Table of Contents
- Introduction
- What are protective coatings and what is their function?
- Main coatings inspection methods
- Surface profile evaluation
- Visual inspection and defect detection in coatings
- Discontinuity detection tests
- Technological advances that are transforming coatings inspection
- Benefits of efficient coating inspection
- Importance of surface preparation in coatings
- Compliance with industrial coating standards
- The coating inspector: A key factor
- Recent data and statistics
- Success stories in the application of inspection methods
- Conclusions
- References
Introduction
Coatings inspection is an essential process within industrial asset management. Its main function is to ensure that industrial coatings meet established standards, ensuring effective protection against corrosion, abrasion and other adverse environmental factors. To achieve this, key characteristics such as thickness, adhesion test and resistance of the coating under different conditions are evaluated.
In this article, we will discuss the most effective coatings inspection methods, the benefits of their application and the technological advances that are revolutionizing this discipline in the industry.
What are protective coatings and what is their function?
Protective coatings are materials designed to be applied to industrial surfaces to protect them against corrosion, abrasion, chemical agents and adverse environmental conditions. Their main function is to prolong the useful life of assets and preserve their structural integrity, preventing deterioration caused by external factors. An important aspect in the effectiveness of coatings is the surface preparation, since the correct adherence and performance of the applied material depends on it.
Its usefulness is important for the management and control of the protective coatings process, standing out in:
- Protection against corrosion and oxidation.
- Resistance to wear and friction.
- Defense against extreme weather conditions.
- Protection against chemical agents and natural contaminants.
- Increased resistance to shocks, impacts and stains.
- Aesthetic improvement through color and decoration.
- Facilitates cleaning and maintenance.
The most commonly used types of coatings include industrial paints, epoxy coatings and advanced polymeric systems, designed to suit different environmental conditions and industrial needs.
Main coatings inspection methods
There are multiple techniques to evaluate the quality and effectiveness of an applied coating. The main methods used in the industry are discussed below:
Coating thickness measurement
The thickness of the coating is a key parameter to ensure its performance and durability. Proper application ensures protection against corrosion, wear and other environmental factors. To measure it accurately, different coating thickness gauges and devices are used depending on the type of substrate and coating:
- Magnetic and electromagnetic thickness gauges: Ideal for metallic surfaces, they allow to accurately evaluate the coating layer without damaging it.
- Ultrasonic gauges and probes: Used on non-metallic substrates or multilayer coatings, providing detailed measurement without direct contact.
- X-ray fluorescence technique: It allows determining the thickness and chemical composition of coatings on different types of materials, being especially useful in advanced industrial applications.
Correct thickness measurement is essential to ensure that the coating meets quality standards and provides the expected protection in each application.
Coating adhesion test
The adhesion of a coating to its substrate is essential to ensure its durability and strength. However, poor surface preparation can compromise adhesion and significantly reduce the effectiveness of the coating.
Different methods, such as the cross-cut adhesion test and the tear-off adhesion test, make it possible to evaluate the quality of the bond between the coating and the surface. These tests confirm whether the surface preparation was performed correctly or if there are problems that could affect the protection of industrial assets. The most common procedures are listed below:
- Cross-cut test: This method is widely used to evaluate the adhesion of thin coatings. It is a quick and easy test, ideal for field inspections.
- Scrape adhesion test: In this test, a device with a blade or rounded tip is moved over the coated surface while the applied load is gradually increased. The objective is to determine the load required for the coating to peel or fail. This method is useful for evaluating the resistance of the coating to mechanical forces and is commonly employed in laboratory settings.
- Pull-Off test: Considered one of the most quantitative tests for measuring adhesion, this method involves adhering a load-bearing device, known as a “dolly” or “platen”, to the surface of the coating using a suitable adhesive. Once the adhesive has cured, a perpendicular tensile force is applied to the surface until the coating peels off. The force required for this release is measured and reported in units of pressure, such as psi or MPa. This method provides a direct measure of bond strength and is applicable to a wide variety of coatings and substrates.
The selection of the appropriate test method depends on several factors, including the type of coating, the substrate and the expected service conditions.
How is a coating adhesion test performed?
The main activities involved in each of the mechanical tests used to measure coating adhesion are described below:
Pull-Off Test Procedure
This method quantifies the force required to detach the coating from the surface using a pulling device. The procedure consists of:
- Sample preparation: A metal disk (dolly) is adhered to the coating with a strong adhesive.
- Adhesive curing: Wait the necessary time for the bond between the disc and the coating to be firm.
- Application of tensile force: A mechanical or hydraulic device is used to apply a force perpendicular to the surface.
- Failure point recording: The amount of force applied in units of pressure (psi or MPa) until the coating peels off is measured.
This method provides a quantifiable value of adhesion and allows to determine whether the failure occurs in the coating, at the interface with the substrate or within the coating material itself.
Cross-Cut Test Procedure
It is a quick and simple test used mainly in thin coatings. Its procedure is as follows:
- Making lattice cuts: A special blade is used to make grid cuts on the coated surface.
- Tape application: A high adhesion adhesive tape is placed and pressed on the grid.
- Tape removal and visual evaluation: The tape is removed quickly and the amount of coating that comes off is inspected.
The result is classified according to the amount of material that has come off, which indicates whether the adhesion is adequate or if there are problems in the application of the coating.
Scrape Adhesion Test Procedure
This method evaluates the resistance of the coating when scraped with a blade or metal tip. The procedure includes:
- Application of a progressive load: Equipment is used to gradually increase the pressure on the coated surface.
- Peel resistance observation: The point at which the coating begins to fail and peel from the substrate is determined.
It is a useful test to evaluate the mechanical resistance of the coating under impact or abrasion conditions.
Importance of adhesion testing
Adhesion testing is essential to ensure that the coating meets quality standards and can perform its protective function effectively. These tests allow:
- Detect failures in the application of the coating.
- Evaluate the compatibility between the coating and the substrate.
- Ensure the durability of the coating under extreme operating conditions.
- Optimize application processes to improve efficiency and reduce costs.
The selection of the appropriate method will depend on the type of coating, substrate and industry requirements. In many cases, it is recommended to combine several tests to obtain a more accurate evaluation.
Surface profile evaluation
Before applying a coating, it is crucial to ensure that the surface has the proper roughness. The following are used:
- Roughness profile comparators, to verify surface preparation.
- Digital roughness testers, which offer a more accurate evaluation.
Visual inspection and defect detection in coatings
Visual inspection is the first step in detecting problems. It is the most basic and essential method for evaluating the quality of a coating. It is based on the naked eye examination of the surface to identify defects such as blisters, cracks, corrosion, bubbles, discoloration, inclusions and discontinuities. Although it is a simple technique, its effectiveness depends on the experience of the inspector and the lighting conditions in which it is performed.
To improve the accuracy of this inspection and detect anomalies that might go unnoticed, we use specialized tools such as:
- UV lamps: Ideal for inspecting fluorescent coatings and revealing defects in applications requiring high precision.
- High resolution cameras: They allow to document and analyze in detail the surface of the coating, facilitating the identification of irregularities and ensuring a better quality control.
Discontinuity detection tests
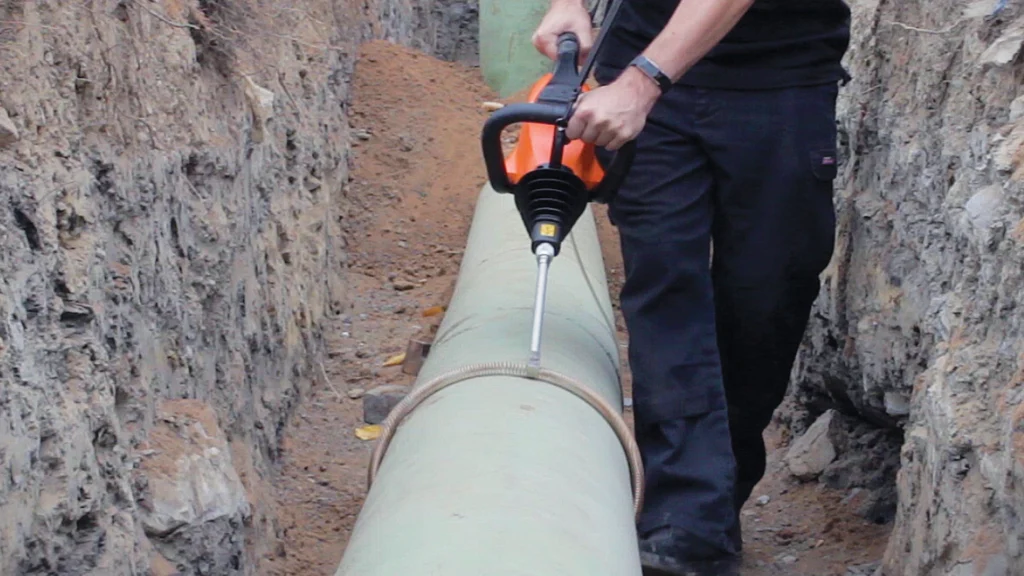
In addition to visual inspection, advanced methods are used to detect defects that are not visible to the naked eye, ensuring the integrity and continuity of the coating. Among the most commonly used tests are:
- Wet sponge test: It is used to identify discontinuities in thin coatings. It consists of applying a sponge moistened with a conductive solution on the coated surface while measuring the electrical resistance. Any variation in the signal indicates the presence of a defect.
- Holiday test: Used on thicker coatings to detect imperfections or areas where protection could be compromised. A high voltage current is applied to the surface and, if there is a discontinuity, an electric arc is generated to pinpoint the location of the defect.
Companies such as Elcometer offer innovative solutions in the inspection of industrial coatings, facilitating the inspection of the condition of the coating by means of high voltage porosity detectors (Holiday Detectors). This equipment allows efficient and reliable detection of discontinuities in thicker coatings, identifying pores, cracks and defects that compromise corrosion protection.
The Elcometer 266 inspects coatings up to 7.5 mm with automatic voltage adjustment, while the Elcometer 280, with pulsed DC technology, allows ungrounded fault detection, ideal for large surfaces and pipelines. Both models feature accurate test voltage, sensitive alarms and robust design for demanding industrial applications.
Technological advances that are transforming coatings inspection
Coatings inspection has undergone a significant transformation thanks to the adoption of innovative technologies that optimize accuracy, reduce evaluation times and improve process safety. Among the most notable advances are:
- Drones with high-resolution cameras: Allow inspection of difficult-to-access surfaces without the need for scaffolding or direct human intervention, reducing risks and operating costs.
- 3D scanning systems: Generate detailed, real-time representations of the condition of coatings, facilitating more accurate defect analysis and wear monitoring.
- Smart sensors: Incorporated in coated structures, these devices measure wear in real time and issue alerts for preventive maintenance, avoiding premature failures and optimizing the useful life of coatings.
These advances not only streamline inspection processes, but also allow for more efficient maintenance management, reducing costs and minimizing environmental impact.
Benefits of efficient coating inspection
Implementing rigorous coating inspection on industrial coatings offers multiple advantages, including:
- Increased asset reliability: Protects structures against corrosion and wear, prolonging their useful life.
- Reduced operating costs: Minimizes unplanned repairs and premature replacements.
- Predictive maintenance: Allows to anticipate failures and optimize the planning of interventions without affecting production.
- Optimization of industrial processes: Facilitates the planning of preventive maintenance and avoids unnecessary shutdowns.
- Regulatory compliance: Guarantees compliance with quality standards required by national and international organizations.
- Corrosion protection: Ensures that the assets maintain their structural resistance to aggressive agents.
- Structural integrity inspection: Verifies that coatings retain their protective function over time.
- Sustainability and safety: Reduces environmental impact and protects working conditions in critical industries.
Importance of surface preparation in coatings
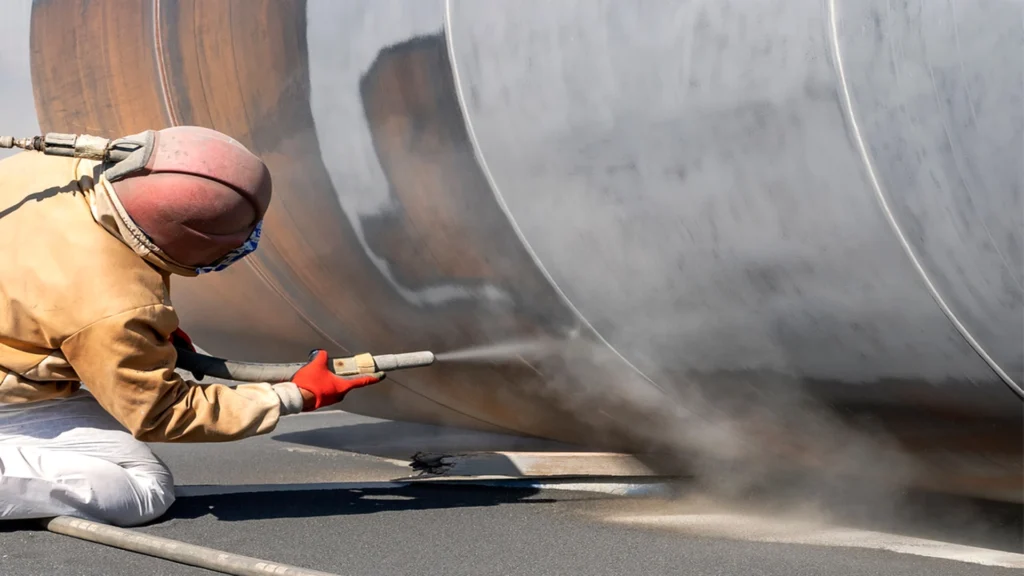
Surface preparation is a critical step prior to the application of protective coatings, as it directly influences the durability and effectiveness of the corrosion protection. A properly prepared substrate ensures that the coating adheres uniformly and fulfills its function of protecting industrial assets against adverse conditions.
In industries such as energy and petrochemical, where metal structures and pipelines are constantly exposed to corrosive agents, extreme temperatures and other deteriorating factors, poor surface preparation can drastically shorten the service life of coatings.
Among the main benefits of good surface preparation are the following:
- Corrosion prevention: Corrosion is one of the main challenges in the industry. Techniques such as shot blasting or abrasive blasting remove impurities such as calamine, oxides and deteriorated coatings, providing an optimal anchor profile for subsequent coating application. This is essential in chemical and petrochemical environments, where surfaces are exposed to aggressive substances. Poor adhesion can lead to detachment of the coating and leave structures vulnerable.
- Reduced maintenance costs: Good surface preparation minimizes premature failures, reducing corrective interventions and extending the life cycle of industrial assets.
- Sustainability: Optimizing surface preparation reduces the need for frequent replicate coatings and equipment replacement, reducing industrial waste generation and the environmental footprint of operations. It also helps to avoid environmental accidents resulting from spills or releases of hazardous substances.
- Safety in critical environments: In ATEX zones (explosive atmospheres) and areas where flammable products are handled, proper surface preparation mitigates risks, ensuring efficient coating application.
Poor preparation compromises the integrity of the coating and the equipment it protects, increasing the likelihood of serious incidents. Therefore, ensuring a proper preparation process not only improves operational efficiency, but also enhances the safety and reliability of industrial assets.
Compliance with industrial coating standards
Compliance with industrial coating standards is essential to guarantee the quality, durability and safety of protected surfaces. These regulations establish specific standards on the application, inspection and performance of coatings, ensuring that they meet the technical and operational requirements of each industry.
Different sectors, such as energy, petrochemical, automotive and infrastructure, require coatings that protect assets against corrosion, wear and chemical agents. To this end, international organizations have developed regulations and certifications that establish the performance criteria that coatings must meet and the appropriate inspection procedures.
Some of the most important coating standards include:
- NACE/AMPP (National Association of Corrosion Engineers/Association for Materials Protection and Performance): One of the most influential organizations in corrosion control and protective coating performance. Its standards, such as NACE SP0188 and NACE SP0178, provide detailed guidelines for the inspection and application of coatings on industrial structures, ensuring their corrosion resistance under demanding conditions.
- ISO 12944 – Corrosion protection of steel structures by paint systems: This international standard defines the requirements for the selection and application of coatings on steel structures exposed to different levels of corrosion. It includes durability tests, paint system recommendations and inspection methods to ensure optimum long-term performance.
- SSPC (Society for Protective Coatings): Standards for surface preparation and protective coatings, SSPC establishes criteria for cleaning, application and quality control of coatings. Standards such as SSPC-SP10 (abrasive blast cleaning to near-white metal) and SSPC-PA2 (coating thickness measurement) are widely used in the industry.
- ASTM (American Society for Testing and Materials): This organization establishes test methods to evaluate the quality and adhesion of coatings. Standards such as ASTM D4541 (tensile adhesion test) and ASTM D3359 (cross-cut test) verify the resistance of coatings and their ability to withstand adverse operating conditions.
- Environmental and safety regulations: In addition to technical standards, regulatory compliance in industrial coatings also encompasses environmental and occupational safety regulations. Standards such as the VOC Directive in Europe and EPA (Environmental Protection Agency) regulations in the U.S. set limits on the use of volatile organic compounds (VOCs) in paints and coatings to reduce environmental impact and improve workplace safety.
Compliance with coating standards ensures the protection of industrial assets and prolongs their useful life.
The coating inspector: A key factor
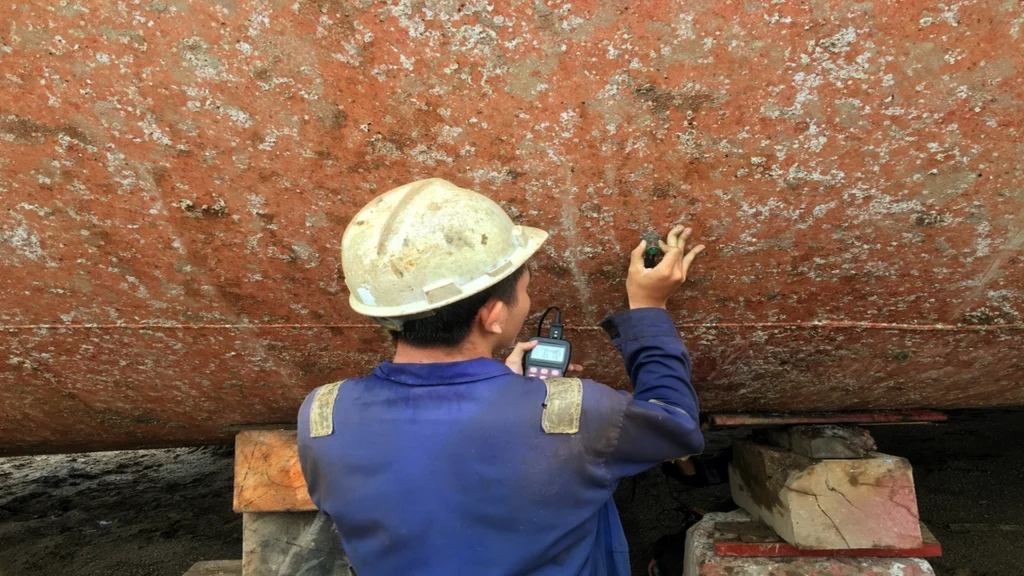
The quality of coating inspection depends not only on the technologies and methods used, but also on the experience and training of the coating inspector. Their work ensures that coatings meet the quality, safety and durability standards demanded by the industry.
A trained coating inspector not only detects defects, but is also able to identify problems in surface preparation, application and curing of the material. To ensure rigorous quality control, it is essential to have recognized certifications, such as:
- Review of the design and engineering specifications, verifying the adequate coating specified by the client according to the service to be provided in its operation.
- Evaluation of the condition of the surface prior to the application of the coating, verifying that it meets the requirements of cleanliness and anchorage profile.
- Supervision of the application process, ensuring that the specifications of thickness, adhesion and adequate environmental conditions are followed.
- Performing quality tests and trials, such as thickness measurement, adhesion and discontinuity detection.
- Generation of inspection reports, documenting findings, defects and recommendations to ensure coating effectiveness.
Training and certification of inspection personnel
To ensure rigorous quality control in coatings inspection, it is essential to have personnel certified in coatings standards and specialized methodologies. Some of the most recognized certifications worldwide include:
- NACE/AMPP (Coating Inspector Program – CIP): The AMPP (formerly NACE) certification program is one of the most prestigious in the coatings industry. It provides expertise in the evaluation, application and inspection of protective coatings, with levels ranging from basic (CIP Level 1) to advanced (CIP Level 3).
- SSPC (Society for Protective Coatings): It offers programs such as the Protective Coating Inspector (PCI), focused on the inspection of industrial coatings, including surface preparation and regulatory compliance.
- FROSIO (Norwegian Professional Council for Education and Certification of Inspectors of Surface Treatment and Insulation): It is a widely recognized certification in the oil and gas industry, focused on inspection of coatings and surface treatment.
- ASTM certification and specialization courses: In addition to formal certifications, training programs based on ASTM standards, such as adhesion testing (ASTM D4541, ASTM D3359) and thickness gauging (ASTM D7091), complement the technical training of inspectors.
Coatings inspection is a discipline that requires not only technical knowledge, but also experience and professional judgment to assess the quality of the work performed. Investment in training and certification of inspection personnel is undoubtedly a key strategy to ensure the longevity and reliability of assets protected with industrial coatings.
Below, a video courtesy of Weld Maniac presents the inspections every coating inspector should know about.

Recent data and statistics
- Anti-corrosion coatings market growth: In 2023, the anti-corrosion coatings segment led the specialty coatings market, reaching a valuation of US$1,388.9 million. This growth reflects the increasing demand for corrosion protection in various industries.
- Economic impact of corrosion: According to a 2016 study, the global cost of corrosion was estimated at approximately $2.5 trillion, representing 3.4% of global GDP in 2013. This data underscores the importance of implementing effective inspection and maintenance strategies to mitigate these costs.
Success stories in the application of inspection methods
The following is a case study of success in the oil industry related to the selection, cleaning, surface preparation, application, testing, inspections and compliance with engineering standards in the inspection of coatings:
Corrective maintenance of a 100,000 barrel crude oil storage tank
At an oil facility, a corrective maintenance project was carried out on a 100,000 barrel capacity crude oil storage tank, following API 653 guidelines. The main objective was to restore the integrity of the asset through mechanical repairs and the implementation of corrosion control methods.
Process implemented
- Initial inspection:
- A detailed inspection of the tank was carried out to evaluate its condition, identifying areas affected by corrosion and determining the necessary repairs.
- Surface preparation:
- High-quality abrasive cleaning was carried out, achieving a white or near-white metal cleanliness grade, according to SSPC-SP5 and SSPC-SP10 standards. This process completely removed contaminants such as oil, grease, dirt, mill scale and oxides, ensuring an optimum surface for coating application.
- Coating application:
- A coating system suitable for continuous immersion service was selected, guaranteeing high electrical resistivity and resistance to corrosive agents. The application was performed strictly following the manufacturer’s specifications and the recommended environmental conditions.
- Quality control and regulatory compliance:
- Throughout the process, inspections and tests were carried out to verify compliance with applicable engineering standards, ensuring the quality and durability of the applied coating.
Results obtained
- Restoration of tank integrity: Mechanical repairs and the application of the appropriate coating restored the structural integrity of the tank.
- Effective corrosion control: Proper surface preparation and coating application ensured effective corrosion protection, prolonging the life of the asset.
- Compliance with engineering standards: The project was executed in accordance with API 653, SSPC-SP5 and SSPC-SP10 standards, ensuring high quality and safety standards.
This case highlights the importance of proper coating selection, meticulous surface preparation and strict adherence to engineering standards to ensure the reliability and durability of assets in the oil industry.
Conclusions
Coatings inspection is a fundamental pillar in the protection of industrial assets, ensuring their durability and corrosion resistance. Implementing rigorous evaluation methodologies allows early detection of failures, optimizing maintenance costs and ensuring compliance with international standards.
In addition, technological advances, such as drones and smart sensors, are revolutionizing coating monitoring, reducing operational risks and improving industrial safety. Regular inspections not only extend the useful life of infrastructures, but also contribute to the sustainability and profitability of operations.
Protect your assets today with effective coating inspections!
References
- Defelsko Inspection instruments: “Métodos de prueba para la adhesión del revestimiento”
- Kings research: “Tamaño del mercado de recubrimientos especiales”
- MILTON JULIÁN BALLÉN FIALLO: Tesis de grado en Gestión de integridad de corrosión “MANTENIMIENTO CORRECTIVO DE TANQUE DE ALMACENAMIENTO DE CRUDO MEDIANTE INTERVENCIÓN MECÁNICA Y APLICACIÓN DE RECUBRIMIENTO”