Introduction
The planning and control of plant shutdown inspections transcends the need to ensure compliance with required or requested inspection activities to ensure the integrity and reliability of the plant under maintenance. Planning for plant shutdown inspections begins with several deadlines prior to the scheduled start date; this process must be managed comprehensively, both before, during and after the completion of the shutdown activities.
Planning inspections under the requirements of a well-defined scope of work and inspection plans creates the opportunity to create precise strategies and proactive solutions that fit within the time constraints of the operational window. This perspective also allows the identification of potential problems and the generation of proactive solutions that maintain the context of inspection planning during the shutdown.
By aligning inspection objectives with the specific needs of the plant, smooth execution is ensured and the risks of unexpected delays or failures are minimized, improving the overall progress of shutdown planning. In this article we will learn about the importance of inspections during plant shutdowns, outlining appropriate inspection planning strategies, the relevance of resource allocation and identification of critical areas.
What are plant shutdowns?
Shutdowns are a cyclical process where industrial plant operations are interrupted. Also known as turnarounds, plant shutdowns are operational requirements that are met in planned periods where the plant is out of service to perform critical maintenance activities such as inspection, cleaning, repair, replacement, modifications and upgrades, in order to run efficiently and safely during the next operational run.
The scheduling of these shutdowns is based on the condition of the systems and equipment, and the risk level of the facilities, and is fundamental to prevent unplanned shutdowns that result in significant production losses and other problems. Additionally, these shutdowns facilitate the inspection and maintenance of equipment that cannot be inspected during normal operations, allowing the efficient identification and resolution of potential failures.
Most industries go through an extensive inspection and testing process during a shutdown because they inspect hundreds of equipment and piping systems. If during the shutdown the inspection or test identifies severe problems, the duration time may be extended.
Importance of inspections during shutdowns
Plant shutdown inspections are defined as the evaluation of the physical and structural conditions of the components or mechanisms that make up the plant during a scheduled shutdown. Inspections involve comprehensive processes necessary to ensure that planned objectives are met.
Non-destructive testing and inspections are important to ensure the integrity and functionality of the equipment and systems evaluated, repaired and tested; they identify and address problems that could lead to failures that could result in facility safety hazards or loss of process efficiency.
Inspections during shutdowns also allow to delimit repairs, replacements or to request any necessary change or improvement, which is impossible or highly risky to execute during regular operations.
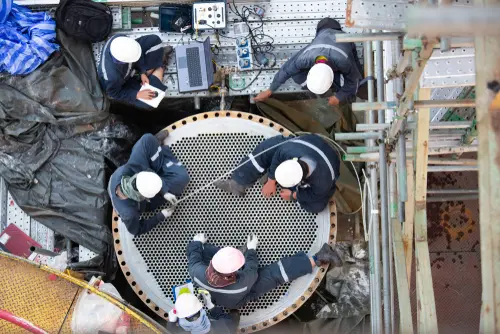
Inspection services detect and address problems such as corrosion, pitting, cracks, material degradation and equipment defects, mostly on the internal side. Each step of inspection, testing and quality control is recorded in detail; through documentation, control of activities, repairs and test results is achieved, providing valuable information for future interventions.
Inspection planning strategies for plant shutdowns
In plant shutdowns, planning and inspection strategies maximize the benefits for resource and time management during these operational windows; scheduling involves pre-, during and post-shutdown tactics to ensure process effectiveness and safety. A well-structured and well-defined inspection planning ensures effective and safe management of inspections during plant shutdowns.
The planning of inspection services during shutdowns presents several strategies before, during and after plant handover:
Previas: It is a key process to comply with maintenance management.
- Plan inspection and testing activities based on the scope of work and the inspection plan, adjusting to the timing of the overall shutdown planning.
- Form a work team, defining roles and functions of each inspector.
- Take into account the information indicated in the work procedures and inspection plans to determine the activities and risks associated with each equipment or system to be inspected.
- Coordinate in advance bidding processes with providers of advanced inspection and specialized NDT services that include the necessary new inspection technologies.
- Define critical routes and high risk areas for inspection to manage resources.
- To know and have available the resources required for each inspection activity, highlighting the specialized manpower and thus, avoid waiting times for service providers.
During: This phase of the shutdown comprises the deployment of the planned activity.
- Maintain planning and progress control of inspection activities. Purge inspected and approved systems or equipment; and identify pending inspections to be performed.
- Ensure that everything requested in the scope of work can be executed within the allotted time. Sequencing activities to optimize the use of all allocated resources.
- Maintaining communication with the safety, maintenance and equipment inspection teams is a relevant strategy for the progress of activities.
- Track current schedule versus planned or forecasted schedule.
- Ensure logistics for personnel and specialized non-destructive testing.
- Know the status of inspection tasks: in progress, completed and approved.
- Keep in mind that part of the work to be carried out depends on the results of the inspections performed.
- Adhere to acceptance and rejection criteria during inspection results to avoid rework or additional activities.
- Maintain a record control of the repairs generated by damages found during inspections, this monitoring must be systematic and with responsible persons to verify the progress and that the repairs have been accepted and released.
- Anticipate possible constraints and schedule unforeseen situations that are not included in the scope. The ability to handle unexpected problems maintains project deadlines.
- Maintain a robust action response when a problem or delay occurs due to resource availability. Take action with available resources.
Subsequent: Focused on continuous post-delivery follow-up of the shutdown
- Unaccepted or unfinished inspections or repairs should be documented to maintain continuous tracking of their condition or status.
- Conduct a comprehensive post-shutdown evaluation and lessons learned session, identifying areas for improvement and documenting valuable ideas.
- Prepare final inspection and test reports. These reports are necessary tools to optimize the planning of inspections for the next shutdown.
These strategies ensure that the planning of plant shutdown inspections is effective, where critical routes and the most important aspects of the plant are prioritized and evaluated accurately, reliably and in compliance with standards to ensure asset integrity, thereby reducing the likelihood of unexpected failures or accidents after shutdown.
Identification of critical areas
In the inspection section, critical areas in the plant are identified with their operational conditions, maintenance and inspection history. This step is fundamental to the inspection process; these areas often include critical equipment and systems that are essential to the continued operation of the plant, maintain a history of problems, or pose significant safety risks.
By focusing on these areas, planners allocate resources and efforts more effectively, ensuring that the most important components receive the attention they need. Inspections that require certified technical personnel or specialized Non Destructive Testing (NDT) methods that require specific resources are also considered critical. Likewise, inspections to be performed in confined spaces, at heights or tasks that require other maintenance activities.
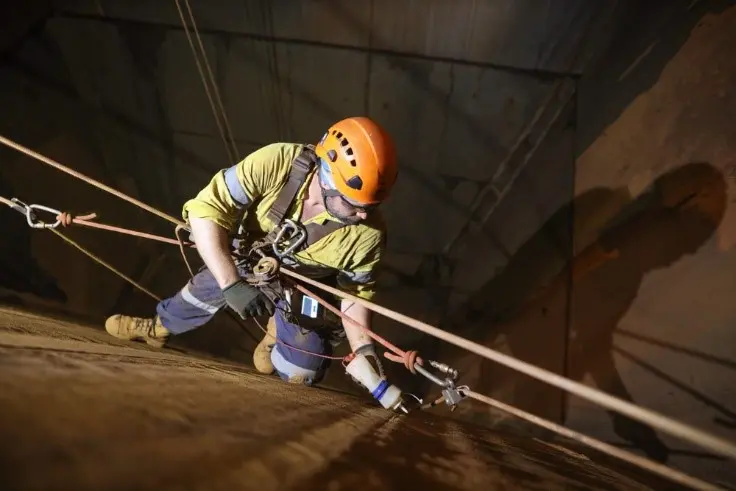
Implement inspection technologies
Nowadays, the application of advanced inspection technologies streamlines the inspection process, improving the efficiency, effectiveness and response times of inspections during shutdowns. Technologies such as drones, robotic inspection devices, advanced NDT methods with specialized sensors provide real-time results and detailed comparisons that require a better view of plant conditions.
Inspection technologies not only improve the quality of inspections but also reduce turnaround time, minimize safety risks, have greater efficiency in data processing, which contributes to a more efficient shutdown process. Advanced inspections are usually supported by conventional methodologies that fit the customer’s requirements; but already having an overview of the conditions.
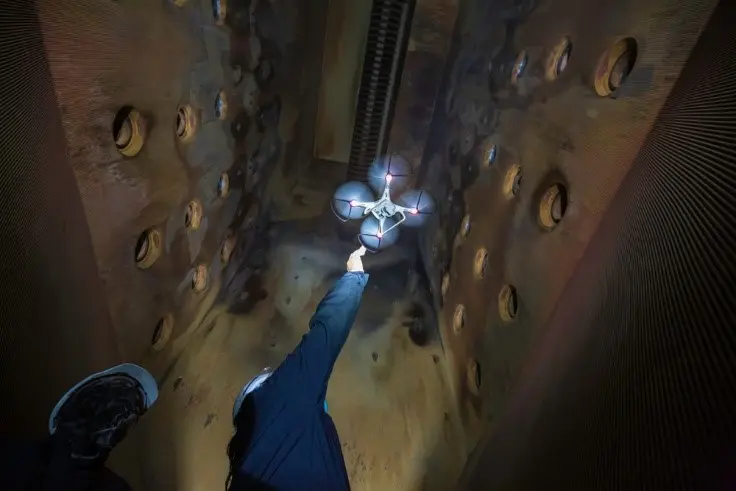
Traditional inspection methods are often slow, manual and require extensive scaffolding and other resources, resulting in increased downtime. That is why today state-of-the-art inspection technologies are dominating the industry.
Conclusions
In plant shutdowns all inspection activities must be prepared, calculated, monitored and executed in the shortest possible time, since the efficiency of the inspections represents not only the success of the planning, but also the reliability and structural assurance of all the evaluated systems.
Compliance with inspection planning during plant shutdowns involves strategies and solutions that fit within operational time limits, allowing the identification of potential problems. By aligning inspection objectives with the specific needs of the plant, risks are minimized and the efficiency of the shutdown process is improved.
Comprehensive planning, involving inspection planning strategies from the pre-stop phase to the conclusion of the shutdown, ensures smooth and safe execution, highlighting the importance of effective resource management and the identification of critical areas for inspection.
References
- https://www.jouav.com/blog/refinery-turnaround.html
- https://guiadelgas.com/paradas-de-planta-una-actividad-que-requiere-maxima-eficiencia/