Table of Contents
Introduction
One of the most effective techniques to detect and analyze flaws is Lock-in Thermography (LIT). This non-destructive testing (NDT) technique is applied to find sub-surface defects that are often not detected by other diagnostic methods.
The detection and evaluation of faults in various components is a fundamental aspect of ensuring the reliability and safety of electrical and electronic systems. As these systems become more complex, the use of advanced diagnostic tools is necessary. In this article, the principles of Lock-in Thermography, its applications and its advantages in the evaluation of faults in various applications are presented.
What is Lock-in Thermography (LIT)?
Lock-in Thermography (LIT) is an active infrared imaging technique used to detect thermal anomalies in materials and components generated by internal faults. The term “lock-in” refers to the synchronization of a periodic external excitation (such as an electric current, laser or mechanical stress) with the infrared camera that captures the thermal response of the object under test. By analyzing the phase lag and amplitude of the generated thermal waves, The thermography can identify defects such as cracks, delaminations, voids, and other sub-surface anomalies.
How does lock-in thermography work?
The principle of operation of Lock-in Thermography involves several key steps:
- Excitation: The object under test is subjected to an external periodic energy source. This excitation may be in the form of eddy current, laser, ultrasound, microwave, xenon lamp, halogen lamp or other form of energy depending on the material and type of defect being sought.
- Thermal wave generation: Excitation causes localized heating within the material, leading to the generation of waves. These waves propagate through the thermal material changing phase as they are absorbed, and interact with any internal defects by partially reflecting. This reflected portion interacting with the incoming wave creates an interference pattern on the surface of the component, which oscillates at the same frequency as the thermal wave1.
- Infrared imaging: An infrared camera captures the surface temperature distribution over time. The camera is synchronized with the excitation source, allowing it to “lock” onto the generated thermal waves.
- Data analysis: The captured infrared data is processed to extract phase and amplitude information. The internal structure of the object under examination can be obtained by evaluating the phase shift of local surface temperatures relative to the input energy wave2. Defects are generally identified by anomalies in the phase shift and amplitude of the thermal waves. These anomalies indicate variations in thermal conductivity or heat capacity caused by the defects.
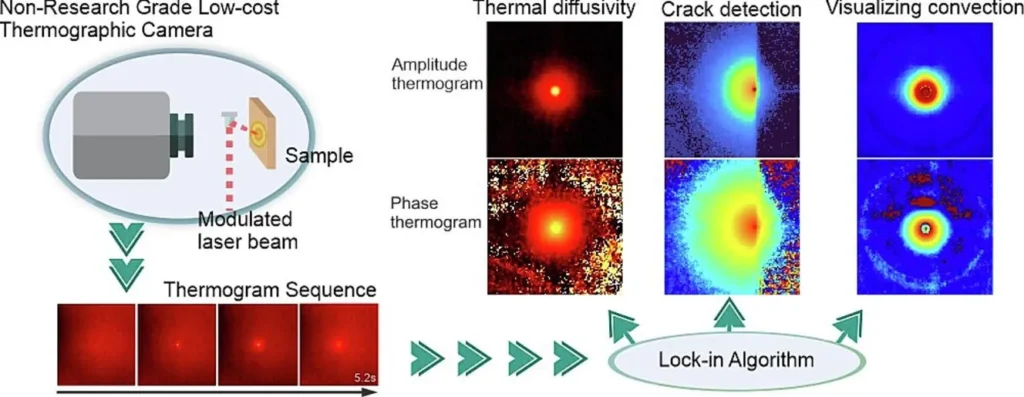
Lock-in thermography applications (H2) in the evaluation of common thermal failures
Lock-in Thermography has a wide range of applications in various industries. Below are some key areas where it is used for the evaluation of common thermal faults:
- Electronic testing: In the electronics industry, Lock-in Thermography (LIT) is used to detect faults in printed circuit boards (PCBs), integrated circuits (ICs) and other electronic components. Thermal failure analysis in electronics can lead to overheating, reduced efficiency and eventual device failure. Lock-in thermography is particularly effective in detecting defects in solder joints, delaminations and voids that can compromise the performance of electronic components.
- Aerospace and defense: The aerospace and defense industries require the highest levels of reliability and safety. Lock-in thermography is used to inspect critical components such as turbine blades, composite structures and adhesive bonds. The ability of lock-in thermography to detect sub-surface defects without disassembly makes it an invaluable tool for maintaining the integrity of aerospace components.
- Automotive industry: In the automotive industry, Block Thermography is used to detect and evaluate failures in various components, including batteries, motors, and electronic control units (ECUs). For example, in electric vehicles (EVs), battery thermal management is crucial for safety and performance. Lock-in thermography can detect manufacturing defects in battery cells and modules, ensuring that only high-quality components are used.
- Power generation: Power generation systems, especially those involving turbines and generators, are susceptible to thermal failures due to high operating temperatures. Block Thermography is used to inspect components such as rotors, stators, and insulation systems for thermal anomalies. Early detection of such failures can prevent costly downtime and extend the life of power generation equipment.
- Materials science and research: In materials science, Block Thermography is used to study the thermal properties of materials, including their conductivity, diffusivity and specific heat. Researchers use block thermography to evaluate the quality of composites, ceramics, and other advanced materials. By identifying defects such as cracks and voids, block thermographic contributes to the development of stronger, more reliable materials.
For more information, we invite you to watch the following video. Source : Movitermo, Advanced Thermography Solutions
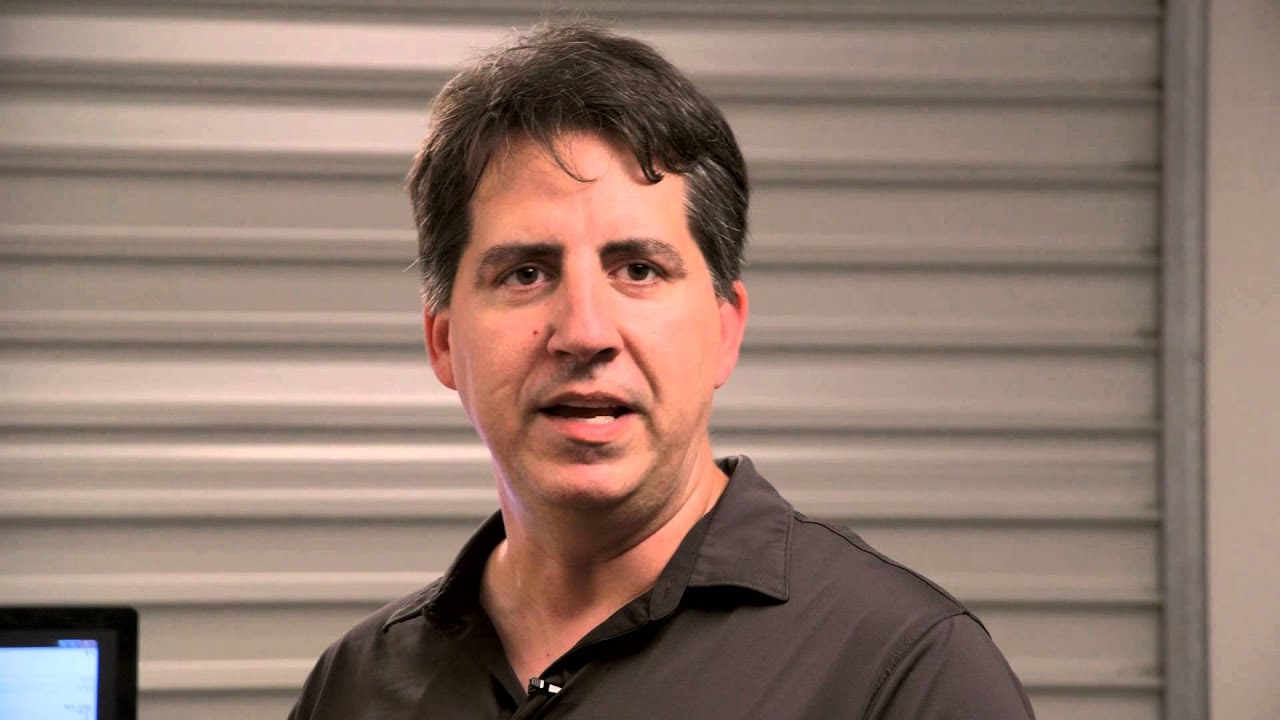
Thermography NDT solution.
Thermal Failure Analysis by IR Lock-in Thermography
This non-destructive technique represents a key tool for the thermal failure analysis. It allows the detection of local heat sources on the surface of a material, with a higher sensitivity than other thermal imaging techniques. Thanks to its nature, it minimizes lateral heat diffusion, improving detection accuracy. With improved spatial resolution, it is ideal for locating leakage currents and subsurface heat sources in integrated circuits (ICs) and electronic components.
Some of the most common thermal failure analysis that can be detected with this technique are:
- Leakage currents: The LIT is extremely sensitive to detect leakage currents that generate small heat sources in integrated circuits (ICs) or electronic components.
- Hot spots: Hot spots are areas where excessive heat builds up, which can indicate electrical overloads, component failures or manufacturing defects.
- Connection defects: Poor connections, such as cold or damaged solder joints, create resistances that generate heat, easily detected by LIT.
- Semiconductor failures: Faulty semiconductors generate heat due to failures in PN junctions, doped layers or transistors, which can be identified by LIT.
- Internal short circuits: Short circuits inside printed circuit boards or components generate localized heat, accurately identifiable by LIT.
- Internal delamination or separations: In multilayer or composite materials, internal defects, such as delamination, cause heat build-up due to alterations in heat transfer.
- Sub-surface defects: Allows detection of heat sources below the surface, useful to identify problems in encapsulations or protective layers.
Advantages of Lock-in Thermography
Lock-in thermography offers several advantages over other methods of detecting and analyzing component failures. These advantages make it a preferred choice for many industries:
- Nondestructive testing: One of the main benefits of Lock-in Thermography is that it is a nondestructive testing method. Unlike other techniques that may require cutting or disassembling the object under test, blocking thermography can detect defects without damaging the material. This non-invasive approach preserves the integrity of the component, allowing for continued use after testing.
- Detection of sub-surface defects: Lock-in thermography is particularly effective in detecting sub-surface defects. Traditional infrared thermography techniques can capture only surface temperature variations, missing internal anomalies. By analyzing the phase shift and amplitude of the thermal waves, Block Thermography can reveal defects located deep within the material.
- High sensitivity and resolution: Block Thermography is known for its high sensitivity and resolution. It can detect minute temperature variations caused by small defects, providing detailed information on the size, location, and nature of the anomaly. This level of accuracy is essential to ensure the reliability of critical components.
- Wide range of applications: As mentioned above, Block Thermography has a wide range of applications in different industries. Its versatility makes it a valuable tool for fault detection and evaluation in electronics, aerospace, automotive, power generation and materials science. Whether detecting faults in electronic circuits or inspecting turbine blades, lock-in thermography delivers consistent and reliable results.
- Cost-effectiveness: Although the technology is highly advanced and consequently expensive, Lock-in Thermography is cost-effective. The ability to detect defects early in the manufacturing process or during routine maintenance can prevent costly failures and downtime. By ensuring that only defect-free components are used, lock-in thermography reduces the need for costly repairs and replacements.
Challenges and considerations
Despite its many advantages, there are some challenges and considerations associated with blocking thermography:
Equipment Costs: The initial investment in blocking thermography equipment, including infrared cameras and excitation sources, can be high. However, this cost is often offset by the long-term savings achieved through increased reliability and reduced downtime.
Expertise required: Interpretation of lock-in thermography data requires specialized knowledge and experience. The complexity of phase and amplitude analysis means that skilled operators are needed to obtain accurate results.
Material limitations: The effectiveness of Lock-in Thermography can vary depending on the material being tested. For example, materials with low thermal conductivity may require longer excitation times or higher energy inputs to generate detectable thermal waves.
Conclusion
Lock-in Thermography is a powerful tool for thermal flaw assessment, offering nondestructive evaluation with high sensitivity and resolution. Its ability to detect sub-surface defects in a wide range of applications makes it an invaluable resource in industries where reliability and safety are paramount. As technology continues to advance, this technique will likely play an even more significant role in ensuring the integrity and performance of critical components in various fields.
References
- MOVITHERM. Lock-In Thermography NDT Technique; Consultado en fecha 30 de Agosto de 2024. https://movitherm.com/blog/what-is-lock-in-thermography/#:~:text=The%20reflected%20portion%20of%20the%20wave%20interferes%20with%20the%20incoming%20input%20wave%20at%20the%20surface%20of%20the%20object%2C%20causing%20an%20interference%20pattern%20in%20the%20local%20surface%20temperature%2C%20which%20oscillates%20at%20the%20same%20frequency%20as%20the%20thermal%20wave
- A. Bedoya, F. Rodríguez-Valdés, E. Marín; “Laser-spot lock-in thermography with a non-research-grade thermal camera: From thermal diffusivity measurements to visualizing free convection”; Infrared Physics & Technology; Volume 137, March 2024, 105161.