Introducción
El mantenimiento industrial ha evolucionado significativamente en las últimas décadas, pasando de enfoques reactivos y de reparaciones y sustituciones cíclicas a un modelo más proactivo, basado en los avances del Mantenimiento Centrado en Confiabilidad (RCM) y en la recolección y análisis de datos. Este nuevo enfoque ha sido impulsado por el acelerado avance de las tecnologías digitales y la Industria 4.0 y en conjunto buscan optimizar los procesos de mantenimiento para mejorar la seguridad, reducir los costos y aumentar la eficiencia operativa.
¿Qué es el mantenimiento industrial inteligente?
El Mantenimiento Inteligente se define como “un sistema que utiliza análisis de datos y herramientas de apoyo a la toma de decisiones para predecir y prevenir posibles fallas de las máquinas1. Los recientes avances en tecnología de la información, computadoras y electrónica han facilitado el diseño y la implementación de dichos sistemas. Los elementos clave de investigación de los sistemas de mantenimiento inteligente consisten en:
- Transformación de datos a información al conocimiento y sincronización de las decisiones con sistemas remotos.
- Algoritmos de pronóstico inteligentes e integrados para evaluar la degradación y predecir el rendimiento en el futuro.
- Plataformas de software y hardware para ejecutar modelos en línea.
- Servicios de productos integrados e información sobre el ciclo de vida para diseños de productos de circuito cerrado.
El concepto es más amplio, por lo que este artículo abarcará ambos enfoques.
Definimos el mantenimiento industrial inteligente como aquel que toma mayor provecho del entendimiento de la lógica del RCM y de los adelantos tecnológicos que la complementan, hasta llagar hoy día a los beneficios del uso de la inteligencia artificial.
Es conveniente comenzar revisando cómo el RCM muestra la nueva lógica para ver el mantenimiento. En otros artículos se ha tratado el tema de la importancia del entendimiento de los seis Patrones de Falla de RCM para poder diseñar las políticas adecuadas de manejo de los modos de falla de los activos. En resumen, estos patrones de falla, mencionando que estos concluyen en tres aspectos de suma importancia:
1. Que alrededor de 70% de la probabilidad condicional de fallas de equipos está relacionada con la “Mortalidad Infantil”. Y las formas como esta alta probabilidad de fallas pueden ser prevenidas que se convierta en fallas es mediante dos políticas muy claras. Una, es cuidando todos los aspectos relacionados con el diseño, materiales e instalación o ensamble de los componentes.
Es importante utilizar las partes originales (o sustitutas de igual calidad) y vigilar el cumplimiento de los procedimientos estrictos de manejo y armado de partes (secuencia, ajustes, torque, holguras, desalineación remanente, entre otras) con personal debidamente capacitados y con herramientas y ambiente de trabajo adecuados. La segunda forma de evitar la mortalidad infantil es evitar el sobre mantenimiento. Esto es, evitar realizar mantenimientos a frecuencias innecesarias (relacionado con el punto 3) y tratar de ser lo menos invasivo posible durante los mantenimientos.
2. Alrededor de un 11% de las fallas responde a una probabilidad condicional de fallas relacionada a “Desgaste” o vida útil conocida. Esto significa que alrededor de este porcentaje deberían estar planteadas las tareas de servicio o sustitución cíclicos.
3. El 89% de las fallas responden a una probabilidad condicional de fallas aleatorias, por lo que no se benefician mucho de tareas cíclicas de servicio o sustitución, y es donde el mayor beneficio se obtiene del mantenimiento predictivo o mantenimiento basado en condición.
Una estrategia que utiliza tecnologías avanzadas para monitorear continuamente el estado de los equipos industriales y predecir cuándo es necesario realizar una intervención de mantenimiento. A diferencia del mantenimiento cíclico descrito en el punto anterior, el mantenimiento por condición se activa únicamente cuando los datos indican que una falla es inminente.
Al analizar el Árbol de Decisión de RCM podemos observar que privilegia el mantenimiento por condición y esto va totalmente en línea con lo expresado en el punto 3 anterior. Pero también es claro en este árbol que debe valer la pena realizar este tipo de mantenimiento, el cual podría ser costoso. Claro que también coloca el condicionante de si “vale la pena” realizar cualquier otro tipo de mantenimiento: reparación o sustitución cíclica, combinación de tareas o búsqueda de fallas (para modos de falla ocultos). Si ninguno de estos vale la pena, aunque sean técnicamente factibles, la política adecuada será “Operar hasta la Falla (RTF)”, aunque aclara que “Podría ser deseable un cambio”.
Componentes clave del mantenimiento industrial inteligente
Consideramos mantenimiento inteligente todo aquello que nos apoye en la reducción del tiempo de inactividad, la optimización de costos, mayor confiabilidad de los equipos, mejora de la seguridad, aumento de la vida útil de los equipos y mayor eficiencia energética. Para alcanzar estos objetivos, el mantenimiento inteligente debe disponer de los siguientes componentes:
- Evitar ser afectados por la mortalidad infantil: Cuidar de realizar los mantenimientos de la mejor manera posible, evitando que tengamos que ponerlos en operación con un rosario entre nuestras manos.
- Evitarlos sobre mantenimientos, tanto en frecuencia como es la intensidad invasiva sobre los equipos. En otras palabras, “dejar quieto lo que está quieto”.
- Privilegiar el mantenimiento por condición o “Mantenimiento industrial predictivo” sobre cualquier otra política, aunque siempre será requerida su justificación costo-riesgo-beneficio. Dentro de este mantenimiento encontraremos distintos dispositivos de monitoreo de condición, con los cuales realizaremos “Análisis de tendencias”.
- Seleccionar los dispositivos adecuados de condición: Un estudio concienzudo de los intervalos y curvas P-F nos brindará información valiosa de cómo seleccionar los dispositivos adecuados de condición. Por ejemplo, los rodillos guía de una cinta transportadora o los motores eléctricos de baja criticidad, probablemente justificarán una cámara termográfica para captar incremento de la temperatura de sus rodamientos, fenómeno que se encuentra a la mitad de la curva P-F.
Mientras que los rodamientos de un equipo crítico seguramente justificarán el monitoreo con ultrasonido, análisis de lubricante o vibración, para detectar defectos más hacia el inicio de la curva P-F.
- Dispositivos de monitoreo: En cuanto al monitoreo de condición, deben localizarse los tipos adecuados según el activo analizado. Atado a esto encontraremos múltiples herramientas en el mercado donde, afortunadamente, estas han bajado considerablemente de precio y se han hecho más eficientes, como el caso de los Sensores IoT, que recolectan datos en tiempo real sobre el estado de los equipos, como vibraciones, temperatura, presión y consumo de energía. Una excelente guía para seleccionar las técnicas y herramientas para el monitoreo de condición lo ofrece el libro de RCMII de John Moubray2 en su Anexo 4.
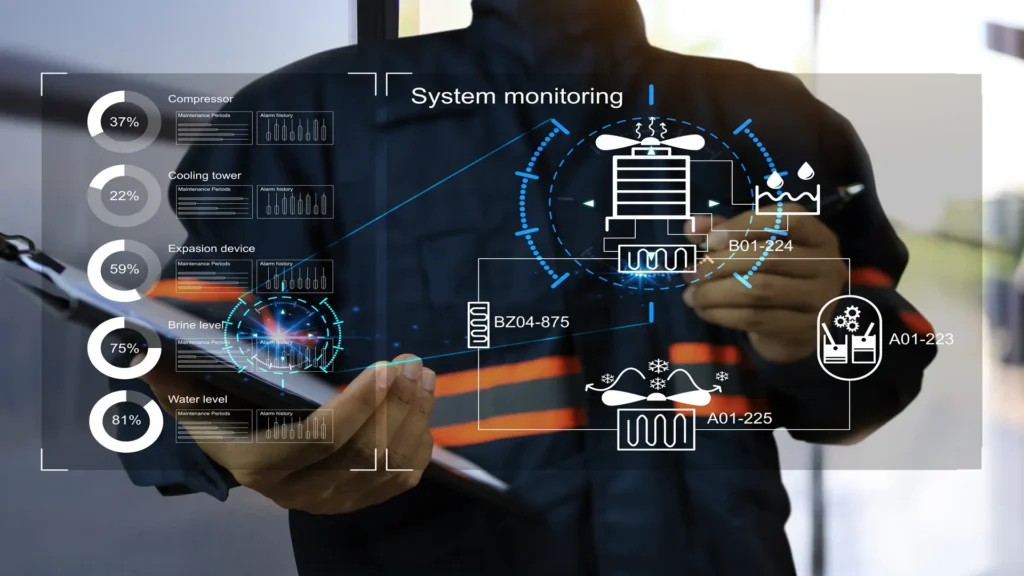
- Operar la falla: Será la política adecuada para aquellos modos de falla donde no vale la pena realizar ningún esfuerzo preventivo (incluidos reparación o sustitución cíclicos, inspección, monitoreo de condición o búsqueda de fallas).
- Apoyarse en la inteligencia artificial: Una forma de apoyarse en IA es que esta procesa y analiza los datos recopilados por sensores, mediante algoritmos de inteligencia artificial y machine learning para identificar patrones y detectar anomalías y su adecuado diagnóstico.
- Plataformas de gestión: Como las CMMS (tipo SAP-PM o Máximo) o los APM (tipo Meridium) que centralizan la información y permiten a los técnicos y gestores visualizar el estado de los equipos, generar alertas, planificar las intervenciones de mantenimiento, llevar indicadores y apoyarse con herramientas de análisis de fallas, entre otras.
- Datos como elemento central del mantenimiento: Datos que primero se recopilan del equipo a través de IoT y luego se analizan para permitir que el mantenimiento predictivo reaccione rápidamente y tome las decisiones correctas. Esto busca optimizar las intervenciones de los técnicos y reducir el tiempo de inactividad del equipo.
Conclusiones
El mantenimiento industrial inteligente representa la complementación entre la selección de políticas adecuadas para evitar fallas, plataformas de data, gestión, indicadores y análisis adecuadas unidos a una revolución que se encuentra en marcha y no se detendrá en la forma en que las empresas gestionan sus activos.
Las organizaciones y empresas mediante el uso de las tecnologías digitales, inteligencia artificial y machine learning pueden aumentar la eficiencia, reducir costos y mejorar la fiabilidad de sus operaciones. A medida que la industria continúa evolucionando, el mantenimiento inteligente se convertirá en un componente esencial para garantizar la competitividad en el mercado global.
Referencias
- https://en.wikipedia.org/wiki/Predictive_maintenance
- John Moubray; «RCM2 Mantenimiento Centrado en Confiabilidad»