Table of Contents
Permanent sensors play a considerable role in industrial risk analysis, as risks associated with industrial operations need to be accurately and proactively addressed for optimal development. Although completely eliminating risks in this context implies constant challenges, such as optimizing safety, identifying and efficiently managing potential dangers and operational problems in real time.
These advanced devices allow the timely detection of possible risks, thus contributing to the prevention of incidents and the improvement of industrial safety. In addition, by constantly monitoring operating conditions, permanent sensors enable predictive maintenance, increasing efficiency and prolonging the useful life of equipment, collecting data in real time, facilitating informed decision making and improving operational efficiency by reducing lead times. inactivity.
These devices can be perceived as the key to continuous and accurate risk assessment, allowing an agile response to any deviation in industrial systems. This technical approach strengthens the ability of companies to meet security challenges in complex environments. Below are some relevant aspects of these sensors, and their influence on risk assessments.
What is a permanent sensor?
It is a measurement device permanently installed in a specific infrastructure, such as an oil well, with the purpose of providing continuous and precise monitoring of variables, such as: pressure, temperature and flow, throughout the production. This type of sensors, inspired by the concept of the permanent downhole gauge ( PDG ) introduced in 1963 1 , represent a fundamental technology in the monitoring and characterization of oil fields.
The DataCan downhole meters shown in Figure 1 record fundamental well parameters, such as pressure, temperature and flow, to obtain details about well performance and provide information relevant to productivity improvements. These memory meters can collect data for a few hours or for months or even years.
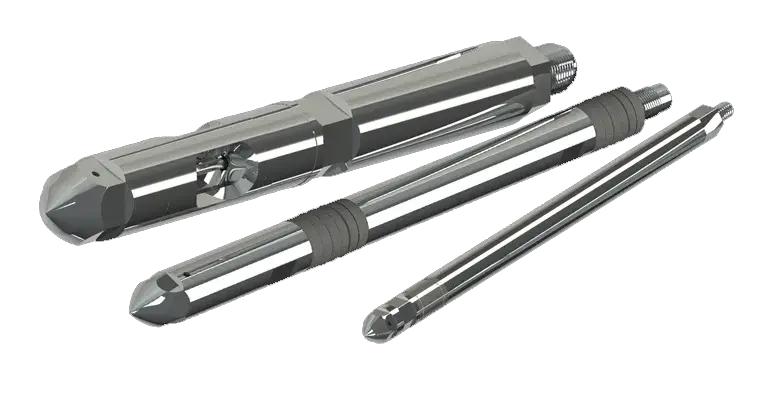
Downhole meters (Figure 2) are designed to withstand the most aggressive conditions, including high pressures and temperatures in corrosive environments. These types of meters have applications in oil, gas, and geothermal wells to determine fluid characteristics.
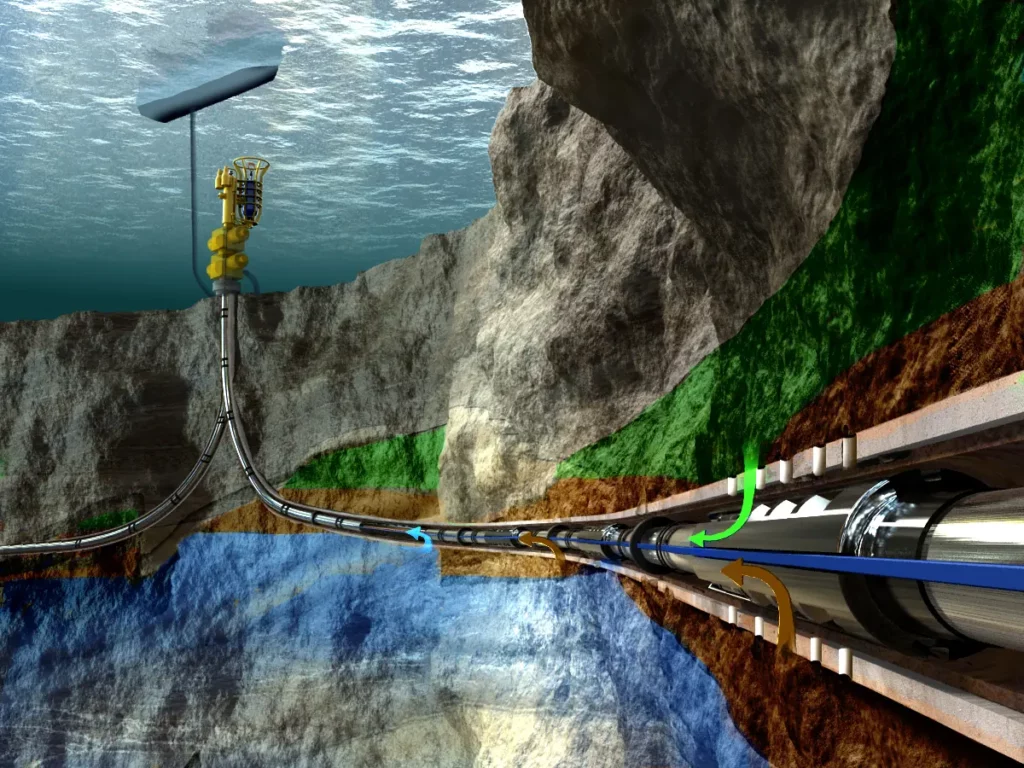
Its permanent installation allows for continuous data on reservoir performance, providing valuable information for the interpretation and analysis of well tests. In the industrial field, permanent sensors stand out for their significant contribution to the understanding and optimization of processes through the continuous collection of critical data.
Use of permanent sensors in industrial risk analysis
- Continuous monitoring of critical parameters: This type of sensors allow uninterrupted monitoring of variables such as pressure, temperature and flow in industrial environments, identifying possible deviations and risks.
- Anomaly detection: By providing real-time measurements, it facilitates the immediate identification of unwanted behaviors in industrial processes, contributing to a proactive response.
- Reservoir evaluation: In the oil sector, they are necessary when evaluating reservoirs, this is due to the constant proportion of data on well performance and facilitating informed decision making.
- Historical Data Analysis: Continuous data collection over time allows for the creation of detailed histories, ideal for developing retrospective analyzes to identify patterns, trends, and potential improvements to risk management procedures.
- Validation of risk models: The constant information provided represents a valuable source to validate and improve existing risk models, guaranteeing a more accurate and realistic evaluation.
Advantages of using permanent sensors
Improvement of industrial safety
Detecting potential threats such as unexpected pressure increases or cement sealing problems after well casing are examples of the importance of permanent sensors in industrial operations. Mainly, because these systems provide critical information for the safety of production systems and well optimization.
One of its greatest impacts occurs in the management of well casing integrity, since timely detection of pressure increases is crucial to prevent casing deterioration, oil and gas migrations, and possible gas explosions. . The constant monitoring of the well bottoms, in conjunction with these sensors, contributes significantly to the improvement of safety standards in this type of industrial operations.
Costs reduction
The implementation of sensors in the analysis of industrial risks can generate an optimization of the work team’s time, this translates into significant savings by eliminating the costs associated with on-site inspections and manual monitoring of the fluid level.
Some of these downhole measurement systems offer real-time data and allow remote monitoring and control, replacing expenses related to logistics, fuel and insurance. Additionally, improved protection of downhole equipment through reliable real-time data can avoid costly replacement processes.
For processes such as hydraulic fracturing and steam-assisted gravity drainage, where the resources used are considerable, efficient management facilitated by permanent sensors optimizes production. The way to achieve this is by eliminating peaks and dips in variables such as flow, pressure and temperature, ensuring effective use of resources and maximizing profitability.
Optimization of production and profitability
Implementing these permanent sensors also translates into significant optimization of production and profitability in operations. Faced with the costly challenges associated with operations such as drilling new wells, permanent systems function as an effective alternative with a lower cost, increasing profitability by increasing production and income in all operating wells, in a manner comparable to the development of new projects, but at a fraction of the cost.
In environments where liquidity is a challenge and staff cuts are inevitable, permanent measurement systems allow for effective reallocation of responsibilities. Real-time data allows personnel to focus on critical projects, while permanent sensors efficiently manage and monitor well performance.
This cost-effective strategy offers energy companies the ability to quickly increase their production and revenue without compromising quality and operational efficiency, which is why it is considered one of the greatest advantages of using permanent sensors.
Analysis of data from permanent sensors in industrial risk management
Although the constant collection of critical data through permanent sensors is an important factor to guarantee the mitigation of industrial risks, it is essential to correctly analyze the information obtained. This is because, based on data analysis, the necessary measures can be carried out to ensure optimal problem resolution.
Various authors have contributed by offering different aspects of data analysis from permanent downhole sensors, which can be implemented in industrial risk management. One of these was Athicanagorn (1999), who presented a methodology to carry out long-term data analysis from permanent downhole meters, covering a series of steps to achieve effective interpretation of the data 2 . These phases are:
1. Removal of outliers: Outliers are defined as observations that deviate significantly from the general trend of the data. Identifying and eliminating these is part of the filtering process, using properties both before and after these outliers. This elimination involves the application of Wavelet transformations.
2. Noise removal: The term “noise” refers to the dispersions and variations present in the general trend of the data. Like outliers, noise is removed through Wavelet transformations by nullifying the low-frequency Wavelet detail coefficient, resulting in the reduction of high-frequency noise in the data signal. In Figure 3, you can see a comparison between an original signal and its result after noise removal.
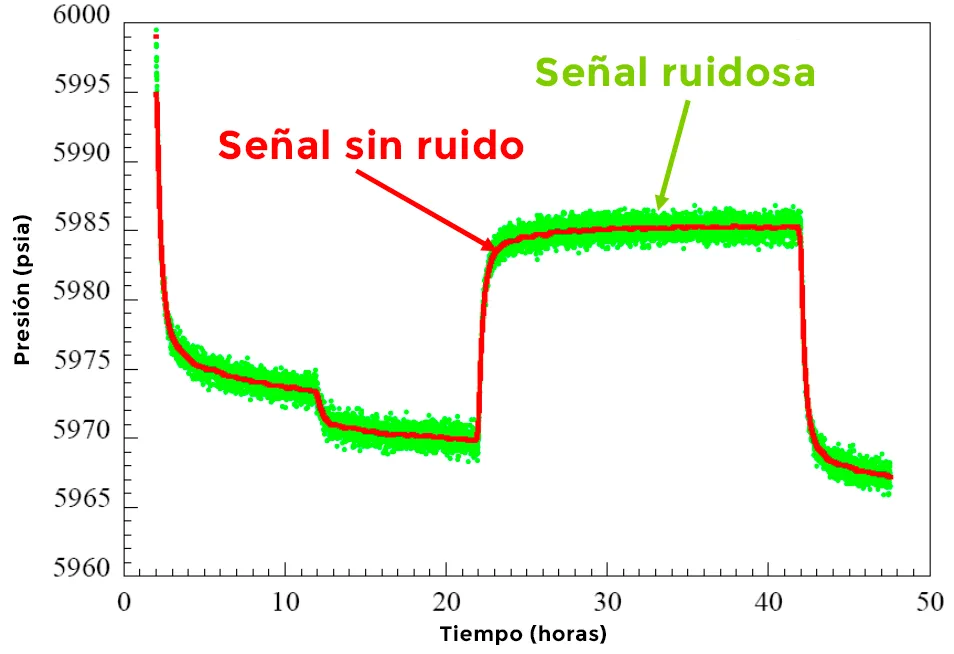
3. Identification of transients: It involves the subdivision of the data set into different periods of the variable, such as flow, these sets are known as transients. This process requires the identification of breakpoints, which mark the start and end of each transient. Identification is achieved by detecting abrupt changes in pressure data, thus indicating variations in well flow.
4. Data reduction: With the purpose of managing the large amount of data obtained by the sensors.
5. Reconstruction of the historical flow: It involves calculating missing flows using regression analysis, as it is often impossible to obtain a complete flow history 3 .
6. Filtering by behavior: This involves the identification and exclusion of data segments that deviate from the general trend of the measurements. Based on the inference of an appropriate reservoir model, this process uses the variance between the data and the modeled response as a selection criterion.
7. Data interpretation: To carry out this final phase, the application of a technique based on sliding windows is required. This methodology considers the potential variation of reservoir and fluid properties during the recovery process 3 . Finally, a non-linear regression analysis is carried out to extract the relevant conclusions.
This methodology provides an approach to optimize industrial risk management by leveraging accurate and contextualized data in strategic decision making.
Conclusions
The use of permanent sensors in industrial risk analysis can be perceived as a comprehensive strategy to optimize safety and efficiency in industrial operations. These devices not only enable continuous monitoring of critical parameters such as pressure, temperature and flow, but also allow the immediate detection of anomalies and the exhaustive evaluation of oil fields, ideal for identifying threats present in industrial processes.
Additionally, its contribution is reflected in the improvement of different organizational aspects, such as the management of well casing integrity, cost reduction and optimization of production and profitability. Demonstrating that the data provided is of great value for operational management and optimization.
It should be noted that it is necessary to carry out a correct implementation and analysis of the data obtained by the permanent sensors. Since adequate manipulation of the information obtained will end up offering a solid approach to face security and efficiency challenges in industrial environments.
References
- WA Nestlerode. The use of pressure data from permanently installed bottomhole pressure gauges (SPE paper 590). In SPE Rocky Mountain Joint Regional Meeting, Denver, Colorado, USA, 1963.
- Athicanagorn, S., Horne, RN and Kikani J. “Processing and Interpretation of Long-term Data from Permanent Downhole Pressure Gauges.” Paper presented at the SPE Annual Technical Conference and Exposition, Houston, Texas, October 1999.
- Thomas, O. (2002). THE DATA AS THE MODEL: INTERPRETING PERMANENT DOWNHOLE GAUGE DATA WITHOUT KNOWING THE RESERVOIR MODEL.