Introduction
When we start a project, the first thing we really consider when thinking about it is everything related to its feasibility and the necessary studies for its design, execution and development. Sometimes, we face challenges that push us to be more ingenious in the search for solutions to the most complex challenges. A good example of this is the construction of infrastructure in extreme environments, such as deserts and the sea, which present significant complications due to the unique conditions of these ecosystems.
Corrosion, in this context, remains one of the main obstacles, as it impacts both the durability and functionality of the materials we use. In deserts, factors such as high temperatures, sudden temperature changes and abrasion caused by sand particles can accelerate the deterioration of structures.
On the other hand, marine environments are particularly hostile due to water salinity, high humidity and the action of microorganisms that promote microbiological corrosion. Let’s look at the particularities of these environments, the materials used, the technological solutions available and the economic and environmental challenges we face in material protection against corrosion.
Environmental characteristics and their impact on corrosion
Desert environments
Deserts present a unique combination of factors that directly affect the service life of materials. Although characterized by low relative humidity, the presence of nighttime condensation, coupled with the accumulation of salts in the sand, creates conditions for localized corrosion. In addition, sandstorms exert an abrasive effect that wears away protective coatings and exposes vulnerable surfaces (Zhou et al., 2020).
It should be noted that extreme thermal oscillations also play an important role, since expansion and contraction cycles can generate cracks in materials, favoring the infiltration of corrosive agents.
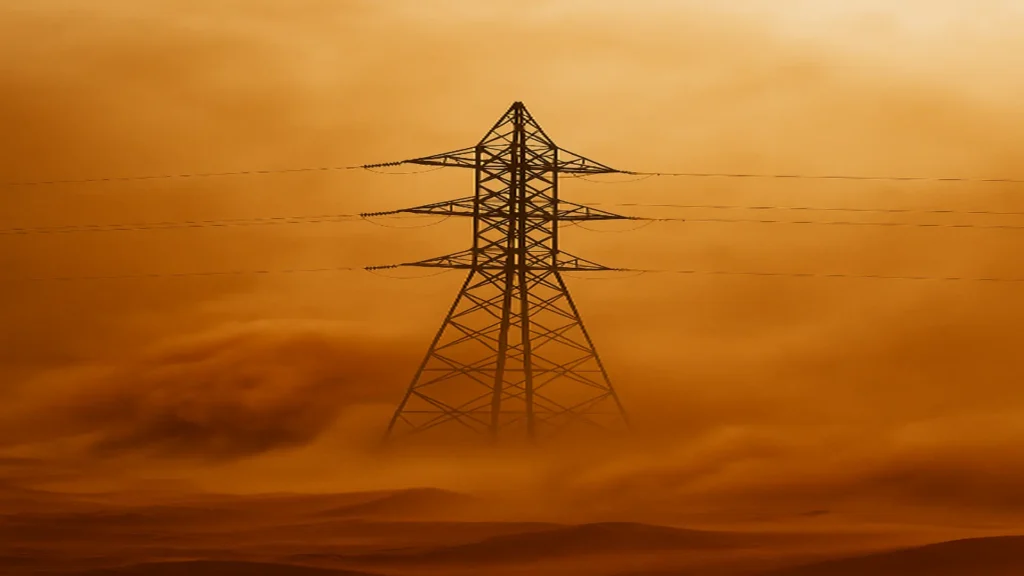
In addition, intense solar radiation can degrade certain polymers used in external components, reducing their service life. In infrastructures such as solar plants, water distribution networks or industrial facilities, this combination of factors requires the selection of materials with high thermal, mechanical and chemical resistance.
Dust accumulation also presents a challenge, as it not only increases abrasion, but also prevents proper ventilation of surfaces, retaining heat and moisture. It is common in these environments to implement structural designs that minimize exposed surfaces and use physical barriers against sand impact. Adaptation to desert conditions involves not only protecting against corrosion, but also ensuring functional performance in conditions of continuous and extreme exposure.
Maritime environments
In marine environments, the levels of aggressiveness are even more pronounced due to the constant interaction with seawater and salty air. The chlorides present in the water facilitate electrochemical reactions that degrade metals, even those with coatings. In turn, salt spray transports corrosive particles inland, extending the scope of corrosion. In addition, the action of microorganisms in the water generates biofilms that can accelerate the deterioration of metallic materials (Baboian, 2005).
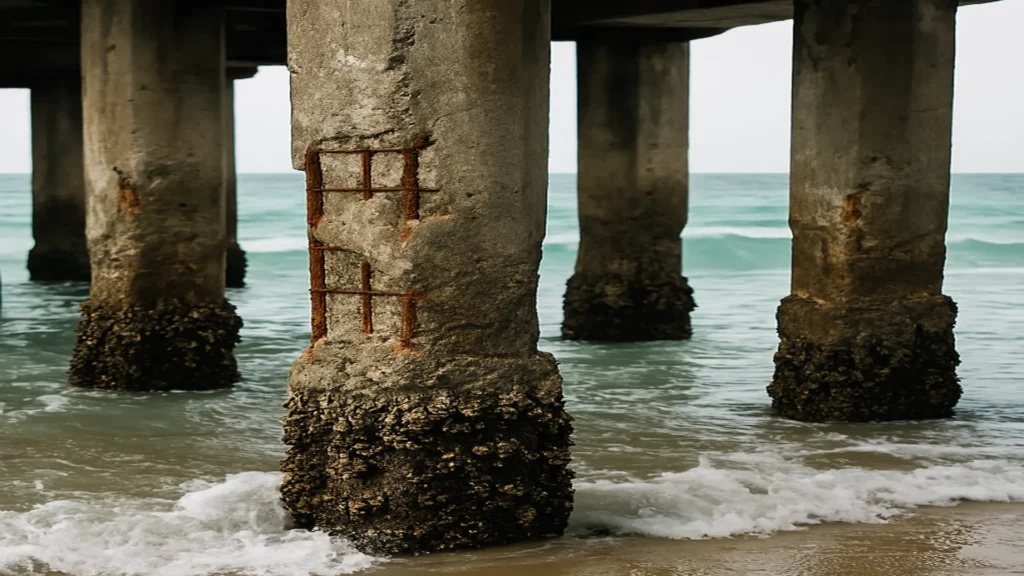
The variability of these environmental conditions also plays a relevant role. While we consider that in tropical coastal areas constant temperature and humidity favor an ideal environment for continuous corrosion, also in temperate regions cold seasons can generate freezing and thawing cycles that affect the condition of coatings.
On the other hand, submerged or partially exposed structures, such as pier piles, jetties or offshore wind towers, are subject to the intertidal zone, where exposure to oxygen and salts alternates, generating particularly severe conditions. Biofouling not only accelerates corrosion processes, but also increases maintenance costs by requiring periodic cleaning.
Corrosion solutions in marine environments require a comprehensive approach that combines technological innovation, appropriate material selection and advanced mitigation strategies. The use of materials with high corrosion resistance, frequent preventive maintenance and the application of specialized technologies, such as antifouling coatings and hybrid cathodic protection systems, are essential. In addition, modern monitoring techniques allow real-time evaluation of the interaction between materials and environmental factors, thus optimizing the durability and performance of structures exposed to severe marine conditions.
Materials used in critical infrastructure
Reinforced concrete
Reinforced concrete, widely used in maritime environments, faces particular challenges such as chloride penetration through microcracks. This can lead to corrosion of internal steel reinforcement, weakening the structure (Andrade & Alonso, 1996). Recently, special admixtures and epoxy coatings have been used to increase the corrosion resistance of concrete. However, the implementation of these advances depends on economic factors and the specific location of the project.
In addition to coatings, technologies have been developed that modify the composition of the concrete, incorporating low-permeability cements or pozzolanic materials that reduce porosity and hinder the penetration of aggressive agents. In areas with high exposure to salt water, additional protective layers are also used, such as waterproofing membranes or drainage systems that reduce direct contact with water.
A more recent approach includes the use of polymeric or metallic fibers that, by better distributing internal stresses, reduce crack formation. In desert contexts, concrete must also withstand extreme thermal cycling, which requires a formulation that minimizes thermal cracking.
Carbonation monitoring and the implementation of preventive maintenance strategies are key to prolonging structural durability, especially in critical infrastructure such as dams, roads or water treatment plants.
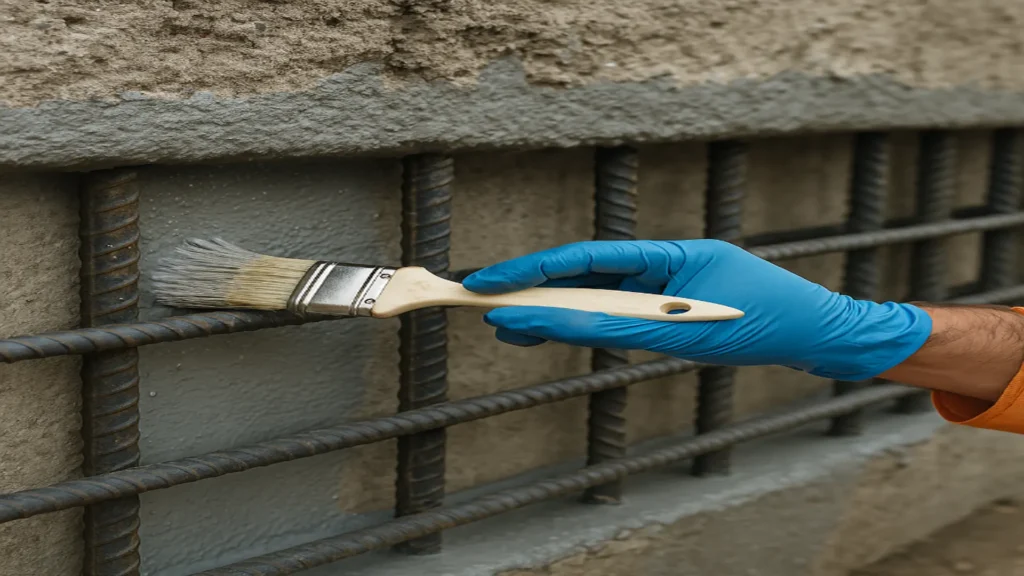
Advanced metals and alloys
Metals such as stainless steel and aluminum have been optimized to withstand extreme conditions. In particular, alloys with high chromium, nickel and molybdenum contents offer greater resistance to saltwater corrosion. However, their high cost limits their use to projects where durability is critical (Song & Atrens, 1999).
The development of new alloys has made it possible to adjust material properties to the specific needs of each environment. For example, nickel- or titanium-based superalloys, although expensive, are essential in high-pressure, high-temperature marine environments, such as offshore platforms.
Another example is desert contexts, where abrasion is a constant concern, so the use of metallic coatings by thermal spraying or surface treatments such as aluminum anodization substantially improves resistance. Materials with shape memory or self-repairing properties that allow an adaptive response to physical or chemical damage are also being investigated.
Despite advances, the selection of the metal or alloy depends on a balance between cost, expected service life, criticality of the structure and local availability, factors that must be analyzed at the design stage of any corrosion resistant infrastructure.
Technological solutions against corrosion
Technological solutions against corrosion
Advanced protective coatings, such as epoxy paints and ceramic nanoparticles, are essential to prevent direct contact between materials and corrosive agents. These coatings, in addition to being impermeable, possess self-healing properties that prolong their functionality under adverse conditions (Wang et al., 2018).
Emerging technologies include coatings with corrosion inhibitors that are released in a controlled manner in the presence of moisture or mechanical damage. Intelligent paints have also been developed that change color upon detection of active corrosion zones, enabling early detection of failures.
The incorporation of graphene, for example, improves the barrier properties of the coatings while maintaining the lightness of the system. In desert environments, coatings must also resist UV radiation and constant abrasion, so combinations of polymers with mineral fillers that improve surface resistance are being studied.
The correct application of these coatings is key: it involves rigorous surface preparation, temperature and humidity control during the process and periodic maintenance to ensure their effectiveness. Advances in nanotechnology and microencapsulation have opened up new opportunities to develop protective barriers with multiple functions, capable of actively responding to changing environmental conditions.
Active monitoring and predictive maintenance
The use of smart sensors and real-time monitoring systems has revolutionized infrastructure maintenance. These tools make it possible to identify areas with high susceptibility to corrosion before damage becomes irreversible, thus optimizing maintenance and repair resources (Melchers, 2003).
Current systems include sensors infiltrated into the concrete, fiber optics to detect microcracks, and wireless networks that transmit data on humidity, temperature, pH and electrochemical potential. These technologies allow the creation of predictive models using artificial intelligence, which anticipate structural behavior and prioritize interventions before major failures occur.
In remote or difficult-to-access environments, such as deserts or offshore platforms, these solutions minimize human risk and improve operational efficiency. The integration of digital twins – virtual replicas of physical infrastructures – makes it possible to simulate deterioration scenarios and evaluate the impact of various maintenance strategies. In the long term, this approach significantly reduces intervention costs, extends the service life of structures and improves the sustainability of operations.
Cathodic protection
The cathodic protection technique remains one of the most effective techniques for preventing corrosion in buried or submerged metallic structures, such as oil pipelines and oil platforms. This system uses sacrificial anodes that protect the base metal by reducing electrochemical activity (Jones, 1996).
There are two main methods: galvanic cathodic protection, in which more reactive metal anodes are used; and impressed current protection, which uses an external source of energy to maintain the protection potential. In marine applications, these systems are carefully designed to compensate for the progressive loss of mass of the anodes, which must be replaced periodically.
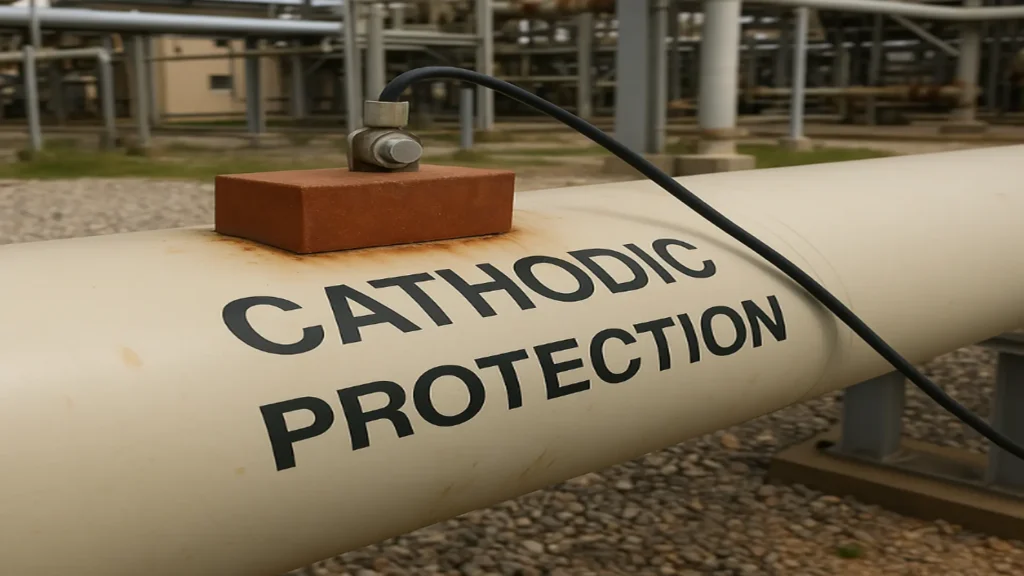
In desert environments, this technology is used in subway pipelines, where the presence of saline moisture in the soil can cause corrosion. Effective implementation requires continuous monitoring of the electrochemical potential, control of soil resistivity and proper installation of the connection systems. Despite its effectiveness, its use can involve high initial costs, so it is reserved for high-value assets or assets with restricted access for frequent maintenance.
Economic and environmental challenges
Economic costs
Corrosion protection involves significant costs as we well know, from advanced materials to monitoring technologies. However, studies have shown that these investments reduce long-term expenses by preventing premature structural failures (Koch et al., 2016).
Life cycle assessment of infrastructures has shown that investing in prevention and monitoring significantly reduces the costs associated with repairs, operational shutdowns or even total replacements. This is particularly important in strategic sectors such as energy, transportation or water supply.
In addition, the implementation of smart technologies allows optimizing resources by intervening only where and when necessary, avoiding unnecessary expenses. However, high initial costs may limit their adoption, especially in regions with low infrastructure budgets. In such cases, it is key to prioritize critical areas and seek funding through international cooperation programs or public-private partnerships.
Lack of preventive maintenance and the use of inadequate materials have proven to be much more costly in the medium term; therefore, a risk management strategy based on data and continuous monitoring is economically favorable.
Environmental impact
However, some anti-corrosion solutions, such as chemical coatings, raise environmental concerns due to their composition. Therefore, sustainable approaches that balance material protection and environmental conservation, such as the use of biomaterials and low-impact technologies, are required (Schleich et al., 2020).
The use of volatile organic solvents, heavy metals and non-biodegradable substances in traditional coatings poses risks both during application and at the end of their useful life. In response, environmentally friendly alternatives such as water-based coatings, biopolymers and natural inhibitor pigments have been developed.
Likewise, the reuse of materials and the design of solutions with a lower carbon footprint are gaining ground. Circular economy strategies applied to materials engineering are also reducing waste and promoting sustainability.
In coastal and desert areas, where ecosystems are particularly sensitive, it is essential that the technologies applied do not compromise biodiversity or generate secondary pollution. Environmental criteria must be considered from the design stage, seeking a balance between durability, efficiency and ecological responsibility.
Conclusion
From the above, it is clear that protecting infrastructure from corrosion in desert and maritime environments requires a comprehensive approach that combines technological advances with sustainable practices. Innovation in materials and monitoring strategies can mitigate damage and reduce long-term costs, although initial investments can be significant. As we move into an era of sustainability, prioritizing solutions that balance economic, environmental and durability needs is critical.
References
- Andrade, C., & Alonso, C. (1996). Corrosion and concrete durability in the marine environment. Cement and Concrete Research, 26(3), 453-463.
- Baboian, R. (2005). Corrosion tests and standards: application and interpretation. ASTM International.
- Jones, D. A. (1996). Principles and prevention of corrosion. Prentice Hall.
- Koch, G. H., Brongers, M. P. H., Thompson, N. G., Virmani, Y. P., & Payer, J. H. (2016). Corrosion costs and preventive strategies in the United States. NACE International.
- Melchers, R. E. (2003). Modeling of marine immersion corrosion for mild steel. Corrosion Science, 45(5), 1023-1036.
- Revie, R. W., & Uhlig, H. H. (2012). Corrosion and corrosion control. Wiley.
- Schleich, F., et al. (2020). Sustainable coatings for corrosion protection. Journal of Applied Polymer Science, 137(22), 48522.
- Shi, X., & Zhang, Y. (2021). Corrosion in desert environments: Factors and countermeasures. International Journal of Corrosion Science, 19(7), 365-378.
- Song, J., & Atrens, A. (1999). Understanding corrosion resistance of magnesium alloys. Corrosion Science, 41(6), 1237-1267.
- Wang, J., et al. (2018). Nanotechnology in coatings for corrosion resistance. Nanomaterials, 8(9), 672.
- Zhou, W., et al. (2020). Challenges of infrastructure durability in desert regions. Construction Materials Journal, 14(4), 412-418.