Table of Contents
- Introduction
- Caustic cracking overview and impact on the industry
- Factors and conditions that cause caustic cracking
- Prevention and mitigation
- Nace Standard SP0403: Caustic Embrittlement Corrosion Control
- Challenges in caustic cracking prevention
- Technological advances and limitations
- Conclusions
- References
Introduction
Caustic embrittlement cracking represents one of the most significant challenges in the service life of industrial assets, ranging from oil refining to nuclear power production. This phenomenon mainly affects carbon and low alloy steels, seriously compromising the structural integrity of the equipment.
Throughout this article, we will explore what caustic cracking is, its causes, how to prevent and mitigate it; providing a comprehensive view of the industry’s challenges in managing caustic cracking prevention.
Caustic cracking overview and impact on the industry
Caustic cracking, also known as caustic stress corrosion cracking, is a type of deterioration that affects metals and alloys when they are exposed to alkaline solutions in the presence of tensile stresses. This phenomenon not only compromises the structural integrity of equipment, but also represents a significant risk to operational safety and economic efficiency in several key industries.
This type of corrosion occurs when carbon and low alloy steels come into contact with highly concentrated alkaline solutions, especially under high temperature and tensile stresses, causing the formation of intergranular or transgranular cracks that weaken the metal.
The implications of caustic cracking come down to costs associated with inspections, maintenance, and repairs of damaged equipment, which can amount to millions of dollars annually for a single operating plant.
In addition, equipment failures can result in unplanned shutdowns, lost production and, in the worst case, accidents that compromise human safety and the environment.
Factors and conditions that cause caustic cracking
To develop effective prevention and mitigation strategies, it is crucial to understand the factors that contribute to caustic cracking. These include the concentration of the alkaline solution, the operating temperature and the level of tensile stress present in the material.
Generally speaking, the occurrence of alkali caustic cracking of carbon steel and low alloy steel requires three conditions:
- Caustic soda concentration: The risk of cracking increases significantly when the NaOH concentration exceeds 5% in carbon and low alloy steels.
- Temperature: The critical temperature for caustic cracking is around 50 °C, increasing dramatically near the boiling point of the solution.
- Tensile stress: According to theory, the Stress Corrosion Cracking (SCC) mechanism of low carbon steel in alkaline solution with hot concentrate belongs to intercrystalline anodic dissolution, and the potential of SCC lies in the activation-passivation transformation range. When the local NaOH is higher than 10%, the protective oxide film of the metal will dissolve and react further with the base.
The susceptibility of the material to caustic corrosion and CSCC is highly dependent on the concentration of caustic soda, the process temperature and the type of metal alloy. Carbon steel is the most common material used for caustic environments and is susceptible to CSCC and general corrosion or pitting at temperatures above 50-60 °C and NaOH concentrations below 20 wt%. Stainless steel provides more protection, but is at risk of CSCC and aggressive corrosion above 120 °C. As shown in the following image.
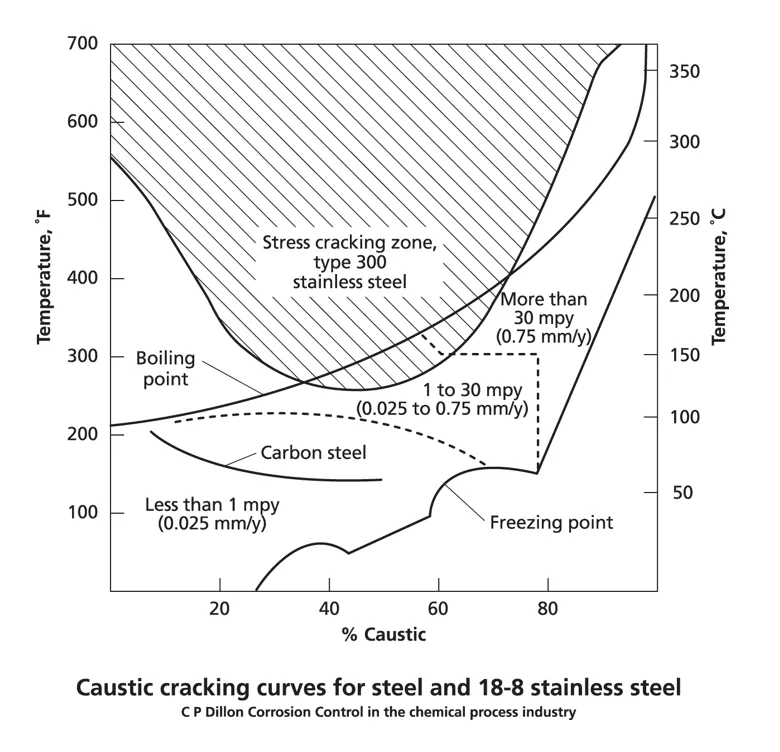
(Source: ASSDA)
Prevention and mitigation
Prevention and mitigation of caustic cracking involves a combination of proper material selection, stress management, use of corrosion inhibitors, and control of operating conditions. These strategies not only help extend equipment life, but also improve safety and operational efficiency.
Material selection
Selection of the right material is critical to avoid caustic cracking. Carbon and low alloy steels may be suitable for certain conditions, but their susceptibility increases with NaOH concentration and temperature.
The use of austenitic stainless steels, although more expensive, can offer high corrosion resistance in alkaline aqueous media. The addition of elements such as titanium and niobium has been shown to improve the resistance to caustic cracking in certain steels.
Reduction of residual stress
Proper residual stress management through fabrication and welding techniques is crucial. Implementation of proper preheating and post-heating during welding, along with control of the welding sequence, can minimize residual stresses that contribute to cracking.
In addition, post weld heat treatment (PWHT) can be effective in reducing stress and improving the microscopic structure of the material.
Corrosion inhibitors
The use of corrosion inhibitors is an effective strategy to reduce the risk of cracking. Compounds such as phosphates, nitrites and sulfates can form a protective layer on the surface of the metal, decreasing its reactivity in alkaline environments.
The proper selection and dosage of these inhibitors depends on the specific operating conditions and must be determined by testing.
Temperature and concentration control
Maintaining temperature and NaOH concentration within safe limits is essential to prevent caustic cracking. This can be achieved through proper design of process systems and implementation of operational controls that prevent excessive evaporation and concentration of alkaline solutions.
Continuous monitoring of these conditions allows early detection of risk situations. Today’s tools allow the user to control these variables through this monitoring.
Nace Standard SP0403: Caustic Embrittlement Corrosion Control
Among effective strategies to combat caustic cracking, NACE SP0403 stands as a guiding light for the industry. This standard details procedures and best practices to prevent caustic stress corrosion cracking on carbon and low alloy steels, which are critical in the context of refinery equipment.
By advocating rigorous material selection, advanced process control methods and conscious system design, NACE SP0403 provides an invaluable framework for engineers and plant operators. Implementing the recommendations of this standard can not only significantly extend equipment life, but also increase process safety and operational efficiency.
Challenges in caustic cracking prevention
Caustic cracking in metals, particularly in carbon and low alloy steels, represents a persistent problem for industries including petrochemical, petroleum refining, and power generation.
Despite significant efforts to understand and prevent this type of stress corrosion cracking, there are several challenges that complicate its complete mitigation.
Variability of operating conditions
One of the main difficulties in preventing caustic cracking is the high variability of operating conditions to which equipment and structures are exposed. Differences in temperature, concentration of caustic solutions, and mechanical stresses can vary significantly, not only from one facility to another, but also within the same plant.
For example, in oil refineries, where caustic soda is used to remove acids from crude oil, variations in crude oil composition can alter corrosion conditions in unpredictable ways.
Technological evolution of industrial processes
The continuous evolution of industrial processes presents another challenge. As industries seek to improve efficiency, reduce costs and comply with stricter environmental regulations, the processes and materials used change with technological advancement. These changes may introduce new vulnerabilities to caustic cracking.
For example, the increased use of enhanced oil recovery techniques, such as steam injection, may increase the risk of cracking in equipment due to the high temperatures and pressures involved.
Need to balance cost efficiency with material integrity
The balance between cost efficiency and material integrity is perhaps the most significant challenge. Implementing caustic cracking prevention measures, such as the selection of corrosion resistant materials, the use of protective coatings and the application of heat treatments, involves additional costs. Companies must balance these costs against the potential risk of equipment failure and associated consequences, such as unplanned downtime and accidents.
An example of this trade-off is the decision between using carbon steel, which is less expensive but susceptible to caustic cracking, versus austenitic stainless steels or nickel alloys, which offer greater strength but at a significantly higher cost.
Despite advances in the understanding and mitigation of caustic cracking, the industry faces continuing challenges in the effective prevention of this phenomenon. These challenges include the variability of operating conditions, the evolution of industrial processes and the need to balance cost efficiency with material integrity.
Technological advances and limitations
Technological advances in the prevention of caustic cracking, especially in the fields of corrosion-resistant materials and corrosion inhibitors, are leading the way to more effective and durable solutions. However, the adoption of these innovations faces significant barriers, mainly related to costs and the complexity of integrating new technologies into established infrastructures and systems.
Some practical examples of these advances and the limitations associated with their implementation are detailed below.
Technological advances in materials
- Corrosion-resistant alloys: New alloys, such as nickel-based superalloys and duplex stainless steels, have been developed that offer superior resistance to caustic cracking in extreme environments. These alloys are designed to withstand high concentrations of caustic soda and elevated temperatures without degrading.
- Example: In the petrochemical industry, the use of duplex stainless steel piping in catalytic cracking units has been shown to significantly reduce the risks of caustic cracking, extending the life of the facilities and minimizing unscheduled maintenance shutdowns.
- Limitations: The cost of these superior alloys is significantly higher than traditional materials such as carbon steel. In addition, welding and processing of these alloys may require specialized techniques and advanced equipment, further increasing implementation costs.
Advances in corrosion inhibitors
- High efficiency corrosion inhibitors: Research in materials chemistry has led to the development of more effective corrosion inhibitors, which can be added to systems to prevent caustic cracking by forming a protective layer on metal surfaces. These inhibitors are designed to be effective at low concentrations and over a wide range of operating conditions.
- Example: In industrial cooling systems using water treated with caustic soda, the addition of phosphate or silicate-based inhibitors has been shown to be effective in preventing corrosion and cracking of metal components.
- Limitations: Although modern inhibitors are more efficient and versatile, their selection and dosing require a thorough knowledge of the specific system chemistry and operating conditions. In addition, continuous monitoring and adjustment of inhibitor concentration can increase operating costs. There is also the challenge of ensuring the compatibility of these inhibitors with the environment and discharge regulations.
Integration of new technologies
- Advanced monitoring and diagnostics: Real-time monitoring technologies and advanced diagnostic systems, such as electrochemical impedance spectroscopy (EIS) and IoT (Internet of Things)-based sensors, offer new opportunities to detect and prevent caustic cracking before it causes significant damage.
- Practical example: Implementing wireless sensors on pipelines and vessels to monitor corrosion conditions and stresses in real time allows chemical plants and refineries to identify areas of risk and proactively take corrective action.
- Limitations: Installing advanced monitoring and diagnostic systems in existing plants can be challenging due to the need to integrate these systems with existing control hardware and software. The initial investment and maintenance costs of these technologies can be prohibitive for some operations.
While technological advances offer promising solutions to combat caustic cracking, their effective implementation requires overcoming significant challenges. The balance between the cost and benefit of these innovations is a critical factor that industries.
Conclusions
Caustic cracking presents a significant challenge to the integrity and safety of industrial equipment, but with a thorough understanding of its causes and the implementation of effective prevention and mitigation strategies, it is possible to manage and minimize this risk.
As the industry moves towards adopting more advanced technologies and more efficient processes, collaboration and continued commitment to innovation will be key to overcoming the challenges associated with caustic cracking.
Caustic cracking is estimated to be responsible for more than 20% of equipment failures in the petrochemical industry, underscoring the importance of effectively addressing this problem.
“Find out how to protect your equipment against caustic cracking – act now!”
References
- API (American Petroleum Institute) Publications
- API 571: “Damage Mechanisms Affecting Fixed Equipment in the Refining Industry”.
- API 945: “Avoiding Environmental Cracking in Amine Units”.
- NACE International
- NACE TM0177: “Laboratory Testing of Metals for Resistance to Sulfide Stress Cracking and Stress Corrosion Cracking in H2S Environments”.
- NACE SP0403: “Avoiding Caustic Stress Corrosion Cracking of Refinery Equipment and Piping“.
- Australian Stainless Steel Development Association. (n.d.). FAQ 8 – General Corrosion Resistance: The Normal State for Stainless. Retrieved March 1, 2024 from https://www.assda.asn.au/publications/technical-faqs/faq-8-general-corrosion-resistance.