Introduction
Corrosion Under Insulation (CUI) poses a considerable challenge in critical sectors such as oil, gas, chemicals and energy. Risk-Based Assessment (RBI) emerges as a key tool to address this problem. The question that arises is: Under what approach, qualitative or quantitative, should this evaluation be carried out? The answer is critical to developing effective corrosion management strategies.
Choosing between quantitative and qualitative approaches in Risk Based Assessment (RBI) should not be a conundrum, but rather an opportunity to improve the reliability of your assets. This article focuses on that reality, where we demystify the complexity of selecting the correct path to evaluate Corrosion Under Insulation (CUI) through the application of Risk Based Inspection (RBI).
Importance for the reader
For energy sector professionals, this article offers a critical look at corrosion management, providing insights that could transform the way daily challenges are addressed.
Students, eager to immerse themselves in the complexities of the world of work, will find here an essential guide to understanding how decisions in the CUI assessment can impact their professional future.
Entrepreneurs and companies, aware that the integrity of their assets is important for the operation of the company, will discover strategies. This article is not just technical information; is a topic that connects diverse audiences with knowledge that can transform their approaches to corrosion management.
What is Corrosion Under Insulation (CUI)?
Corrosion Under Insulation (CUI) is a phenomenon that normally affects carbon steel pipes and equipment, but also sometimes stainless steel elements when exposed to operational variables that cause the problem. This type of corrosion occurs as a result of water entering or condensation under the thermal insulation.
Below are the factors that contribute to Corrosion Under Insulation (CUI):
- Fluctuating temperatures
- Condensation
- High relative humidity
- Contamination
- Design or installation defects
Corrosion Under Insulation (CUI) can cause deterioration and damage to the surface of equipment that is covered with insulating materials, and is mainly caused by the accumulation of moisture. This category of corrosion can also include Corrosion Under Fireproofing (CUF) of pipes and pressure equipment.
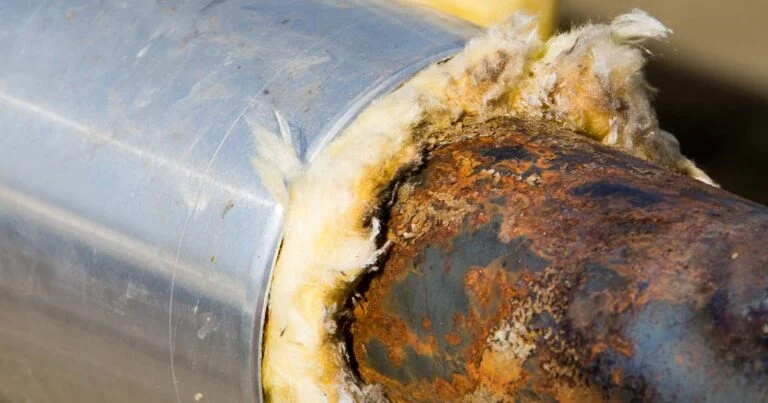
The most common problems that arise are:
- Failures in pipes, equipment and structures
- fluid losses
- Property damage
- Personal injuries
These important problems in industries where piping and pressure vessel systems are used, such as the oil and gas industry, chemical industry and energy industry, must be managed efficiently by their operators.
According to the International Corrosion Association (NACE), Corrosion Under Insulation (CUI) can cause economic losses of up to $200 billion a year.
Risk-Based Assessment is a methodology that helps prioritize and efficiently manage corrosion risks. However, the question arises: Should we use a quantitative or qualitative approach in addressing CUI under RBI?
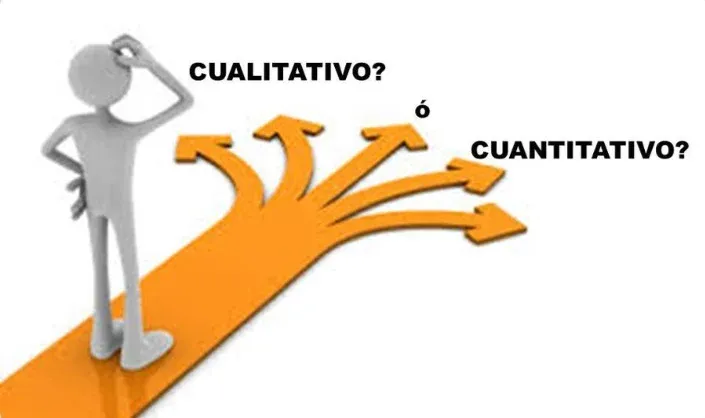
How to select the right approach?
Selecting the appropriate approach for Corrosion Under Insulation (CUI) assessment using Risk Based Assessment (RBI) is a strategic decision that requires careful consideration. To make the right decision it is necessary to follow the following steps:
- Understand the nature of the equipment: Analyze the specific nature of the equipment and piping. For critical and high importance components, a quantitative approach may be more appropriate for detailed evaluation. For example, an Asset that impacts safety, productivity and manages critical operational variables (high temperatures, high pressures and large flows) or any of them.
- Data Availability: Assess data availability and quality. If you have access to detailed and reliable data on environmental conditions, inspection histories, and chemical composition, the quantitative approach may be viable. It is advisable to have software to carry out management such as history and review calculations for early decision making.
- Operational criticality: Consider the operational criticality of equipment, in situations where precision is necessary to avoid significant operational disruptions, a quantitative approach may be preferable.
- Available Resources: Evaluate available resources, both in terms of technology and trained personnel. A quantitative approach may require significant upfront investments in technology and training.
- Inspection History: Review inspection and maintenance history. If there is a strong history of effective visual inspections and preventive maintenance, a qualitative approach may be sufficient.
- Time and costs: Consider time and cost constraints. If a rapid and cost-effective evaluation is sought, a qualitative approach may provide acceptable results.
- Hybrid approach: Do not rule out the possibility of a hybrid approach. Combining quantitative and qualitative elements can offer a comprehensive strategy that takes advantage of the best of both approaches.
- Consult experts: Seek the opinion of corrosion and asset management experts. Consulting experienced professionals can provide valuable information about the appropriateness of each approach for your specific situation.
- Consider the industry trend: Be aware of emerging trends. The widespread adoption of a particular approach can indicate its effectiveness and relevance today.
- Continuous evaluation: Corrosion management is a continuous process, the approach must be reviewed and adjusted periodically based on evolving operating conditions and technological advances.
Ultimately, selecting the appropriate approach will depend on the unique combination of factors in the operating environment. Carefully evaluating these elements will allow you to make informed decisions that benefit the long-term integrity of your assets.
Quantitative approach to the evaluation of Corrosion Under Insulation
To effectively manage Corrosion Under Insulation (CUI), the quantitative approach emerges as a beacon of mathematical precision. This method, backed by detailed data and predictive models, provides deep insight into the rate of deterioration and remaining useful life of the equipment.
Quantitative evaluation involves the use of numerical data and mathematical models to calculate the probability and impact of corrosion. Detailed data must be collected about the system, such as temperature, humidity, chemical composition, and inspection history. This data is used to feed corrosion models that predict the rate of deterioration and remaining useful life of the equipment.
Below we present the advantages and challenges of this approach, exploring success stories, revealing percentages and the innovations that are transforming the landscape of CUI management.
Advantages of the quantitative approach
- Unprecedented Accuracy: Comprehensive data, from environmental conditions to inspection histories, feeds models that provide accurate corrosion rate results.
- Informed Decision Making: Industry leaders and CEOs of leading companies support the accuracy of the quantitative approach when making informed decisions about repairs, replacements, and inspection strategies.
- Resource optimization: Statistics have indicated that companies that adopt quantitative approaches experience a reduction in maintenance costs, thanks to the efficient allocation of resources based on accurate risk assessment.
- Technological innovations: Technology integrated with artificial intelligence has improved corrosion prediction, revolutionizing the way companies apply the quantitative approach.
Challenges of the quantitative approach
- Complexity in data collection: Although accuracy is key, a considerable number of companies experience some complexity in the data collection process when adopting the quantitative approach.
- Sensitivity to variables: Notable cases, such as incidents or accidents in case studies, have revealed that quantitative models can be sensitive to small variations in input variables, affecting the accuracy of predictions.
- Associated costs: Despite long-term resource optimization, the initial implementation of the quantitative approach can entail significant costs in terms of technology and staff training.
The quantitative approach, supported by accurate data and innovative technologies, stands as a pillar in the effective management of CUI. However, overcoming key challenges is essential to fully leverage its benefits and ensure successful implementation in the energy sector.
Qualitative approach to the evaluation of Corrosion Under Insulation
The qualitative approach arises from human experience and detailed observation. Below are the advantages and challenges:
Advantages of the qualitative approach
- Speed and efficiency: Visual evaluation and human experience allow for rapid identification of problem areas. This translates into a quick response to possible risks.
- Less reliance on quantitative data: In situations where the availability of detailed data is limited, the qualitative approach provides a valuable alternative, freeing operations from the rigidity of extensive data collection.
- Empirical knowledge: Experienced professionals support the wealth of empirical knowledge in the evaluation of CUI. Experience accumulated over the years can provide invaluable insights.
- Lower startup costs: Statistical studies indicate that companies that take a qualitative approach experience a 20% reduction in startup costs compared to quantitative approaches.
Challenges of the qualitative approach
- Subjectivity in evaluation: The subjectivity inherent in qualitative evaluations can generate variations in the interpretations of different professionals. This highlights the importance of standardization.
- Limitation in predicting useful life: Unlike quantitative models, the qualitative approach may have limitations in accurately predicting the remaining useful life of equipment, which can lead to a more reactive than preventive approach.
- Reliance on human experience: This largely depends on human experience. Staff turnover or lack of training can affect consistency in evaluation.
Qualitative assessment relies on experience and expert judgment to assess corrosion risk. Visual inspections , maintenance histories and empirical knowledge are used to classify the risk of CUI.
Conclusions
In summary, through quantitative and qualitative approaches in an evaluation of Corrosion Under Insulation (CUI) through Risk Based Assessment (RBI), it is not a unilateral decision, but a strategy that must be adapted to the uniqueness of each operating environment.
From the mathematical precision of the quantitative approach to the agility and human expertise of the qualitative approach, each approach brings strengths and faces challenges. The key lies in a deep understanding of operational needs, data availability and long-term vision.
Ultimately, the integration of quantitative and qualitative elements could be the path towards holistic management of Corrosion Under Insulation (CUI). A hybrid approach based on the precision of mathematical models and human experience can offer a robust strategy that not only addresses current challenges but also adapts to future innovations.
CUI management is not just a technical issue; It is a continuous issue of adaptation and improvement. As we close this chapter, it is important to consider the choice between quantitative and qualitative approaches; which is a tool that allows us to maintain the integrity of the assets, moving wisely towards a more resilient and efficient future in the energy sector.
By adapting the methodology to the specific needs of each case, industries can significantly improve the integrity and reliability of their assets against corrosion.
Act Now to Protect your Assets!
References
Own source