Pipeline corrosion represents one of the main challenges in the oil and gas industry, since these structures form the transport systems of the process flows. Every day, thousands of kilometers of pipelines transport hydrocarbons and their derivatives between extraction, refining, and distribution facilities. However, these pipelines are exposed to aggressive environments that favor corrosion, compromising their integrity and operational efficiency.
Currently, through the use of appropriate technologies and maintenance practices, this problem can be controlled, significantly extending the useful life of your assets.
Corrosion mechanisms in pipelines
Corrosion is a natural process in which metals deteriorate over time due to electrochemical reactions with the environment. Without proper maintenance and regular monitoring, this process can lead to leaks or even rupture of pipelines, with serious consequences for the environment, public safety and companies’ financial results. The following image shows the corrosion of iron in a steel pipe.
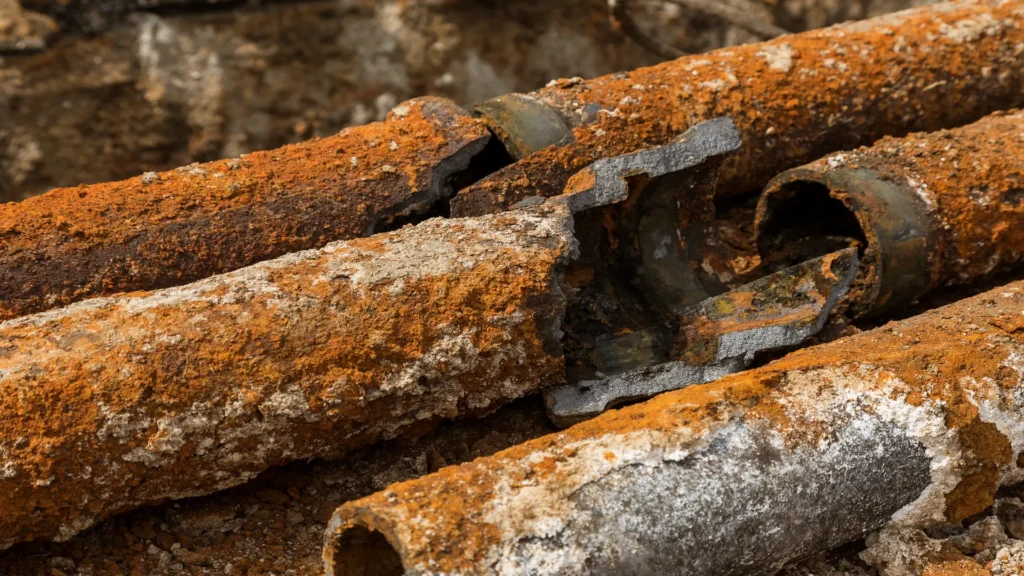
Types of corrosion in conveyor systems
- Galvanic corrosion: Occurs when two dissimilar metals are in contact in the presence of an electrolyte. The less noble metal (anode) corrodes, while the more noble metal (cathode) remains intact.
- Pitting corrosion: This is a type of localized attack that produces small holes in the surface of the metal. Particularly dangerous because it is difficult to detect and can progress rapidly.
- Microbiologically Influenced Corrosion (MIC): Caused by the metabolic activity of microorganisms such as Sulfate Reducing Bacteria (SRB).
- Stress Corrosion Cracking (SCC): Combination of mechanical stresses and corrosive environment that produces cracks in the metal.
- CO₂ Corrosion (Sweet Corrosion): Common in the oil industry, occurs when dissolved carbon dioxide forms carbonic acid.
- H₂S corrosion (Sour Corrosion): Caused by hydrogen sulfide present in crude oil and natural gas, particularly aggressive and can cause hydrogen embrittlement.
Factors influencing corrosion rate
- Composition of transported fluid: Presence of water, CO₂, H₂S, oxygen, chlorides, etc.
- High temperatures and pressures.
- Flow velocity: Erosion-corrosion in high velocity zones.
- pH of the medium.
- Metallurgical properties of the pipe.
- Soil conditions (for buried pipes).
- Air-water-soil interfaces (triple interface zones).
Corrosion prevention and control methods
Material selection
The first line of defense against corrosion begins with the proper selection of materials, including:
- High strength low alloy steels (HSLA).
- Stainless steels for particularly corrosive environments.
- Corrosion resistant alloys (CRAs) such as Inconel, Hastelloy, etc.
- Composite materials for specific applications.
Corrosion protection coatings
These are a special type of coating applied to metal surfaces to protect the underlying surface from possible corrosive damage caused by water, oxygen or electrolytes, acting as a physical barrier between the metal and the corrosive environment.
Innovations in surface coatings include new formulations, advanced applications and improvements in curing. Of particular note is the use of thermosetting or thermoplastic resins in powder coatings, which are electrostatically applied to metal surfaces and thermally cured to achieve a uniform, durable and tough coating. The most commonly used include:
- FBE (Fusion Bonded Epoxy) epoxy coatings
- Three-layer systems (3LPE/3LPP): Epoxy + adhesive + polyethylene/polypropylene
- Internal coatings for protection against corrosive fluids
- Specialty paints for surface installations
Cathodic Protection (CP)
Cathodic protection is a technique for the control of electrolytic corrosion on metallic components exposed to conductive media. Its implementation is fundamental to extend the useful life of critical metallic structures, such as pipelines, tanks and offshore platforms. This protection technique is carried out through two main methods:
- Sacrificial anode cathodic protection: a more active metal (the anode, such as zinc or aluminum) is connected to the structure to be protected (the cathode). The anode corrodes instead of the structure, protecting it.
- Impressed current cathodic protection: An external current source (such as a rectifier) is used to supply current to the structure, making it the cathode of the electrochemical cell.
Monitoring is significant to prevent deterioration of these structures, ensuring their maintenance, structural integrity and operational efficiency. Effectiveness is validated by testing cathodic protection criteria. The correct application of appropriate techniques and the use of modern video surveillance systems simplify control operations, thus ensuring the effectiveness of the cathodic protection system over time.
Corrosion inhibitors
Corrosion inhibitors are used to prevent the degradation of metals, when added in small concentrations to an aggressive environment, they exert a control of electrochemical reactions, thus slowing down the rate of the oxidation reaction. Their mechanism of action includes the formation of a protective film on the metal surface, which can be achieved by passivating the metal, neutralizing corrosive agents or altering the electrochemical reactions responsible for corrosion.
These compounds are necessary in industrial applications, such as pipelines, machinery, storage tanks, to ensure the durability and reliability of metal components. The following are the most commonly used types of corrosion inhibitors.
- Film inhibitors: Form a protective layer on the metal surface
- Anodic and cathodic inhibitors: Interfere with electrochemical reactions
- Volatile inhibitors: For confined spaces and decommissioned systems
- Biocides: Control microbiological corrosion
Advanced technologies for corrosion control
Advanced technologies for pipeline corrosion control are transforming the way industries manage the protection and maintenance of their assets. Thanks to digitization, remote monitoring has become a fundamental tool to detect and prevent damage before it becomes a major problem.
IoT sensors enable continuous monitoring of critical parameters such as humidity, temperature and corrosive agent concentration, providing real-time data that facilitates a fast and efficient response.
In addition, the use of digital twins has opened a new horizon for modeling and predicting corrosive behavior, allowing scenarios to be simulated and maintenance strategies to be optimized based on accurate and up-to-date data.
Artificial intelligence complements these advances by analyzing large volumes of information, identifying patterns and recommending preventive actions that maximize the useful life of materials.
Regulatory framework
To ensure the integrity and safety of industrial systems subject to corrosion, it is essential to comply with internationally recognized technical standards and regulations. Among the most relevant are the NACE/AMPP standards, the American Petroleum Institute (API) standards, as well as the specific regulations of each region and the certifications of the personnel involved in inspection and corrosion control.
Conclusions
Corrosion in oil and gas pipelines is a technical challenge that can be controlled through integrated strategies such as proper material selection, cathodic protection, advanced coatings, chemical inhibitors and continuous monitoring. The adoption of emerging technologies, such as smart coatings and self-healing materials, improves resistance to degradation, optimizes operation and reduces maintenance costs.
In an increasingly digitized world, new technologies offer unprecedented opportunities to optimize corrosion management, enabling the transition from a reactive to a predictive and finally to a prescriptive approach, where intelligent systems can recommend specific actions before problems materialize.
References
- NACE/AMPP International: www.ampp.org
- American Petroleum Institute: www.api.org
- Pipeline and Hazardous Materials Safety Administration: www.phmsa.dot.gov