Preventive maintenance: Any strategy should be structured, robust and appropriate for inspecting piping, vessels, towers and other insulated components.
Conclusions
Insulating coatings have been developed to solve both safety and technical problems, such as protecting personnel, protecting against condensation and freezing, keeping the process stable, minimizing evaporative losses and reducing radiant heat gain.
Organic coatings are one of the most widely used strategies to protect metals against corrosion. They can be applied in different ways, such as dipping, spraying, electrophoresis, casting, painting or flow coating.
They exhibit great flexibility in material design and excellent value for money. In addition, self-healing has evolved as a new research topic for protective organic coatings in recent years. Sensitive materials play a crucial role in this new research field. Such knowledge would enable the design of optimized coatings for specific applications.
References
- https://www.pcimag.com/coatings-conference/agenda
- https://content.ampp.org/corrosion/article-abstract/
- https://content.ampp.org/corrosion/article-abstract/
- https://insulation.org/io/articles/insulation-materials-guide/
- https://industrial.sherwin-williams.com/emeai/gb/en/corrosion-under-insulation.html
https://advanced.onlinelibrary.wiley.com/doi/epdf/10.1002/adma.202300101
Frequently asked questions (FAQs) on corrosion under insulation
What conditions favor the development of CUI?
CUI (Corrosion Under Insulation) refers to the occurrence of corrosion caused by moisture on the external surface of insulated equipment. Conditions that favor its development include: Environmental factors: exposure to frequent atmospheric steam and condensation, contaminants in the insulation or atmosphere (such as chlorides and sulfides) that dissolve in water, repetitive moisture-dryness cycles, water ingress through damaged seals or deteriorated vapor barriers. Critical temperature ranges: Carbon steel: -4°C (25°F) to 149°C (300°F) presents the greatest risk of CUI, Maximum risk zone: 77°C (140°F) to 110°C (248°F), Stainless steel: 80-130°C (176-280°F) for stress corrosion cracking.
What types of coatings help prevent it?
Barrier systems: Robust coating/paint systems backed by well-maintained insulation, seals and vapor barriers to prevent water ingress, thick epoxy coatings (u003e300 microns), thermally sprayed aluminum (TSA) systems.u003cbru003eAdvanced technologies: Nanostructured ceramic coatings, self-repairing damage-responsive systems, hybrid coatings with enhanced anti-corrosion properties
How can it be detected without removing insulation?
Certified technicians use non-destructive testing (NDT) technology to identify and locate CUI damage. Primary methods include:u003cbru003eu003cbru003eAdvanced NDT techniques: Pulsed Eddy Current (PEC), real-time radiography (RTR), profile radiography, computed radiography and digital detector arrays, infrared thermography, neutron backscatter analysis and radiography, profile radiography, point ultrasonic readings and real-time X-ray.u003cbru003eu003cbru003eEmerging technologies: Researchers in Norway are using machine learning and ultrasound to detect pitting corrosion in steel, automated radiographic testing (ART) as a preferred method to detect corrosion defects in pipelines.
What materials are most vulnerable to this corrosion?
Carbon steel: Services operating from freezing temperatures to 300°F, risk range: -4°C to +175°C (highest risk area: +60°C to +120°C), carbon steel piping systems, including those insulated for personnel protection, operating between -4°C and 120°Cu003cbru003eu003cbru003eStainless steel: Vulnerable to stress corrosion cracking from external chlorides, critical range: 80-130°C (176-280°F), increased susceptibility in the presence of chlorides and humid environmentsu003cbru003eu003cbru003eVulnerability factors: equipment operating continuously below -4°C usually remains corrosion free, CUI is particularly aggressive where operating temperatures cause condensation and frequent re-evaporation of atmospheric moisture.