Table of Contents
- What is the cause and effect diagram?
- What are the categories used in a cause and effect diagram?
- Relationship with other quality tools
- Importance of the diagram in process optimization
- How to create a cause and effect diagram
- Benefits of using a cause and effect diagram
- Practical application cases
- Conclusions
- References
In today’s business and manufacturing world, optimizing processes is a guarantee for efficiency, cost reduction and quality improvement of products or services. Among the most commonly used tools to identify problems and promote effective solutions is the cause and effect diagram, also known as the Ishikawa diagram or fishbone diagram. This article discusses how the use of the cause and effect diagram can effectively optimize processes and solve problems, what are the most common categories used in its elaboration, and why it is so effective in problem-solving.
What is the cause and effect diagram?
The cause and effect diagram, developed by Dr. Kaoru Ishikawa in the 1960s, is a graphic tool used to identify and analyze the possible causes of a problem. Its fishbone structure has led to it also being referred to as a “fishbone diagram”. Its main objective is to organize and categorize the potential causes of a problem in a clear manner, allowing a systematic approach to problem-solving.
This diagram is commonly used in manufacturing, service and operations processes to break down the root causes of a problem, facilitating the implementation of effective solutions, and represents a fundamental tool within quality management that promotes continuous improvement and process optimization.
What are the categories used in a cause and effect diagram?
The Ishikawa diagram is generally structured in six main categories, known as the 6M. These are the most common, although they can be adapted according to the needs of the analysis:
- Human: Refers to the people involved in the process, such as operators, employees, or users. It analyzes factors such as training, skills, motivation and human error.
- Machines: Considers the equipment, machinery, tools, or technology used. It includes aspects such as maintenance, mechanical failures, age and incorrect adjustments.
- Material: Examines raw materials, components, or inputs used. Includes quality, specifications, availability, and variations in materials.
- Methods: Analyzes the processes, procedures, or practices followed. Includes process steps, standards, instructions and work methods.
- Environment: Examines external and environmental conditions that may affect the process. Includes temperature, humidity, lighting, noise and other environmental variables.
- Measurement: Refers to the measurement systems and tools used to control the process. It considers accuracy, calibration, error, and data collection methods.
If the analysis is non-manufacturing related, these categories can be adapted, using terms such as “Processes”, “People”, “Policies”, etc.
These categories provide a framework for breaking down and analyzing any problems, ensuring that important factors are not omitted during the root cause analysis.
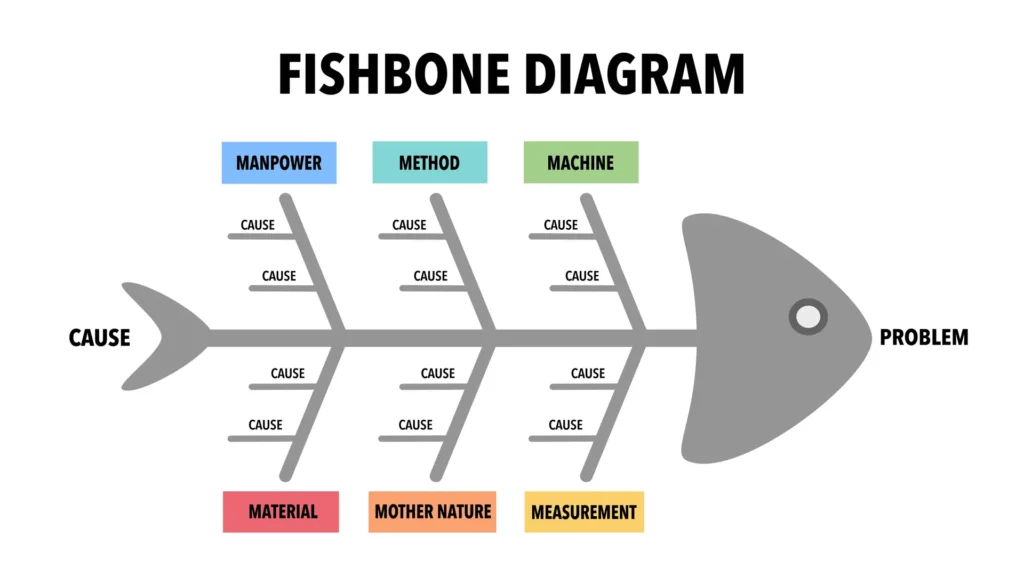
Relationship with other quality tools
The Ishikawa diagram does not act in isolation, but complements other quality tools, such as:
- Diagram: Helps to prioritize the most significant causes.
- Brainstorming: Generates an initial list of possible causes.
- SWOT analysis: Identifies strengths, opportunities, weaknesses, and threats related to the problem.
- Quality Circles: Promotes employee participation in problem-solving.
Together, these tools provide a comprehensive approach to problem analysis and process optimization.
Importance of the diagram in process optimization
Process optimization requires a structured approach to identify inefficiencies and bottlenecks. The Ishikawa diagram allows for a comprehensive root cause analysis, resulting in more effective solutions. Some main applications of the diagram include:
- Identification of recurring problems: Allows complex problems to be broken down into specific causes, facilitating the implementation of specific solutions.
- Facilitating teamwork: As a visual tool, the diagram encourages collaboration between different departments by identifying causes from multiple perspectives.
- Basis for continuous improvement: By identifying the causes of a problem, organizations can implement changes that not only solve the current problem, but also prevent future problems.
How to create a cause and effect diagram
1. Identify the problem (effect): The first step is to clearly define the problem or effect to be analyzed. It must be specific and relevant to the process in question.
2. Draw the basic structure: Draw a horizontal line from the problem to the left. This main line will be the “backbone” of the diagram. From this line, draw diagonal lines that connect and will represent the main categories of causes (6M).
3. Choose the main categories (the 6M): Organize the potential causes into main categories. The 6Ms (very common in manufacturing) are an excellent starting point. If the analysis is not related to manufacturing, these categories can be adapted, using terms such as “Processes”, “People”, “Policies”, etc.
4. Identify specific causes: In each main category, write down the specific possible causes that contribute to the problem. For this, use techniques such as:
- Brainstorming: Bring the team together and allow everyone to contribute possible causes.
- Direct observation: Examine the process in action to detect problems
- Data review: Analyze reports and statistics to identify trends and anomalies.
5. Drill down to root causes: For each cause identified, ask ‘Why’ several times (using the 5 whys technique) until the root cause is found. This avoids superficial solutions and ensures that actions are focused on the fundamental factors.
For example; in a high defect rate problem and the initial cause is untrained labor. You ask:
- Why? No regular training programs are offered.
- Why? There is no budget allocated for staff training.
- Why? Management prioritizes other areas of expenditure.
6. Review and validate the diagram: Share the diagram with the team to validate that all relevant causes have been included. If necessary, adjust or add new categories and causes.
7. Prioritize and plan corrective actions: With the diagram complete, prioritize the causes that have the greatest impact on the problem and develop an action plan to address them. Use tools such as the Pareto diagram to identify the most critical causes.
For example, if the root cause is “lack of training,” implement a training program.
If the problem is with materials, change suppliers or improve receiving and quality control of inputs.
8. Monitor results: Once corrective actions are implemented, evaluate their impact on the problem. If the prioritized.
Benefits of using a cause and effect diagram
The use of the Ishikawa diagram offers multiple benefits, including:
- Promoting collaboration: By involving multiple stakeholders in the creation of the diagram, communication, and teamwork is encouraged. Likewise, promoting the participation of all team members ensures that all perspectives are considered.
- Clarity and focus in problem identification: Provides a clear visual structure for analyzing complex problems. By categorizing causes, the team can focus on specific areas in a logical and orderly manner rather than addressing the problem in a general way.
- Prevention of recurring errors: By addressing root causes, implemented solutions are more effective and sustainable, preventing recurring problems.
- Quality and efficiency improvement: Helps identify key areas for improvement in processes and products.
- Cost reduction: By optimizing processes and eliminating inefficiencies, operating costs are reduced and profitability is improved.
- Facilitating teamwork: Encourages cross-departmental collaboration by analyzing the problem from multiple perspectives.
- Basis for continuous improvement: Identifies key areas for improvement, promoting progressive changes in processes.
- Greater precision in decision-making: Provides a clear view of root causes, allowing decisions to be made based on data rather than assumptions.
Practical application cases
The cause and effect diagram is used in a wide variety of industries, from manufacturing to services. Some examples include:
- Automotive industry: Identifying defects in components during assembly.
- Service industry: Improving customer service response times.
- Healthcare: Reducing medical errors in hospitals through root cause analysis.
- Education: Identification of factors that influence low academic performance.
Conclusions
The cause and effect diagram is a fundamental tool for root cause analysis, problem-solving and process optimization. Its ability to organize and categorize causes in a visual and structured manner makes it an indispensable resource for organizations seeking to implement continuous improvement. By addressing problems in a systematic and collaborative way, this diagram helps identify the causes of a problem, and also promotes a culture of quality and efficiency.
References
Own source