At the forefront of the transition to cleaner and more sustainable energy, corrosion protection for wind turbines is emerging as a key pillar for harnessing the potential of renewable energies. As the world moves towards an energy matrix less dependent on fossil fuels, the importance of maximizing the efficiency and durability of these structures cannot be underestimated.
A persistent challenge in the operation and maintenance of wind turbines is corrosion, a phenomenon that threatens not only the structural integrity of these facilities, but also their performance and, ultimately, their economic viability. Corrosion, induced by adverse environmental factors such as humidity, salinity, and extreme temperature variations, presents a considerable obstacle to the service life of wind turbines, particularly those located in marine or high salinity environments.
This article sets out to explore and break down the most advanced and promising anticorrosion technologies designed to meet this challenge. From innovations in materials and coatings to predictive maintenance strategies, the goal is to provide solutions that protect these structures against corrosion and promote more efficient wind power generation. The need for innovative solutions is clear, and this article seeks to present the answers that today’s technology offers to overcome this challenge.
Strategies and technologies for anticorrosive protection
Advanced materials
The selection of advanced, corrosion-resistant materials is a fundamental pillar in the manufacture and maintenance of wind turbines intended to operate in harsh environments. These materials must withstand factors such as high salinity in marine environments, extreme temperature variations, and constant exposure to humidity, factors that can accelerate corrosive processes. The right choice of materials not only increases the durability and reliability of the turbines, but also optimizes their long-term performance, reducing the need for frequent and costly maintenance.
Advanced composite materials, such as glass or carbon fiber reinforced polymers, offer lightweight, yet extremely corrosion resistant alternatives. These materials not only resist chemical degradation, but also efficiently handle the dynamic loads to which the blades and other wind turbine components are subjected. Their use significantly reduces the overall weight of the structure, which translates into lower tower and foundation loads, and facilitates installation and maintenance operations.
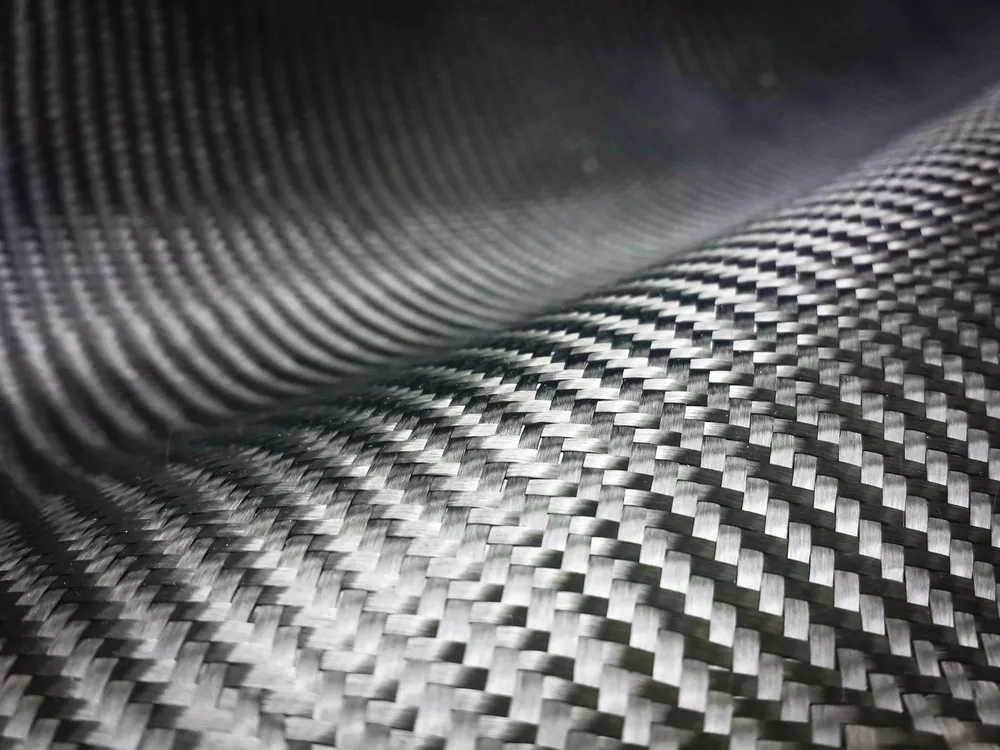
Among the corrosion resistant alloys, duplex and super duplex stainless steel stand out for their excellent performance. These alloys combine superior mechanical strength properties with high corrosion resistance, especially in saline and humid environments. Its two-phase structure, which mixes the ferritic and austenitic phases, makes it exceptionally robust against pitting corrosion and stress cracking, common problems in structures exposed to marine environments.
The development and integration of new advanced materials in wind turbine design represents a crucial advance in the fight against corrosion. Its application not only ensures greater longevity of wind turbines, but also promotes energy efficiency and sustainability in the renewable energy sector. As materials technology evolves, the ability to withstand adverse conditions while maintaining efficient operation becomes a critical standard for the future development of the wind industry.
Innovative coatings
Advances in the field of coatings have radically transformed corrosion protection strategies for wind turbines, offering more durable, efficient and self-healing solutions. Among these advances, nanotechnological and polymer-reinforced coatings stand out for their innovative approach to combating corrosive effects in harsh environments.
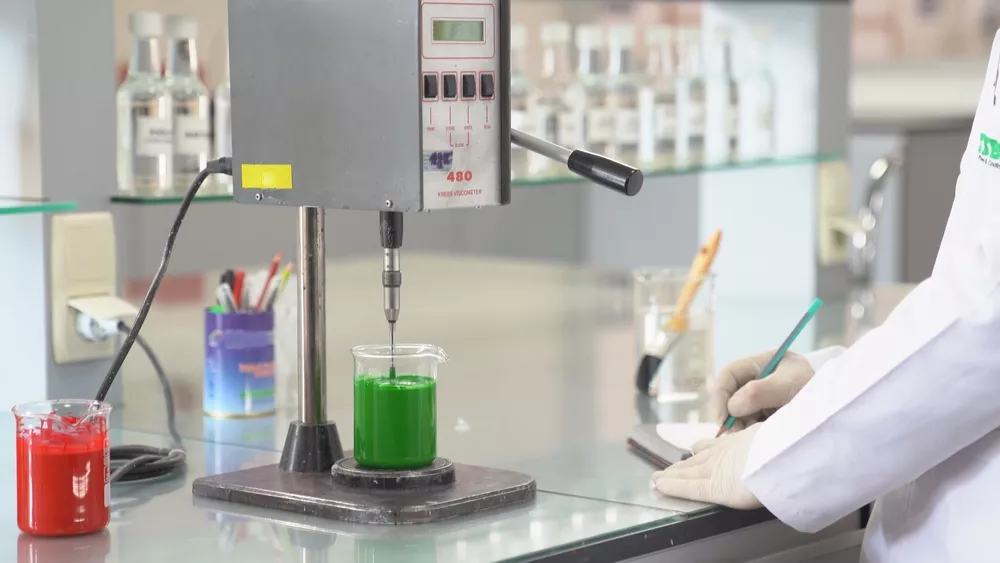
Nanotechnological coatings, composed of nanoparticles, create barriers that are virtually impermeable to corrosive agents. They provide a density and uniformity in the coating that would traditionally be difficult to achieve, offering superior protection against the penetration of water, oxygen and salts, critical elements in the corrosion process. In addition, some of these coatings are self-healing under the action of external agents; in the presence of small cracks or damage, the nanoparticles reorganize to fill the damaged spaces, restoring the integrity of the coating without external intervention.
On the other hand, coatings based on reinforced polymers represent another state-of-the-art in corrosion protection. By incorporating ceramic or metallic fibers or particles, these coatings significantly improve mechanical strength and durability against extreme environmental conditions. The presence of these reinforcements increases resistance to abrasion and wear, extending the life of the coating and, therefore, of the turbine components they protect.
These innovative coatings not only offer advanced corrosion protection, but also reduce the frequency and need for maintenance, contributing to greater operational efficiency and long-term cost reduction. Continued research and development in this field promise further improvements in the effectiveness, sustainability and applicability of coatings, ensuring that wind turbines can meet corrosive challenges with renewed confidence.
Cathodic protection systems
Cathodic protection systems are an essential strategy in the prevention of corrosion in metallic structures, particularly those that are submerged or exposed to highly corrosive environments, such as wind turbines. These systems work on the electrochemical principle of cathodicity, offering active corrosion protection through two main approaches: sacrificial anode cathodic protection and impressed current cathodic protection.
- Cathodic protection by sacrificial anodes: In this control method, a more reactive metal (electronegative anode) is used with respect to the material of the structure to be protected. Commonly, metals such as zinc, magnesium or aluminum are used for sacrificial anodes. These anodes preferentially corrode, thus protecting the metal of the structure (e.g., wind turbine steel) by making it the cathode of an electrochemical cell.
- Cathodic protection by impressed current. This control method is particularly useful for large and complex structures, where the uniformity of the protection current is decisive. Through rectifiers, they are adjusted to the passivation potential of the material to be protected, ensuring that each area of the structure receives a uniform protection current density.
The implementation of cathodic protection systems is important for the preservation of wind turbines, significantly extending their service life and reducing the costs associated with maintenance and repair of corrosion damage. These systems not only safeguard the structural integrity of the turbines against the destructive effects of corrosion, but also ensure the long-term operational efficiency and safety of these critical renewable energy generation facilities.
Predictive maintenance strategies
The integration of predictive maintenance strategies, supported by advanced monitoring and predictive analytics technologies, is revolutionizing the way wind turbine maintenance is performed, especially in corrosion prevention and management. These strategies are based on real-time data collection and analysis, allowing early identification of potential problems before they become critical failures. Artificial intelligence (AI) and machine learning play key roles in this process, processing large volumes of data from sensors installed in the turbines to detect patterns, predict deterioration trends and prescribe proactive maintenance actions.
Continuous monitoring of conditions such as humidity, air salinity, temperature and other environmental factors that contribute to corrosion allows wind turbine operators to anticipate when and where corrosion is most likely to occur. This is achieved through the use of sensors and IoT (Internet of Things) devices that collect real-time operational and environmental data. AI analyzes this data to identify anomalies or trends that indicate an increased risk of corrosion.
With this information, it is possible to schedule precise and focused maintenance interventions, specifically targeting the areas identified as high risk. This not only improves maintenance efficiency, reducing downtime and associated costs, but also prolongs turbine life by preventing corrosion damage before it occurs.
In addition, predictive analytics facilitates the optimization of maintenance strategies, allowing operators to adjust maintenance interventions based on actual operating and environmental conditions, rather than following a fixed maintenance schedule. This ensures that resources are used more efficiently, while maintaining the structural and operational integrity of the wind turbines.
In summary, the application of monitoring and predictive analytics technologies in wind turbine maintenance represents a significant advance towards minimizing corrosion and optimizing maintenance, ensuring the long-term operability and sustainability of these renewable energy facilities.
Conclusion
The integration of advanced technologies and strategies to combat corrosion marks a milestone in the evolution of the wind industry. These innovations not only extend the service life of wind turbines and optimize their performance, but also embody the spirit of progress needed to meet today’s environmental and operational challenges. By reducing the need for maintenance and increasing reliability, these solutions contribute directly to the efficiency and sustainability of wind energy.
Continuous innovation is essential in this dynamic field, driving not only the development of new technologies but also the adaptation and improvement of existing ones. This proactive attitude towards research and development is essential to keep pace with emerging challenges and maximize the potential of wind energy as a pillar of the sustainable energy matrix.
Advances in the synthesis of advanced corrosion-fighting materials strengthen the position of wind energy in the global renewable energy scenario. As we move forward, the synergy between science, technology and sustainability will remain key to unlocking the true potential of wind energy and its vital contribution to a greener, cleaner energy future.
References
Own source