Table of Contents
- What is RBI and how can it be improved?
- How to improve the effectiveness of IBR programs
- RBI methodology for storage tanks
- Integration of the risk matrix
- Strategic planning of the RBI program
- RBI Evergreen: Keeping the risk model alive
- How to Apply RBI to Storage Tanks
- Robotics in risk-based storage tank inspection
- Conclusion
- References
Traditional storage tank inspection plans are often based on fixed intervals dictated by standards such as API Standard 653, which do not reflect actual operating conditions or the evolving risk profiles of these assets. This time-based approach can result in unnecessary inspections or missed opportunities to prevent failures. In contrast, Risk Based Inspection (RBI) offers a smarter, more strategic approach by prioritizing inspections according to the probability and consequence of failure specific to the asset and its operational context.
The RBI methodology, based on the internationally recognized standard API RP 580 (Risk-Based Inspection) and complemented by API RP 581 (Risk-Based Inspection Technology), is considered a best practice for asset integrity management. This article examines its application in storage tanks, explores methods to evaluate and optimize its effectiveness, describes the strategic planning required, and presents a step-by-step guide to its implementation. It also discusses the RBI Evergreen concept and the impact of robotic technology on the process.
What is RBI and how can it be improved?
It is defined as a structured methodology of the API 580 standard that provides the guidelines required to design, implement and maintain a reliable risk-based inspection and maintenance program. Its function is to optimize resource allocation, improve safety and maximize the operational integrity of assets through a joint Probability of Failure (PoF) and Consequence of Failure (CoF) analysis.
Supplemented by API 581, which details the quantitative aspects of the assessment, the RBI allows the calculation of PoF by considering factors such as degradation mechanisms, inspection history, and operating conditions. CoF focuses on potential impacts on safety, the environment, and the economy.
The main objective is to concentrate finite inspection and maintenance resources on critical assets; in order to achieve tangible benefits such as:
- Increased operational safety and reliability: By proactively identifying and mitigating the most significant risks.
- Cost optimization: By reducing unnecessary inspections on low-risk equipment and avoiding unplanned shutdowns.
- Optimized inspection intervals: Possibility to extend intervals safely, based on data and risk analysis, without compromising integrity.
- Standards alignment: Compliance with API 580 / API 581 guidelines.
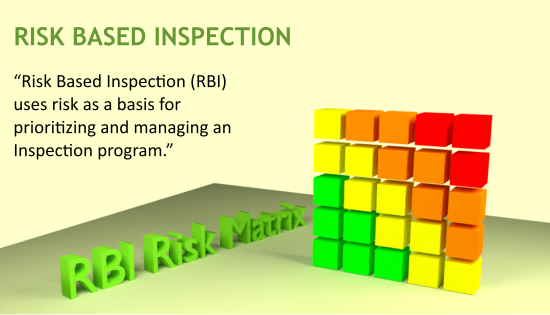
How to improve the effectiveness of IBR programs
Once the fundamental principles of effectiveness are understood, it is key to analyze how this methodology is specifically adapted to RBI in storage tanks, whose operational challenges require a differentiated treatment.
The effectiveness of an RBI program is not measured just by performing inspections, but by the program’s ability to correctly identify risks and guide mitigation actions that efficiently reduce those risks. An inspection is effective if it uses the right technique, at the right place, and at the right time to detect active damage mechanisms before they lead to failure.
To achieve greater effectiveness of the process, it is necessary to consider the following aspects:
- Understanding PoF and CoF: Correctly identify probability drivers (corrosion, fatigue, operating conditions) and consequences (product type, volume, location, environmental/safety impact).
- Proper selection of inspection techniques (intrusive vs. non-intrusive): Choose Non-Destructive Testing (NDT) methods that are capable of detecting and quantifying the expected damage mechanisms. For example, Conventional Ultrasound (UT), Phased Array (PAUT), Magnetic Flux Leakage (MFL), Pulsed Currents (PEC), etc. The choice between intrusive (requires taking the tank out of service) and non-intrusive (performed in operation, often with robotics) inspections is necessary for RBI optimization.
- Linking damage mechanisms to inspection methods: Ensure that the selected technique has a high probability of detection (PoD) for the specific damage being sought (e.g., MFL for bottom corrosion, PAUT for welds).
- Data quality and validation: Accuracy of input data (thicknesses, corrosion rates, history) is critical. Validate inspection results and use them to recalibrate RBI models.
- Continuous updating: Implement a model that is regularly updated with new data to maintain the accuracy of the operational risk profile.
One metric used to assess whether the RBI is effective is Overall Inspection Effectiveness (OIE), which weighs the quality of inspection planning, execution and analysis of inspection results in direct relation to quantified risk mitigation. A high OIE is achieved when resources are focused on high-risk areas and appropriate mitigation strategies are applied.
RBI methodology for storage tanks
The application of RBI to storage tanks requires detailed consideration of their unique characteristics and specific degradation mechanisms, going beyond traditional fixed interval based approaches such as those set out in API 653. The assessment should be broken down by major components, considering damage mechanisms, probability and consequence of failure factors, and appropriate inspection techniques.
Bottom and annular ring
- Damage mechanisms: Soil side corrosion (contact with the base/wet soil), product side corrosion (microbiologically influenced corrosion, localized coating failures), atmospheric corrosion at the bottom edge, pitting, differential settlement.
- PoF factors: Age of tank, type and condition of internal coating and cathodic protection system (if applicable), product type (presence of free/emulsified water), base design and condition, documented history of leaks, previous MFL/UT results.
- CoF factors: Tank volume, product type (toxicity, flammability), proximity to aquifers, populated areas, containment dikes.
- Common NDT techniques: Visual inspection, UT for spot thickness measurement, MFL (Magnetic Flux Leakage) scanning and Guided Wave Phased Array (GWPA) for general corrosion detection; Pulsed Eddy Current (PEC) for annular plate inspection from the outside. Currently, there are robotic equipment that inspect the bottom without emptying the tank.
Helmet
- Damage mechanisms: External corrosion (atmospheric, Corrosion Under Insulation – CUI in insulated tanks), internal corrosion (variable liquid level, corrosive product), general thinning, cracking).
- PoF factors: Age, effectiveness of paint/insulation system, environmental conditions (humidity, salinity), operating temperature, product corrosivity.
- CoF factors: Risk of vapor emission, structural collapse (rare but severe), evaporative product loss in floating roofs.
- Common NDT techniques: UT, VT, Thermography (for CUI), PEC.
Roof (Fixed or floating)
- Damage mechanisms: Internal corrosion (vapor phase), atmospheric corrosion, CUI (insulated roofs), structural damage (water accumulation, wind).
- PoF Factors: Roof design, coating effectiveness, drainage, environmental conditions.
- CoF factors: Risk of vapor emission, structural collapse (rare but severe), evaporative product loss on floating roofs.
- Common NDT techniques: VT, UT, drones for external visual inspection.
Integration of the risk matrix
For a comprehensive risk assessment, a specific risk matrix for storage tanks is used. This matrix cross-references the probability of failure and the consequence of failure identified for each combination of component and damage mechanism. The risk matrix can be qualitative, semi-quantitative or quantitative, depending on the availability of data and the objectives of the analysis. Its main function is to visualize and rank risk levels (e.g., low, medium, high, critical), which in turn allows prioritization of risk-based inspection actions in tanks and maintenance in a strategic manner, focusing resources on the areas of highest risk.
Strategic planning of the RBI program
Strategic planning is the foundation on which a successful and sustainable RBI program is built. While the methodology describes the technical execution, RBI inspection planning defines the framework, resources and philosophy that will guide the entire effort. An accurate plan ensures that objectives are clear, resources are allocated efficiently and appropriate tools are used.
Key components
- Organizational alignment and definition of strategic objectives
- Management commitment
Establishment of clear and measurable goals (SMART)
Initial scope definition and expansion planning
- Management commitment
- Program structure, roles and resources
- Formation of a multidisciplinary team
- Definition of roles and responsibilities
- Allocation of budget and required tools
- Establishing the data management framework
- Identification of essential data requirements
- Determination of data sources and validation of data prior to modeling
- Selection and implementation of appropriate technology platforms
- Definition of methodological framework and risk tolerance
- Selection of RBI analysis methodology (qualitative, semi-quan
- titative, quantitative)
- Adaptation of criteria and establishment of corporate risk matrix
- Damage mechanism review process (DMR)
- Implementation, mitigation and sustainability strategy
- Development of an implementation plan with realistic timeline
- Definition of mitigation philosophy adapted to different levels of risk
- Institutionalization of the review cycle
Tools and support for RBI inspection planning
- RBI Software: Commercial tools such as PCMS, Capstone RBMI, SagePlus, API RBI Software, etc. facilitate calculations, data management and planning.
- Standards: API 580 (general methodological framework), API 581 (detailed quantitative methodology), API 653 (inspection, repair and alteration of tanks), ISO 55000 (global asset management).
RBI Evergreen: Keeping the risk model alive
The RBI Evergreen approach represents an evolution from the traditional RBI model. Rather than performing static assessments every several years, the Evergreen model is characterized by its ability to continuously update itself with real-time data, enabling dynamic risk management.
Technological tools for an Evergreen RBI
- Effective implementation of an RBI Evergreen model relies on a variety of technologies that facilitate the collection, analysis and
- IoT sensors: These devices allow real-time monitoring of critical variables such as temperature, pressure and corrosion, providing updated data on the asset’s operating conditions.
- Predictive analytics platforms: These use advanced algorithms to analyze collected data, identify patterns and predict potential failures, enabling proactive planning of inspections and maintenance.
RBI management software: Tools such as GE Digital APM and DNV Synergi Plant integrate data from multiple sources, automate risk analysis and facilitate informed decision making.
API 580 emphasizes the importance of maintaining an up-to-date and dynamic RBI program, noting that effective risk management requires the integration of real-time data and the ability to adapt to changes in operating conditions. API 581 also provides quantitative methodologies for assessing PoF and CoF, which are integrated into technology platforms to improve the accuracy and efficiency of the RBI program.
How to Apply RBI to Storage Tanks
Implementing an RBI program for tanks follows a structured workflow:
Define objectives and scope: categorize tanks (e.g., atmospheric, conical/floating roof, pressurized), define their operational criticality, and establish reliability goals and optimization of inspection intervals for this equipment.
- Collect and validate data: Gather design specifications (materials, nominal thicknesses), service history (stored products, temperatures), previous inspection data (measured corrosion rates, CMLs), condition of coatings, maintenance and repair records, and environmental conditions; data validation is a strategic point in RBI.
- Identify degradation mechanisms: For each tank and component, identify active and potential damage mechanisms (e.g., internal corrosion, external atmospheric corrosion, bottom pitting by MIC). Grouping tanks with similar conditions optimizes the analysis.
- Calculate PoF and CoF: Apply qualitative, semi-quantitative or preferably quantitative models (see API 581 Sections 6 and 7 for detailed calculation methodologies) to estimate the probability of failure of each mechanism (age, historical, operational variables) and associated consequences (environmental, safety, economic). If data is limited, start with a qualitative approach and define as more data is obtained to a quantitative approach.
- Assess and rank risk: Combine PoF and CoF in the risk matrix to determine the level of risk (low, medium, high, critical) of each component / damage mechanism. This allows prioritization of assets.
- Plan the inspection and mitigation strategy: Based on the risk level, define:
- Inspection frequency: Shorter intervals and/or more thorough inspections for high-risk components; safe and justified extension of intervals for low-risk components.
- Inspection scope: Define what percentage of the component to inspect and where to concentrate efforts (e.g., 100% bottom inspection vs. spot UT on hull CMLs).
- Appropriate NDT techniques: Select the most effective techniques for the dominant damage mechanisms (e.g., high resolution MFL for critical bottoms, PAUT for major welds).
- Prescribed mitigation actions: Define specific corrective or preventive actions (e.g., coating repair, drainage improvement, inhibitor application, planned replacement).
- Execute and supervise: Perform inspections according to plan. Consider non-intrusive / robotic inspection for internal or at-height inspections without taking equipment out of service.
- Post-inspection review and update: The RBI program should be updated periodically with new inspection data, operational changes, repairs, or new information on damage mechanisms. This keeps the model “alive” or Evergreen.
The result of an RBI assessment is an inspection plan. This plan is based on the determination of targets or acceptable risk limits for each assessed component. When the estimated risk of a component meets or exceeds these targets, it is important to implement specific actions, such as inspections or mitigation measures, to ensure the operational integrity of the equipment.
Traditional Inspection (Time-Based – API 653) vs. Risk-Based Inspection (RBI – API RP 580 / 581)
Aspect | Traditional Inspection | Risk-Based Inspection |
---|---|---|
Frequency | Fixed predefined intervals | Variable, based on calculated risk |
Approach | Uniform for all similar assets | Priority given to critical or high-risk assets |
Decision Basis | Time / calendar | Risk (PoF x CoF) and current condition |
Cost | Potentially high (unnecessary inspections) | Optimized, focused where it’s most needed |
Effectiveness | May be low (inspects non-critical areas) | High (focused on preventing significant failures) |
Flexibility | Low, rigid | High, adaptable to operational and condition changes |
Optimization | Limited | Maximum resource and safety optimization |
Standard RBI vs. Evergreen RBI
Aspect | Standard RBI (Periodic Assessment) | Evergreen RBI (Dynamic Model) |
---|---|---|
Frequency / Update | Every 3–5 years or after major events | Continuously with new data |
Dataintegration | Manual and periodic | Automated (ideally), continuous integration |
Response tochange | Delayed until next review | Immediate adjustment to condition changes |
Inspection optimization | Based on past “snapshots” of risk | Dynamically refined with the latest trends |
Resource allocation | Reactive to the latest assessment | Proactive and based on live data |
Regulatory compliance | Meets minimum requirements at the time | Exceeds standards through real-time monitoring |
Robotics in risk-based storage tank inspection
Robotics is a strategic enabler for optimizing RBI programs in tanks, especially for non-intrusive inspections. Autonomous or remotely operated robots (submersible, floating, magnetic) can be used:
- Perform internal inspections (bottoms, annular rings) without removing the tank from service, reducing costs and downtime.
- Collect high quality data for PoF evaluation: thickness measurements (UT, PAUT), corrosion detection (MFL, GWPA, PEC), and use of machine vision systems.
- Improve safety by minimizing confined space entry.
- Integrate data directly into RBI software, streamlining risk model updating and decision making.
The use of robotic technology provides information on the actual condition of the asset, which is essential for refining PoF calculations, justifying interval extensions and focusing maintenance on the most critical components. Companies such as Gecko Robotics have developed climbing robots equipped with advanced sensors that enable non-destructive inspections of tanks; they collect data on wall thickness and other indicators of structural integrity, integrating with RBI software platforms for real-time analysis.
Conclusion
The implementation of Risk-Based Inspection (RBI), based on the API 580 standard, allows for prioritizing inspections according to the actual risk of storage tanks, optimizing technical resources and reducing unnecessary interventions. This approach, complemented by the quantitative calculations of API 581 and continuously updated through the Evergreen philosophy, strengthens decision-making based on reliable data.
References
- API Recommended Practice 580 – Risk Based Inspection
- API Recommended Practice 581 – Risk Based Inspection Technology
- API Standard 653 – Tank Inspection, Repair, Alteration, and Reconstruction
- https://www.iqpc.com/media/7466/10042.pdf