Table of Contents
A gas station, is far more than a simple fuel refueling point; they are complex systems where advanced technologies and rigorous safety protocols converge to provide efficient and safe service. Each time we fill a vehicle’s tank, we rarely consider the precision required to monitor the fuel level accurately, ensuring safe and controlled dispensing. Behind every fuel dispenser, every underground tank, and each safety measure, there is meticulous engineering aimed at optimizing both performance and safety.
This article delves into the technical operation of gas station, breaking down the mechanisms behind fuel dispensers, safety systems, and fault prevention and detection technologies. From the nozzle trigger that automatically stops the flow to advanced systems that monitor and prevent potential problems, we will explore how engineering and technology come together to enable a reliable and safe fueling service. Through this exploration, we will understand the importance of these systems in ensuring operational and environmental safety at gas station.
How does the gas pump know when to stop?
In a gas station, the fuel dispenser process is an act of technological precision. It begins with the dispensing nozzle, a component that not only delivers fuel but also detects when the vehicle’s tank is full. The nozzle features an integrated vacuum system that performs this task automatically. When the fuel reaches the maximum level in the tank, it blocks a small tube at the nozzle’s tip, creating a pressure change that triggers the automatic shutoff mechanism. This system ensures that there are no spills, making refueling safe and precise.
In addition to this automatic shutoff system, fuel dispenser accuracy relies on a device called a positive displacement meter. This meter contains a series of internal gears that rotate in relation to the volume of fuel passing through them, allowing for precise measurement of the fuel flow into the tank. Each rotation of the meter corresponds to a specific amount of fuel, ensuring that the customer receives exactly what they are paying for.
The nozzle structure is designed to withstand the harsh conditions of continuous use and exposure to highly corrosive fuels. Materials like anodized aluminum and stainless steel are commonly used, as they resist corrosion and wear. These materials not only extend the equipment’s lifespan but also prevent fuel contamination from unwanted particles.
The engineering behind fuel dispensers is carefully crafted to maximize safety and precision—two essential pillars in gas station operation. These mechanisms guarantee a controlled, risk-free operation for the user.
Want to see how this system works? We invite you to watch the following video. Courtesy of: Sabins Civil Engineering.
Safety systems in fuel dispensers
Safety in a gas station is fundamental, especially in environments where flammable and pressurized substances are handled. To prevent accidents and minimize risks, fuel dispensers are equipped with multiple safety systems that operate in an integrated and efficient manner.
A critical component in fuel dispenser safety is the quick-release check valve. These safety valves are designed to immediately shut off the fuel flow if the nozzle accidentally disconnects from the vehicle or if there is a problem in the supply line. This prevents fuel spills and, in critical situations, significantly reduces the risk of fires.
Static electricity control is another essential element in the dispenser’s design. Since friction and fuel flow can generate static charges, gas station have grounding systems that safely discharge this energy. This system reduces the risk of sparks that could ignite a fire in the presence of gasoline vapors.
Finally, fuel dispensers are equipped with an automatic shutoff and fire detection system. If a fire is detected near the fuel dispenser, these systems automatically stop the fuel flow to prevent the fire from spreading. Some systems even include automatic fire extinguishers that activate when an unusual temperature increase is detected, limiting flame propagation.
Together, these safety mechanisms enable gas station operate under safe conditions, minimizing the risk of accidents in a highly flammable environment. These advanced systems protect both users and operators from potential incidents, acting as a crucial barrier against adverse events.
Vapor recovery technology
The vapor recovery system in a gasoline station is a key technology for minimizing the release of volatile organic compounds (VOCs) into the environment and improving fuel efficiency. It also has components such as pressure sensors that are indispensable for monitoring the internal pressure in the return lines.
During vehicle refueling, vapors generated in the tank could escape into the air if not controlled, increasing atmospheric pollution and fuel waste. This system captures and redirects these vapors to the fuel dispenser’s storage tank, complying with environmental regulations and optimizing resources.
Main components and their functions
- Vapor recovery nozzle: This device initiates the vapor recovery process. Unlike standard nozzles, the recovery nozzle has a nrubber seal ring that fits around the vehicle’s tank opening, creating an airtight seal that prevents vapor leakage. It includes a secondary path for vapor aspiration while the tank is being filled with fuel.
- Vacuum pump: The vacuum pump provides the suction needed to transport vapors from the vehicle’s tank to the underground storage tanks. When the user activates the fuel nozzle, the vacuum pump also engages, creating a controlled vapor flow through the return line.
- Vapor return pipe: This pipe connects the recovery nozzle to the underground tank and is constructed with corrosion-resistant materials to ensure safe and leak-proof vapor transport.
- Storage tank with pressure compensation chamber: Once in the storage tank, vapors enter a chamber that adjusts the internal pressure, allowing partial condensation of the vapors back into liquid fuel.
- Pressure relief valve: If overpressure occurs, the relief valve activates, safely releasing the excess pressure to protect the system.
- Controller and pressure sensors: Advanced sensors monitor pressure and report to the system controller. If unusual variations are detected, the system issues alerts, ensuring safety and optimal operation.
Environmental impact and operational safety
By capturing and preventing vapor release, this system reduces environmental impact and worker risks. This technology demonstrates the industry’s commitment to sustainability and safety, achieving efficient, environmentally responsible operations.
Structure and maintenance of underground tanks
An underground tank is an essential component in a gas station, designed to store fuel safely and environmentally securely. Constructing and maintaining these tanks requires advanced engineering and specific materials to prevent corrosion and potential leaks.
Most underground tanks are made from corrosion-resistant alloys and are coated with special protective layers that minimize direct contact between the fuel, tank walls, and surrounding soil. This coating not only prevents tank degradation but also minimizes the risk of soil contamination.
A leak monitoring system is essential for ensuring the integrity of underground tanks. This system includes advanced sensors that detect variations in fuel volume or pressure within the tank, identifying any anomaly that could indicate a leak. Fuel level sensors in an underground tank provide real-time monitoring, helping maintain optimal inventory and preventing potential leaks or overfilling. These sensors, strategically placed at critical points, allow for early and precise detection, protecting both personnel safety and the environment. Fuel leaks pose a significant risk as they can contaminate groundwater and soil, and monitoring technology is a key barrier to preventing these issues.
Regular maintenance of an underground tank is another pillar of safe operation. Protocols include visual inspections, tightness tests, and Non-Destructive Testing (NDT) methods that allow tank condition verification without direct intervention. Regulations also establish preventive maintenance schedules to ensure all system components meet safety standards.
The long-term integrity of underground tanks depends not only on their initial construction and protective coatings but also on proactive maintenance and the use of technology, such as fuel level sensors, to monitor conditions continuously. This combination of advanced materials, maintenance, and monitoring ensures that underground tanks remain durable, safe, and environmentally secure over time.
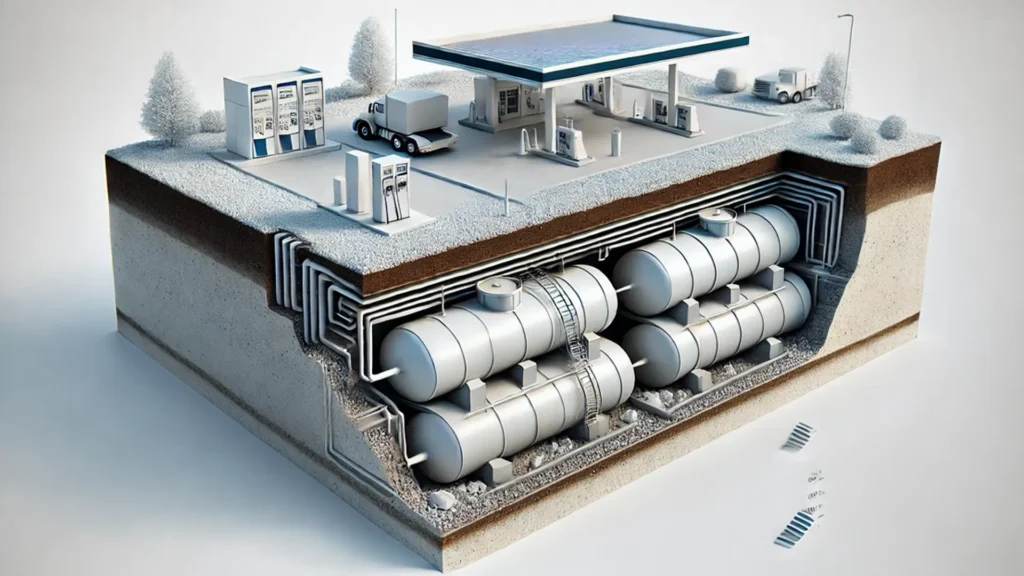
Preventive management in gas stations
A gas station is exposed to various damage mechanisms that can affect system integrity and safe operation. Among the main problems is corrosion, which occurs due to the exposure of metal components to aggressive agents like water, oxygen, and chemicals present in the soil and fuel itself. Corrosion is particularly harmful to tanks, pipes, and fuel dispensers, where it can lead to leaks and contamination.
Another wear factor is mechanical fatigue, especially in components subjected to continuous movement or pressure, like pumps and valves, which may develop microcracks over time.
Preventing these damages starts with the use of high-resistance materials and specialized coatings that minimize deterioration. For example, underground tanks are made of steel coated with fiberglass or special resins to prevent corrosion. Dispensers also include durable materials and reinforced components that withstand constant friction and pressure.
Regular inspections are essential for identifying problems in their early stages. Non-destructive testing (NDT) methods, such as ultrasound and visual inspection, are common in preventive maintenance, as they allow internal condition assessment of tanks and other systems without disrupting operations. These tests, combined with predictive maintenance based on monitoring data, help detect and repair issues before they escalate into critical failures.
Additionally, it is crucial to implement measures to prevent sediment accumulation in filters and tanks. Particles and sediments can clog pipes and reduce system efficiency, so regular cleaning of filters and pipes is a key maintenance practice. Together, these proactive strategies ensure that gas station systems remain operational, safe, and in optimal condition, minimizing risks and extending their useful life.
Station control and monitoring software
In a modern gas station, control and monitoring software is essential for managing daily operations, preventing failures, and ensuring constant oversight. This software, connected to a series of strategically placed sensors, enables real-time monitoring of operating conditions and generates alerts that anticipate issues before they become major failures.
A key component of the monitoring system is fuel level sensors in the underground storage tanks. These sensors record not only the fuel level but also the temperature, helping operators maintain optimal inventory levels and identify potential issues like leaks or overfilling. Sudden fluctuations in the fuel level can indicate problems such as leaks or temperature shifts, allowing for immediate intervention to prevent environmental or operational hazards.
Accurate fuel level data also supports inventory management, ensuring that supplies are consistently available without risk of shortage or excess.In the vapor recovery system, pressure sensors are concealed along the return pipe, especially at critical connection points. These sensors monitor system pressure, detecting variations that may indicate obstructions or leaks. Their role is to maintain the safe and stable flow of vapors back to storage tanks, minimizing overpressure risks and protecting the recovery system’s integrity.
Wear and vibration sensors in pumps and dispensers are integrated into the mechanical components of this equipment. By recording vibration and wear patterns, these sensors detect early signs of fatigue or mechanical failure, allowing the software to issue alerts before equipment failure. This facilitates preventive intervention and reduces downtime in case of technical issues.
For environmental safety, gas sensors in areas at risk of gas leaks, like dispensers and underground tanks, detect any leaks. When activated in the presence of vapors, these sensors automatically trigger an alarm, alerting personnel and activating emergency protocols.
Finally, vacuum pump and vapor suction system sensors control vapor flow and pressure during suction, detecting obstructions or damage in the system, ensuring continuous vapor recovery
The software integrates this data and activates predictive maintenance based on historical and real-time data. Its integration with the point of sale (POS) system allows inventory management and quick response alerts in case of issues, creating a digital monitoring system that complements physical maintenance. Thus, the monitoring software always maintains station safety and efficiency.
Innovation and the future of gas station
The future of gas station is evolving toward a more diversified and sustainable service model, adapting to emerging energy and technology trends. One of the most notable innovations is the integration of hybrid stations, where traditional service station now include infrastructure for charging electric vehicles. This adaptation responds to the increase in electric vehicle use, allowing stations to remain relevant refueling points in the transport sector.
Moreover, there is a growing focus on using alternative and sustainable fuels. Biofuels, hydrogen, and synthetic fuels are gaining traction as cleaner options compared to traditional gasoline. This allows stations to diversify their energy offerings and align with greenhouse gas emission reduction goals. Station infrastructure is evolving to accommodate these new fuels, adapting tanks and safety systems to handle various types of products.
Automation and remote monitoring represent another significant trend. With advances in the Internet of Things (IoT) and artificial intelligence, future stations will be remotely monitored and controlled, reducing the need for direct human intervention and improving operational efficiency. This technology will enable remote problem detection, maintenance optimization, and quick incident response.
These trends demonstrate how the industry is adapting to environmental and sustainability demands, ensuring gas station evolve toward a more diversified and responsible energy model.
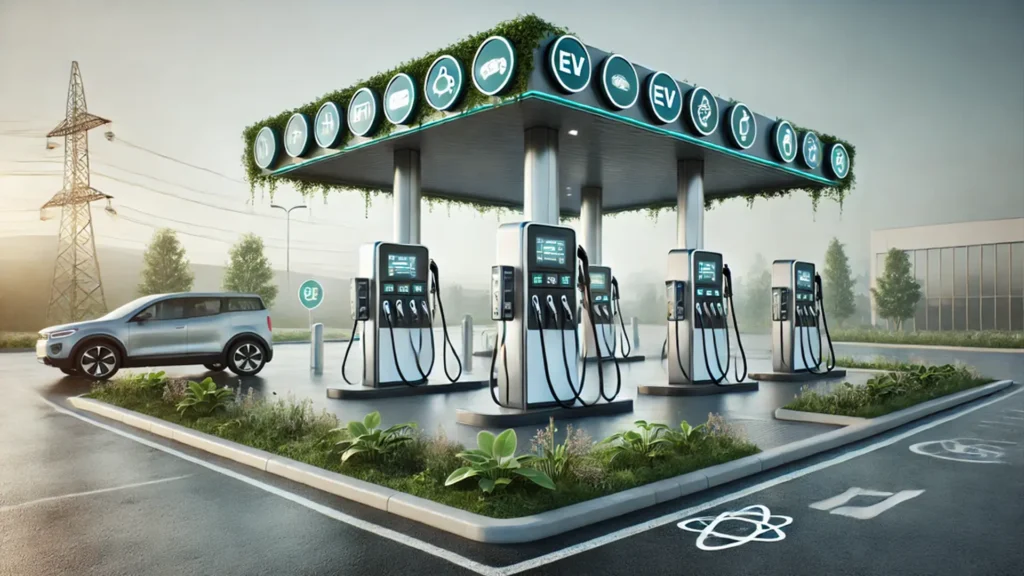
Conclusions
Modern gas station are complex and highly technical systems, designed to offer safe and efficient service. Throughout this article, we explored the key systems that make the daily operation of these facilities possible, from fuel dispensing mechanisms and safety systems to vapor recovery technology, underground tank structures, and digital monitoring software.
Each of these systems plays a fundamental role in gas station operations, contributing to both user safety and operational efficiency. Implementing advanced technology and proactive maintenance practices helps prevent accidents, reduce environmental impact, and optimize resource use. Additionally, innovations in alternative fuels and automation are positioning gas station to address the challenges of a more sustainable energy future.
Although often unnoticed, these systems and technologies represent the technical backbone of gas station. Their precise and safe operation is essential for energy supply and environmental protection, demon
References
Own source