Introduction
Subsea pipelines are systems that are fully or partially submerged in water and are of critical importance in the global energy industry by facilitating the transportation of crude oil and its derivatives through marine terminals. Maintaining its integrity is essential to ensure a safe and reliable energy supply. However, these structures constantly face problems and damage due to erosion corrosion, which can compromise the stability and continuity of the energy supply.
In this article, we will explore the crucial role of marine pipelines, the devastating impact of erosion corrosion on their operability, effective methods to control, prevent and detect it, as well as innovations that are extending their service life.
Marine pipelines as a means of transport
Offshore pipelines in the oil and gas industry are critical for transporting crude oil, natural gas and refined products from producing fields to onshore processing facilities.
These subsea pipelines are used to connect offshore production platforms with existing onshore infrastructures, enabling the efficient transport of hydrocarbons. They are also used to transport refined products to tank farms that are generally located near the refinery, but could be hundreds of kilometers away.
In addition, in ultra-deep water, subsea pipeline construction represents technological challenges unprecedented in the industry. This has led to the development of new technologies, not only in the field of metallurgy, but also in the construction of vessels for the transfer and laying of pipes, as well as the operation of advanced monitoring systems.
It is important to note that the construction and maintenance of these subsea pipelines require a large investment and careful planning to ensure their safe and efficient operation. Impact of erosion corrosion on the operability of marine pipelines.
Erosion corrosion in marine pipelines is a phenomenon that occurs when the movement of a corrosive agent, such as salt water, over a metal surface accelerates its destructive effects due to mechanical wear. This process can be particularly intense with the presence of abrasive particles in the flow, high velocity conditions, turbulence and shock, and is frequent in pumps, mixers and pipelines, especially in bends and elbows.
Factors to consider in the integrity of marine pipelines
- Material wear: This type of corrosion causes wear of the material that can generate obstructions, breaks and loss of the quality of the liquid or gas transported by the pipeline.
- Weakening of pipelines: Erosion corrosion can gradually but steadily weaken pipelines. As metals corrode, they lose strength and may present structural failures, jeopardizing the safety and functionality of the facilities.
- Increased roughness: Erosion corrosion can increase the roughness of pipelines, which affects their bearing capacity.
- Reduced service life: The constant presence of salt water and exposure to marine elements accelerate the corrosion process. This can significantly reduce the lifespan of marine infrastructure, resulting in additional repair, replacement and maintenance costs.
It is important to implement preventive and control measures to minimize erosion corrosion in marine pipelines and ensure their long-term integrity and functionality.
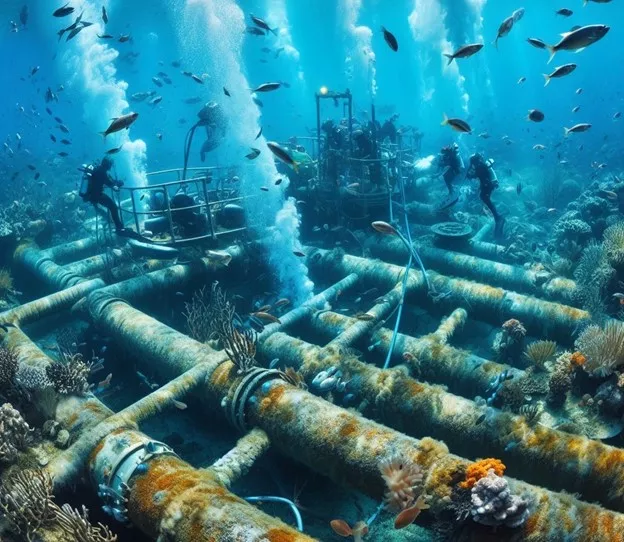
How can erosion corrosion in marine pipelines be prevented and controlled?
It is important to remember that the best strategy for controlling erosion corrosion will depend on the specific conditions of each situation, including the type of pipeline, the environment and the fluid being transported. Erosion corrosion control in marine pipelines involves a combination of preventive and corrective strategies:
- Material selection: Selecting materials that are inherently resistant to erosion corrosion corrosion can be an effective strategy.
- Coatings and linings: They act by forming a physical barrier between the pipeline material and the corrosive medium. This may include paints, epoxy coatings and other protective materials.
- Specific corrosion inhibitors: The application of chemical inhibitors can reduce the corrosion rate and protect exposed metal surfaces in marine pipelines.
- Pipeline design: Pipeline design can be modified to minimize erosion. For example, pipelines can be designed to minimize sharp bends that can cause turbulence and increase erosion.
- Flow velocity control: Controlling the velocity of fluid flowing through pipelines can help minimize erosion. Lower speeds can reduce damage caused by erosion corrosion.
- Regular inspections: The implementation of real-time monitoring systems and advanced inspection technologies allows constant surveillance of the condition of offshore pipelines. From detecting corrosion changes to identifying vulnerable areas, these tools are essential for proactive structural integrity management.
- Cathodic protection: A control method used to protect pipelines from corrosion. It involves the use of a more “sacrificial anode” metal (such as zinc) that corrodes instead of the metal of the pipe.
- Maintenance and repair: Taking a proactive approach to marine pipeline maintenance is essential to mitigate the effects of erosion corrosion. Cleaning programs, coating repair and replacement of corroded sections help prevent deterioration and ensure the continued operability of the subsea infrastructure.
- Protective and anti-flotation structures: To mitigate erosion problems, geotextile mattresses that are filled with cement mortar or using geotextile tubes that are filled with in situ materials and placed over pipelines as protective and anti-flotation structures can be used.
It is important to remember that the prevention of erosion corrosion in marine pipelines requires a comprehensive approach that takes into account both environmental factors and the materials and techniques used. The choice of prevention strategy will depend on the specific conditions of each project.
How can erosion in marine pipelines be detected?
Erosion detection in marine pipelines can be challenging due to the harsh conditions of the marine environment. However, there are several techniques that can be used to detect erosion:
- Visual inspection: It is the basic inspection before starting a detection and quantification process to identify any potential damage or risk.
- Ultrasonic testing: Conventional ultrasonic testing (Thickness Measurement) and PAUT defectology ultrasonic testing are non-destructive testing techniques that allow the inspector to verify the pipeline while in service.
- X-ray tests: Although they require evacuation of the area to limit personnel exposure to radiation (conventional) and digital radiography tests, where applicable, may be useful in detecting erosion.
- Inspection with ROV (Remotely Operated Vehicle): ROVs are unmanned vehicles that are remotely controlled from the surface and are equipped with cameras and other instruments to perform various tasks. They are especially useful in the inspection of marine structures, as they can operate in deep water and in difficult conditions where it would be dangerous or impossible for human divers. ROVs can perform visual inspections and acquire data with multibeam sonar.
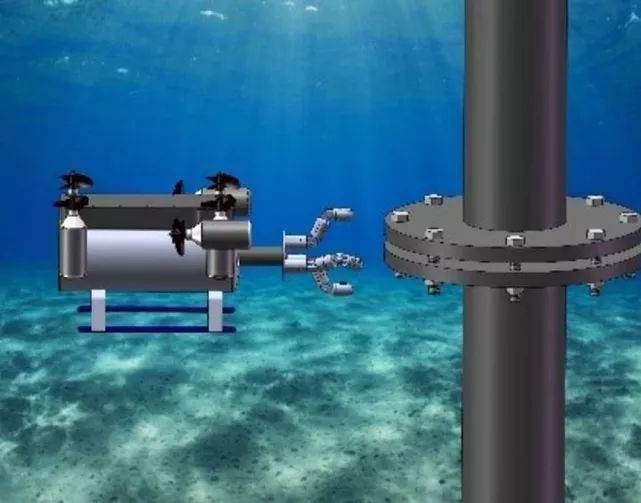
- Ultrasonic guided wave testing: Despite some limitations, ultrasonic guided wave testing remains a valuable tool for subsea pipeline inspections, especially for detection and monitoring purposes.
It is important to remember that no single detection technique is totally reliable and they are often used in combination to obtain comparison results to make the best decision on the condition of offshore pipelines.
Conclusions
In a world where the demand for energy is insatiable, the integrity of offshore pipelines is essential to ensure a safe and sustainable supply. Through the use of advanced technologies, proactive maintenance practices and a culture of corrosion prevention, the energy industry can safeguard its critical assets and extend the life of its offshore pipelines.
Investment in ongoing research and development is essential to meet present and future challenges, thus ensuring a reliable supply of energy for generations to come.
Erosion corrosion control is an important aspect of offshore pipeline management. There are a number of control mechanisms that can be used to ensure operability and extend pipeline life.
Oil and gas companies should take a proactive approach to erosion corrosion control. This includes assessing corrosion risks, implementing appropriate control measures and performing regular inspections.
Recommendations
Oil and gas companies can adopt the following recommendations to control erosion corrosion in their offshore pipelines:
- Conduct a risk assessment to identify areas that are most prone to erosion corrosion.
- Implement appropriate control measures, such as reducing fluid flow velocity, use of anti-corrosion coatings or composite materials.
Marine pipelines require your control!
References
Own source