Los Ensayos No Destructivos (END) son una disciplina de gran aporte a la integridad de los materiales y un factor primordial en la gestión de activos en diferentes sectores industriales, tales la construcción, petróleo y gas, generación de energía, aeronáutica y la manufactura. Los END permiten la inspección, monitoreo y evaluación de materiales, componentes o ensamblajes sin causar daño, garantizando su continuo funcionamiento. Entre los materiales frecuentemente probados, el acero al carbono y el acero inoxidable se destacan por su uso generalizado y las bondades que cada uno ofrece.
Aleaciones con alto contenido de níquel y con base en cobre comparten similitudes con el acero inoxidable austenítico, tales como: Apariencia de una superficie cercanamente pulida, buena resistencia para varios escenarios de corrosión, buena conductividad eléctrica, entre otros, por lo que, al destacar las características del acero inoxidable austenítico en este artículo, estas consideraciones también aplican para las aleaciones con alto contenido de níquel y aleaciones de cobre.
Este artículo proporciona un análisis comparativo de las pruebas no destructivas en acero al carbono vs. acero inoxidable, enfocándose en las técnicas, desafíos y mejores prácticas asociadas con cada uno.
Diferencias entre acero al carbono e inoxidable
Antes de profundizar en los detalles de los END acero al carbono vs. acero inoxidable, es crucial entender las diferencias fundamentales entre el acero al carbono y el acero inoxidable.
Acero al carbono: El acero al carbono es conocido por su resistencia, dureza y asequibilidad, el cual resulta de una combinación de dos elementos principales, hierro y carbono. Otros elementos están presentes en cantidades demasiado pequeñas para afectar sus propiedades y necesarios para su producción, tales como silicio y manganeso1. El acero al carbono tiende a ser susceptible a la corrosión para ciertos escenarios, lo que puede comprometer su integridad con el tiempo en ambientes agresivos.
Acero inoxidable: En contraste, el acero inoxidable contiene una cantidad significativa de cromo, que forma una capa pasiva de óxido de cromo en la superficie, evitando la corrosión. Esto hace que el acero inoxidable sea ideal para aplicaciones que requieren tanto resistencia mecánica como a la oxidación y corrosión en diferentes entornos agresivos. Sin embargo, su costo es más alto y el manejo de estos materiales en la construcción de sistemas de tubería, equipos y estructuras, requieren de mayores consideraciones para garantizar su integridad.
Métodos y técnicas no destructivas
Diferentes métodos y técnicas de END se utilizan comúnmente para evaluar la integridad tanto del acero al carbono como del acero inoxidable. La elección de la técnica para acero al carbono vs. acero inoxidable, a menudo depende de las propiedades específicas del material y la naturaleza de los defectos que se están inspeccionando. Es importante considerar las diferentes etapas de procesamiento de los materiales y las condiciones del servicio a la que está expuesto, esto con el objeto de definir acertadamente el tipo de falla a encontrar y con ello el método END y la técnica dentro de esta para su detección.
Inspección Visual (VT)
- Acero al carbono: La inspección visual es sencilla debido a las características superficiales del material. Problemas comunes como corrosión, grietas e irregularidades superficiales pueden detectarse fácilmente.
- Acero inoxidable: Aunque la inspección visual también es efectiva en este tipo de material, la superficie reflectante del acero inoxidable puede a veces dificultar la detección de los defectos. Puede ser necesario un nivel de iluminación y preparación de la superficie apropiado para la inspección del componente.
Inspección Ultrasónica (UT)
- Acero al carbono: Es altamente efectivo para detectar defectos internos como inclusiones, vacíos y grietas. Igualmente, es muy efectivo para la evaluación de corrosión mediante medición de espesores por la técnica de pulso eco o mediante técnicas más avanzadas como mapeo de corrosión con Ultrasonido por Arreglo de Fases (PAUT). Las propiedades acústicas del acero al carbono permiten una transmisión clara de las ondas ultrasónicas.
- Acero inoxidable: La estructura de grano grueso típica del acero inoxidable puede causar una mayor atenuación de las ondas ultrasónicas, requiriendo equipos y técnicas más sofisticadas para obtener resultados precisos. La inspección de soldaduras de acero inoxidable austenítico es un reto complejo que requiere de técnicas y procedimientos especiales.
Inspección con Partículas Magnéticas (MT)
- Acero al carbono: Siendo ferromagnético, el acero al carbono es adecuado para MT. Esta técnica puede detectar eficazmente discontinuidades superficiales y cercanas a la superficie.
- Acero inoxidable: La mayoría de los aceros inoxidables de uso industrial son austeníticos y no magnéticos, lo que hace que MT sea inefectivo. Sin embargo, para los grados magnéticos de acero inoxidable (martensíticos y ferriticos) MT aún puede ser aplicable.
Inspección Radiográfica (RT)
- Acero al carbono: Este método es efectivo para identificar defectos internos como vacíos, inclusiones y grietas. El contraste en las imágenes radiográficas generalmente es claro debido a la densidad del material.
- Acero inoxidable: Puede ser utilizado de manera igualmente efectiva en la evaluación de diferentes componentes fabricados con este material. Sin embargo, hay que considerar que este tipo de materiales es comúnmente utilizado en usos críticos, por lo que su aplicación en ocasiones tiende a ser más estricto, requiriendo medios de registro de mayor resolución (películas más lentas por ejemplo) y mayores tiempos de exposición lo que puede aumentar las preocupaciones de seguridad y los costos de inspección.
Inspección con Corrientes de Eddy (ECT)
- Acero al carbono: Es difícil de aplicar en este material, al igual que en los aceros de baja aleación por la baja conductividad que presentan estos materiales. Sin embargo, una variante de esta técnica conocida como Corrientes Eddy Pulsadas (PEC) o su variante mejorada de Matriz Corrientes Eddy Pulsadas (PECA), es efectiva en la detección de corrosión bajo aislamiento térmico y fireproofing (CUI y CUF).
- Acero inoxidable: La mayor conductividad eléctrica del acero inoxidable austenítico en comparación con el acero al carbono, hace que esta pueda ser aplicada en la inspección de materiales fabricados con este material y otros con características de alta conductividad (aleaciones de alto contenido de níquel y aleaciones de cobre). Los aceros inoxidables, martensíticos y ferríticos poseen una baja conductividad, por lo que son difíciles de inspeccionar con ECT.
Inspección con Líquidos Penetrantes (PT)
- Acero al carbono: Es efectivo en la detección de defectos que abren a la superficie, tal es el caso de grietas, siendo un requisito indispensable que el material no sea poroso por la alta retención y la dificultad para la remoción del penetrante. El proceso es sencillo y rentable.
- Acero inoxidable: Este ensayo es igualmente efectivo para el acero inoxidable, sin afectación en cuanto a las propiedades electromagnéticas, condición de la superficie, estructura de grano, entre otros. Sin embargo, hay que tener en cuenta que el contenido de haluros (cloruros y fluoruros) sebe ser muy bajo al aplicarlo en aceros inoxidables austeníticos. Este requerimiento igual aplica para el Titanio. Por otro lado, para el caso de las aleaciones con alto contenido de níquel, el contenido de sulfuros en los líquidos a utilizar debe ser muy bajo.
Inspección Termográfica (IRT)
- Acero al carbono: El estado de oxidación de la superficie tiene cierta afectación en la emisividad del material que se está evaluando, por lo que se deben aplicar ciertos procedimientos para corregir este parámetro al evaluar temperaturas de piel en este material y en aceros de baja aleación.
- Acero inoxidable: La reflectividad típica de las superficies de los aceros inoxidables afectan las lecturas obtenidas de las evaluaciones termográficas, necesitando realizar los ajustes necesarios para corregir los resultados obtenidos.
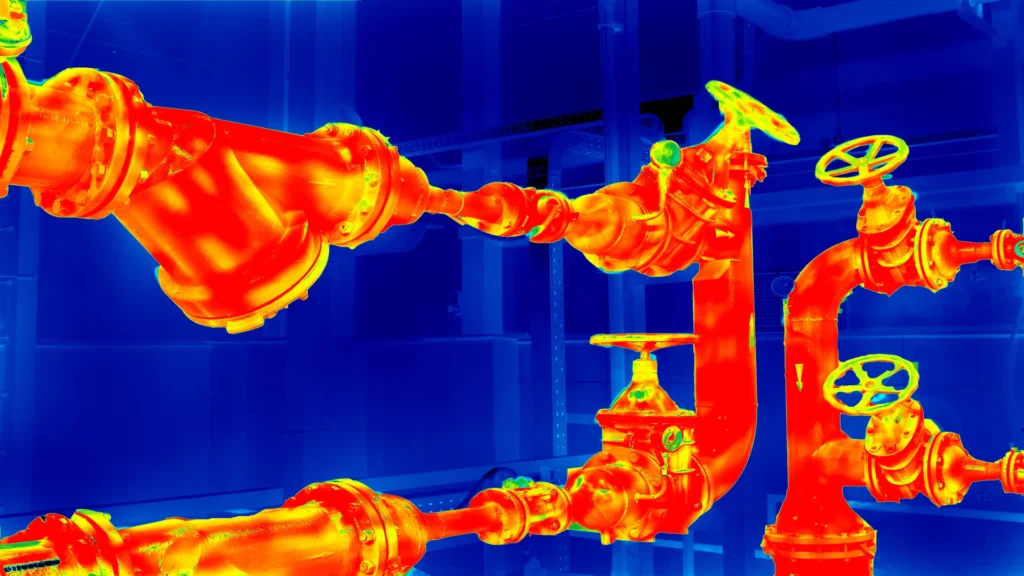
Inspección con Fuga de Campo Magnético (MFL)
- Acero al carbono: Siendo ferromagnético, el acero al carbono y aceros de baja aleación, al igual que el ensayo de partículas magnéticas, también son adecuados para el ensayo de MFL. Esta técnica puede detectar eficazmente discontinuidades superficiales y cercanas a la superficie.
- Acero inoxidable: La mayoría de los aceros inoxidables de uso industria son austeníticos y no magnéticos, lo que hace MFL sea inefectivo al igual que MT. Sin embargo, para los grados magnéticos (martensíticos y ferríticos) de acero inoxidable, MFL aún puede ser aplicable.
Acero al carbono vs. acero inoxidable: Desafíos para los END
Las propiedades únicas del acero al carbono y el acero inoxidable presentan desafíos distintos en los END.
Acero al carbono
- Corrosión: La susceptibilidad del acero al carbono a la corrosión puede en ocasiones complicar los END. Las áreas corroídas pueden afectar la aplicación de algunos métodos de ensayo como ultrasonido al dificultar el barrido del transductor. En otros casos, la remoción de escamas y productos de corrosión en tuberías o equipos de contención con servicios de alta peligrosidad, puede representar un alto riesgo, por lo que debe evaluarse con cuidado las alternativas a aplicar para la evaluación no destructiva de estas zonas. Para este último caso Corrientes Eddy Pulsadas (PEC) es una alternativa.
- Propiedades magnéticas: Aunque beneficiosas para los ensayos de partículas magnéticas, la naturaleza ferromagnética del acero al carbono no es apropiado para ECT, sin embargo, PEC si es efectiva en este material para la detección de corrosión bajo aislamiento térmico y bajo fireproofing (CUI y CUF). Para el resto de los ensayos no tiene ninguna afectación.
- Condición de la superficie: En las evaluaciones termográficas, parámetros como la emisividad y la temperatura reflejada, son claves para la obtención de resultados confiables. Por ejemplo, una superficie oxidada tiende a aumentar la emisividad, por lo que debe ajustarse este parámetro al de ejecutar la inspección.

Solución de Corrientes Eddy Pulsadas.
Acero inoxidable
- Atenuación y reflexión: El tamaño de grano grueso del acero inoxidable pueden llevar a una mayor atenuación de las ondas ultrasónicas, haciendo que UT sea más desafiante. Por décadas la evaluación de soldaduras de acero inoxidable austenítico ha sido un reto para el método de ensayo de ultrasonido al adicionar dificultades como el redireccionamiento del haz (ondas de corte) y la limitación de inspeccionar en la primera pierna con ondas longitudinales. Esto se debe a que un gran porcentaje del haz cambia al modo de ondas de corte al incidir en la pared interior (modo de cambio), las cuales se atenúan fácilmente dentro de la estructura del depósito de la junta.
- Naturaleza no magnética (aceros inoxidables austeníticos): Para la mayoría de los grados de acero inoxidable, la falta de propiedades magnéticas limita el uso de MT y MFL, necesitando métodos alternativos como PT, ECT y RT.
- Condición de la superficie: La superficie reflectante y a menudo pulida del acero inoxidable debe ser tomada en cuenta al realizar inspecciones visuales, ya que un exceso de iluminación y con ello una mayor reflexión, puede afectar el buen discernimiento de la evaluación. Las inspecciones termográficas también son afectadas por esta condición, ya que las superficies reflectantes son emisores poco eficientes2.
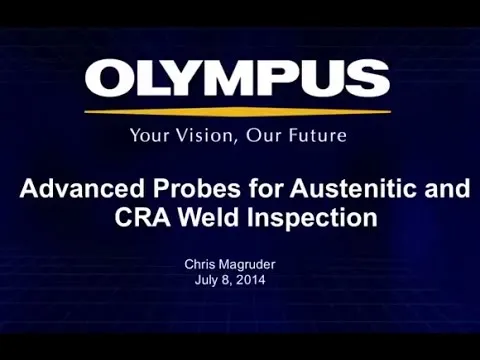
Sondas avanzadas para la inspección de soldaduras austeníticas y CRA.
Mejores prácticas para los END en acero al carbono y acero inoxidable
Para lograr resultados confiables y precisos acero al carbono vs. acero inoxidable, se deben seguir prácticas específicas al realizar END en cada uno de estos tipos de materiales.
Para acero al carbono
- Preparación de la superficie: Asegúrese de que las superficies estén limpias y libres de corrosión y escamas para mejorar la precisión de las inspecciones visuales, líquidos penetrantes, partículas magnéticas y el movimiento y acople del transductor para las inspecciones ultrasónicas.
- Ajuste de frecuencia para el ensayo de Ultrasonido: Dependiendo de la estructura de grano y espesor del componente, haga uso de la frecuencia necesaria para el transductor con el objeto de minimizar los efectos de la atenuación.
- Ajuste de frecuencia para el ensayo de Corrientes Eddy: Dependiendo de la conductividad del material, haga uso de la frecuencia ideal para evaluar el entero espesor o la profundidad requerida del componente.
- Calibración del equipo: Tener disponibles los patrones de calibración y procedimientos necesarios y debidamente aprobados para las diferentes calibraciones de los equipos END. Para las inspecciones con partículas magnéticas y fuga de campo magnético, obtener la fuerza del campo magnético necesario para asegurar la inspección de las diferentes áreas del componente.
- Ajustes de parámetros para evaluaciones termográficas: Ajuste aquellos parámetros que sean afectados por la condición de oxidación de la superficie del metal a fin de obtener resultados confiables.
Para acero inoxidable
- Acondicionamiento de la iluminación: Acondicione la iluminación necesaria para evitar reflejos excesivos que puedan interferir con la evaluación de la superficie a través métodos como VT, PT, MT y Pruebas de Fuga (LT).
- Técnicas avanzadas de UT: Utilice pruebas ultrasónicas de arreglo en fase (PAUT) y uso de transductores lineales en arreglo dual o de matriz, y otras técnicas avanzadas para superar los desafíos planteados por la atenuación, anisotropía, redireccionamiento del haz y modos de cambio en la evaluación de soldaduras austeníticas. La tecnología de matriz 2D le brinda el poder de optimizar el enfoque y la dirección del haz acústico3. Se requiere hacer uso de transductores de menor frecuencia en estas aplicaciones.
- RT de baja energía: Para pruebas radiográficas en componentes altamente críticos, considere el uso de fuentes de energía más bajas y medios de registro que ofrezcan una mayor resolución, para obtener de esta manera una mejor sensibilidad.
- Ajuste de frecuencia para la técnica ECT: Ajuste la frecuencia y utilice métodos avanzados de procesamiento de señales en ECT para obtener resultados precisos.
- Ajustes de parámetros para evaluaciones termográficas: Ajuste aquellos parámetros que sean afectados por la condición de la alta reflectividad de la superficie del metal a fin de obtener resultados confiables.
Conclusión
En el ámbito de los Ensayos No Destructivas, entender las diferencias entre el acero al carbono vs. acero inoxidable es crucial para seleccionar los métodos y las técnicas apropiadas y superar los desafíos inherentes. Aunque ambos materiales son importantes para diferentes aplicaciones industriales, sus propiedades distintas requieren enfoques NDT personalizados para asegurar evaluaciones precisas y confiables. Siguiendo las mejores prácticas con el uso de tecnologías avanzadas, los profesionales pueden evaluar efectivamente la integridad de estos materiales, protegiendo la seguridad y vida útil de estructuras y componentes críticos.
Referencias
- WIKIPEDIA. Carbon steel; Consultado en fecha 16 de julio de 2024. https://simple.wikipedia.org/wiki/Carbon_steel
- FLUKE. Understanding and fixing infrared thermography issues on reflective surfaces; Consultado en fecha 16 de julio de 2024. https://www.fluke.com/es-es/informacion/blog/termografia/resolucion-problemas-termografia-reflectividad
- ZETEC. NDT for Austenitic Stainless Steel: The Shift to Phased Array Ultrasonic; Consultado en fecha 17 de julio de 2024. https://www.zetec.com/blog/ndt-for-austenitic-stainless-steel-the-shift-to-phased-array-ultrasonic/