Table of Contents
- Coker heater vs. delayed coker heater
- Key Difference: Heat transfer vs. controlled thermal cracking
- Common challenges in delayed coker heaters
- The importance of inspection in delayed coker heaters
- Recommended inspection methods
- Best practices for risk management
- Success stories and lessons learned
- Conclusions
- References
Delayed coker heaters play a critical role in the hydrocarbon refining industry, particularly in the delayed coking process, which maximizes the conversion of heavy residues into valuable products such as gasoline, diesel, and petroleum coke. These heaters rely on heater coils to transfer the necessary heat to thermally decompose heavier hydrocarbons, promoting their conversion into lighter fractions and petroleum coke.
However, delayed coker heaters operate under extreme conditions, including high temperatures, pressure, and the presence of corrosive compounds. These factors increase the risk of coke deposits forming in the coils, internal corrosion of materials, and thermal fatigue. Failures in these units not only reduce operational efficiency but also pose significant safety risks and result in substantial economic losses.
The purpose of this guide is to provide a practical and technical approach to the inspection and maintenance of delayed coker heaters, ensuring their optimal performance, minimizing risks, and maximizing efficiency in hydrocarbon refining.
Coker heater vs. delayed coker heater
In the refining industry, heaters play a key role in converting heavy residues into more valuable products. Within the coking process, it is essential to differentiate between a Coker Heater and a Delayed Coker Heater, as each serves specific functions in the thermal transformation of heavy hydrocarbons.
Coker heater: General heat transfer for the coking process
The Coker Heater is a conventional process heater used in various stages of coking and other refining applications. Its primary function is to transfer heat to residual hydrocarbons before they enter the next processing phase, facilitating the thermal breakdown of heavy compounds and improving product separation efficiency.
- Process location: It can be found at different points within a coking unit or other thermal processes.
- Operation: It operates at high temperatures but is not specifically designed for the direct conversion of heavy residues into coke.
- Application: Used in refineries to heat hydrocarbon flows without necessarily participating in the formation of coke within the coking drums.
Delayed coker heater: What are delayed coker heaters?
The Delayed Coker Heater is specifically designed for the delayed coking process, where the conversion of heavy residues into lighter fractions and petroleum coke is maximized. Its primary function is to raise the feed temperature to the thermal cracking point, ensuring that coking occurs inside the coke drums and not within the heater coils.
- Process location: Positioned just before the coking drums, ensuring the feed enters with the proper thermal energy for conversion.
- Operation: Handles high temperatures (480-500°C) and processes residual feedstocks with high asphaltene content, preventing premature coke formation inside the heater itself.
- Application: Specific to delayed coking units, where alternating coke drum operation requires precise thermal control to avoid blockages and efficiency losses.
Elements that make up the delayed coke heaters
Delayed coke heaters are composed of several key elements, which are:
- Coils: Internal tubes where the hydrocarbons to be heated circulate.
- Combustion chambers: Areas where heat is generated by burners.
- Heat exchangers: Systems that optimize heat transfer to reduce energy losses.
Key Difference: Heat transfer vs. controlled thermal cracking
While a Coker Heater can be used in various refining stages to heat hydrocarbons without inducing coke formation, the Delayed Coker Heater is designed to operate under extreme conditions in the delayed coking process, ensuring that residue transformation into coke occurs exclusively in the drums. Its design must prevent coke accumulation in the heater coils, making inspection and maintenance critical for unit safety and efficiency.
This differentiation is crucial to understanding the importance of inspecting and maintaining delayed coker heaters, which operate in high-temperature environments and severe conditions that demand advanced monitoring and cleaning strategies. In the following sections, we will explore the main operational challenges, inspection methodologies, and the best approaches for preventive maintenance of these essential refining units.
Common challenges in delayed coker heaters
Delayed coker heaters face various operational issues due to extreme operating conditions. The main challenges include:
- Coke deposits in coils: The accumulation of coke in the heater coils decreases thermal efficiency, obstructs hydrocarbon flow, and increases the risk of catastrophic failures due to overheating.
- Overheating and material wear: Prolonged exposure to high temperatures leads to the degradation of internal materials, compromising structural integrity and reducing component lifespan.
- Internal corrosion: The presence of acidic compounds in hydrocarbons, such as hydrogen sulfide, can severely damage the internal surfaces of coils and other heater components.
- Thermal fatigue: Frequent temperature fluctuations during operational cycles generate thermal stresses in materials, potentially causing cracks or structural failures.
The impact of these challenges not only affects plant productivity but also the quality and consistency of byproducts like petroleum coke, which can suffer from impurities or inefficient processing when equipment fails. Regular inspection and maintenance are essential to mitigate these challenges and ensure safe, efficient hydrocarbon processing.
The importance of inspection in delayed coker heaters
Regular inspection of delayed coker heaters is critical to prevent catastrophic failures and ensure compliance with international standards, such as API 530 and ASME Section VIII. These units operate under extreme conditions of temperature and pressure, making them vulnerable to issues such as wear, corrosion, and the buildup of petroleum coke in heater coils.
The primary goal of inspections is to ensure operational safety, maximize thermal efficiency, and extend equipment lifespan. This is achieved through several key actions:
- Detecting wear or corrosion: Identifying areas where materials have experienced thickness loss or degradation due to adverse operating conditions.
- Locating failures in welds and coils: Inspections can pinpoint cracks, leaks, or defects in welds that could compromise system integrity.
- Evaluating structural integrity: Verifying that major components, such as coils and combustion chambers, can withstand operating conditions.
Compliance with standards such as API 530 ensures inspections are conducted using standardized procedures, guaranteeing consistent results and reducing risks associated with unexpected failures.
Recommended inspection methods
Visual inspection
Visual inspection is the most basic yet essential method for evaluating the condition of delayed coker heaters. This process includes:
- Basic procedures: Identifying cracks, deformations, coke deposits, or visible wear on coils and other internal surfaces.
- Specialized tools: Using inspection cameras for hard-to-reach areas, such as internal tubes, to detect irregularities with greater precision.
Non-Destructive Testing (NDT)
NDT methods are crucial for obtaining detailed information without compromising equipment integrity:
- Ultrasound (UT): Measures wall thickness in coils and detects internal corrosion before it becomes critical.
- Industrial radiography (RT): Identifies weld defects, such as cracks or porosities, using X-rays or gamma rays.
- Magnetic particle testing (MT): Detects surface cracks in ferromagnetic materials using magnetic particles.
- Liquid penetrant testing (PT): Reveals fissures or cracks on external surfaces by applying contrasting liquids.
Online monitoring
Real-time monitoring is an advanced solution for continuously supervising the condition of heaters:
- Sensors: Detect variations in pressure, temperature, and emissions, enabling immediate responses to potential anomalies.
- IoT systems: Provide early alerts about operational conditions outside safe parameters, reducing the risk of catastrophic failures.
Preventive maintenance program
Designing an effective maintenance plan
A well-designed maintenance program ensures that delayed coker heaters operate efficiently and safely:
- Identification of critical points: Determine the most vulnerable areas, such as coils, welds, and burners.
- Recommended frequency: Perform regular inspections and cleaning based on operating conditions and applicable regulations.
- Historical record: Document all maintenance activities to identify patterns and optimize future procedures.
Decoking
The decoking process is essential for removing solid coke deposits, maintaining thermal efficiency, and preventing blockages:
- Mechanical methods: Use internal and external scrapers to remove solid coke deposits accumulated in the tubes.
- Chemical methods: Apply specific solvents that dissolve coke without damaging the coil materials.
To better understand the coil cleaning process in delayed coker heaters, here is an explanatory video from DDT Technology showcasing advanced technologies for coke removal in industrial tubes:
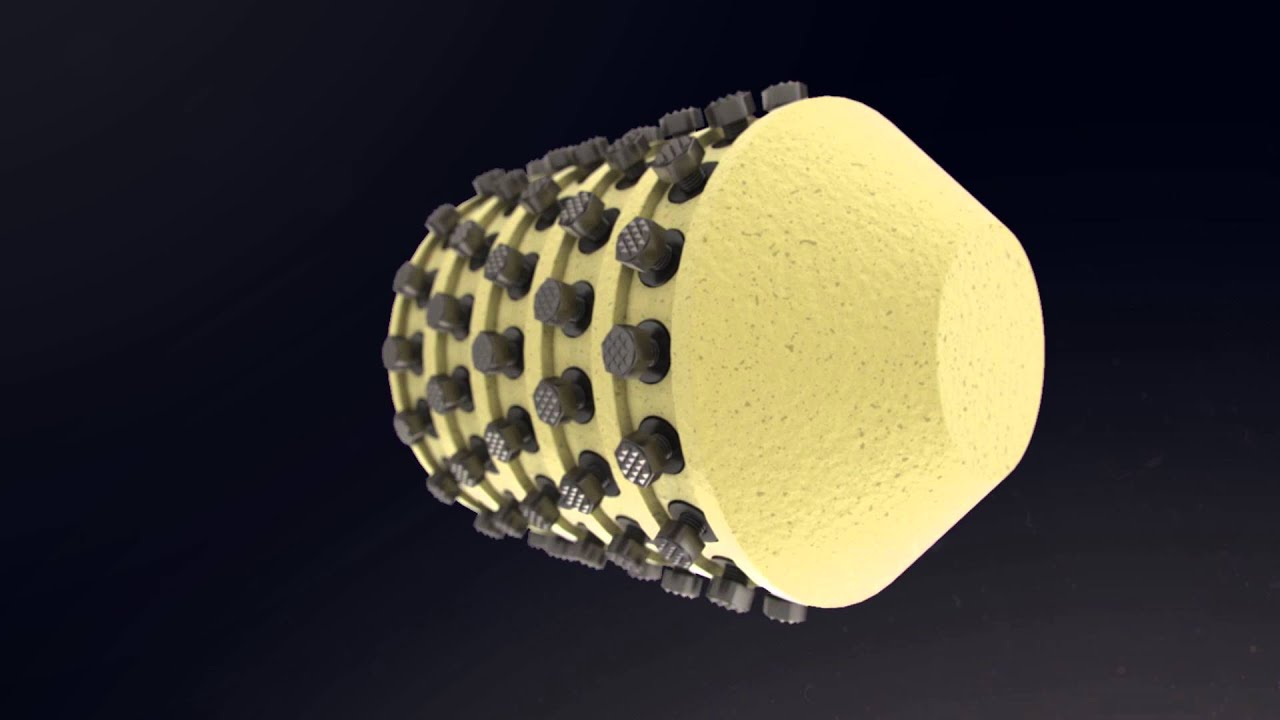
Advanced technologies in coke removal.
Repair and replacement of components
Keeping components in optimal condition prevents operational interruptions:
- Safe replacement: Substitute coils, joints, and other components following standardized procedures and regulations such as API 530.
- Weld repair: Use approved techniques to ensure the integrity of joints..
Inspection of burners and combustion chambers
Maintaining combustion systems ensures efficient heat transfer:
- Calibration and adjustment: Optimize burners to maximize thermal efficiency and reduce fuel consumption.
- Cleaning and repair: Remove buildup in combustion chamber refractories and repair structural damage.
Implementing a preventive maintenance program based on these actions ensures that delayed coker heaters operate safely, efficiently, and in compliance with industry standards..
Best practices for risk management
Risk management in delayed coker heaters is essential to ensure safety, minimize downtime, and maximize operational efficiency in hydrocarbon processing. One of the key practices is the implementation of regular safety audits during inspection and maintenance activities. These audits help identify potential risks, ensure compliance with international standards such as API 530 and ASME, and guarantee that operations are carried out under safe conditions.
Another critical aspect is technical staff training, ensuring that operators and technicians are well-versed in advanced inspection, maintenance, and handling procedures for critical equipment. This not only improves the quality of inspections but also reduces the risk of human error.
The use of advanced technology, such as digital twins, is also an invaluable tool for predicting failures and optimizing operations. Digital twins allow for simulating real operating conditions, analyzing thermal stress scenarios, and evaluating the impact of changes in operating parameters, facilitating data-driven decision-making.
Adopting these practices reduces risks while improving the safety and productivity of operations related to delayed coker heaters.
Success stories and lessons learned
BECHT
- Specialization: BECHT is an engineering and consulting firm with extensive experience in optimizing industrial processes, including improving the performance of delayed coker heaters.
- Proven results: BECHT has implemented solutions such as mechanical integrity analysis, thermal fatigue evaluation, customized chemical cleaning, and continuous monitoring systems using IoT. Their approach adheres to international standards such as API and ASME, ensuring quality outcomes.
Honeywell UOP
- Specialization: Develops technologies for refining processes, including maintenance and operation systems for delayed coker heaters.
- Proven results: Improved heater designs to enhance energy efficiency and reduce corrective maintenance by integrating remote monitoring tools and data analysis.
Siemens Energy
- Specialization: Focuses on digital solutions and advanced monitoring technologies for refining equipment.
- Proven results: Implemented IoT systems for real-time monitoring of delayed coker heaters, enabling failure detection and preventive maintenance planning.
These companies have demonstrated tangible results in optimizing delayed coker heaters by implementing inspection and maintenance practices based on advanced technology and international standards.
Conclusions
This guide has explored the fundamental aspects of inspecting and maintaining delayed coker heaters, from their importance in hydrocarbon refining to advanced methods for ensuring optimal performance. We have highlighted the most common operational challenges, such as coke buildup, internal corrosion, and thermal fatigue, as well as the available technical solutions, including non-destructive testing and online monitoring.
The implementation of preventive programs and the use of advanced technologies, such as digital twins and IoT sensors, make it possible to anticipate problems and reduce long-term costs. Inspection and maintenance are essential to prevent catastrophic failures, and represent a strategic investment to maximize productivity, thermal efficiency and operational safety of refineries.
We recommend establishing partnerships with specialized industrial inspection providers, such as BECHT, Honeywell UOP, and Siemmens Energy, which have proven track records of success in optimizing these units. Such collaborations ensure access to innovative solutions and practices aligned with international standards like API and ASME, improving performance and sustainability in hydrocarbon processing.
References
Own source