En la era de la Industria 4.0, la telemetría industrial se ha convertido en un pilar para el monitoreo en tiempo real de equipos rotativos críticos como turbinas y compresores. Esta tecnología permite recopilar, transmitir y analizar datos clave sobre el estado operativo de la maquinaria, mejorando la eficiencia energética, reduciendo fallas inesperadas y extendiendo la vida útil de los equipos.
Estas máquinas son importantes en la generación de energía, la producción petroquímica y la fabricación a gran escala, requieren un seguimiento continuo y preciso para mantener su rendimiento y evitar fallos. La telemetría proporciona datos en tiempo real sobre variables operativas como la temperatura, la vibración, la presión y la velocidad de rotación, lo que permite el mantenimiento predictivo y la optimización de la eficiencia.
¿Qué es la telemetría industrial?
La telemetría industrial se refiere a la medición y transmisión remota de datos desde equipos que operan en diversas condiciones industriales. Permite a los equipos de mantenimiento predictivo recibir información importante sin necesidad de estar físicamente presentes en las instalaciones, lo que agiliza el diagnóstico y la detección temprana de fallos. Se basa en una red de sensores, transmisores y sistemas de procesamiento a través de los cuales, se analizan variables en tiempo real. Los datos pueden visualizarse a través de sistemas SCADA, aplicaciones móviles o plataformas en la nube.
La telemetría industrial consiste en un sistema de monitoreo remoto que recolecta datos desde sensores instalados en maquinaria o procesos industriales, enviándolos a una estación central de análisis a través de redes cableadas o inalámbricas. Datos como presión, temperatura, vibración, flujo, posición, entre otros parámetros físicos y eléctricos.
Esta tecnología es fundamental para sistemas de mantenimiento predictivo, control operativo en tiempo real, en equipos rotativos como turbinas y compresores.
Telemetría en turbinas industriales
La telemetría aplicada a turbinas industriales permite recopilar y transmitir datos operativos en tiempo real, como temperatura, presión, vibraciones y velocidad de rotación. Esta tecnología se basa en una red de sensores estratégicamente ubicados en la maquinaria, los cuales envían información continua a sistemas de monitoreo remoto. De esta manera, se obtiene una visión detallada del comportamiento de la turbina durante su funcionamiento, lo que facilita el análisis de desempeño y la detección temprana de desviaciones o fallas potenciales.
Las turbinas (de gas, vapor o hidráulicas) son equipos de alta velocidad y potencia, donde pequeñas variaciones en condiciones operativas pueden generar daños severos. La telemetría permite monitorear variables en línea como: Temperaturas de entrada y salida, velocidad del eje, vibraciones de los cojinetes, presión del vapor o gas.
Además, el uso de sensores piezoeléctricos y ópticos en turbinas permite detectar desequilibrios, problemas de alineación y signos de cavitación, activando alarmas preventivas o deteniendo el equipo automáticamente para evitar fallas considerables. La integración en entornos industriales representa un paso clave hacia la eficiencia, la seguridad operativa y la digitalización de los sistemas de generación y conversión de energía.
Telemetría en compresores industriales
La telemetría aplicada al monitoreo remoto de compresores industriales ya sean centrífugos, de tornillo o de pistón permite supervisar en tiempo real parámetros críticos como la presión de descarga, la temperatura de operación, el estado del sistema de lubricación y el desgaste en componentes como válvulas o rotores. Estos equipos, fundamentales en sectores como el petroquímico, el alimentario y el energético, requieren un control continuo para garantizar su eficiencia y evitar fallas inesperadas que puedan afectar la producción o comprometer la seguridad operativa.
Mediante el uso de sensores inteligentes y algoritmos analíticos avanzados, la telemetría facilita la detección temprana de anomalías y la identificación de patrones de falla. Esta información permite realizar ajustes operativos y planificar intervenciones de mantenimiento de forma proactiva, sin recurrir a inspecciones manuales frecuentes. Como resultado, se incrementa la disponibilidad de los compresores, se reducen los costos de operación y se extiende la vida útil del equipo dentro de un entorno industrial cada vez más automatizado y orientado a la eficiencia energética.
Soluciones de telemetría para el control y la supervisión industrial
SCADA: Supervisión eficiente para procesos industriales
El sistema SCADA (Supervisory Control and Data Acquisition) es una herramienta esencial en la era de la automatización y la transformación digital industrial. Diseñado para recopilar, analizar y visualizar datos en tiempo real, SCADA integra componentes de hardware y software para ofrecer supervisión y control de procesos en sectores como petróleo y gas, energía, alimentos, farmacéutica, agua y manufactura avanzada.
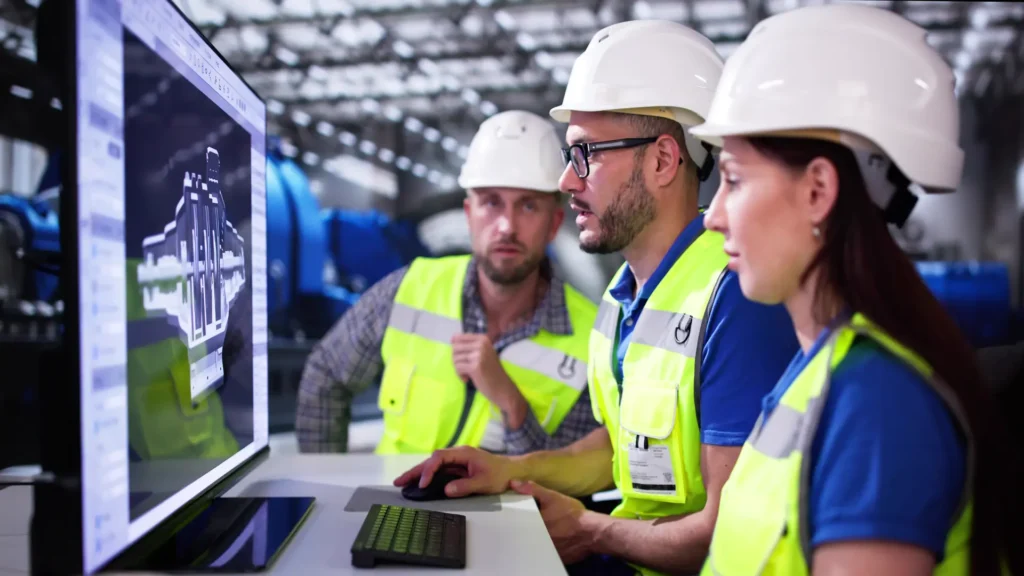
A través de sensores, PLCs/RTUs e interfaces HMI, se logra monitorear fallas operacionales, activar alarmas y optimizar recursos energéticos. Su arquitectura convierte datos operativos en información estratégica, eliminando silos informativos y mejorando la eficiencia operativa.
Implementar SCADA no solo reduce costos y tiempos de mantenimiento, sino que también alinea la producción con objetivos de sostenibilidad. Su valor radica en facilitar decisiones basadas en datos confiables, prolongar la vida útil de los activos y potenciar la productividad en entornos industriales inteligentes.
Sensores de temperatura: clave para la seguridad
Los sensores de temperatura son fundamentales en la telemetría industrial. Ayudan a prevenir daños por sobrecalentamiento en motores, cojinetes, sellos mecánicos y sistemas de refrigeración.
Tipos más comunes:
- RTDs (Resistance Temperature Detectors)
- Termopares (Tipo J, K, T)
- Sensores infrarrojos (sin contacto)
En combinación con la telemetría, estos sensores ofrecen datos continuos para controlar zonas críticas, evitando incendios o pérdidas por paradas inesperadas
Sensores piezoeléctricos y vibración mecánica
La tecnología piezoeléctrica convierte las vibraciones mecánicas en señales eléctricas, permitiendo:
- Monitorear desequilibrios rotacionales
- Detectar fallas en rodamientos
- Medir picos de impacto en sistemas dinámicos
Estos sensores son significativos para el funcionamiento adecuado de compresores y turbinas porque detectan con alta sensibilidad incluso pequeñas irregularidades, la mayoría de las veces invisibles para otros tipos de sensores.
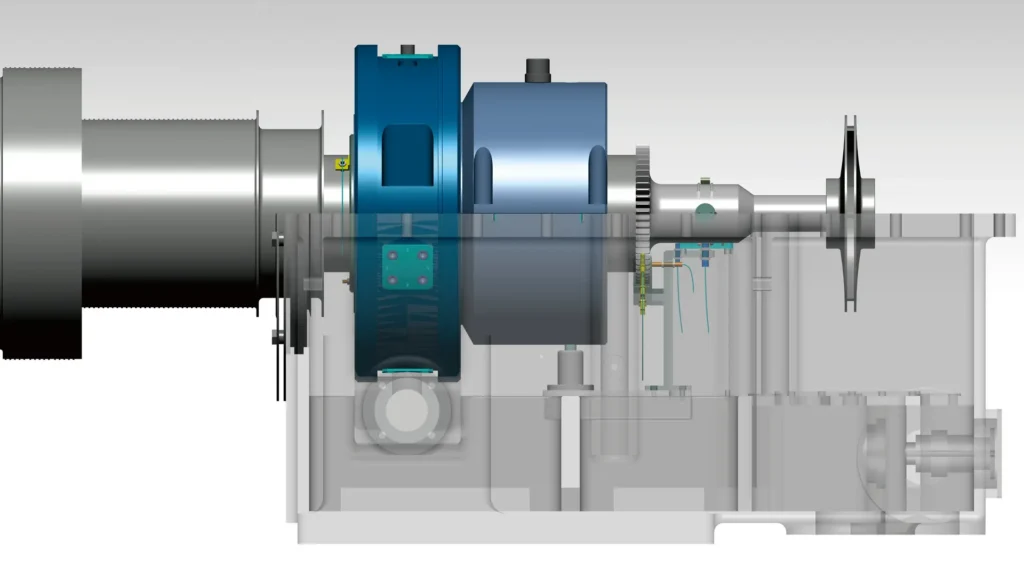
Beneficios de la telemetría en equipos rotativos
La integración de sistemas de telemetría en equipos rotativos como compresores, turbinas y bombas industriales mejora significativamente la gestión del mantenimiento predictivo. Esta tecnología permite recolectar y analizar datos operativos en tiempo real, facilitando la supervisión continua de variables críticas como vibraciones, temperatura, presión y consumo energético.
Entre los beneficios clave de esta tecnología destacan:
- Detección temprana de fallas: Los sensores identifican desviaciones sutiles en el comportamiento del equipo, lo que permite intervenir antes de que se produzcan fallos mayores o paradas no programadas.
- Optimización del mantenimiento: El análisis continuo de los datos permite programar intervenciones solo cuando son necesarias, eliminando mantenimientos innecesarios y reduciendo las tareas correctivas.
- Extensión de la vida útil del equipo: Al operar dentro de sus rangos óptimos, los equipos sufren menos desgaste prematuro, lo que prolonga su funcionamiento y retrasa la necesidad de reemplazo.
- Toma de decisiones basadas en datos: La telemetría proporciona información constante y confiable, permitiendo a los responsables de mantenimiento priorizar acciones en función del estado real del equipo.
- Reducción de costos operativos: Al prevenir fallos, reducir tiempos de inactividad y optimizar los recursos, la telemetría contribuye a disminuir significativamente los costos asociados al mantenimiento reactivo.
La telemetría transforma el mantenimiento tradicional en un proceso dinámico, inteligente y centrado en la confiabilidad. Su implementación no solo mejora la productividad, sino que convierte al mantenimiento predictivo en un aliado estratégico para la industria moderna.
Conclusión
La integración de telemetría industrial con sensores avanzados está cambiando la forma en que las turbinas y compresores industriales son monitoreados y mantenidos, este enfoque optimiza la operación de equipos, y protege activos estratégicos y mejora la rentabilidad industrial. La transición hacia plataformas inteligentes y conectadas ya no es una opción, sino una necesidad para las industrias que buscan sostenibilidad, competitividad y excelencia operativa.
Referencias
- Mechanical Solutions, Inc. (2025). Centrifugal compressor impeller strain measurement via FM telemetry: case study. Recuperado de https://www.mechsol.com/case-study/strain-measurement-of-a-centrifugal-compressor-impeller-via-fm-telemetry
- Meyer, A., & Brodbeck, B. (2020). Performance fault detection in wind turbines by dynamic reference state estimation. arXiv. Recuperado de https://arxiv.org/abs/2005.00370