Table of Contents
- Introduction
- What is butt welding? Definition and basics
- Industrial butt welding applications
- Innovations in butt welding: Orbital welding
- Butt welding vs. fillet welding: Practical Comparison
- When to choose which gasket to apply?
- Non Destructive Testing (NDT) for butt weld inspection
- Applicable standards and codes
- Conclusion
- References
Introduction
Butt welding is one of the most widely used joints in the industry, guaranteeing safety, durability and operational efficiency in various applications. Its technical strength and adaptability has evolved significantly with the introduction of new technologies. Sectors such as energy, petrochemical, pharmaceutical and manufacturing benefit greatly from its applications, especially when a robust, precise and reliable joint between metallic components is required.
In this article, we will discuss the concept of the significance of butt welding, the most recent advances in its application, factors such as bevel type, the role of orbital welding and the effectiveness of nondestructive testing (NDT) in ensuring joint integrity. In addition, we will compare butt welding vs. fillet welding, highlighting its applicability according to American Welding Society standards.
What is butt welding? Definition and basics
Butt joint welding is a joining technique in which two parts are placed in the same plane, end to end, allowing for efficient load transfer. This type of joining is ideal for structures that require superior mechanical integrity, and is mainly applied in piping, pressure vessels, metal structures and critical industrial components.
Unlike other joints, butt welding requires precise edge preparation (beveling) and rigorous process control to avoid internal defects.
Bevel types and their impact on butt weld quality
One of the decisions in butt weld engineering is the selection of bevel type. This directly affects bead penetration, process efficiency and joint quality. The most common types include:
- Single or double V bevel
- J or U bevel (used to reduce weld volume)
- No bevel (for thin sheets)
Factors influencing bezel selection
- Material thickness: The thicker the material, the wider bevels are required to allow adequate penetration.
- Material type: Stainless steels or exotic alloys may require special bevel designs to control dilution and avoid metallurgical failure.
- Accessibility: In confined spaces or orbital welds, bevels that minimize the volume of material to be deposited are preferred.
- Welding technique used: MIG, TIG, or FCAW welding processes require different angles and preparations.
Impact on weld quality
Proper bevel selection improves joint quality, optimizes time and costs, and extends the life of the welded structure. Here are some of the most important impacts:
Bead penetration and fusion quality: Bevel geometry defines the ease with which heat and filler material reach the root of the joint. Poor selection can cause:
- Lack of fusion at the root or flanks.
- Slag inclusions in hard-to-reach areas.
- Excessive reinforcement, which affects joint fatigue.
For example, a single V-bevel is sufficient for moderate thicknesses, but if high thicknesses are involved, it is likely that complete fusion will not be achieved without multiple passes, increasing the risk of internal defects.
Welding process efficiency: Bevels directly affect the volume of weld required, which in turn impacts on:
- Execution time.
- Consumption of material of contribution.
- Energy and labor costs.
J or U bevels, although more complex to prepare, allow for a substantial reduction in the volume to be filled, which improves efficiency, especially in automated or high volume applications.
Metallurgical control and failure prevention: In materials such as stainless steels, duplex or nickel alloys, the bevel design helps to:
- Minimize dilution with the base metal.
- Avoid excessive heat affected zones (HAZ) that could become brittle.
- Control the solidification geometry to avoid micro-cracks.
An inadequate choice compromises metallurgical integrity, even if the joint appears visually acceptable.
Welding technique adaptability: Each welding process has different requirements:
- TIG (GTAW) requires clean, narrow bevels, ideal for precision.
- MIG/MAG (GMAW) requires wider access for good coverage.
- FCAW allows tighter bevels due to its high deposition rate.
- In orbital welding, the design must optimize automatic accessibility.
The type of bevel must complement the capabilities and limitations of the selected process. In short, proper bevel selection:
- Improves joint quality.
- Reduces the risk of defects.
- Optimizes time and costs.
- Extends the service life of the welded structure.
While an inadequate selection leads to:
- Increased rework.
- Possible service failures.
- Loss of efficiency and cost overruns.
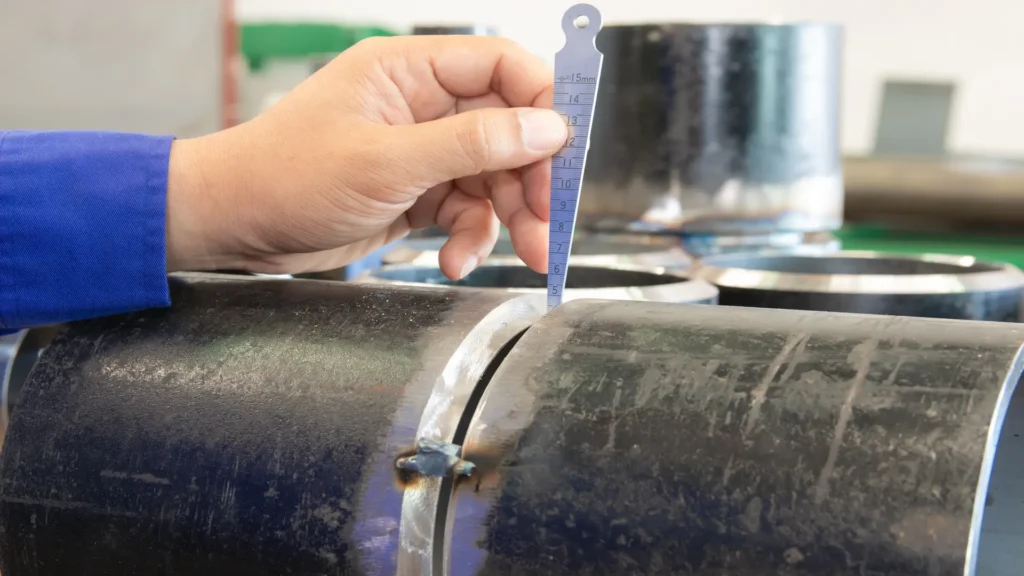
Industrial butt welding applications
Butt joint welding is essential in industries that require high structural strength, automation and ease of inspection. Some of the most prominent applications include:
1.Energy, gas and oil
- Welding of high pressure pipelines, hydrocarbon transport lines and vessels subjected to thermal and mechanical stresses.
- Codes such as ASME Section IX, API 1104 and AWS D1.1 apply.
2. Nuclear industry
- High integrity joints in primary and secondary circuits, where thermal fatigue resistance and reliability are essential.
- Requires full traceability under standards such as ASME III.
3. Food, beverages and pharmaceuticals
- Orbital welding on stainless steel sanitary piping to avoid bacterial accumulation zones.
- Compliance with standards such as ASME BPE and sanitary regulations.
4. Naval and aeronautics
- Applications in structures subjected to vibration, fatigue and aggressive environments.
- Butt joint welding allows weight reduction without compromising integrity.
5. Steel construction and civil structures
- Critical joints in beams, columns and structural nodes in buildings, bridges and offshore platforms.
Innovations in butt welding: Orbital welding
Orbital welding has transformed the butt welding process, especially in small and medium diameter pipes. This automated process improves the accuracy, uniformity and traceability of welds, becoming a standard in industries with high demands.
Orbital welding: Definition and fundamentals
Orbital welding is an automated TIG (Gas Tungsten Arc Welding) welding process in which the welding arc rotates around a static workpiece, usually a pipeline or tube. This method ensures consistent, high quality and repeatable welds, making it ideal for applications requiring precision and high integrity. Orbital welding is especially useful in industries that demand high reliability, such as aerospace, food, pharmaceutical, energy and others that require a clean, safe and traceable weld.
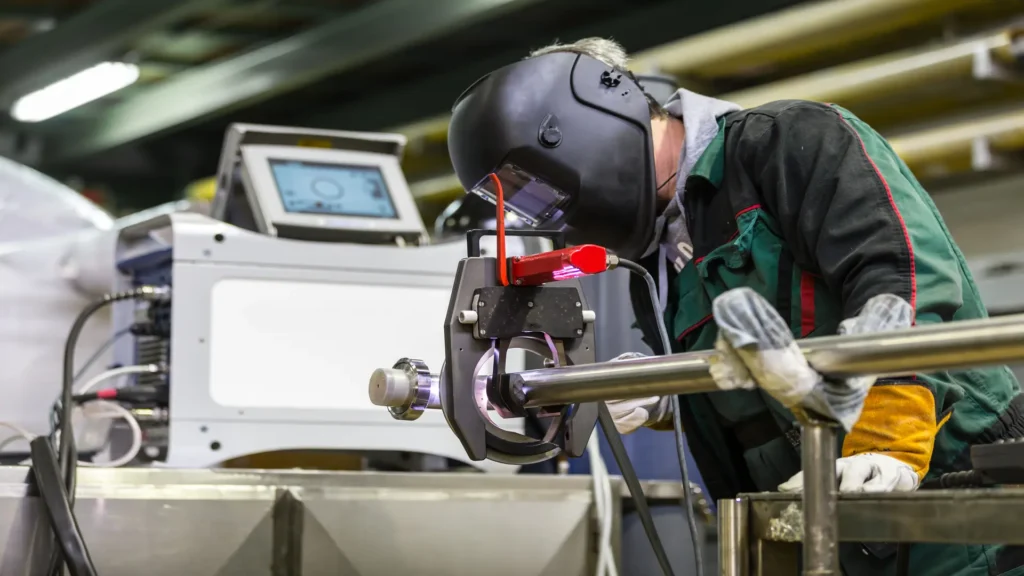
Orbital Welding Machine.
Why is it an innovation for the industry?
- Automated welding with automatic control of critical parameters: Constant regulation of voltage, current, speed and gas flow eliminates operator variability, ensuring consistent results even in harsh environments.
- Drastic defect reduction: Reduced risk of porosity, lack of fusion or incomplete penetration. This translates into fewer rejects and rework, vital in production lines with high standards.
- Productivity without interruptions: By eliminating downtime between passes and manual adjustments, a high deposition rate and feed rate is achieved, which increases operational efficiency.
- Full traceability of every joint: Ideal for audits, quality systems and regulatory compliance. Each weld can be documented, tracked and validated, complying with standards such as ASME or ISO.
What makes it particularly attractive for the energy sector?
In applications such as gas pipelines, nuclear facilities, refineries and chemical plants, where the failure of a weld can have catastrophic consequences, orbital welding offers:
- Operational reliability in areas with difficult access or high demands on structural integrity.
- Compatibility with critical materials, such as stainless steels, duplex and nickel alloys.
- Human risk reduction, key in long duration and high pressure projects.
Do you want to see how an orbital welder works in action? I invite you to watch this video and learn about its operational advantages in critical industries. Courtesy of: KEPUNIWORLDWIDE.
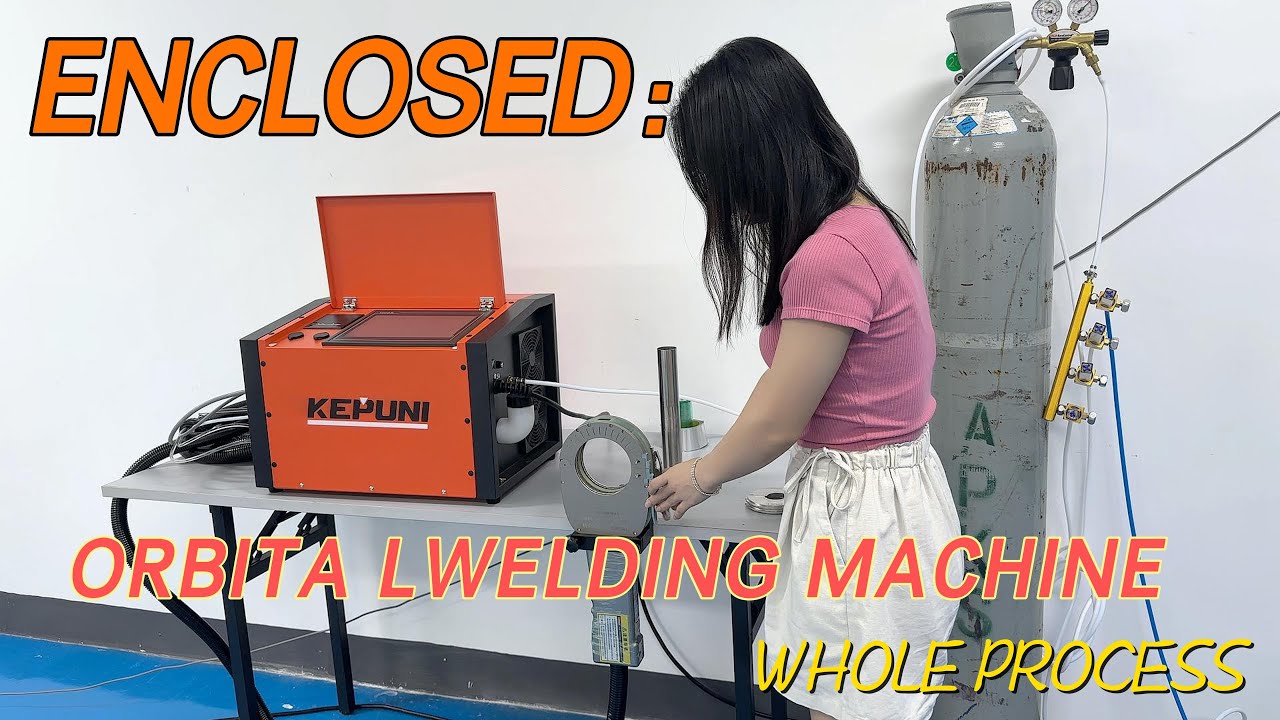
Orbital Welding Machine.
This visual resource is ideal for understanding its actual application in the field, especially in industries such as pharmaceutical, food, energy and nuclear, where joint integrity and cleanliness are critical.
Butt welding vs. fillet welding: Practical Comparison
Both butt joint welding and fillet welding are essential in the fabrication and assembly of metal structures. However, their choice is not arbitrary: it depends on the type of mechanical stress, the configuration of the parts and the operational requirements of the system.
The following is a practical comparison of butt joint vs. fillet welding, to facilitate decision-making on industrial and energy projects:
Characteristic | Butt welding | Fillet welding |
---|---|---|
Type of joint | End to end | Angle between two surfaces (T, L or corner) |
Structural strength | High – Ideal for axial or tensile loads | Medium – Suitable for smaller loads |
Cost and preparation | Larger – Requires bevel preparation and greater alignment control | Smaller – No beveling required, easier to execute |
Quality control | More demanding – Rigorous inspection (NDT, alignment, penetration) | Less demanding, but prone to defects in poorly executed laces |
Aplicaciones típicas | Pressure pipelines, vessels, critical structures (nuclear, gas, oil) | Reinforcements, supports, frames, bodywork, secondary structures |
In the butt welding vs. fillet welding comparison, butt joint welding is preferred when high structural strength is required and joint integrity is essential, while fillet welding is more economical and suitable for applications with lower loads or when ease of part preparation is sought.
When to choose which gasket to apply?
Butt joint welding
It is preferred when total structural continuity, high internal pressure resistance or demanding mechanical strength is required. It is essential in:
- Power plants
- Oil and gas pipelines
- Storage tanks (API 650/653)
- Critical structures with certification
Fillet welding
It is more economical and flexible, used where stresses are lower or well distributed. Ideal for:
- Light structure fabrication
- Bracket mounting
- Auxiliary or temporary structures
Non Destructive Testing (NDT) for butt weld inspection
Non Destructive Testing (NDT) is a fundamental tool to guarantee the quality, reliability and safety of welded joints without compromising their structural integrity. The implementation of these tests in butt welds allows detecting hidden or superficial defects that, if not corrected, could evolve into catastrophic failures, especially in critical applications such as pipelines, pressure vessels or systems in petrochemical and nuclear plants.
More effective methods for inspecting butt welds
- Industrial Radiography (RT): Allows visualization of the complete volume of the weld, ideal for detecting: Internal porosities, longitudinal cracks, and lack of fusion or penetration. Common use in pipe welds, boilers and pressurized equipment.
- Ultrasonic (UT): Emits high frequency acoustic waves to identify volumetric and flat defects with high accuracy, even in inaccessible or thick areas. Detects slag inclusions, cracks and internal misalignments.
- Magnetic particles (MT): For ferromagnetic materials, reveals surface or sub-surface cracks and discontinuities through the application of a magnetic field and fine particles.
- Liquid penetrant testing (PT): Liquid penetrant testing is a highly sensitive method for non-ferrous metal surfaces to detect: fatigue cracks, surface porosity, and manufacturing or repair discontinuities.
Applicable standards and codes
To ensure uniformity in inspection and acceptance criteria, these tests are governed by globally recognized standards:
- ASME Section V: General requirements for NDT in pressure systems.
- AWS D1.1 (American Welding Society): Structural standard applicable to structural steel, defines procedures and acceptance criteria.
- API 1104: Applied to pipeline welds for hydrocarbon transportation, widely used in the energy industry.
- ISO 17635 and EN 9712: European standards defining application requirements and qualification of testing personnel.
Recommendations according to the American Welding Society (AWS)
The American Welding Society establishes technical guidelines that ensure the quality and consistency of weld joints in various applications.
Some key aspects recommended by AWS:
- Proper surface preparation.
- Welding parameters control.
- Welder and procedure qualification.
- Mandatory application of NDT on critical joints.
- Traceability documentation for audits.
Complying with these guidelines not only ensures reliable welds, but also allows compliance with international standards and ISO and ASME certification standards.
Conclusion
Butt welding remains a fundamental technique for ensuring strength, durability and safety in the industry. From the correct choice of bevel to the use of innovations such as orbital welding and advanced inspection techniques, technological advances continue to improve the efficiency and quality of joints. Thanks to standards promoted by organizations such as the American Welding Society, companies now have the tools they need to ensure safe, traceable and long-lasting joints.
Optimize your critical joints with butt welding technology!
References
- Orbital welding: A complete guide – Codinter (https://www.codinter.com)
- ASME Section V: General requirements for NDT in pressure systems.
- AWS D1.1 (American Welding Society): Structural standard applicable to structural steel.