Ensuring the structural integrity of aboveground storage tanks (ASTs) is critical in industrial asset management. These vessels, which are used to store hydrocarbons, flammable liquids, chemicals, fuels and other products, are inherently exposed to deterioration mechanisms such as corrosion, mechanical wear and differential settlement.
The application of specific technical standards for the inspection, maintenance, repair and rehabilitation of these systems is essential to prevent failures that can lead to incidents with serious operational, environmental, economic and safety consequences. Among the most internationally recognized standards for AST inspection are STI SP001, developed by the Steel Tank Institute (STI/SPFA), and API 653, published by the American Petroleum Institute (API).
Both technical documents provide structured methodologies for the inspection of ASTs, but differ in their philosophy, scope, technical requirements for inspection, evaluation criteria and complexity of implementation. This article provides a detailed technical comparison of the two standards, with the objective of providing practitioners with the information needed to make informed technical decisions.
Overview of the scope and applicability of the standards
STI Standard SP001
STI SP001, in its seventh and most recent edition (February 2024), entitled Standard for the Inspection of Aboveground Storage Tanks, represents the current Steel Tank Institute (STI/SPFA) guidance for the inspection of welded metal tanks, typically shop-fabricated under controlled conditions and with standardized geometries, intended to be transported and installed at the site of operation.
Its main scope covers above-ground atmospheric tanks with vertical or horizontal cylindrical shapes, with dimensions up to a maximum diameter of 9.14 m and a height of 15.24 m, designed to store liquids with temperatures between ambient and 93.3 °C (86 °F). It also contemplates small field-built tanks within these limits, as well as 55-gallon metal drums and intermediate bulk containers (IBCs).
It covers single or double wall configurations and secondary containment systems. Non-portable fiberglass or plastic tanks are excluded. The STI SP001 is widely deployed in commercial, logistics, agribusiness, light manufacturing and service station facilities where medium to moderate volume storage requires compliance with environmental and safety regulations.
API Standard 653
API 653, in its fifth edition (November 2014), entitled Tank Inspection, Repair, Alteration, and Reconstruction, with subsequent addenda and errata updating and clarifying its technical guidelines, establishes the American Petroleum Institute’s (API) technical framework for assessing the structural integrity and life-cycle management of storage tanks; it is implemented at refinery assets, petrochemical facilities and storage terminals.
Its applicability is focused on atmospheric, above-ground, welded or riveted steel storage tanks built in the field without specific dimensional limitations, originally under API 650 (Welded Tanks for Oil Storage) or its predecessor API 12C (Specification for Welded Oil Storage Tanks) standards.
The scope of inspection under API 653 is comprehensive, encompassing all structural components of the tank, including the foundation, bottom, body walls, roof (fixed or floating) and its supporting structure, internal linings (if any), general fittings (nozzles, ladders, platforms, etc.), and nozzles up to the face of the first flange or first welded connection.
Technical differences
Inspection methods and frequencies
STI SP001: Establishes an inspection methodology based on risk categorization, where tanks are classified into three levels according to the presence of spill control and Continuous Release Detection Methods (CRDM). This classification directly influences the frequency of visual inspections. Although it does not require the use of Non Destructive Testing on a routine basis, its application is allowed when technically justified. The frequency of inspections is as follows:
- Category 1 (Lower risk – with spill control and CRDM): Monthly external visual inspection (DATCP form TR-WM-128), formal external visual inspection every 10 years (DATCP form TR-WM135), and internal inspection every 20 years.
- Category 2 (Medium risk – with spill control, no CRDM): Monthly external visual inspection, formal external visual inspection every 5 years, and internal inspection every 10 years.
- Category 3 (Higher risk – no spill control or CRDM): Monthly external visual inspection, formal external visual inspection every 5 years, and internal inspection every 10 years (with possible reduction based on risk assessment).
The inspection philosophy is based fundamentally on detailed visual observation by trained personnel, with frequencies adjusted to the inherent risk of the tank, according to its containment and leak detection characteristics.
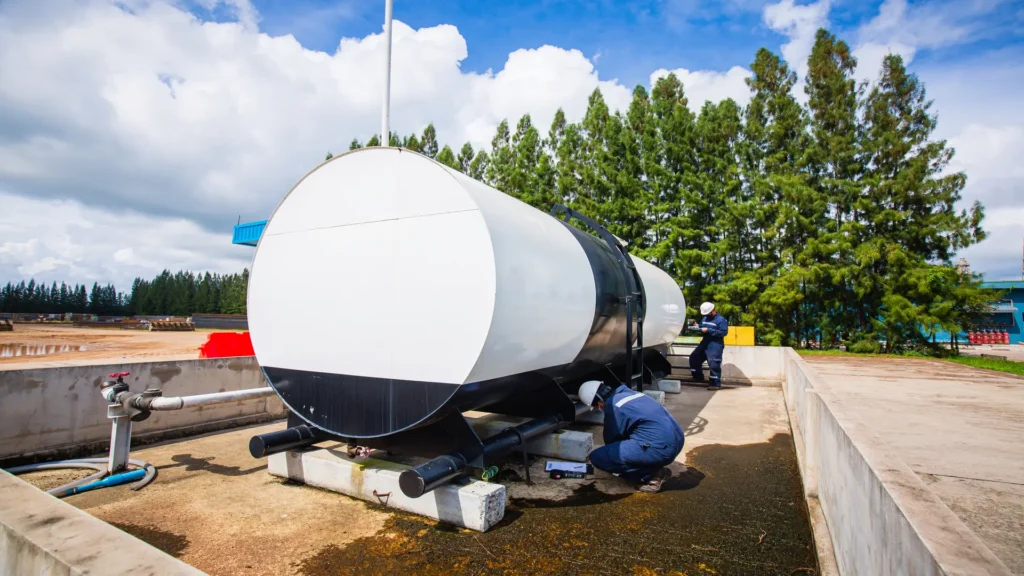
API 653: Requires internal and external inspections performed by API 653 certified inspectors. A distinctive aspect is the use of Non Destructive Testing. Techniques such as ultrasonic (UT) for thickness measurement and lamination detection, radiography (RT) for weld evaluation, magnetic flux leakage (MFL) for tank bottom corrosion detection, liquid penetrant (PT) and magnetic particle (MT) for detection of surface and sub-surface discontinuities.
The frequency is determined by a Risk Based Inspection (RBI), analyzing the probability of failure (considering history, operating variables, corrosion, design, etc.) and the consequence of failure (environmental, safety, economic impact). As an initial guideline, the first internal inspection is between 5 and 10 years of service, subsequently adjusted according to RBI results and operating conditions.
External inspections are performed every 5 years or less, applying a detailed checklist. API 653 also allows the use of advanced internal inspection technologies without the need to empty the tank, such as submersible robots (ROVs) and Pulsed Eddy Currents (PEC) for annular ring evaluation or Automated Scanning (AUT) for wall inspection, always under the supervision of an API Inspector.
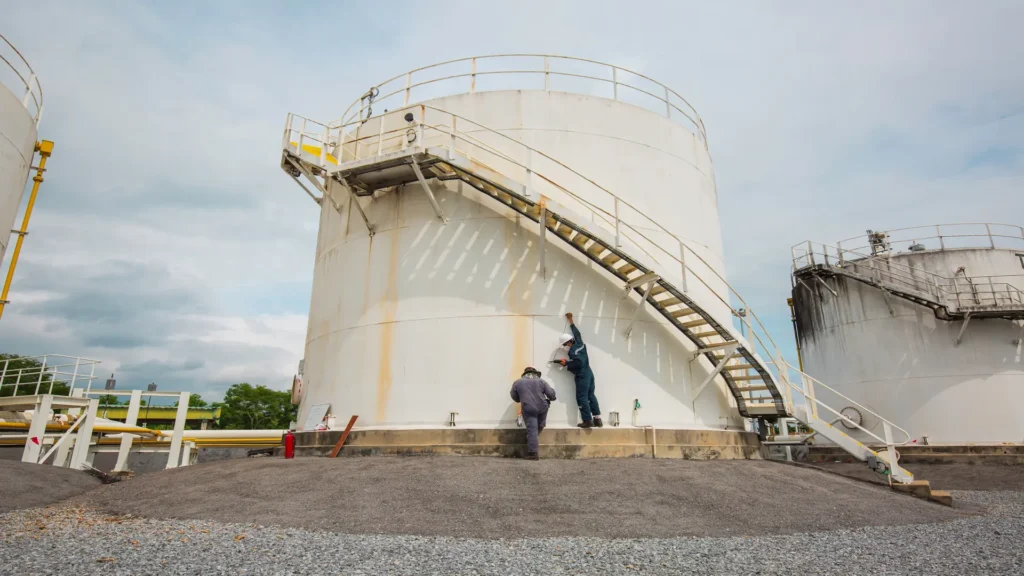
Acceptance criteria and structural defects
STI SP001: Contemplates mainly visual inspection and leak testing. Acceptance and rejection criteria are based on visible deterioration (surface corrosion, dents, deformations), operating conditions and the risk category of the tank. For example, a certain level of surface corrosion might be acceptable on a Category 1 tank, but would require action on a Category 3 tank.
API 653: This standard has a quantitative approach. It uses methods for calculating minimum wall and bottom thicknesses, as well as remaining service life based on measured corrosion rates. Hull dimensional tolerances are evaluated under construction standards. Criteria for acceptance or rejection of defects such as cracks, pitting, uniform corrosion, buckling and settlement are based on defined limits and structural integrity calculations.
Economic and operational considerations
STI SP001: Lower complexity and cost. Ideal for low risk installations. Allows for spaced internal inspections and simple checklists.
API 653: Higher technical, logistic and economic requirements. Suitable for high criticality installations, with exhaustive control and regulatory compliance.
What are the certification requirements of each standard for inspectors?
STI SP001: Periodic inspections performed by trained personnel familiar with the system. Formal inspections, on the other hand, must be performed by an STI Certified Inspector or an API 653 Inspector with STI training. Requires training, examination and recertification every five years.
API 653: All inspections must be performed by a certified API inspector. Certification is valid for three years and involves participation in continuing professional development. This training is complemented by API 650, API 571 and API 580.
Regulatory compliance (EPA’s SPCC program)
Both standards are valued tools that help facilities comply with environmental regulations, such as the U.S. Environmental Protection Agency’s (EPA) Spill Prevention, Control and Countermeasures (SPCC) program. These programs require facilities to develop and implement plans to prevent spills of oil and hazardous substances.
The systematic application of the inspections and maintenance procedures defined in these standards contributes to the early identification of potential failures and the implementation of corrective actions, improving safety and facilitating regulatory compliance.
Summary table: Which inspection standard is suitable for your AST?
The choice between STI SP001 and API 653 for the inspection of your aboveground storage tank depends on the following key characteristics of your asset and your operational requirements:
Characteristic | STI SP001 (Ideal for…) | API 653 (Ideal for…) |
Manufacturing Standard | UL 142 or others of similar scope (lower than API 650) | API 650 or API 12C |
Tank Type | Atmospheric, horizontal or vertical cylindrical (mainly welded), ≤ 93.3 °C | Atmospheric, vertical, welded or riveted. Temperature from ambient to non-cryogenic refrigerated |
Material / Fabrication | Metallic, shop-fabricated or small field-erected tanks | Metallic tanks, mainly field-erected |
Dimensions | Diameter ≤ 9.14 m and height ≤ 15.24 m | No dimensional limitations |
Inspection Methods | Mainly visual, leak testing | Mandatory visual inspection and NDT |
Inspection Frequency | By risk category, visually determined | Based on risk-based inspection |
Inspector | Trained personnel or STI Inspector | API 653 certified inspector |
Acceptance Criteria | Visual and operational | Quantitative and structural |
Technical Complexity | Lower | Higher |
Cost Considerations | Generally lower | Generally higher |
Typical Applicability | Low-risk facilities | Critical Installations |
Conclusions
The choice between STI SP001 and API 653 should be based on a thorough technical analysis that considers the dimensions, manufacturing standard, operating conditions, regulatory environment and operational criticality of the asset. STI SP001 offers a practical and cost-effective solution for the inspection of smaller scale tanks, with a primary focus on risk-stratified visual inspection.
API 653, is essential to ensure the structural integrity of large capacity tanks in complex and high criticality operations, through the rigorous application of NDT and the implementation of an RBI methodology for inspection planning. Both standards are strategic in structuring effective inspection plans and supporting regulatory compliance, contributing to spill prevention and associated facility safety.
References
- https://datcp.wi.gov/Documents/STI-SP001ASTInspections.pdf
- https://www.epa.gov/oil-spills-prevention-and-preparedness-regulations/tank-inspections
- https://es.abcdef.wiki/wiki/Secondary_spill_containment