Table of Contents
- Introduction
- What is the API 610 standard for pump reliability?
- Benefits of API 610/ISO 13709 for centrifugal pumps in the petroleum, petrochemical and natural gas industries
- Update to the API 610 standard in 2021
- Significant changes from the 12th edition of the API 610 standard in relation to product reliability and maintainability
- Types of pumps according to their functionality
- Differences between API 610 and ANSI B73.1 pumps
- Conclusion
Introduction
API 610/ISO 13709, also known as the international standard for centrifugal pumps in the petroleum, petrochemical and natural gas industries, serves a fundamental purpose of ensuring safety, performance and reliability. This standard establishes rigorous requirements for the design, construction and performance of this type of pumps, with the objective of ensuring their suitability for the demanding operating environments within the oil and gas industry.
API 610 is a technical standard developed by the American Petroleum Institute (API); which establishes the minimum requirements for the design, manufacture and testing of centrifugal pumps used in the petroleum, petrochemical and natural gas industries. This standard is widely recognized and accepted in the industry due to the influence and technical experience of this organization in the oil and gas sector.
The main objective of this standard is to guarantee that they meet quality and performance standards, ensuring their durability and safety in the challenging environments found in these industries.
The standard establishes detailed requirements for key aspects of pump design and manufacturing, including materials, dimensions, tolerances and test methods. In addition, the standard also addresses aspects related to mechanical seals, lubrication systems, cooling systems and other critical components of pumps.
What is the API 610 standard for pump reliability?
API 610 is the standard specifically related to these centrifugal pumping systems. It provides engineering criteria for pump design, as well as how such equipment should be tested and what type of base it should be mounted on.
Benefits of API 610/ISO 13709 for centrifugal pumps in the petroleum, petrochemical and natural gas industries
1. Reliability: Pumps aligned with the API 610/ISO 13709 standard are conceptualized to offer exceptional reliability, guaranteeing constant pump performance even under extreme operating conditions.
2. Safety: They are designed to meet rigorous safety requirements, contributing significantly to the overall integrity of facilities in the oil, petrochemical and gas sectors.
3. Efficiency: The standard places special emphasis on the efficiency of centrifugal pumps, promoting optimized use of energy and the subsequent reduction of operating costs.
4. Compliance: Ensures adherence to regulations and industry best practices, providing quality and performance assurance.
5. Customization: Manufacturers offer the ability to customize pumps to fit specific operating requirements while maintaining compliance with established standards.
6. Performance Tests: Pumps manufactured using this standard are subjected to rigorous tests, ensuring that they meet the specified performance requirements and criteria.
7. Versatility: This equipment exhibits suitability for a wide range of applications within process services in the oil, petrochemical and gas industries, demonstrating versatility and adaptability to various operational needs.
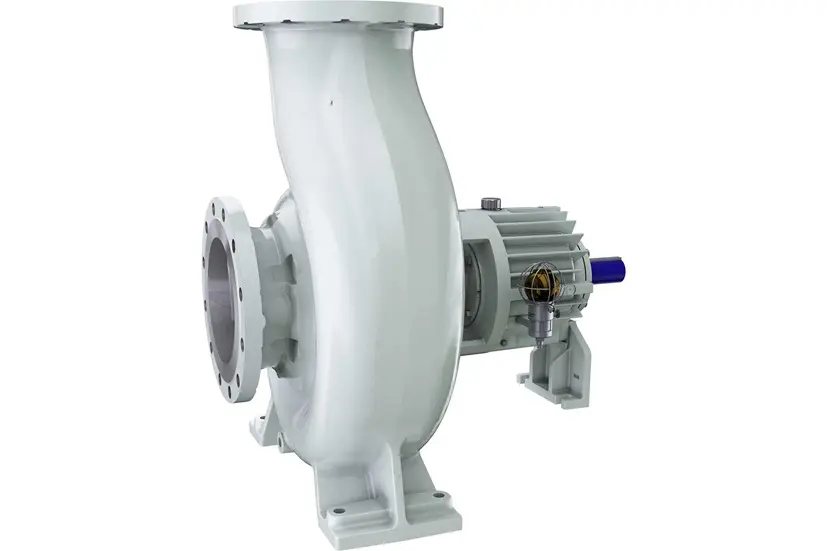
Update to the API 610 standard in 2021
Every time a new edition of global specifications, such as those established by the International Organization for Standardization (ISO) and the American Petroleum Institute (API), is introduced, confusion arises around a detailed understanding of the key changes and the reasons behind them. thereof.
This article addresses some areas of modifications that directly affect pump reliability and pump maintainability, highlighting the changes incorporated into the standard in edition 12.a, Centrifugal pumps for the petroleum, petrochemical and natural gas industries , published in January of 2021.
Documents are usually updated on a 5-year cycle. The 12th edition of API 610 was released in January 2021, approximately 11 years after the publication of the 11th edition, primarily due to key elements that required additional time to resolve. The working group began this update process in 2006, addressing the latest advances in rotating equipment, reliability issues, industry challenges, and proposed changes based on sound, proven engineering and operating practices.
Significant changes from the 12th edition of the API 610 standard in relation to product reliability and maintainability
- New: An annex (Annex O) addressing special purpose pumps has been added.
- New: API RP 691 is introduced for risk-based machinery management.
- Update: Changes have been made to basic design elements such as service life, hydraulic selection requirements, and data sheets.
- Update: New bearing selection criteria, including energy density for pipeline pumps and oil temperatures in the bearings and housing.
- Update: Improvements have been made to the unit packaging, including “shaft” protectors and base plate designs for OH pumps, as well as the location of their auxiliaries and pipe reinforcement.
- An important change is the inclusion of an annex dedicated to high energy special purpose pumps. In the 11th edition, “high energy” was defined in terms of heights per stage and power per stage. However, it was noted that this definition varied between different specialists and the decision was made to label these bombs as “special purpose”.
- A new informational annex was added to address sections on definition, selection criteria, design considerations, materials, manufacturing, and testing guidelines1.
Pumps are one of the most used machinery in process facilities and piping systems. While industry standards and practices cover the design, installation and operation of pumps, there was no general industry guidance on repair practices. In this context it is important to note that the American Petroleum Institute has published a first edition standard, API Recommended Practice (RP) 697, Pump Repair 2.
Types of pumps according to their functionality
- The F-1 turbopumps used in the Saturn V booster rocket engines are single-stage high-speed pumps operating at 5490 rpm and are designed for handling hydrogen and oxygen.
- High-pressure water injection pumps, operating at 6000 rpm and generating 500 bar (7500 psi) of pressure, are capable of generating 500 m (1600 ft) of pressure rise per stage.
- Pipeline pumps used in the ethylene industry are designed to operate at high pressure.
- High pressure boiler feedwater pumps are used to supply high pressure water in boiler systems.
- Refinery cargo pumps without spare parts, with a power of 3 MW to 4 MW (4000 HP to 5400 HP), are used for cargo pumping in refineries. Although special purpose pumps represent only about 1% of total pumps, they present significant challenges to designers and require special design considerations.
In high energy pump engineering, every aspect of the design requires careful review. This includes rotor stiffness, residual stress distribution across metal-to-metal sealing surfaces, determining deflection at critical fits, and establishing proper running clearances. It is essential to perform a structural analysis of impellers and diffusers (or volutes) and determine the adequate margin of the net positive suction head (NPSH) in order to ensure operability in pumps.
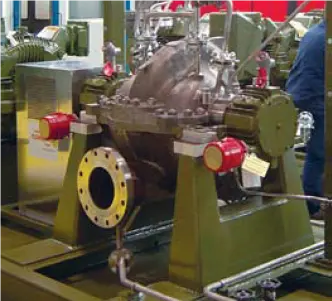
Differences between API 610 and ANSI B73.1 pumps
While ANSI standards refer to dimensional standards, the API standard refers to the pump’s construction, design, and ability to withstand high temperatures and pressures.
API 610 Pumps: This standard is specifically designed for pumps used in the oil, gas and petrochemical industries. Its focus is on pumps designed for handling hydrocarbons, corrosive fluids, as well as applications involving high temperatures and pressures.
ANSI B73.1 Pumps: Also known as ASME B73.1, this standard covers horizontal end suction centrifugal pumps designed for general purpose applications. Its main application is in industrial and commercial environments, where the handling of water, chemicals and other less rigorous fluids is required.
These fundamental differences ensure that each standard is precisely tailored to the specific demands of their respective applications, addressing particular needs in terms of corrosion resistance, extreme condition capability and fluid handling requirements, ensuring performance.
API pumps are recognized for their heavy duty capability compared to ANSI pumps. These differences are evident in the characteristics of the casings, bearing casings, anchor legs and rear cover layout, allowing them to achieve efficient pumping control and demonstrate greater efficiency and reliability in pumps in the recommended applications.
Conclusion
Adherence to API 610 is essential for pump manufacturers, as it ensures the quality and performance of their products, and provides confidence to end users of this equipment that it will operate safely and efficiently. By following the requirements of the standard, the aim is to optimize reliability in pumps, reduce the risks of failure and improve efficiency in fluid management in the petroleum, petrochemical and natural gas industries.
This standard provides precise guidelines for design, construction and performance, ensuring its adaptation to the challenging operating environments found in the oil and gas sector.
API 610, also known as “Centrifugal Pumps for the Petroleum, Petrochemical and Natural Gas Industries,” is a widely recognized standard that establishes specific requirements for reliability in centrifugal pumps used in the aforementioned industries. This standard covers various types of assets, such as horizontal, vertical and cantilever pumps.
On the other hand, the ISO 13709 standard is the international equivalent of the API 610 standard and both standards are aligned to ensure global consistency in specifications for this type of pumps.
Compliance with API 610/ISO 13709 is necessary to maintain the integrity and efficiency of critical equipment, contributing to the safety, productivity and environmental sustainability of oil, petrochemical and gas facilities.
In a constantly evolving environment, the implementation of this standard demonstrates the commitment to operational excellence and the promotion of best practices in the oil and gas industry.
References
- Shaker Heights Ohio, and R. Jones; “Online Exclusive: API 610 12th Edition Addresses Pump Reliability and Maintenance”; Hydrocarbon Processing, 01/20/2022 10:15:13, accessed November 16, 2023; https://www.hydrocarbonprocessing.com/news/2022/01/online-exclusive-api-610-12th-edition-addresses-pump-reliability-maintainability-and-more
- American Petroleum Institute, API; API Recommended Practice (RP) 697, Pump Repair ; first edition.