Table of Contents
Mechanical integrity through equipment inspection in the industry is not simply a technical concept, but a necessity to ensure safety, efficiency and sustainability in operations. Inspection, in collaboration with proactive maintenance practices, is important to maintain the integrity of industrial assets and contribute to operational reliability.
In the field of engineering and industrial maintenance, monitoring mechanical integrity through inspection is an alliance that must be met at all stages of the asset life cycle. This practice is not limited to being a response to existing problems; represents a continuous opportunity to evaluate and improve industrial systems. This article focuses on how asset inspection strengthens mechanical integrity, acting as a necessary tool in preventing failures and optimizing operational performance.
Mechanical integrity and its role in the industrial sector
It refers to the ability of a system or equipment to function adequately and safely, without risk of failure, malfunction or deterioration during its life cycle. It is essential to avoid damage, accidents and potential risks to people, the environment and facilities. This process must be fulfilled from design and manufacturing to installation, operation, inspection and maintenance of industrial assets.
Likewise, it plays a critical role in preventing operational interruptions and guaranteeing the continuity of industrial processes. For example, in the oil and gas industry, the mechanical integrity of pipes and static equipment is essential to maintain to prevent leaks and accidents, protecting infrastructure and the environment.
Adequate integrity management involves the identification and classification of equipment, the development of procedures and maintenance planning, the training necessary to execute the activities, inspections and tests, and the development of an effective quality assurance program. . Mechanical integrity programs must take into account equipment inspections, using established procedures generally accepted as good engineering practices.
When should equipment inspections be performed?
Industrial inspections are evaluation processes that focus on the conditions of the equipment; They aim to identify problems and take necessary measures to mitigate risks and maintain optimal and safe performance; They must have established frequencies based on factors such as: design specifications, nature of the service, changes in operational variables, results of previous evaluations, corrosion rate, corrosion monitoring systems.
Likewise, there must be an adequate inspection schedule; which must be determined mainly based on the evaluation of risks, specifications and operational variables and the operating history of each equipment, following established regulations such as the American Petroleum Institute (API) and the American Society of Mechanical Engineers (ASME) that guide the inspection, repair and maintenance work of the multiple assets that make up an industrial environment.
Key factors to ensure mechanical integrity
To establish an effective inspection program that maintains the mechanical integrity of assets, the following factors must be taken into account:
- Risk assessment and determination of criticality: These factors are determined through the identification of critical equipment and systems, through a risk analysis. Standards such as API 580-581 are useful for this analysis, considering factors such as frequency and effectiveness of previous inspections, failure history, and operational and maintenance characteristics. The objective is to optimize the resources allocated to inspection, focusing on elements with high risk and relegating those with low risk.
- Development of inspection procedures: For the optimal definition of the procedures, they must define methodologies, frequencies, acceptance criteria and the best work strategies. This documentation must follow good engineering practices that are based on equipment characteristics, manufacturer recommendations and risk assessment.
- Appropriate inspection methods: Selecting appropriate inspection techniques for each type of requirement and equipment is important for the evaluation of mechanical integrity of industrial assets. This should include visual inspections, non-destructive testing (such as ultrasound, radiography, liquid penetrants, robotic inspection, etc.), and condition monitoring.
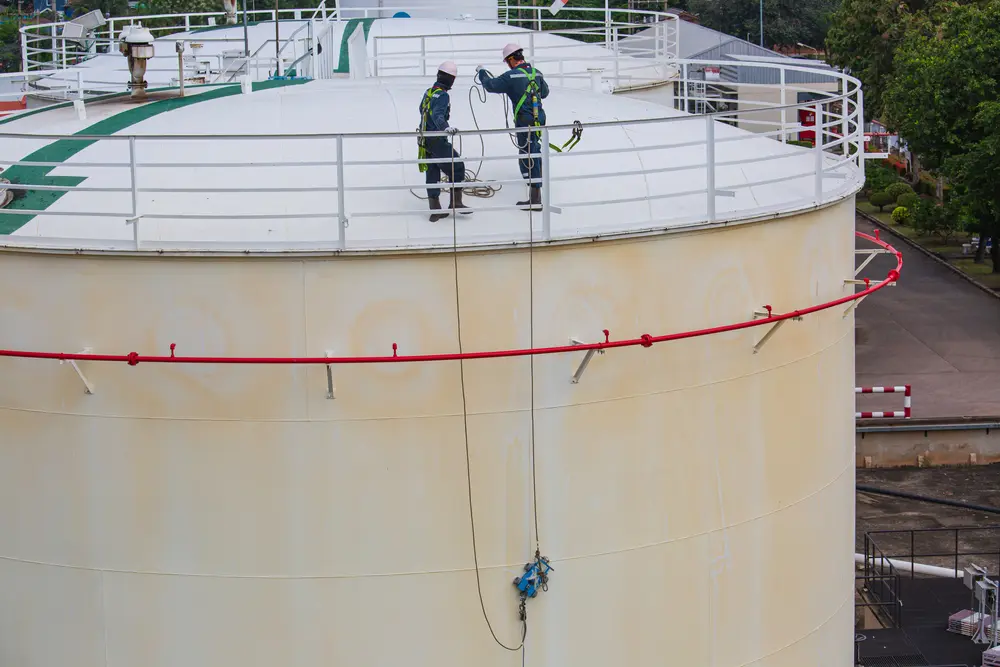
- Implementation of field inspections: Inspections according to the determined frequency, check list type or routine, intermittent or periodic inspections, must be carried out according to pre-established schedules. This step is necessary to maintain an adequate record of the findings and results of the inspections, in order to know the behavior of the evaluated element.
- Data analysis and inspection reports: Through detailed reports with all the information collected, the data can be analyzed to identify trends, predict possible failures and plan preventive maintenance that generates guarantee in the evaluations. This also includes tracking the operating history of the equipment.
- Management of findings and recommendations: It is essential to develop an action plan to address critical findings detected during inspections, including maintenance, necessary repairs or improvements to operating procedures.
- Audits and continuous improvement: Periodic audits of inspection programs are necessary to evaluate their effectiveness and make adjustments for continuous improvement of inspection processes.
Compliance with equipment inspection programs is part of the basis for maintaining the mechanical integrity of industrial assets. These programs not only prevent failures and unplanned plant shutdowns, but also contribute to safer, more efficient and profitable operation of industrial facilities.
Impact of inspections on the useful life of industrial assets
Inspections are a necessary factor within mechanical integrity management, not only ensuring the optimal and safe functioning of the systems, but also giving value and extending their operational continuity. Through inspections, detected problems are identified and addressed, thus avoiding unexpected failures.
The implementation of an inspection program must be accompanied by a detailed maintenance plan that immediately responds to the findings of the inspections, in order to maintain the mechanical integrity of industrial assets. This is a proactive approach; which allows organizations to optimize maintenance programs and fully comply with them to give their assets longer life.
The value of the experience and training of the personnel involved
Specialized training, in the context of maintaining the mechanical integrity of industrial assets, is a relevant factor; Inspection methodologies and technologies are constantly evolving, and staying up to date with these innovations guarantees the execution of effective evaluations. Training should not only understand traditional inspection techniques and recent technologies, but also understand how to interpret related regulations and standards.
The experience of the staff is equally significant. Inspectors with years of practice provide deep knowledge for the early identification of problems and the efficient application of inspection techniques. Regular practice in the field allows for a more intuitive understanding of how equipment works, how and when it can fail, and what decisions must be made, which improves the quality and results of inspections.
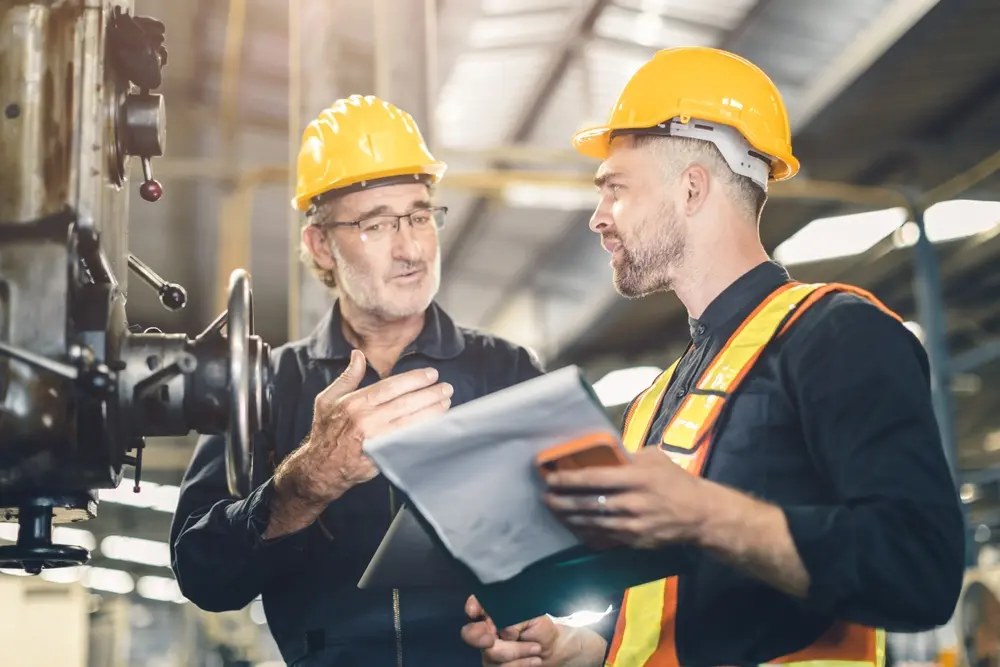
The combination of specialized training and experience of the personnel who perform the inspections provides greater guarantee of the mechanical integrity of industrial assets. This duality ensures that inspections are carried out successfully, with a deep understanding of both practical and theoretical applications, generating a safer work environment and more reliable equipment.
Conclusions
Maintaining mechanical integrity through thorough inspection of industrial equipment is a process that is integrated into all stages of the asset life cycle. This approach goes beyond simply reacting to existing problems, becoming an ongoing practice for evaluating and maintaining industrial systems. Equipment inspections reinforce mechanical integrity, being essential in preventing failures and strengthening operational performance.
An effective inspection program, based on risk assessment, together with a detailed maintenance plan, optimize the durability and efficiency of industrial equipment. The experience and training of the personnel participating in the inspections improves their quality and results, ensuring that they are carried out successfully and with a deep understanding of both the practical and theoretical applications, providing greater guarantee of the integrity of the system. or equipment evaluated.
References
Own source