Table of Contents
- What is Stress corrosion cracking?
- How SCC differs from other types of degradation
- Causes and mechanisms of SCC
- Susceptible materials and conditions
- Which materials are susceptible to stress corrosion cracking?
- Stainless steel SCC: Common failure cases in industry
- Nickel-based alloys vs. carbon steels: SCC reaction differences
- Impact of corrosion materials in different environments
- Methods to increase SCC resistance through material selection and stress reduction
- Characteristics of stress corrosion cracking
- How SCC differs from other forms of cracking
- Intergranular vs. transgranular cracking
- SCC in pipelines and welds
- Detection, testing, and inspection techniques
- Prevention and mitigation strategies
- How to prevent stress corrosion cracking: Design improvements and stress relief techniques
- Material selection: Choosing corrosion-resistant alloys
- Surface treatments and coatings to minimize SCC
- How to avoid stress corrosion cracking: Practical tips for engineers
- Use of inhibitors and protective coatings in industries
- Industry best practices for SCC prevention
- Future trends and advances in SCC mitigation
- Conclusions
- References
Stress corrosion cracking (SCC) is a severe and insidious form of material degradation that occurs when susceptible metals are exposed to a corrosive environment under tensile stress. Elevated temperatures significantly exacerbate this process. Unlike uniform corrosion, which leads to a predictable material loss, SCC can cause sudden and often unexpected failure of critical infrastructure, sometimes without visible signs of deterioration.
The formation of microcracks, which are fine and often invisible at first, is a defining characteristic of SCC. These microcracks propagate over time, potentially leading to catastrophic failure even if the material appears intact externally. High temperatures can accelerate the SCC process by increasing both the corrosion rate and the cracking mechanism, thereby enhancing the chemical reactions between the metal and its corrosive environment. This makes SCC particularly hazardous in high-temperature environments, where the risk of failure is significantly elevated.
Industries such as oil and gas, nuclear power, marine engineering, and aerospace are especially vulnerable to SCC, as they operate under extreme conditions involving tensile stress and corrosive agents, often at elevated temperatures. For instance, pipelines in the petrochemical sector, heat exchangers in nuclear reactors, and offshore structures exposed to seawater are at a higher risk of SCC in elevated temperature environments. Additionally, materials like stainless steels and other alloys, commonly used in these industries, may experience reduced strength or altered properties at higher temperatures, making them more susceptible to SCC.
This article analyzes the behavior of stress corrosion cracking (SCC) in temperature-dependent environments and presents effective detection and control strategies in order to ensure the safety and durability of industrial infrastructure.
What is Stress corrosion cracking?
Stress corrosion cracking (SCC) is a degradation mechanism that occurs when a metal is exposed to a corrosive environment under stress, with the additional factor that high temperatures significantly influence the process. Unlike other types of corrosion in metals, SCC is particularly dangerous because it results in the formation of microcracks, which are fine and often initially invisible fissures.
These microcracks propagate over time without noticeable loss of material or visible signs of damage, leading to sudden failures when the material can no longer withstand operational loads or stresses. The following image shows the failure of a water pipeline due to SCC.
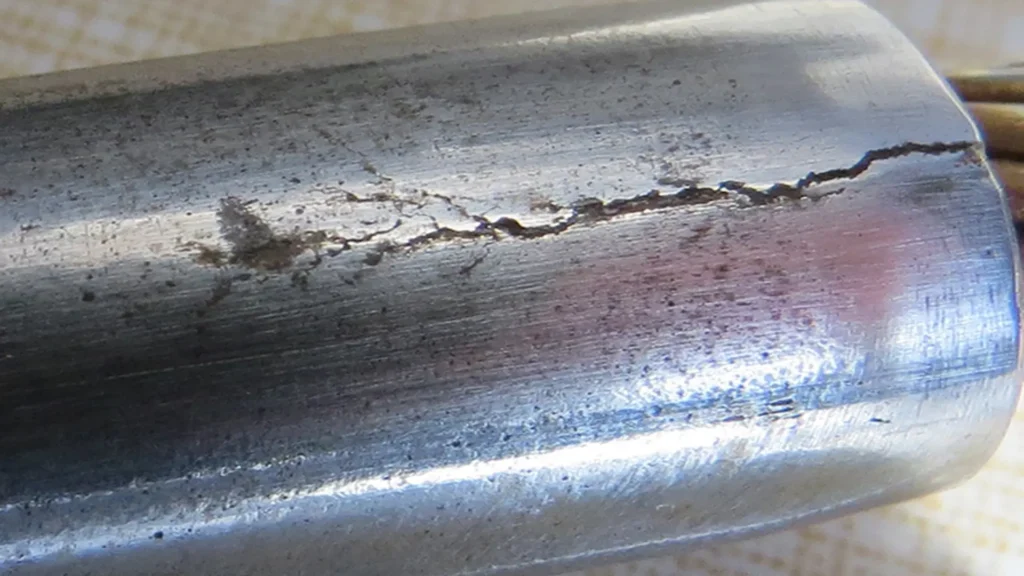
High temperatures accelerate the SCC process by enhancing the rate of corrosion and weakening the mechanical properties of the metal, making it more prone to cracking under stress. As the temperature increases, the metal’s microstructure can also change, making it more susceptible to cracking in the presence of corrosive agents like chlorides or sulfides.
For example, austenitic stainless steels are more susceptible to SCC in high-temperature environments, such as those found in chemical plants, nuclear reactors, or offshore oil rigs exposed to harsh chemicals or seawater. The combined effect of tensile stress and temperature can cause these microcracks to propagate rapidly, potentially resulting in catastrophic material failure.
High-temperature SCC is particularly dangerous because it often occurs in critical structures that are under constant operational stress, such as pressure vessels, pipelines, and heat exchangers. Effective prevention strategies include selecting materials with greater resistance to SCC at elevated temperatures, minimizing operational stresses, and using protective coatings or inhibitors to mitigate the corrosive effects of the environment.
For more information on stress corrosion cracking determination, identification and analysis, I invite you to watch the following video. Source: RJ Lee Group, Inc.
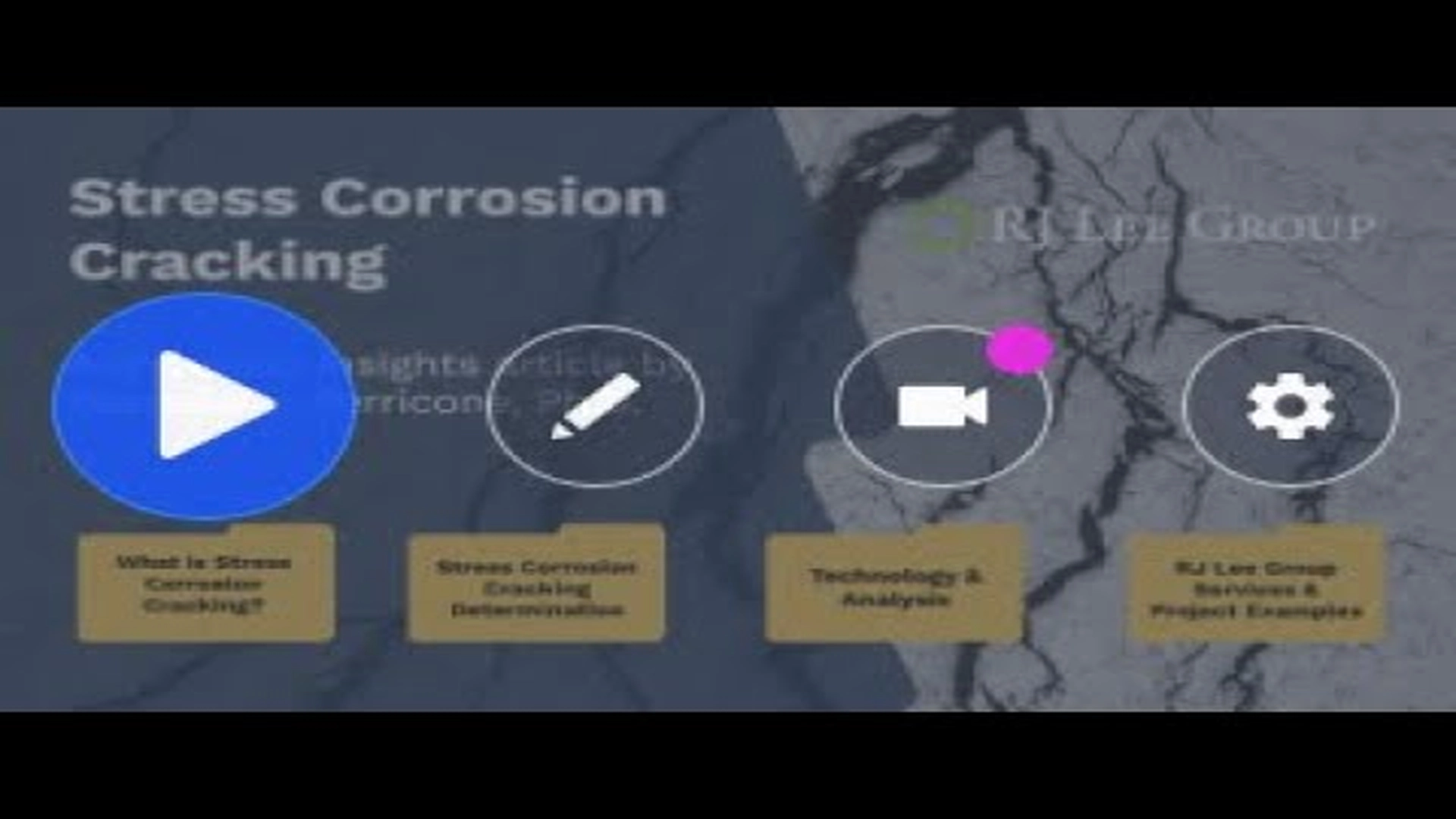
Determination, identification, and analysis of Stress Corrosion Cracking,
How SCC differs from other types of degradation
SCC is distinct from other forms of material degradation in the following ways:
- General corrosion: This leads to uniform material loss, whereas SCC involves the formation of microcracks without significant material loss.
- Pitting corrosion: Pitting leads to localized cavities or holes in the material, whereas SCC leads to crack formation that can spread and compromise the structural integrity of the material over time.
- Fatigue failure: Fatigue failure is caused by cyclic loading and is primarily driven by mechanical stresses, rather than environmental factors like corrosion.
- Hydrogen embrittlement: Hydrogen embrittlement weakens the metal due to hydrogen absorption but does not necessarily require a corrosive environment to initiate the degradation.
Three main factors leading to SCC
SCC development requires the simultaneous presence of three key factors:
I. Tensile stress (residual or applied)
SCC does not occur unless the material is under tensile stress. There are two main types of tensile stress that contribute to SCC:
A. Residual stress (Stress already present in the material)
- Generated during manufacturing, welding, heat treatment, or machining.
- Does not require external forces to act—it exists within the material itself.
- Example: Welded stainless steel pipelines retain residual stress from the cooling process, making them susceptible to chloride-induced SCC.
B. Applied stress (stress from external forces)
- Results from operational loads, pressure fluctuations, thermal expansion, or mechanical tension.
- Often occurs in high-pressure vessels, pipelines, aircraft fuselage panels, and offshore structures.
- Example: High-pressure gas pipelines experience applied tensile stress due to internal pressure fluctuations.
II. Corrosive environment
The presence of a corrosive environment is essential for SCC to occur. Common corrosive agents include:
- Chloride-induced SCC (Cl-SCC) is common in stainless steels and marine environments.
- Alkali and ammonia SCC affects brass and copper alloys in industrial cooling systems.
- Sulfur-related SCC occurs in oil refineries processing high-sulfur crude oil.
III. Material susceptibility
- Stainless steels (304, 316) are prone to Cl-SCC in high-humidity environments.
- Nickel-based alloys like Inconel exhibit superior SCC resistance but are costly.
- High-strength carbon steels suffer SCC in hydrogen sulfide (H₂S)-rich environments, particularly in oil & gas applications.
Why stress is critical in SCC
Unlike general corrosion, where material gradually wears away, SCC requires tensile stress to initiate and propagate cracks. This makes SCC particularly dangerous because cracks can propagate while the material appears to be intact on the outside. It is only when these cracks have propagated far enough that the material fails catastrophically, often without any visible sign of damage or deterioration.
SCC in critical industries
- Aerospace: SCC in aluminum aircraft components leads to structural integrity concerns.
- Petrochemical: Reactors and pipelines in refineries experience sulfide SCC due to exposure to high-temperature hydrogen sulfide.
- Nuclear power: SCC in reactor components (e.g., Inconel tubes) can lead to leaks and operational hazards.
Causes and mechanisms of SCC
What causes stress corrosion cracking?
SCC arises from the combined effects of mechanical stress, environmental aggressors, and material vulnerability. It is a synergistic process, meaning that the presence of a corrosive medium alone does not cause SCC unless tensile stress is also applied. Likewise, stress alone does not trigger SCC unless an active corrosive agent is present. However, the most critical aspect of SCC is the formation and growth of microcracks, which initiate within the material’s microstructure and propagate over time until failure occurs.

Key environmental factors influencing SCC
I. Chloride ions (Cl⁻):
- One of the most aggressive species causing SCC, particularly in stainless steels and aluminum alloys.
- Found in seawater, deicing salts, and industrial cooling waters.
- Leads to localized breakdown of passive oxide layers, creating weak points where microcracks can nucleate and propagate.
II. Hydrogen embrittlement (HE):
- Hydrogen penetration into the metal matrix weakens atomic bonding.
- Occurs in high-strength steels, titanium alloys, and nickel-based alloys.
- Common in welded components exposed to hydrogen-rich environments (e.g., electrochemical reactions in acidic solutions).
- Hydrogen-assisted SCC can accelerate microcrack propagation by reducing the material’s ductility, making it more brittle.
III. High-temperature environments:
- SCC in boilers, heat exchangers, and refinery units occurs at elevated temperatures.
- Caustic SCC (Caustic Cracking): Develops alkaline environments in carbon steel pressure vessels.
- Thermal cycling not only increases stress but also enhances crack initiation at existing microcracks, making SCC progression more severe.
Microstructural changes leading to SCC
Intergranular vs. transgranular cracking
SCC manifests in two distinct crack propagation patterns:
I. Intergranular cracking:
- Crack growth along grain boundaries, where impurities and precipitates weaken the metal.
- Common in sensitized stainless steels, where chromium carbide formation depletes protective chromium at grain boundaries.
- Microcracks tend to nucleate at weakened grain boundaries before evolving into larger cracks.
- Often observed in nuclear reactor components and heat exchangers due to the critical combination of high operating temperatures, residual stresses generated during welding, and exposure to aggressive chemicals.
II. Transgranular cracking:
- Crack growth through the grains themselves, rather than along the boundaries.
- More common in nickel-based alloys and aluminum alloys.
- Microcracks typically initiate at surface defects or stress concentration points, progressing into larger cracks as SCC advances.
- Exhibits brittle fracture appearance under a microscope.
Environmental conditions that accelerate SCC
- High humidity: Water condensation facilitates chloride attack.
- Seawater exposure: Combines high chloride content with mechanical stress from waves and currents.
- High pH solutions: Caustic cracking in boilers and refinery pipelines.
- Thermal cycling: Frequent temperature changes induce expansion/contraction, leading to the formation and widening of microcracks.
Real-world SCC failures
I. Pipeline ruptures:
- SCC has caused catastrophic gas and oil pipeline failures, leading to environmental disasters.
- Microcracks initiated by residual stresses and chloride exposure have been found as precursors to large-scale pipeline failures.
- Example: TransCanada Pipeline SCC failure due to Residual stress es and chloride exposure.
II. Nuclear reactor vessel failures:
- SCC in reactor coolant systems has led to steam generator tube leaks, compromising safety.
- Intergranular microcracks were identified as the primary failure mechanism in several nuclear plant incidents.
- Example: SCC in Inconel tubing within pressurized water reactors (PWRs).
III. Aircraft structural failures:
- SCC in airframe aluminum alloys can lead to crack growth in fuselage panels.
- Undetected microcracks were identified as contributors to the catastrophic failure of several aircraft components.
- Example: Aloha Airlines Flight 243 accident, where SCC-induced cracks contributed to structural failure.
Susceptible materials and conditions
Which materials are susceptible to stress corrosion cracking?
Not all metals exhibit susceptibility to stress corrosion cracking (SCC), but certain alloys, particularly those with passive oxide layers, are more vulnerable under specific environmental conditions. Stainless steels, nickel-based alloys, and carbon steels are among the most commonly affected materials, depending on their exposure to chloride-rich, alkaline, or hydrogen-containing environments.
Stainless steel SCC: Common failure cases in industry
Austenitic stainless steels (304, 316, 321) are especially prone to chloride-induced SCC (Cl-SCC) due to their reliance on a chromium oxide passive layer for corrosion resistance. When exposed to chlorides in humid environments or seawater, this protective layer can break down, leading to the initiation and propagation of microcracks.
- Common failure cases: Offshore platforms, desalination plants, cooling water systems, heat exchangers.
- Example: Stainless steel tubing in a nuclear power plant suffered catastrophic Cl-SCC due to prolonged exposure to steam containing chlorides.
Nickel-based alloys vs. carbon steels: SCC reaction differences
- Nickel-based alloys (e.g., Inconel, Hastelloy): Highly resistant to SCC due to their strong passivation properties, making them ideal for extreme conditions in nuclear reactors and chemical processing plants. However, if microcracks do form, they can be difficult to detect due to the high fracture resistance of these alloys.
- Carbon steels: Generally resistant to Cl-SCC but susceptible to hydrogen-induced cracking (HIC) and sulfide stress cracking (SSC) in hydrogen sulfide-rich environments, such as oil and gas pipelines.
Impact of corrosion materials in different environments
- Marine environments: Chloride SCC in stainless steel.
- Industrial environments: Caustic SCC in carbon steels.
- High-temperature environments: Oxidation-assisted SCC in superalloys.
Methods to increase SCC resistance through material selection and stress reduction
- Material selection: Using ferritic stainless steels (e.g., 430, 446) or duplex stainless steels that have higher resistance to Cl-SCC.
- Stress relief techniques: Post-weld heat treatment to reduce residual stress.
- Protective coatings: Inhibitor coatings for oil & gas pipelines.
- Environmental control: Reducing chloride exposure via deionized water or non-chloride-based descalers.
Characteristics of stress corrosion cracking
How SCC differs from other forms of cracking
SCC is distinct from other failure mechanisms because it combines chemical and mechanical stress factors. It differs from:
- Fatigue cracking: Occurs due to cyclic loading, independent of corrosive environments.
- Hydrogen embrittlement: Caused by hydrogen absorption but does not necessarily require a corrosive medium.
- General corrosion: Uniform material loss rather than localized cracking.
Intergranular vs. transgranular cracking
SCC propagates in two primary modes:
I. Intergranular cracking:
- Occurs along grain boundaries due to segregation of impurities or depletion of corrosion-resistant elements (e.g., chromium in stainless steels).
- Seen in sensitized stainless steels and heat-affected zones of welds.
- Microcracks initiate within the grain boundaries, eventually leading to larger crack formations that result in mechanical failure.
II. Transgranular cracking:
- Propagates through the crystal grains themselves, forming brittle fracture patterns.
- Common in nickel-based alloys and high-strength steels.
Microstructural characteristics under electron microscopy
- Intergranular SCC appears as branched cracks following grain boundaries.
- Transgranular SCC shows cleaved-like structures with sharp crack tips.
- Microcracks form at stress concentrators and can propagate rapidly once they reach critical size.
Crack propagation rate and detection challenges
SCC is dangerous because it progresses undetected until failure occurs. Unlike fatigue cracks, SCC grows without warning, and traditional visual inspection techniques often fail to detect early-stage cracks. Early detection of microcracks is crucial, as once they develop, propagation can occur rapidly.
- Non-destructive test (NDT) methods such as Eddy Current Testing (ECT) and Acoustic Emission Monitoring (AEM) are essential for detecting microcracks in early stages.
Failure patterns: Why SCC leads to sudden and unexpected failures
- SCC initiates with microcracks at stress concentration points, which propagate beneath the material surface (subsurface), often undetectable by standard visual inspection.
- It frequently occurs in high-stress areas, such as welds, pipe bends, and pressurized vessels, where tensile stresses amplify microcrack formation and progression.
- Unlike uniform corrosion, SCC can lead to catastrophic failure with minimal material loss, resulting in instantaneous rupture once cracks reach a critical size.
Understanding these failure patterns is key to developing preventative maintenance strategies and ensuring long-term asset reliability.
SCC in pipelines and welds
What is stress corrosion cracking in pipelines?
SCC in pipelines is one of the most significant integrity threats in the oil, gas, and chemical industries. Pipelines are exposed to high internal pressures, fluctuating temperatures, and corrosive substances, making them highly susceptible to SCC-related failures
Pipeline-specific SCC failure causes
- High-pressure hydrogen SCC: Occurs in pipelines transporting hydrogen-rich fuels, where hydrogen absorption leads to embrittlement and crack initiation.
- Near-neutral pH SCC: Found in buried gas pipelines, typically caused by groundwater infiltration containing aggressive species like bicarbonates and chlorides.
- High-temperature SCC: Affects pipelines exposed to steam or superheated fluids, accelerating crack propagation due to microstructural changes and oxidation.
How SCC affects welds?
Welded joints are high-risk areas for SCC due to residual stress buildup from the welding process, which enhances crack formation and propagation.
- Poor welding practices create localized heat-affected zones (HAZ) that are more prone to SCC due to metallurgical changes.
- Improper alloy composition in filler materials can lead to weld cracking, especially in environments with high chloride exposure.
- Stress concentration at weld defects accelerates microcrack initiation and subsequent SCC progression.
Which of the following welds are highly resistant to chloride SCC?
- Duplex stainless steel welds (e.g., 2205, 2507) provide superior resistance to SCC by balancing ferrite and austenite phases.
- Nickel-based filler materials (Inconel 625, Hastelloy) significantly reduce SCC risks in welded structures.
- Low-stress weld procedures (post-weld heat treatment) minimize residual stress, enhancing SCC resistance.
The role of residual stress in welded joints
- Residual stress or tensile stress in the HAZ significantly increases SCC risk, especially in environments with chlorides or hydrogen.
- Post-weld annealing or mechanical stress relief techniques (e.g., shot peening, cold rolling) help mitigate residual stress, reducing SCC susceptibility.
- Shot peening or compressive stress treatments improve weld durability by introducing compressive surface stresses that counteract SCC initiation
Case study: SCC failure in high-pressure gas pipelines
In 2019, a refinery located in the Gulf of Mexico experienced multiple failures in critical pipelines due to SCC, resulting in significant production losses and costly unscheduled downtime. Traditional inspection methods like visual inspections, Magnetic Particle Inspection (MPI), and Liquid Penetrant Inspection (LPI) were limited, slow, and operator-dependent, proving insufficient for accurate and timely detection of SCC.
Eddyfi technological solution
To address this challenge, Eddy Current Array (ECA) technology from Eddyfi, specifically the Sharck™ equipment, was implemented. This tool employs induced currents to detect and accurately size cracks caused by SCC. Additionally, Eddyfi’s Phased Array Ultrasonic Testing (PAUT) technology, using the Gekko® system, was deployed for confirmation and validation of deeper and more complex findings.
Implementation
Specific areas prone to SCC were identified, including welds, joints, and areas with high residual stress levels. The Sharck™ equipment initially conducted a rapid and effective surface sweep, identifying early-stage cracks in specific regions. Subsequently, the Gekko® PAUT technology was employed for detailed analysis, obtaining real-time ultrasonic imaging to assess the precise depth and extent of each identified defect.
Results achieved
- Early and precise detection of SCC prevented potential structural failures that could have had catastrophic consequences.
- Significant reduction in inspection time compared to conventional techniques.
- Reliable digital data facilitated subsequent analysis and informed predictive maintenance decisions.
- Estimated operational cost savings of approximately USD $2 million due to drastically reduced unplanned downtime. This case underscores the critical need for proactive SCC management in pipeline networks, focusing on residual stress control and early crack detection.
Detection, testing, and inspection techniques
How to coupon metals for stress corrosion cracking: Laboratory and field testing methods
To assess a material’s susceptibility to stress corrosion cracking (SCC), industries use standardized coupon testing, a method where metal samples (coupons) are exposed to controlled stress and corrosive environments.
- Laboratory testing: Coupons are subjected to accelerated SCC conditions, such as boiling magnesium chloride solutions for stainless steels (ASTM G36 is a widely used test for chloride SCC susceptibility).
- Field testing: Coupons are placed in real-world environments (e.g., seawater, refinery units) to evaluate SCC risks under operational conditions.
These tests aid engineers in selecting corrosion-resistant materials and optimizing environmental controls to minimize SCC risks. To reinforce the reliability of these methods, laboratory equipment is required to control the loading conditions during the tests. Metal coupon tests, used to evaluate the susceptibility of materials to SCC, require the application of precise and constant axial loads in controlled environments that simulate corrosive conditions.
In this context, the deadweight testers developed by Cortest allow to maintain stable stresses on metallic specimens during prolonged periods, enabling the monitoring of the material behavior under sustained stress. These tests evaluate the initiation and propagation of cracks by SCC and compare the resistance between different materials or treatments, facilitating decisions in material selection and pre-vention of failures in service.
Non-destructive testing (NDT) techniques for SCC detection
SCC is particularly difficult to detect because cracks often originate as microcracks beneath the surface. Non-destructive testing (NDT) is essential for early SCC identification:
I. Ultrasonic Testing (UT):
- Uses high-frequency sound waves to detect subsurface cracks.
- Highly effective for detecting SCC in pipelines and welds, even in early microcrack stages.
II. Radiographic Testing (RT):
- Uses X-rays or gamma rays to identify internal defects.
- Ideal for detecting hidden SCC cracks in thick-walled components where microcracks may be deeply embedded.
III. Eddy Current Testing (ECT):
- Employs electromagnetic induction to detect surface-breaking SCC.
- Commonly used for aircraft components and stainless steel heat exchangers.
Early detection to prevent catastrophic failures
Regular SCC monitoring reduces failure risks in pipelines, power plants, and aerospace structures. Combining periodic NDT inspections with AI-based monitoring systems enhances early SCC detection, preventing costly failures and ensuring long-term structural integrity.
Prevention and mitigation strategies
How to prevent stress corrosion cracking: Design improvements and stress relief techniques
SCC prevention requires a multi-faceted approach, integrating mechanical design modifications, material selection, and environmental controls. Since SCC initiates as microcracks, addressing stress concentration points and residual stress is critical.:
I. Reducing residual stress:
- Post-weld heat treatment (PWHT) relieves welding-induced stresses, reducing the likelihood of SCC initiation at microcrack sites.
- Mechanical stress relief techniques (e.g., shot peening, cold rolling) introduce compressive stresses, which counteract tensile stress that accelerates SCC formation.
II. Design improvements:
- Eliminating sharp corners, notches, and stress concentrators reduces the likelihood of microcrack formation at vulnerable sites.
- Optimizing drainage and fluid flow patterns prevents liquid stagnation in SCC-prone environments, reducing localized corrosion hotspots.
Material selection: Choosing corrosion-resistant alloys
Using SCC-resistant materials is one of the most effective long-term strategies for preventing failures. Key materials include:
- Duplex stainless steels (e.g., 2205, 2507): Offer high resistance to chloride SCC, widely used in offshore platforms and chemical processing.
- Nickel-based alloys (Inconel 625, Hastelloy C-22): Preferred for extreme environments in aerospace and nuclear applications, exhibiting superior SCC resistance even in high-stress conditions.
- Low-carbon stainless steels (316L, 317L): Minimize carbide precipitation, reducing intergranular SCC susceptibility.
Surface treatments and coatings to minimize SCC
- Passivation: Enhances protective oxide layers, limiting microcrack initiation sites in stainless steels.
- Electroplating: Nickel or zinc coatings form protective barriers, reducing SCC risk in aggressive environments.
- Ceramic coatings: Provide high-temperature SCC protection in turbine blades and jet engine components.
- Weld overlay: Weld Overlay is an effective technique for mitigating SCC, as it provides a protective layer of corrosion-resistant material over the substrate. It is used in pipelines, heat exchangers, and pressure vessels exposed to aggressive environments. However, if proper post-weld heat treatment is not performed, it can introduce new residual stresses that promote SCC instead of preventing it.
How to avoid stress corrosion cracking: Practical tips for engineers
- Minimize exposure to chlorides in cooling water and industrial processes to reduce SCC risks.
- Use cathodic protection in underground pipelines to mitigate electrochemical reactions leading to SCC.
- Apply corrosion inhibitors (e.g., molybdate-based inhibitors) in cooling systems to slow SCC propagation.
Use of inhibitors and protective coatings in industries
- Oil & Gas: SCC-resistant coatings (e.g., fusion-bonded epoxy for pipelines) protect against environmental chloride attack. However, these coatings can degrade over time, develop microcracks, or experience localized failures, allowing corrosive agents to penetrate and initiate SCC beneath the protective layer.
- Aerospace: Anodized aluminum coatings prevent SCC in aircraft fuselage structures by enhancing surface protection. However, they do not mitigate tensile stress within the base material, meaning SCC can still occur if stress factors are not controlled.
- Nuclear power: Nickel-based claddings in steam generator tubing protect against SCC in high-radiation environments. Despite their effectiveness, cladding defects, improper application, or localized damage can expose the underlying material to SCC risks over time.
Industry best practices for SCC prevention
- Oil & Gas: Implementing SCC monitoring programs in high-pressure pipelines to detect microcracks before critical failures occur.
- Aerospace: Routine eddy current inspections of aircraft components for early SCC detection.
- Nuclear power: Maintaining strict water chemistry controls to prevent chloride-induced SCC in reactor systems.
By proactively integrating these strategies, industries can reduce SCC-related failures, increase equipment lifespan, and enhance operational safety.
Future trends and advances in SCC mitigation
New materials development: High-entropy alloys and ceramic coatings
Advancements in metallurgy have led to the development of high-entropy alloys (HEAs)—multi-component metal mixtures with exceptional SCC resistance. These materials are being tested for nuclear reactors and deep-sea oil drilling applications, where extreme conditions accelerate SCC-related failures.
Additionally, next-generation ceramic coatings with superior resistance to high-temperature oxidation and SCC are emerging, offering enhanced durability for turbine blades and aerospace components.
Advanced monitoring systems: AI-driven SCC detection
Artificial Intelligence (AI) and Machine Learning (ML) are revolutionizing SCC detection and prevention by analyzing real-time sensor data to predict early-stage SCC initiation.
- Predictive maintenance algorithms detect stress-induced microcrack formation before cracks become visible.
- Automated drones and robotic crawlers equipped with NDT tools are being deployed to inspect hard-to-reach pipeline sections, improving SCC detection efficiency.
AI-based SCC monitoring is already being integrated into offshore oil platforms, nuclear plants, and aerospace maintenance programs, reducing unexpected failures.
Sustainability in SCC prevention: Green inhibitors and eco-friendly materials
- Green corrosion inhibitors (e.g., plant-derived organic compounds) are replacing traditional toxic inhibitors in industrial applications.
- Eco-friendly SCC-resistant coatings reduce the environmental impact of chemical treatments.
What’s next? Industry projections for SCC management
The future of SCC mitigation will be driven by:
- Development of self-healing materials that regenerate protective oxide layers after SCC-induced damage.
- Expansion of AI-driven corrosion monitoring across critical infrastructure.
- Widespread adoption of SCC-resistant superalloys in energy, defense, and transportation sectors.
By embracing these cutting-edge innovations, industries can achieve long-term SCC mitigation, reduce environmental impact, and enhance safety across critical infrastructure.
Conclusions
Stress corrosion cracking (SCC) remains one of the most insidious and catastrophic forms of material degradation, threatening the integrity of critical infrastructure across multiple industries. Its ability to develop microcracks and progress undetected until sudden failure makes SCC a silent yet formidable challenge in oil & gas, nuclear power, aerospace, and marine engineering. Understanding its underlying mechanisms—where tensile stress, corrosive environments, and material susceptibility converge—is essential to mitigating its risks.
Advancements in detection, inspection, and non-destructive test, such as Ultrasonic Testing (UT), Radiographic Testing (RT), and AI-driven predictive maintenance, are revolutionizing early SCC detection. Meanwhile, prevention strategies are evolving, with industries embracing stress relief methods, corrosion-resistant alloys, protective coatings, and advanced inhibitors to extend asset lifespan and reduce failures before they become catastrophic.
Looking ahead, the future of SCC mitigation lies in self-healing materials, high-entropy alloys, AI-driven monitoring systems, and eco-friendly corrosion inhibitors. As industries push toward sustainability and resilience, investing in SCC research and advanced engineering solutions will be crucial. By staying ahead of emerging SCC threats, industries can safeguard critical infrastructure, ensuring safety, reliability, and longevity in the face of one of the most persistent challenges in material science.
References
Own source