Table of Contents
- Importance of AWS D17.1 in aerospace welding
- A standard forged in precision and trust
- Scope and applicability in aerospace projects
- NDT methods required for aerospace welds
- From plan to flight: quality control in aerostructures
- Challenges and future of aerospace fusion welding
- Final thoughts: Why AWS D17.1 is more than just welding code
- References
In aerospace engineering, where precision determines not just performance but survival, the integrity of every weld becomes non-negotiable. Behind every successful launch, long-haul flight, or deep-space probe lies a foundation of disciplined procedures, thorough inspections, and well-documented welding protocols.
At the heart of this safety-first culture is AWS D17.1, the welding standard that governs fusion welding for aerospace components, issued by the American Welding Society. While invisible to most, this code shapes how materials are joined, how quality is verified, and how aerospace systems earn their reliability.
This article explores AWS D17.1 from its technical backbone to its human impact. From WPS/PQR/WPQ protocols to non-destructive testing and material-specific requirements—especially for nickel alloys and titanium, we’ll break down why this standard is not just a technical guideline, but a blueprint for aerospace trust.
Importance of AWS D17.1 in aerospace welding
In aerospace engineering, precision is not a luxury, it’s a necessity. The margins for error are razor-thin, and a single flaw in a weld can compromise entire missions or put lives at risk. This is why welding standards in aviation aren’t just technical documents, they are lifelines. AWS D17.1 stands as a cornerstone in this reality, defining how fusion welds must be executed, qualified, and inspected across the aerospace sector.
Safety in the skies begins with the weld
Welds rarely make headlines, but they’re everywhere: in aircraft fuselages, turbine housings, engine mounts, satellite frames. These quiet joints bear the load of extreme temperatures, high stress, and flight-induced vibration. And when they fail, the consequences are catastrophic.
The 1980 DC-10 crash near Chicago, for example, was traced back to a poorly executed engine pylon repair, one that ignored fundamental welding guidelines. In space missions, microscopic welding defects have caused mission delays and even the loss of satellites. These failures are not just technical lapses, they are reminders of the silent power of a weld done right, or wrong.
A standard forged in precision and trust
First published in 1999 by the American Welding Society (AWS), AWS D17.1 was developed in response to the growing complexity of aerospace materials and designs. It replaced the older military specifications and introduced a unified framework to govern fusion welding across both civilian and military aerospace components.
Over time, D17.1 has evolved with the industry. Today, it applies globally across aircraft, spacecraft, and UAV manufacturing. Its criteria guide everything from welder qualification and WPS development to inspection classes and material-specific rules for nickel alloys, titanium, and high-performance composites. What makes D17.1 stand out is not just its rigor, but the trust it represents. In every compliant weld lies a commitment to excellence, and in aerospace, that commitment saves lives.
Understanding the core of AWS D17.1
The AWS D17.1 standard is more than a checklist, it’s a technical framework that defines how aerospace fusion welds should be planned, executed, and evaluated to ensure safety, repeatability, and compliance. Its detailed provisions cover design requirements, welder qualifications, inspection protocols, and acceptable criteria across various flight-critical components.
To explore the code structure and key sections in detail, check out this AWS D17.1 Code Clinic Demo: Source: American Welding Society (AWS).
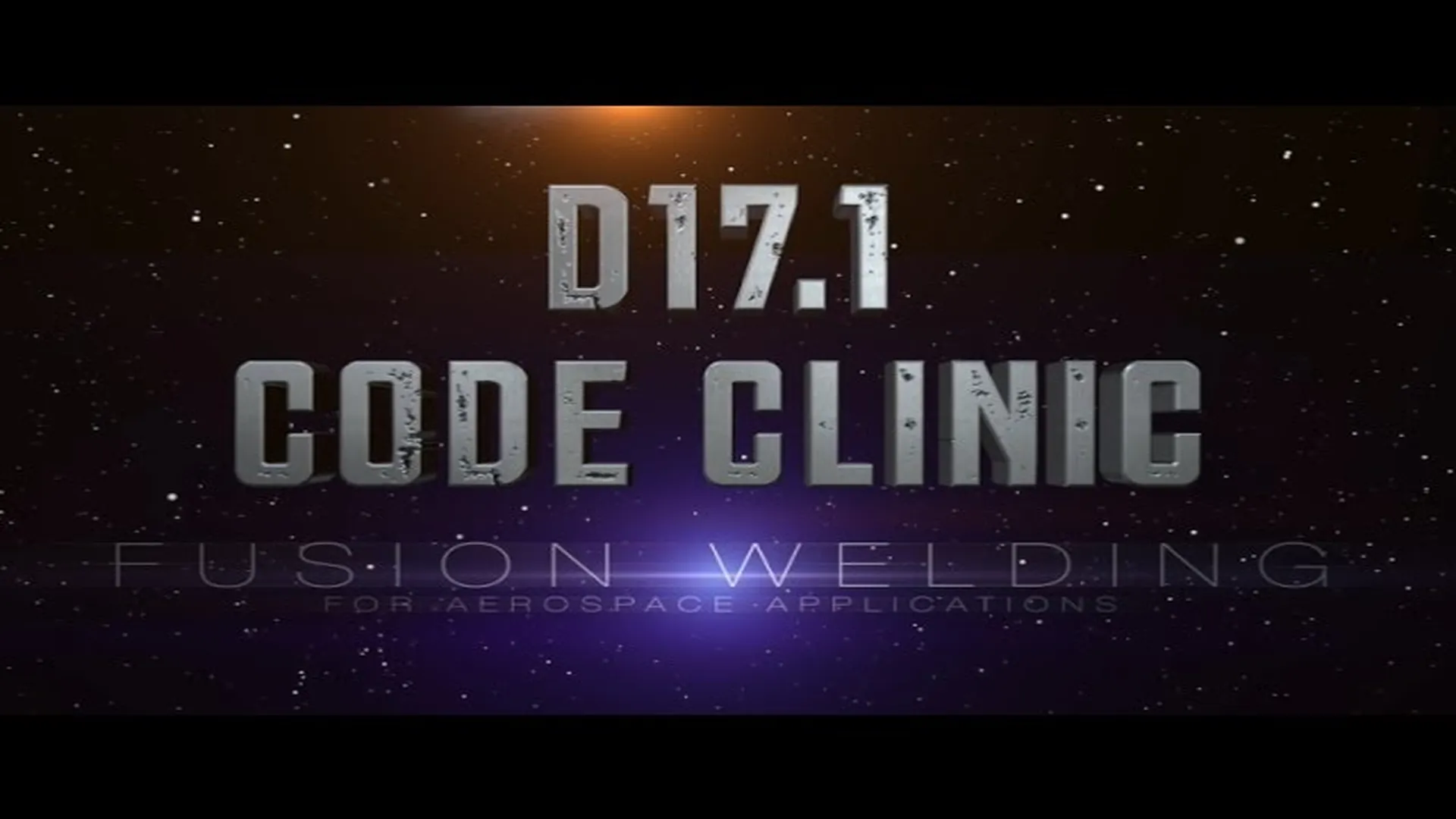
D17.1 Code Clinic Demo.
Video included for illustrative purposes. All credit belongs to the original YouTube creator: American Welding Society (AWS).
Scope and applicability in aerospace projects
AWS D17.1 applies to both primary and secondary structural components in civilian and military aircraft, spacecraft, and unmanned aerial vehicles (UAVs). Primary structures include fuselage sections, engine mounts, and wing spars—components where failure is catastrophic. Secondary structures may not be as critical to immediate flight safety but still demand strict quality standards.
The D17.1M edition (metric version) aligns the standard with global practices and enables harmonization with other codes such as AS9100, NADCAP requirements, and legacy military specifications. This makes it adaptable to internmational supply chains and ensures uniformity in complex, multi-vendor aerospace programs.
Base materials: nickel alloys and Titanium
The standard places special attention on nickel-based alloys and titanium, materials commonly used in jet engines, cryogenic systems, and high-temperature aerospace environments. These materials offer excellent strength-to-weight ratios, corrosion resistance, and thermal stability—but they also present welding challenges.
Titanium is highly reactive at high temperatures, requiring inert gas shielding to prevent contamination. Nickel alloys can suffer from hot cracking and segregation during fusion welding. AWS D17.1 outlines specific pre-weld preparation, filler material compatibility, and post-weld inspection procedures for these critical metals, ensuring structural reliability under extreme conditions.
Specifications and requirements for WPS qualification
At the core of AWS D17.1 lies the principle of repeatability and documentation. Every weld must be reproducible, traceable, and verifiable. This is achieved through the development and qualification of WPS, PQR, and WPQ, and enforced through rigorous inspection and testing.
WPS, PQR, and WPQ: ensuring repeatability
- WPS (Welding Procedure Specification) defines how a weld must be performed: joint type, filler, position, parameters, etc.
- PQR (Procedure Qualification Record) is the document that records the test results proving the WPS produces acceptable welds.
- WPQ (Welder Performance Qualification) certifies that the welder can produce quality welds following the WPS.
Together, these three documents form the technical chain of trust required by D17.1.

NDT methods required for aerospace welds
AWS D17.1 mandates non-destructive testing (NDT) based on the criticality of the weld and its classification. Common methods include:
- Ultrasonic testing (UT)
- Radiographic testing (RT)
- Magnetic particle testing (MT)
- Liquid penetrant testing (PT)
Each method is selected based on material type, weld geometry, and required defect sensitivity.
Inspection Classes A, B, and C Explained
- Class A: Highest criticality; zero tolerance for major defects. Typically used in pressure-critical or load-bearing structures.
- Class B: Moderate criticality; limited defect acceptance.
- Class C: Non-critical parts; broader tolerance range.
This classification ensures that inspection effort matches the consequence of failure.
From plan to flight: quality control in aerostructures
From concept to takeoff, the structural integrity of an aerospace system is never accidental—it’s the result of meticulously applied standards like AWS D17.1. This code does more than govern welds; it builds the bridge between design assumptions and operational reality.
How AWS D17.1 supports design integrity
Every weld influences stress distribution, fatigue life, and failure modes. AWS D17.1 ensures that fusion welds meet the exact mechanical properties anticipated in the design phase. By standardizing welding processes, inspection classes, and material specifications, it aligns manufacturing with the structural analysis behind flight systems.
In systems where failure is not an option—such as aircraft wings, engine mounts, or spaceframe connections, D17.1 reinforces the design intent through verified weld quality. It minimizes variability, controls distortion, and ensures that every joint performs exactly as the engineers intended.
Training and certification of aerospace welders
The best aerospace designs are worthless without skilled professionals executing the welds. AWS D17.1 sets strict criteria for welder qualification, requiring proficiency tests under real-world conditions, documented via WPQ (Welder Performance Qualification).
This qualification framework ensures that certified welders can repeat high-integrity joints, even in exotic materials like titanium or Inconel. The result is a workforce of precision welders, capable of meeting the demanding tolerances and inspection standards of aerospace manufacturing. Training programs aligned with D17.1 are not just about compliance, they build a human infrastructure of reliability.
Challenges and future of aerospace fusion welding
As aerospace innovation accelerates, welding standards like AWS D17.1 face a new frontier. From hybrid structures to AI-integrated inspections, the next generation of aerospace systems will demand deeper adaptability and strategic foresight from welding codes.
- Additive Manufacturing and New Joint Designs: Is revolutionizing how parts are built—layer by layer, with internal geometries never possible through traditional means. This disrupts conventional welding assumptions: joints may now involve composite-metal interfaces, hollow lattices, or curved fusion zones. D17.1 will need to evolve to address:
- Qualification of AM-welded interfaces.
- New criteria for dissimilar metal fusion.
- Hybrid structures combining printed and welded elements.
This transition will require collaboration between code committees, industry leaders, and material scientists to ensure standards remain relevant and enforceable.
- Automation, robotics, and real time quality monitoring: Welding robots equipped with adaptive sensors, vision systems, and machine learning algorithms are now capable of making in-process adjustments. AWS D17.1 must increasingly incorporate guidelines for digital traceability, automated inspection, and data-driven acceptance criteria.
The future of aerospace welding is not only precision, but predictability and real-time validation. Integrating these technologies into the standard will be essential to maintain safety in an era of high complexity and rapid production cycles.
Final thoughts: Why AWS D17.1 is more than just welding code
As aerospace systems grow more complex and ambitious, the need for precision, traceability, and confidence grows in parallel. AWS D17.1 isn’t simply a checklist or a technical guide, it’s a guardian of flight. It ensures that every fusion weld joining titanium, nickel alloys, or aluminum is not just strong, but predictably reliable under the most extreme conditions imaginable.
Behind every successful mission, behind every passenger seated at 35,000 feet, lies a silent infrastructure of codes and craftsmanship. AWS D17.1 represents more than metallurgical standards, it reflects a culture of accountability, foresight, and human excellence. Every weld made under its rules carries the weight of responsibility and the promise of safety.
For engineers, inspectors and industry leaders, adopting D17.1 is not just about meeting a standard, it’s about welding confidence into every structure that takes off into the sky.
It’s not just about the weld It’s about trust in flight
References
- American Welding Society. (2017). AWS D17.1/D17.1M:2017 – Specification for Fusion Welding for Aerospace Applications. Miami, FL: American Welding Society.
- Messler, R. W. (2004). Principles of welding: Processes, physics, chemistry, and metallurgy. Hoboken, NJ: John Wiley & Sons.