Table of Contents
- Uses and applications of refractory materials
- Application methods
- Quality control and evaluation tests
- Limitations and challenges
- Environmental and health challenges
- Regulations and Standards
- The new Recommended Practice RP 982
- Inspections and maintenance
- Inspection techniques used in refractory materials
- Additional considerations in inspections and maintenance
- Conclusions
In the advancement of industrial innovation, refractory materials play a primary role in the oil and gas industry . These materials, known for their resistance to extremely high temperatures and aggressive conditions, are necessary in processes that require a high degree of thermal efficiency and chemical resistance.
This article explores the uses, composition, regulations, inspections and challenges of refractories in the oil and gas industry , highlighting their importance and innovations in this field.
These materials are inorganic ceramic compounds capable of withstanding temperatures greater than 1000 °C. They are mainly composed of aluminum oxides (alumina), silicon (silica) and magnesium (magnesite), among others. They are classified into:
- Acid Refractories: Resistant to acidic environments, generally made of silica.
- Basic Refractories: Effective against bases, composed mainly of magnesite and dolomite.
- Neutral Refractories: Resistance to both acids and bases, often made of alumina or chromite.
Uses and applications of refractory materials
Refractories are essential in industrial processes such as fluidized catalytic cracking and catalytic reforming, where high temperature reactions are common. They provide thermal insulation and protection against erosion and corrosion, thus improving the efficiency and longevity of the equipment.
Additionally, refractories are applied in a wide variety of processes and environments within the oil and gas industry, mainly in furnaces and boilers, as well as in other industries where resistance to high temperatures and corrosive environments is required. Here I detail how these materials are applied in various contexts:
Lining of equipment and structures: Ovens and boilers: Refractories are used to internally line ovens and boilers, used in the refining and processing of oil and gas. Also used in reformers and reactors, these coatings protect reactors where high temperature and erosion processes such as catalytic reforming are carried out.
Protection against corrosion and wear: Specifically used in combustion and burning areas in order to ‘protect the areas where direct combustion occurs, resisting high temperatures, erosion and corrosion caused by combustion products.
Structural Support: They are used in foundations and supporting structures, in order to provide structural support that can resist heat and wear over the long term.
Maintenance and repair: Refractories are applied for quick emergency repairs, in cases of damage or wear, maintaining the structural integrity and functionality of the equipment.
Application methods
- Guniting or Shotcreting: A method where refractories are projected at high speed onto a surface to form a coating.
- Laying in the form of bricks: Using this procedure, bricks are cut and molded, then placed and joined together to form a solid covering.
- Ceramic fibers: They are distributed in the form of blankets and take the geometric shape of the material to be protected, held with special anchors (very susceptible to damage due to erosion and friction).
Quality control and evaluation tests
Refractory installations require periodic evaluation tests in order to detect any early signs of wear, cracks or irregularities in the refractory structure, thus preventing the progression of possible damage. During assembly and installation (see figure 1), various aspects must be considered such as verification of structural integrity, identification of areas prone to wear, measurement of lining thickness and evaluation of possible changes in refractory properties.
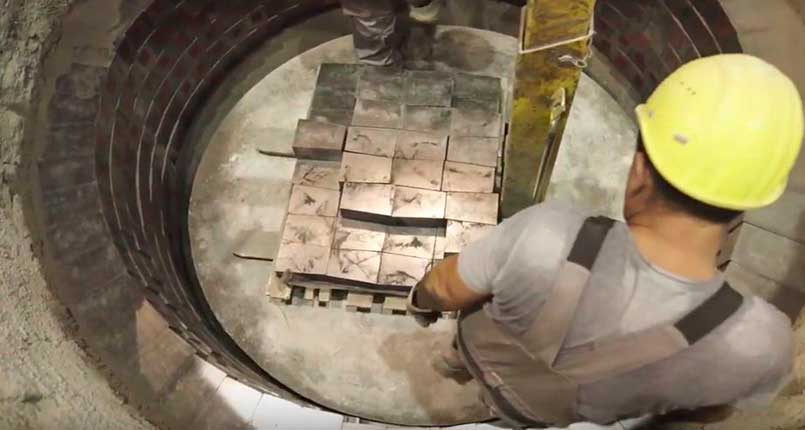
Below are some evaluation techniques:
These tests are carried out in order to evaluate the resistance and durability of the applied refractories; which are necessary to ensure efficiency in extreme conditions, such as in the oil and gas industry.. They allow you to evaluate how refractories will withstand thermal, mechanical and chemical stress during use. The types of tests, methods and equipment used are detailed below:
Thermal resistance tests: Thermal Shock Tests: Used to evaluate the refractory’s ability to withstand rapid changes in temperature, it consists of heating and cooling the material repeatedly and observing the appearance of cracks or failures. Likewise, High Temperature Creep tests are carried out, which allow measuring the deformation of the refractory under constant load at high temperatures for a long time. Equipment used: High temperature ovens, thermal shock chambers, load testing presses.
Mechanical Resistance Tests: Compression and Flexion Tests to determine the resistance of the refractory to mechanical loads, measuring the force necessary to break or deform a sample. Abrasion Tests Through this test the resistance of the material to erosion caused by moving particles is evaluated. Equipment used: Universal testing machines, abrasion testing equipment.
Chemical resistance tests: Corrosion Analysis, for the application of this method, refractories are exposed to corrosive chemical agents to evaluate mass loss or structural changes. Equipment used: Autoclaves, gas exposure chambers, high precision analytical balances.
Durability tests: Accelerated aging tests are available, for which the effect of time and environmental conditions that interact with the refractories are simulated to predict their useful life; and porosity and density tests to analyze the porous structure of the material, which can influence its strength and durability. Equipment used: Aging ovens, porosimeters, densimeters.
Additional Methods and Techniques: Electron Microscopy: To examine microstructural changes after testing and X-ray Spectroscopy to analyze chemical composition and changes after exposure to high temperatures or chemical agents.
Quality control and certification: Rigorous documentation; Each test is documented in detail to ensure traceability and compliance with industry standards. Refractory materials must comply with international certifications and standards such as ASTM or ISO.
Refractories are applied in multiple forms and methods, depending on the specific use and industry needs. Their correct selection and application are essential to guarantee the efficiency, safety and durability of the equipment and processes in which they are used. Strength and durability testing of refractory materials is complex and requires specialized equipment and advanced methods. These tests are necessary to ensure that refractories operate safely and efficiently in applications within the oil and gas industry.
Limitations and challenges
Despite their advantages, refractories face challenges such as:
- Wear and corrosion: Continued exposure to high temperatures and chemical reagents can degrade refractories.
- Thermal shock: Sudden changes in temperature can cause cracks.
- Sustainability: The production of refractories has a significant environmental impact, driving the search for more ecological materials.
Environmental and health challenges
The manufacturing of refractory materials (see video) presents significant challenges in terms of health and the environment, both in production processes and in their application in various industries. In refractory factories, permanent contamination with dust can be a cause of health risk. In addition to technical measures, a periodic medical check-up is essential.
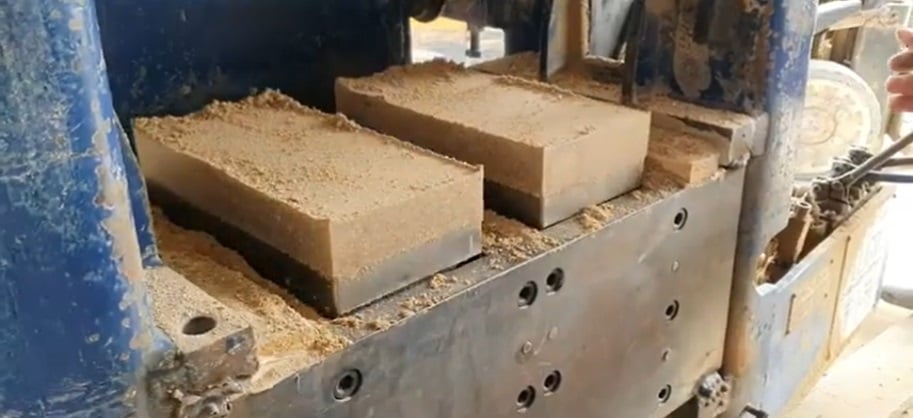
video about the refractory manufacturing process, Courtesy of Industrial Manufacturing.
These challenges include:
Manufacture of refractories
- Gas and dust emissions: The manufacture of refractory materials can generate fine dust and harmful gases, such as sulfur and nitrogen dioxides, affecting air quality.
- Energy consumption and CO 2 emissions: The production of refractories is energy intensive, contributing to a larger carbon footprint.
- Use and extraction of raw materials: Obtaining raw materials for the manufacture of these materials may involve mining practices with negative impacts on the environment.
- Worker health: Exposure to dusts and chemicals during production can cause respiratory problems and other health conditions.
Use of refractories
- End-of-life waste management: Used refractories can contain toxic substances, posing challenges for disposal or recycling.
- Exposure to harmful substances during maintenance and repair: During maintenance of refractory-lined equipment, workers may be exposed to hazardous dusts and fibers.
Strategies and solutions
- Development of more ecological materials: Research and development of refractories with lower environmental and health impacts, such as materials with low CO 2 emissions or with less dust generation.
- Improvement in the energy efficiency of production: Implementation of more efficient technologies and use of renewable energy in the manufacture of refractory materials.
- Recycling and reuse of refractories: Promote the circular economy by recycling refractory materials, thus reducing the need for new raw materials and the generation of waste.
- Rigorous emissions control and improvements in occupational safety: Implementation of emissions control systems and improvement of occupational health and safety standards.
- Compliance with environmental and labor regulations: Ensure that both manufacturing and use comply with national and international regulations regarding environmental protection and workplace safety.
Regulations and Standards
The production and use of refractories in the oil and gas industry are regulated by international standards, such as ISO and ASTM, which guarantee the safety, quality and performance of these materials. It should be noted that the American Petroleum Institute ( API ) has just announced the publication of Recommended Practice (RP) 982, Inspection and Evaluation of Refractory Linings in its first edition.
ISO regulations for refractories
- ISO 10081-1: Classification of dense and insulating refractory materials: This standard classifies dense and insulating refractories according to their chemical composition and physical characteristics. It is essential to identify and select the correct type of refractory material for different applications.
- ISO 1927-5: Preparation and testing of samples of non-formed refractory materials: Defines methods for preparing and testing samples of non-formed refractory materials. It includes guidelines on mixing, forming, drying and cooking samples, which is important to ensure product uniformity and quality.
ASTM standards for refractories
- ASTM C71: Terminology of Refractory Materials: Establishes the definitions and technical terms related to refractories. This standard is necessary to ensure uniform understanding and communication within the industry.
- ASTM C155: Classification of Refractory Silica Bricks: Classifies refractory silica bricks based on their silica content and physical characteristics. It is essential for the proper selection of materials in applications that require high resistance to temperature and corrosive environments.
- ASTM C20: Appearance and Apparent Density Testing of Porous Refractory Materials: Describes methods for determining the appearance and apparent density of porous refractory materials. These factors are important to predict the behavior of the material under service conditions.
The new Recommended Practice RP 982
The first edition, October 2023API RP 982 – Inspection and evaluation of refractory linings1,(Figure 2), has just been released marking an important milestone in the oil and natural gas industry, providing comprehensive and standardized guidelines for the installation, inspection and repair of refractory linings in general-purpose equipment in refineries. This standard’s main objective is to improve the reliability of equipment, optimize operational efficiency, increase personnel safety and ensure the integrity of processes in the industry.
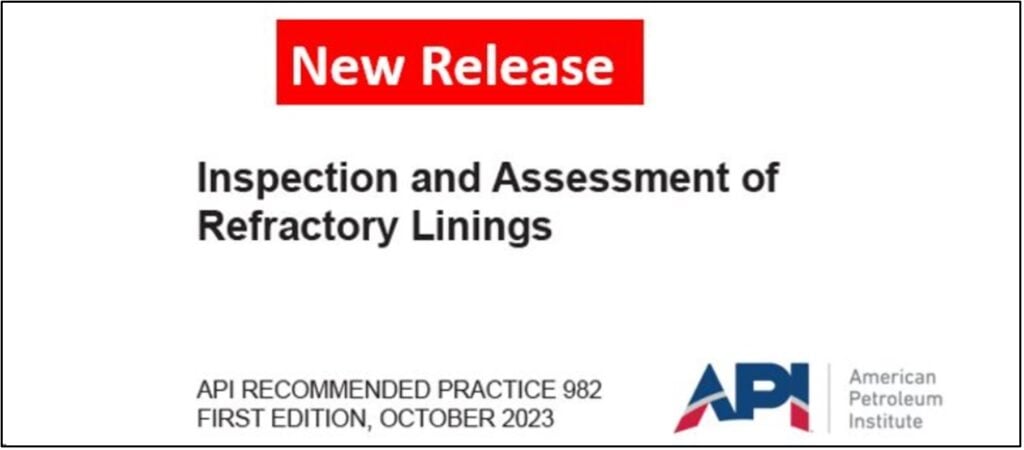
Despite the existence of numerous API standards addressing refractory inspection methods and inspector qualifications, there has been a lack of clarity as to what constitutes proper refractory inspection. RP 982 fills this critical gap, offering clear guidelines on what equipment needs to be inspected, the aspects to consider during an inspection, the appropriate tools to carry it out, and the skills required for refractory inspectors.
The scope of the RP 982 is broad, covering a variety of refinery equipment such as fluid solids units, fluid catalytic cracking units, reforming units, direct fired heaters, incinerators, sulfur recovery units and more. These refractory linings are essential to provide thermal protection, improve energy retention and process efficiency, resist abrasion and corrosion, and ensure personnel safety.
A highlight of their focus on direct-fired furnaces, which are essential in the industry for heating hydrocarbons in high-temperature processes. Effective evaluation of these liners is crucial to maximizing the productivity and durability of these furnaces.
Adopting this practice allows organizations to improve furnace performance, reduce energy consumption, and reduce downtime, making it easier to make informed decisions about lining condition and the need for repairs.
With the publication of RP 982, API will introduce a new certification within its Individual Certification Program (ICP) in the summer of 2024, aimed at certifying personnel specialized in the inspection of refractory linings. This new regulation complements other API certifications and standards, such as API 936, API 975 and API 976, collectively improving the quality and reliability of refractory installations in the industry.
Inspections and maintenance
Inspections and maintenance of refractory materials are essential aspects to ensure their efficient and safe operation, especially in the oil and gas industry, where they are exposed to extreme conditions (see figure 3).
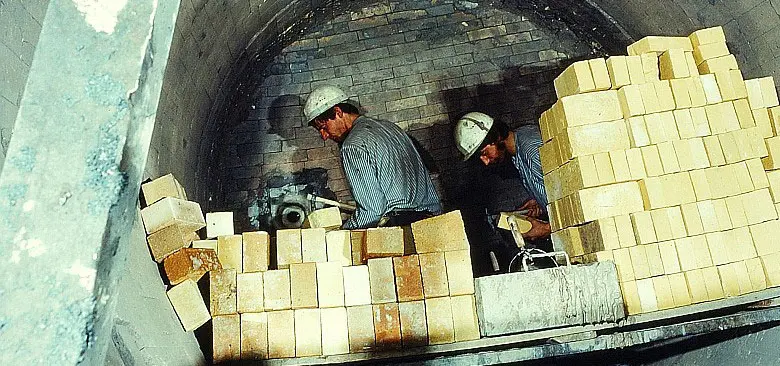
Inspection techniques used in refractory materials
Visual Inspections
- Objective and procedure: This technique involves a detailed examination of refractory surfaces to identify visible signs of deterioration, such as cracks, surface wear, material detachment, and color changes that may indicate overheating or chemical reactions.
- Tools used: Flashlights, magnifying glasses, high-resolution cameras and drones for hard-to-reach areas.
- Importance: Visual inspections are often the first step in the inspection process, as they can quickly reveal problems that require immediate attention.
Thermography
- Background: Thermography uses thermographic cameras to capture and analyze temperature variations on the surface of the refractory.
- Applications: This technique is particularly useful for identifying areas of damaged insulation, hot spots, and cold spots, which may indicate problems such as loss of refractory material, deposit buildup, or insulation system failure.
- Advantages: Thermography is a non-invasive and non-destructive technique that allows quick and real-time inspections.
Ultrasound
- Method: Ultrasound inspection uses high-frequency sound waves that are transmitted through the refractory. The reflected waves are analyzed to detect internal discontinuities.
- Uses: It is effective for detecting internal cracks, cavities, delaminations and for measuring the thickness of refractory linings. Mainly, to detect damage to the protective refractories of metal structures.
- Equipment needed: An ultrasonic transducer and a data display device are used. Often, a couplant, such as a gel, is necessary to facilitate the transmission of sound waves.
Additional considerations in inspections and maintenance
- Frequency of inspections: Depends on the type of installation, the intensity of use and operating conditions.
- Staff training: Inspectors must be adequately trained and certified, especially in more advanced techniques such as thermography and ultrasound.
- Maintenance Planning: Based on the results of the inspections, preventive and corrective maintenance should be planned to address any identified issues.
- Documentation and monitoring: Maintain detailed records of inspections and maintenance actions to ensure traceability and assist in future inspections.
Conclusions
This article highlights the importance of refractory materials in the oil and gas industry, emphasizing their resistance to extreme conditions and their application in equipment coating, thermal insulation and corrosion protection. The application methods and the importance of quality control and compliance with international regulations are detailed, including the new RP 982 of the American Petroleum Institute.
Despite facing challenges such as wear, thermal shock and environmental concerns, solutions such as the development of green materials and energy efficiency are proposed. The importance of regular inspections and maintenance for efficient and safe operation is also highlighted. In conclusion, refractories are essential for efficiency and safety in the industry, with innovation and regulatory compliance, guaranteeing their future relevance.
Sources
- American Petroleum Institute. (2023, November 2). API Releases Standard for the Inspection and Assessment of Refractory Linings . Retrieved November 7, 2023, from https://inspectioneering.com/news/2023-11-02/10828/api-releases-standard-for-the-inspection-and-assessment-of-refractory-linings