In the current era, where technology and industry evolve at a dizzying pace, industrial inspection emerges as a fundamental pillar to guarantee the safety, efficiency, and sustainability of industrial operations. This discipline, which focuses on the evaluation and maintenance of equipment and structures, is crucial not only to prevent accidents and ensure the safety of workers, but also to ensure that industrial processes are as efficient as possible. With the industry facing unprecedented challenges, such as aging infrastructure and the growing demand for sustainable and efficient practices, innovations in industrial inspection become an unavoidable necessity.
The current challenges in the industry are multiple and complex. On the one hand, we are faced with aging infrastructure, where once-state-of-the-art facilities now require constant maintenance and supervision to avoid catastrophic failures. On the other hand, the need for efficiency and sustainability is driving industries to adopt greener and economically viable practices, which in turn requires innovations in inspection and maintenance methods.
In this context, technological innovations are playing a transformative role in industrial inspection. The advent of technologies such as artificial intelligence, large-scale data analytics, and automation is not only changing the way inspections are performed, but is also significantly improving their effectiveness and efficiency. These innovations enable faster and more accurate detection of potential problems, more effective maintenance planning, and ultimately greater longevity and safety of industrial assets. The adoption of these emerging technologies is not only shaping the future of industrial inspection, but is also paving the way for a safer, more efficient, and sustainable industrial future.
Evolution of industrial inspection
The history of industrial inspection is a story of constant evolution and adaptation. In its beginnings, this practice was based on visual and manual methods, where trained inspectors evaluated the integrity of equipment and structures through direct observation and the use of basic tools. This approach, although effective for its time, was limited by human subjectivity and the inability to detect flaws that were not visibly evident.
As time progressed and industrial infrastructures became more complex, these traditional methods began to prove insufficient. The need for greater precision and efficiency led to the introduction of more advanced techniques. For example, in the second half of the 20th century, methods such as non-destructive testing (NDT) became popular, which included techniques such as industrial radiography, ultrasound, and thermography. These techniques allowed inspectors to detect internal flaws and hidden problems without damaging assets.
The real disruptive change in industrial inspection, however, came with the digital revolution. The adoption of digital and automated tools marked a new era in this field. The use of advanced sensors, high-resolution cameras, and drones transformed the way inspections are carried out, allowing access to previously inaccessible areas and providing real-time data. Furthermore, the integration of artificial intelligence and machine learning has allowed the development of systems capable of analyzing large volumes of data, identifying patterns, and predicting failures before they occur.
These technological innovations have not only increased the accuracy and efficiency of inspections, but have also significantly improved worker safety by reducing the need for inspections in hazardous environments. The evolution of industrial inspection, therefore, reflects a continuous commitment to improving safety, efficiency, and sustainability in the industrial sector, adapting and taking advantage of the advantages offered by new technologies.
Innovations in industrial inspection
Industrial inspection is being revolutionized by a number of emerging technologies that are dramatically improving the way these critical tasks are performed. Among the most significant innovations are artificial intelligence (AI), machine learning, drones, and robots for remote inspections. These technologies are not only increasing the efficiency and accuracy of inspections, but are also opening up new possibilities in various industrial sectors.
Artificial intelligence and machine learning are transforming industrial inspection by enabling rapid and accurate analysis of enormous amounts of data. For example, AI algorithms can analyze images captured by cameras or drones to detect cracks, corrosion, or other anomalies in structures and machinery. This early detection capability is vital to prevent failures and ensure safety. Additionally, machine learning allows inspection systems to become smarter over time, improving their ability to identify problems as they process more data.
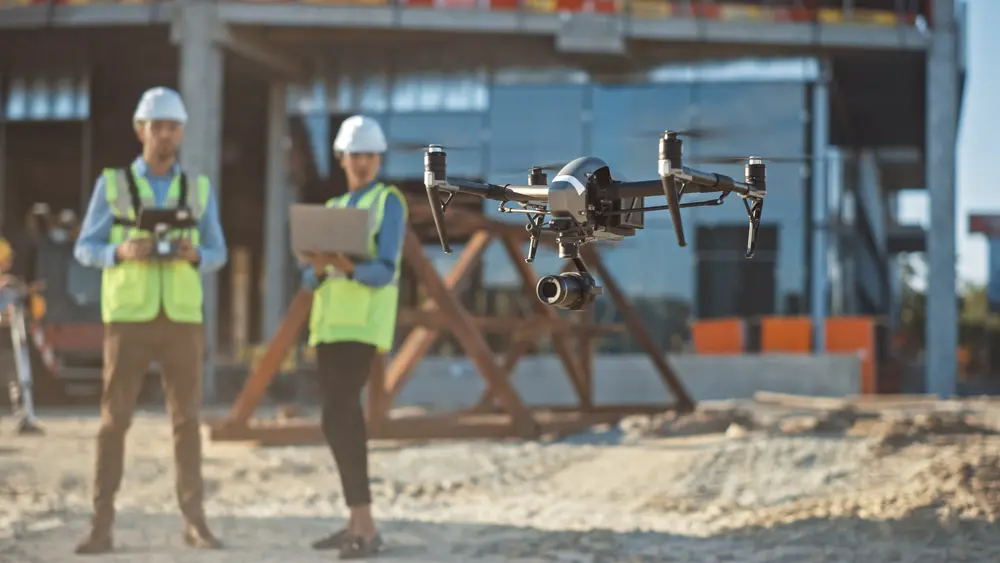
Drones and robots have revolutionized remote inspections, especially in inaccessible or dangerous environments. In sectors such as energy, mining, and construction, drones are used to inspect high-rise structures such as communications towers, wind turbines, or bridges, eliminating the need for workers to carry out risky climbs. Robots, on the other hand, are useful in confined or hazardous environments, such as underground pipelines or nuclear reactors, where they can perform detailed inspections without risking worker safety.
A notable case study is the use of drones equipped with AI technology in the oil industry. These drones perform aerial inspections of oil platforms, identifying areas that need maintenance or repair. This technology has significantly reduced the time and costs associated with traditional inspections, while improving safety by minimizing human exposure to hazardous environments.
Another example is found in the construction industry, where robots equipped with sensors and cameras are used to inspect the foundations and structures of buildings under construction. These robots can access areas that would be difficult or dangerous for humans, providing detailed information that helps prevent future structural problems.
In summary, innovations in industrial inspection are having a profound impact on multiple sectors. By adopting these emerging technologies, industries are not only improving their efficiency and accuracy in inspections, but are also advocating for a safer and more sustainable work environment.
Integrity monitoring and predictive maintenance
The integration of technology into industrial inspection has taken a significant step forward with the development of integrity monitoring and predictive maintenance. These approaches represent an evolution from reactive strategies to proactive and predictive models in industrial asset management. Real-time monitoring and predictive technologies not only improve asset integrity but also play a crucial role in optimizing maintenance processes.
Real-time monitoring involves the continuous use of sensors and other measurement devices to collect critical data about the condition of industrial equipment and structures. This real-time information allows plant managers and maintenance technicians to constantly monitor the condition of assets, resulting in early identification of any signs of deterioration or failure. This is especially valuable in industries where the failure of a critical component can have disastrous consequences, both in terms of safety and operating costs.
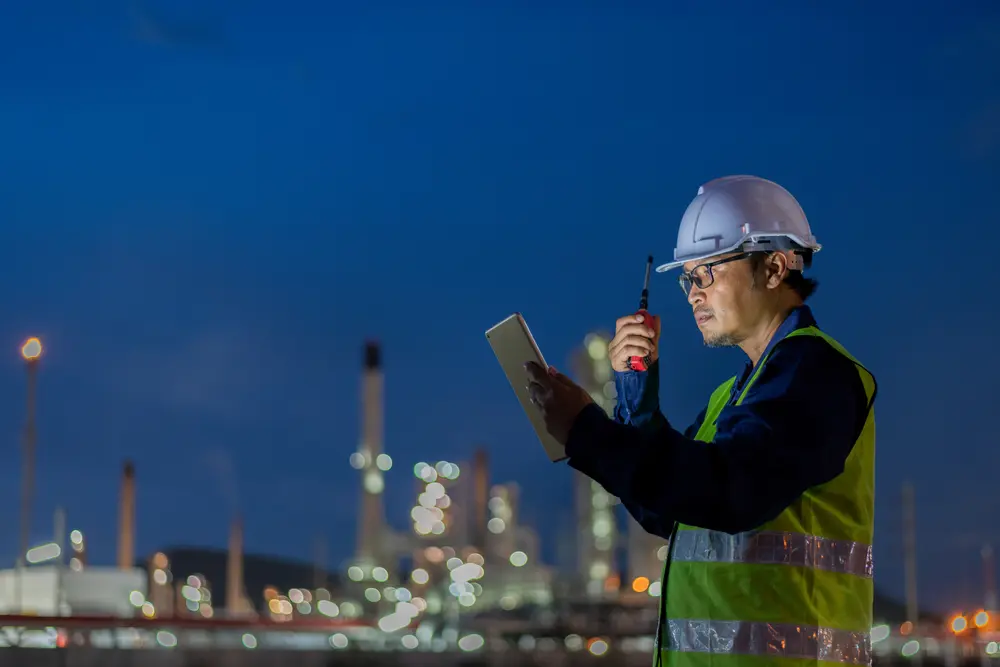
On the other hand, predictive maintenance uses this collected data to anticipate when maintenance or repair will be required, before a failure occurs. This strategy is based on the analysis of historical and real-time data through machine learning algorithms and statistical models. By predicting when problems are likely to occur, companies can plan maintenance more effectively, avoiding unexpected downtime and prolonging the life of their equipment.
Advanced sensor systems are critical in this approach. These sensors can measure a variety of parameters, such as temperature, vibration, pressure, and flow, providing detailed insight into equipment performance and condition. Automated diagnostics, which use this data to evaluate the condition of assets, are an essential tool in predictive maintenance. These diagnostics can identify patterns and trends that indicate imminent wear or failure, allowing for timely interventions.
The impact of these technologies on the industry is considerable. By adopting real-time monitoring systems and predictive maintenance strategies, companies can significantly reduce unplanned downtime, which is often costly and disruptive. Additionally, this proactive approach improves safety by reducing the likelihood of catastrophic failures and ensures greater operational efficiency by optimizing maintenance cycles. In summary, integrity monitoring and predictive maintenance not only improve the reliability and longevity of industrial assets but also reinforce the efficiency and sustainability of operations in the modern era of industry.
Advanced data management in industry
Advanced data management has become a fundamental pillar for evidence-based decision making in the industrial environment. In an era defined by the increasing complexity of operations and the proliferation of inspection and monitoring technologies, the ability to efficiently manage large volumes of data is a crucial factor in business success. This effective data management allows organizations to make more informed decisions, optimize processes, and proactively respond to emerging challenges.
Advances in data storage, processing, and analysis have been instrumental in the transformation of industrial data management. Cloud storage, for example, offers a scalable and affordable solution for handling large data sets. It facilitates remote and collaborative access, essential in the era of industrial globalization. Processing this data, now faster and more efficient thanks to advanced servers and cloud computing technologies, allows companies to quickly analyze large amounts of information. Data analytics, empowered by artificial intelligence and machine learning, provide valuable insights, identifying patterns, predicting trends and facilitating strategic decisions.
In the manufacturing sector, for example, integrating and analyzing inspection data with operational and supply chain information is vital. This amalgamation of data helps companies identify inefficiencies, anticipate maintenance problems, and adjust processes to improve product quality and production efficiency.
In the energy industry, combining sensor data on critical equipment with predictive models is equally transformative. It allows companies to plan preventive maintenance more effectively, optimize the use of energy resources and minimize operating costs.
These examples illustrate how advanced and strategic data management can be a driver of change and efficiency in modern industry. The ability to effectively integrate, process, and analyze large volumes of data not only improves operational efficiency, but also supports a more informed and strategic approach to decision making, a crucial aspect of maintaining competitiveness in a dynamic global market.
Challenges and future perspectives
As industrial inspection continues to evolve with the integration of advanced technologies, new challenges emerge that must be addressed to ensure its effectiveness and long-term sustainability. One of the most significant challenges is data security. In an environment where decision-making is increasingly based on the analysis of large volumes of data, ensuring the integrity and security of this data is crucial. Cyber threats and risks of data breaches raise serious concerns that require robust solutions in terms of cybersecurity and data protection protocols.
Another important challenge is systems integration. Modern industrial inspection involves a variety of technologies, from drones and sensors to artificial intelligence systems and data analytics platforms. The ability to seamlessly integrate these various technologies to work cohesively is essential to maximize their effectiveness. This requires not only technical compatibility, but also strategic planning and coordination between different systems and processes.
Furthermore, staff training is presented as a crucial challenge. As technologies evolve, so does the need for specialized skills and knowledge. Ongoing staff training and development are critical to ensuring workers can efficiently operate new technologies and adapt to changing industrial inspection paradigms.
Looking to the future, the prospects for industrial inspection are promising, marked by continued innovation and increasing adaptability to new challenges. Emerging technologies are expected to continue to advance, offering even more sophisticated and efficient solutions for industrial inspection and maintenance. The adoption of technologies such as augmented reality, the Internet of Things (IoT) and even more advanced artificial intelligence systems promises to take industrial inspection to new horizons of efficiency and precision.
The key to the future will be the ability of industries to adapt to these innovations, proactively addressing current and future challenges. This will involve continued investment in data security, systems integration, and staff training, thus ensuring that the industry not only keeps up with technological innovations, but also effectively leverages them to improve its operations and maintenance strategies. Adaptability and constant innovation will, therefore, be the pillars on which the future of industrial inspection will be built.
Conclusion
Throughout this article, we have explored how innovations are redefining the industrial inspection landscape. From the evolution of manual and visual techniques to the adoption of advanced technologies such as artificial intelligence, machine learning, drones, and robots, industrial inspection has undergone a significant transformation. These innovations have not only improved the accuracy and efficiency of inspections, but have also opened up new possibilities in terms of safety and accessibility.
Real-time monitoring and predictive maintenance, powered by advanced sensor systems and automated diagnostics, have improved asset integrity and reduced downtime, marking a shift toward proactive rather than reactive strategies in industrial maintenance. In parallel, advanced data management has become an essential pillar for strategic decision making, improving operational efficiency and fostering an informed approach in industrial operations.
When reflecting on the importance of these innovations, it is clear that they are fundamental to ensuring a safe, efficient, and sustainable industrial future. Facing challenges such as data security, systems integration, and staff training, the industry is on its way to making the most of these emerging technologies. Adaptability and continued innovation will be crucial to addressing current and future challenges, ensuring that the industry not only keeps up with technological advances but also uses them effectively to improve its operations and maintenance strategies.
In conclusion, innovations in industrial inspection are playing a crucial role in shaping a more resilient industrial future. By embracing these advances, the industry can hope to not only improve the efficiency and safety of its operations, but also contribute to a more sustainable and responsible future.
References
Own source