Introduction
Ceramic materials stand out for their exceptional mechanical properties, making them indispensable in a wide range of industrial applications. Their unique combination of strength, hardness, and thermal stability has driven their use in sectors requiring highly specialized materials. These mechanical properties not only define their performance under extreme conditions but also determine their ability to compete with other materials such as metals and polymers.
Ceramic materials are inorganic, non-metallic compounds formed by ionic or covalent bonds, which provide characteristics such as high hardness, wear resistance, and low thermal conductivity. However, these advantages also come with limitations, such as inherent brittleness and low tensile strength.
Among the most prominent properties, mechanical strength allows ceramics to withstand high loads in compression applications, while their remarkable hardness ensures excellent performance in highly abrasive environments. Nevertheless, their brittleness limits their use in applications requiring flexibility or ductility.
In industry, ceramic materials are fundamental for cutting tools, wear-resistant coatings, and high-temperature components such as ceramic coatings for thermal insulation and protection. Exploring these mechanical properties and their industrial applications reveals why ceramics are key materials in technological innovation.
Mechanical properties of ceramic materials
Mechanical strength
The mechanical strength of ceramic materials is characterized by their ability to withstand high loads, especially under compression. This high compressive strength is due to the nature of their chemical bonds, which provide significant structural rigidity, making ceramic coatings durable for various applications. However, this rigidity results in low tensile strength, as ceramics have a limited capacity to absorb deformations. Consequently, ceramics are inherently brittle materials.
For example, in applications such as ceramic bearings or refractory bricks, compressive strength is critical for withstanding intense mechanical forces without deforming. However, in applications where tensile stresses dominate, such as structural beams, their use is limited due to ceramic brittleness.
Hardness in ceramic materials
Hardness is one of the most distinctive properties of ceramic materials. Defined as resistance to scratching, penetration, or deformation, the hardness of ceramics is significantly higher than that of metals and polymers. This translates into excellent abrasion resistance, making ceramics ideal for cutting tools, industrial coatings, and abrasives.
In comparison, while metals are more ductile and can undergo plastic deformation under load, ceramics maintain their hardness even at high temperatures, thanks to their thermal stability. For instance, cutting tools made of silicon carbide or cubic boron nitride retain a sharp edge for extended periods in intensive industrial processes.
Furthermore, specific tests such as the Vickers and Knoop hardness tests are used to measure ceramic hardness, enabling the evaluation of their wear resistance and performance in adverse industrial environments. This property, combined with their chemical stability, makes ceramics the material of choice for environments where other materials cannot endure.
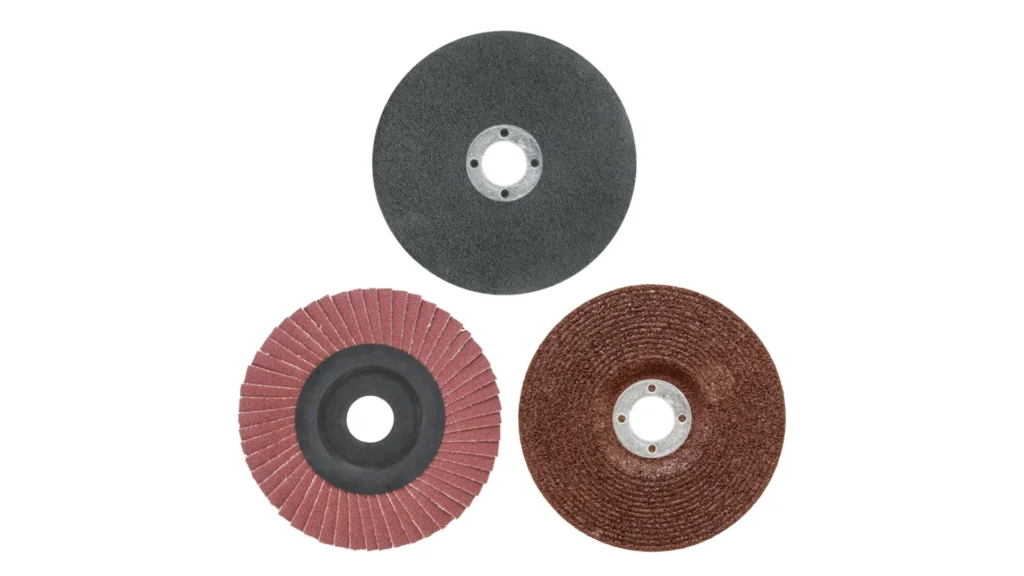
In summary, the mechanical strength and hardness of ceramics position them as indispensable materials in critical industrial applications, despite the inherent limitations of their brittleness.
Crystalline structure and brittlenes
The crystalline structure of ceramic materials plays a fundamental role in their mechanical properties, defining their behavior under various conditions. Ceramic materials are characterized by a microstructure based on ionic and covalent bonds. These bonds are extremely strong, explaining their high compressive strength and hardness, which contribute to the effectiveness of ceramic coatings, but also their limited ductility.
The brittle behavior of ceramics is largely due to the lack of slip between crystal planes. Unlike metals, where atoms can reorganize through dislocation movement, this process is virtually nonexistent in ceramics due to the rigidity of their chemical bonds. As a result, under tensile loads or impacts, ceramics tend to fracture rather than deform.
Moreover, defects in the crystalline structure, such as microscopic cracks or pores, significantly contribute to their brittleness. These defects act as stress concentration points that facilitate the propagation of fractures. This phenomenon, known as ceramic brittleness, is one of the main limitations of these materials in structural applications.
Despite these limitations, their high compressive strength and thermal stability make ceramics indispensable in specific industrial applications. Understanding the relationship between the crystalline structure and mechanical properties is key to designing ceramics with improved properties and expanding their use in new technological areas.
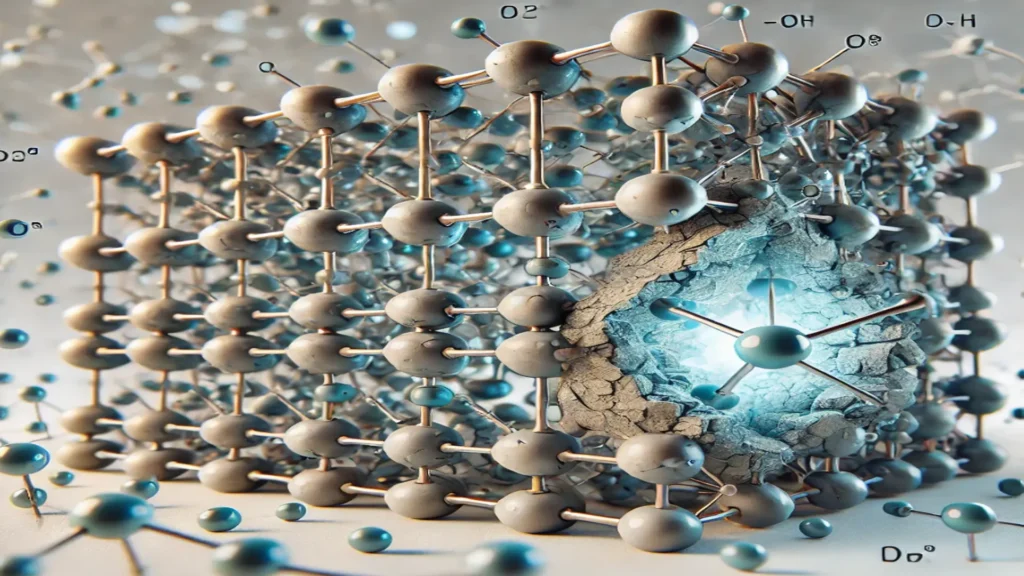
Measuring hardness in ceramics
The hardness of ceramics is a crucial property for determining their wear and abrasion resistance. To measure this characteristic, standardized methods are employed to evaluate the material’s resistance to penetration under controlled load.
The Vickers hardness test is one of the most common methods. It involves applying a load to the material using a diamond-shaped indenter. The resulting indentation is measured to calculate the hardness value. This method is widely used for its precision and versatility.
Additionally, the Knoop microhardness test is particularly relevant for ceramic materials, especially ceramic coatings, to evaluate their performance under stress. This test uses an elongated indenter to evaluate very small areas, such as ceramic coatings or small-sized components. It is ideal for characterizing ceramics with heterogeneous microstructures.
Hardness is not only an indicator of penetration resistance but also of abrasion resistance. Ceramics with high hardness, such as silicon carbide and cubic boron nitride, are used in cutting tools and industrial abrasives, where prolonged wear is a critical challenge.
In summary, measuring hardness in ceramics provides essential information for their selection in demanding industrial applications, where wear resistance and mechanical stability are priorities.
Industrial applications based on mechanical properties
Ceramic materials are indispensable in various industries due to their exceptional mechanical properties. These applications are based on their strength, hardness, and thermal stability, which surpass the capabilities of many other materials.
Applications based on strength
Thanks to their high mechanical strength, especially in compression, ceramics are used in coatings for industrial machinery and tools. For example, in the production of ceramic bearings, these materials provide exceptional wear resistance, even under high-load conditions. Refractory bricks, made from aluminum and magnesium oxides, are another example; their resistance to heat and compression makes them ideal for industrial furnaces and boilers.
Applications based on hardness
The hardness of ceramics makes them ideal materials for cutting tools, abrasives, and ceramic coatings, which enhance durability in industrial environments. For instance, tungsten carbide and silicon nitride are used in cutting tools in the metallurgical industry. These materials maintain their edge even during high-intensity processes. Similarly, ceramic abrasives, such as aluminum oxide, are used in precision grinding and polishing processes.
Impact of thermal stability and abrasion resistance
The abrasion resistance and thermal stability of ceramics make them ideal for components in high-temperature and chemically aggressive environments. Examples include ceramic coatings in gas turbines and engine components, which withstand extreme temperatures and exposure to corrosive agents without losing their mechanical properties.
In conclusion, the mechanical properties of ceramics, combined with their wear resistance and stability under extreme conditions, make them key materials in industrial sectors such as metallurgy, energy, and advanced manufacturing. These applications continue to expand with the development of new ceramic technologies.
Challenges and technological advances
Despite their exceptional mechanical properties, ceramic materials face significant limitations, with brittleness being one of the most critical. This characteristic restricts their use in applications requiring impact resistance or tensile strength. Additionally, microscopic defects in their crystalline structure contribute to their tendency to fracture under high stresses.
However, technological advances have overcome some of these challenges through the development of ceramic composites. By incorporating reinforcing phases, such as fibers or metallic particles, their mechanical strength is enhanced, and their brittleness is reduced. Notable examples include ceramics reinforced with carbon fibers and ceramic matrix composites used in the aerospace industry.
Emerging applications are appearing in high-tech industries such as electronics and biomedicine, where advanced ceramics are used in energy storage devices, medical implants, and semiconductor components, expanding their relevance in future technologies.
Want to dive deeper into how ceramics and composites are transforming modern engineering?
Watch this insightful video exploring the innovations, challenges, and applications of composite materials, including cutting-edge uses of ceramics in advanced technologies. Courtesy of: The Efficient Engineer.
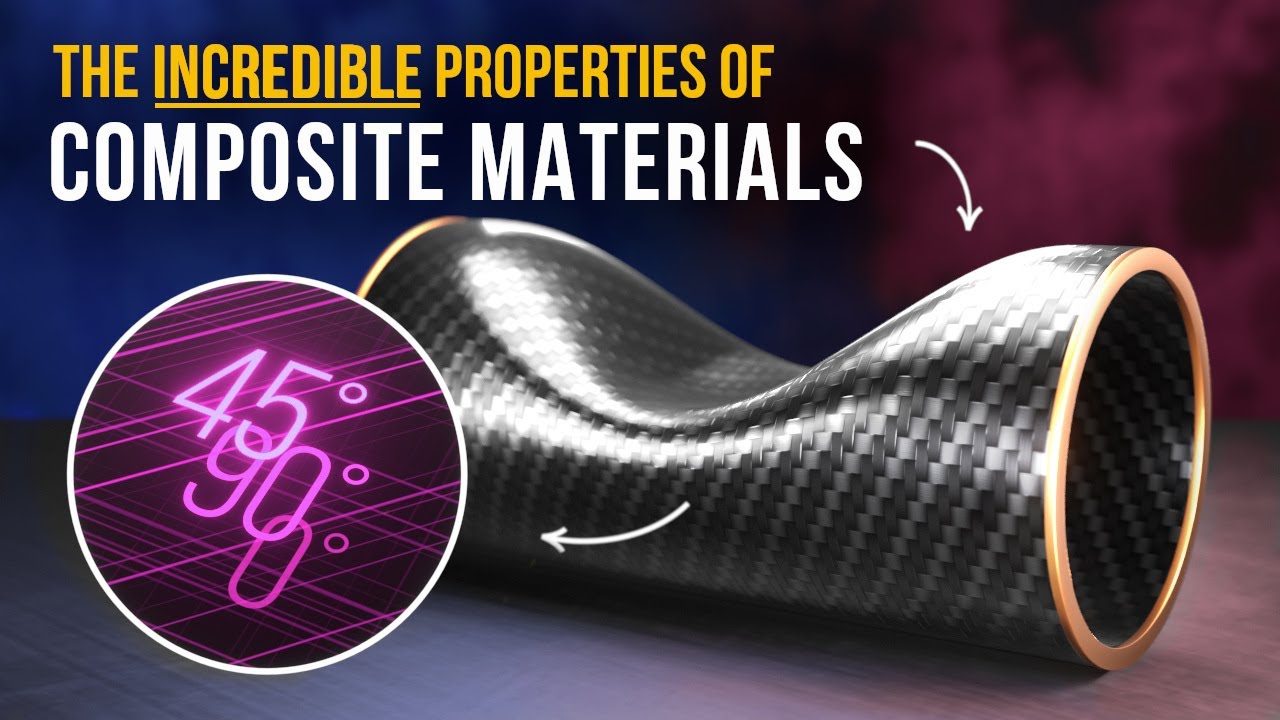
The incredible properties of composite materials.
Conclusions
Ceramic materials, due to their suitable properties such as high mechanical strength, remarkable hardness and thermal stability, are used in a wide variety of industrial applications. Despite their fragility, these mechanical properties position them as key materials in sectors that require high wear resistance, such as cutting tools and protective coatings.
Accurate evaluation of the hardness and mechanical strength of ceramic materials is essential for their optimization in high-demand environments. The application of standardized methods, such as Vickers and Knoop hardness tests, allows quantitative characterization of their mechanical properties, ensuring their reliability and performance under critical operating conditions.
The future of ceramics in industry is promising, thanks to advances in composite ceramics and the development of new technologies. These innovations are making it possible to expand their use in high-tech sectors such as aerospace, electronics and biomedicine, consolidating their role in industrial innovation.
References
Own souce