Table of Contents
- Introduction
- What is FMEA?
- Benefits of FMEA
- How to choose the right type of FMEA for your project
- How to implement FMEA in engineering projects
- Phase 1: Determining the objective and scope of the FMEA
- Phase 2: Formation of a multidisciplinary team
- Phase 3: Identification of failure modes
- Phase 4: Determination of effects and causes of failures
- Phase 5: Evaluation of severity, occurrence, and detection of failures
- Phase 6: Prioritization of failures
- Phase 7: Implementation of corrective and preventive actions
- Phase 8: Follow-up and review
- Conclusions
- References
Introduction
Failure Mode and Effect Analysis (FMEA), created in the 1940s by the United States Army, is an engineering technique used to detect failures in products and processes at an early stage of development. Its implementation in multiple sectors facilitates decision-making and mitigates damages, thus ensuring the competitiveness and sustainability of organizations in the face of the high quality and reliability standards demanded by today’s consumers.
The constant search to be more competitive in the market has led to the development of Failure Mode and Effects Analysis (FMEA), which has become a vital tool in several industrial sectors. This method, developed in the 1940s, is used in engineering to identify and analyze potential failures in products and processes during the early stages of development, being the most important ones.
In the following, we will investigate the most relevant aspects for the implementation of the FMEA. This methodology allows companies to make informed decisions to mitigate risks and damages, thus improving the quality and reliability of their processes and services.
What is FMEA?
Failure Mode and Effects Analysis (FMEA) is an analysis tool that identifies, evaluates, and mitigates any possibility of problems and failures in products, processes, or systems. Its objective is to detect failures in a process or product before they reach the customer1. Additionally, it is a methodology that offers the opportunity to identify the consequences resulting from irregularities in equipment, products, and the safety of work environments. The FMEA allows to anticipate risks and prevent the negative effects of any failure, ensuring the quality and reliability of products and processes.
Benefits of FMEA
- Improved quality: By identifying and addressing failures early on, FMEA improves the quality of products and services, reduces the likelihood of costly failures, and lowers the costs associated with repairs, returns, and warranties.
- Increased brand reputation: Offering highly reliable products and services increases customer satisfaction, which strengthens the company’s reputation in the marketplace.
- Performance optimization and operational efficiency: Focusing on critical issues enables effective resource allocation and continuous improvement in operational efficiency through preventive rather than corrective actions.
- Regulatory compliance and increased safety: The FMEA helps to comply with established requirements and quality standards, ensuring the reliability and safety of products and processes, which are essential for the safe and compliant operation of the company.
How to choose the right type of FMEA for your project
The proper selection among the different types of Failure Mode and Effects Analysis (FMEA) is necessary to ensure quality and reliability in any project or industrial sector. The following is a detailed overview of each type of FMEA, providing clear criteria for choosing the most suitable one according to the characteristics of the project and the sector in question.
Design FMEA
Focuses on anticipating potential problems and failures during the product conception and design phase. This analysis makes it possible to foresee and mitigate any malfunction from the early stages of development. It is a preventive tool that helps identify and address potential failure points before they become costly and complex problems.
When to implement: The implementation of this FMEA methodology is crucial both in the development of new products or services and in the redesign phase of existing products or services2. In the case of a new process, it helps in the identification and mitigation of failures from the early stages of development to ensure the quality and reliability of the final product. While, for product or service redesigns, the design FMEA allows analyzing the possible risks that the proposed changes may represent, in order to have solutions that improve or maintain the quality standards of the product or service.
Sectoral application: In the automotive industry, design FMEA is used for the development of critical components such as braking and safety systems. In consumer electronics, it is applied in the design of new devices to ensure that they meet quality and performance standards. In aerospace, it is essential for the design of control and safety systems, where reliability is of paramount importance.
Process FMEA
It is used for the identification and prevention of problems in production processes. This method focuses on the quality of the final product and worker safety. Detailed analysis of each phase of the production process allows the identification of critical points where failures may arise and the development of strategies to mitigate them.
When to implement: It is essential to perform it before developing control plans for new or modified processes, this in order to recognize and solve failures, to prevent their occurrence2. This FMEA can be used for other purposes, for example, during the planning of process strategies, as a way to evaluate risks and the effectiveness of the strategies in advance. Additionally, it is used to examine failures in current processes, thus enabling continuous improvements and the reduction of potential risks.
Industry application: In manufacturing, process FMEA is fundamental to process optimization for production lines, ensuring that each stage is free of defects and risks. In the consumables industry, it is used to control quality in packaging processes, ensuring that products meet safety and quality standards. In the pharmaceutical industry, it is ideal for validating drug manufacturing processes, ensuring the purity and efficacy of products.
System FMEA
It is specifically applied to software and technological systems, allowing the detection and prevention of failures related to the user interface and system maintenance. This type of FMEA analyzes potential software failures from a technical and functional perspective, helping to develop strategies to mitigate them before they affect the end user.
When to implement: Its use is essential in software management and user interface maintenance2. During these processes, potential system failures are identified at an early stage. In this way, effective planning and then appropriate risk mitigation can take place. This methodology is also used in user interface maintenance, detecting potential failures early, and implementing solutions.
Sectoral application: In the information technology sector, system FMEA is used in the development of applications and operating systems to ensure that they are reliable. In banking and finance, it is applied to the maintenance of secure transaction systems, protecting customer data and operations. In telecommunications, it is crucial for the management of networks and communication systems, ensuring availability and quality of service.
How to implement FMEA in engineering projects
Phase 1: Determining the objective and scope of the FMEA
The first step in implementing the FMEA is to clearly define the objective and scope of the analysis. This involves identifying the process, service or software system to be evaluated. It is essential to have complete information about the software’s performance, system requirements, user expectations, and any previous history of failures. This phase lays the foundation for the entire analysis, ensuring that all relevant aspects of the software are taken into account.
Phase 2: Formation of a multidisciplinary team
The creation of a multidisciplinary team is essential for a proper analysis. This team should include experts in the FMEA method, software developers, system engineers, and end users. The diversity of knowledge and perspectives in the team facilitates the identification of potential failures from multiple angles and ensures that all facets of the software system are addressed.
Phase 3: Identification of failure modes
In this phase, potential failure modes of the software system must be identified. This is accomplished through a thorough review of technical documentation and historical failure records. The team should focus on identifying all possible ways in which the software could fail, from bugs in the code to failures in user interaction.
Phase 4: Determination of effects and causes of failures
Once the failure modes have been identified, the next step is to determine the effects and causes of each failure. The team must analyze how each potential failure could affect the system and users, as well as identify the underlying causes. This phase may involve the use of cause analysis tools, such as the 5 Whys, to ensure a complete understanding of the contributing factors.
Phase 5: Evaluation of severity, occurrence, and detection of failures
Each failure mode identified should be evaluated in terms of severity, occurrence, and detection. Severity measures the impact of the failure, occurrence assesses the probability of occurrence, and detection measures the ability to identify the failure before it causes significant problems. These assessments are typically performed on a scale of 1 to 10, and the assigned values are used to calculate the Risk Priority Number (RPN).
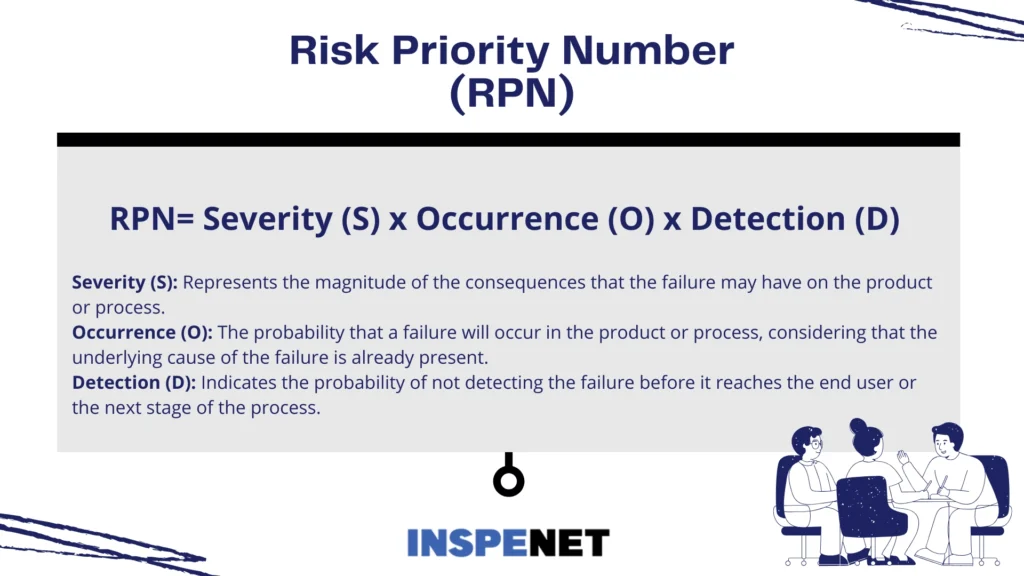
Phase 6: Prioritization of failures
With the RPN calculated for each failure mode, the failures are prioritized. Failures are classified into high, medium, and low-risk categories, allowing the team to focus on the most critical problems first. This prioritization ensures that resources are efficiently allocated to mitigate the most significant risks.
Phase 7: Implementation of corrective and preventive actions
For each priority failure, corrective and preventive actions should be developed and implemented. These actions are designed to eliminate or significantly reduce the risk associated with each failure. It is crucial to assign responsibilities, establish execution dates, and define the resources needed to carry out these measures.
Phase 8: Follow-up and review
Finally, the measures implemented must be continuously monitored to evaluate their effectiveness. This involves recalculating the RPN after the implementation of corrective and preventive actions to verify whether the risks have decreased. Regular monitoring ensures that the software system maintains its reliability and quality over time, allowing for additional adjustments if necessary.
Conclusions
The implementation of Failure Mode and Effects Analysis (FMEA) in engineering is fundamental to ensure the quality and reliability of products and processes. This method, which allows the early identification of potential failures, provides a solid basis for decision-making, mitigating risks, and improving operational efficiency. By using it, organizations can anticipate and prevent problems before they affect consumers, resulting in a significant reduction in costs associated with failures and an increase in customer satisfaction.
Additionally, it contributes to regulatory compliance and improves the safety of products and processes, an extremely important aspect in order to remain competitive in an increasingly demanding market. Therefore, the FMEA methodology works as a means to optimize quality and reliability, as well as to strengthen the reputation and sustainability of companies in different industrial sectors.
References
- Blog QHSE. (2023, January 19). AMEF: evaluación de riesgos y calidad en una sola herramienta. Retrieved August 2, 2024 from https://www.blog-qhse.com/es/amef-evaluacion-de-riesgos-y-calidad-en-una-sola-herramienta.
- Pursell, S. (2023, August 2). Cómo hacer un AMEF, tipos, definición y pasos a seguir. Retrieved August 2, 2024 from https://blog.hubspot.es/marketing/amef.