El desarrollo tecnológico es esencial para desbloquear las oportunidades que el hidrógeno puede ofrecer a los sistemas energéticos. Centrarse en la innovación desde un primer momento ayudaría a desarrollar soluciones tecnológicas adaptadas a las prioridades y condiciones, en consonancia con los objetivos energéticos y climáticos a nivel mundial. Es necesario contar con inversiones internacionales para el desarrollo y avances en investigaciones dirigidas al impulso de nuevas tecnologías aplicadas en diferentes sectores en el futuro, adquirir experiencia y conocimiento en el diseño de equipos. Por ejemplo, los potenciales objetivos en materia de electrólisis en la fabricación de electrolizadores.
Los consorcios y las asociaciones nacionales de hidrógeno, pueden desempeñar un papel importante en la identificación de futuras oportunidades comerciales comunes en Hidrógeno en concordancia a las prioridades de Investigación y Desarrollo (I+D), con el fin de optimizar la inversión y maximizar la transferencia de conocimientos. Una atención temprana al desarrollo de habilidades podría ayudar a generar oportunidades y prevenir futuros problemas de escasez de recursos humanos a medida que la industria se desarrolla. El fomento de capacidades en toda la cadena de valor del hidrógeno, como la fabricación de equipos, la producción de hidrógeno, el despliegue de infraestructuras y usos finales, acarrearía beneficios adicionales más allá de la reducción de emisiones, como desarrollo económico, y oportunidades para los inversionistas.
Esta coordinación también es esencial para garantizar una comunicación eficaz y aumentar el nivel de comprensión de estas tecnologías emergentes entre los potenciales consumidores, los proveedores de servicios y de financiamiento, y en la sociedad en general, así como para manejar las expectativas en torno al uso de estas nuevas energías. Con el fin de fabricar sus productos con materiales más sostenibles, limitar y eliminar el uso de productos químicos tóxicos y reducir el impacto de sus procesos industriales y de fabricación en el medio ambiente y el cambio climático global. Ha llegado una nueva era industrial responsable, donde la fabricación y la producción son más eficientes, más ecológicas, más eficientes, implican menos residuos y con nuevos clientes centrados en el medio ambiente en la protección del planeta para las generaciones futuras.
En este contexto los sectores empresariales actualmente se están incorporando a diferentes proyectos vinculados al uso del hidrógeno a fin de descarbonizar sus actividades. Una de las grandes ventajas que presenta el hidrógeno son las nulas emisiones de dióxido de carbono; de hecho, en el caso de emplear el hidrógeno en una pila de combustible la única emisión resultante será agua, mientras que, en el caso de utilizarlo en motores de combustión interna, ciertamente, todavía presentará unas pequeñas emisiones de óxidos de nitrógeno. Sin embargo, el hidrógeno no es un combustible que se encuentre libre y que se pueda extraer de forma directa de la naturaleza. Por el contrario, el hidrógeno es un resultante energético, es decir, su obtención está sujeta a un proceso de producción que requiere una cierta cantidad de energía. De este modo, si bien el uso del hidrógeno no da lugar a emisiones de efecto invernadero, su obtención sí puede tener unas emisiones asociadas en función del proceso seguido, de las fuentes de energía primaria empleadas y del post-procesado.
En este punto cabe destacar que el hidrógeno será tan limpio y cero emisiones como lo sea su proceso de obtención, y esto es muy importante. Por ejemplo, de nada servirá sustituir todos los vehículos con motores de combustión interna por su equivalente de pila de combustible si el hidrógeno que se le suministra a dichos vehículos ha sido obtenido por una ruta más contaminante que el uso del propio diésel o gasolina. En función de la fuente primaria de energía empleada para producir el hidrógeno, así como de los procesos de obtención empleados, es posible clasificar el hidrógeno obtenido mediante la asignación de una escala de colores, en lo que se ha dado en llamar los colores del hidrógeno, que si bien no está completamente estandarizada sí que se encuentra muy extendida.
Procesos y nuevas tecnologías para la producción de Hidrogeno
- 1 Procesos a partir de gas natural
La principal fuente de obtención de hidrógeno es el gas natural, formado principalmente por metano. La combinación de tres factores: grandes reservas mundiales, su relativo bajo coste y su composición química, hace que el gas natural sea actualmente la fuente de hidrógeno más interesante para el mercado mundial.
El proceso de extracción del hidrógeno del gas natural se conoce cómo reformado. En este proceso se producen óxidos de carbono como subproducto en forma gaseosa lo que constituye su principal desventaja, al generarse del orden de 11 toneladas de CO2 por cada tonelada de hidrógeno. Alternativamente, existe una tecnología en fase de desarrollo, la pirólisis de metano, que da lugar como subproducto a carbón en forma sólida, y en la que se producen como residuo 3 toneladas de carbono por tonelada de hidrógeno.
- Procesos de reformado del metano
Reformado de gas natural se basa en descomposición de la molécula de metano para dar lugar a hidrógeno y óxidos de carbono (CO y CO2). Para que tenga lugar este proceso se requiere la combinación de tres condiciones16: alta temperatura (700-1.100 °C), presencia de un catalizador (en base níquel), y presencia de un agente oxidante (agua y/o aire).
Existen tres métodos de producción en función del agente oxidante
– Vapor de agua: reformado con vapor.
– Oxígeno o aire: oxidación parcial.
– Una combinación de ambos: reformado autotérmico (ATR).
El Proceso de reformado de metano con vapor, es el proceso más extendido, da lugar a la formación de un gas de síntesis, mediante la siguiente reacción:
CH4(g)+H2O(g)⟶3H2(g)+CO(g)
Esta es una reacción fuertemente endotérmica que requiere elevadas temperaturas de hasta 1000 °C. Previo al proceso de reformado es indispensable eliminar las trazas de compuestos de azufre presentes en el gas para evitar el envenenamiento de los catalizadores, siguiendo con un pre-reformado opcional cuyo objetivo es romper los hidrocarburos de cadenas más largas como el butano o el propano de modo que se aumente la riqueza de metano y el proceso sea más eficiente.
La oxidación parcial con aire se utiliza principalmente para producir gas de síntesis a partir de material sólido como el carbón o la biomasa. El reformado autotérmico (ATR) consta de unidades en las que se emplean conjuntamente ambos agentes oxidantes, aire y agua. La inyección de un contenido controlado de aire reduce el consumo de combustible externo en la unidad de reformado debido a que una parte del calor necesario para romper el metano proviene de la oxidación con oxígeno. Se utiliza principalmente para el reformado de hidrocarburos, pero también se realiza a partir de gas natural1.
Independientemente del agente oxidante, el proceso global de producción de hidrógeno actual se basa en 4 etapas en serie (ver figura 1): desulfuración del gas natural, reformado, desplazamiento del gas y purificación del hidrógeno. De todas ellas, la unidad central del proceso es el reformado, pero antes de entrar en el reformador, el gas natural pasa por un proceso de desulfuración, en el que se elimina más de un 99 % del azufre que contiene el gas convencional. Después de la etapa de desulfurización, se obtiene un gas limpio por debajo de las 0,1 ppm de H2S. Este proceso consta de dos unidades: la primera convierte todo el azufre en su forma reducida mediante hidrogenación y un catalizador en base cobalto y molibdeno; la segunda elimina el azufre con un catalizador de óxido de zinc. La desculturización es una etapa clave para reducir el “envenenamiento” del catalizador en el reformado.
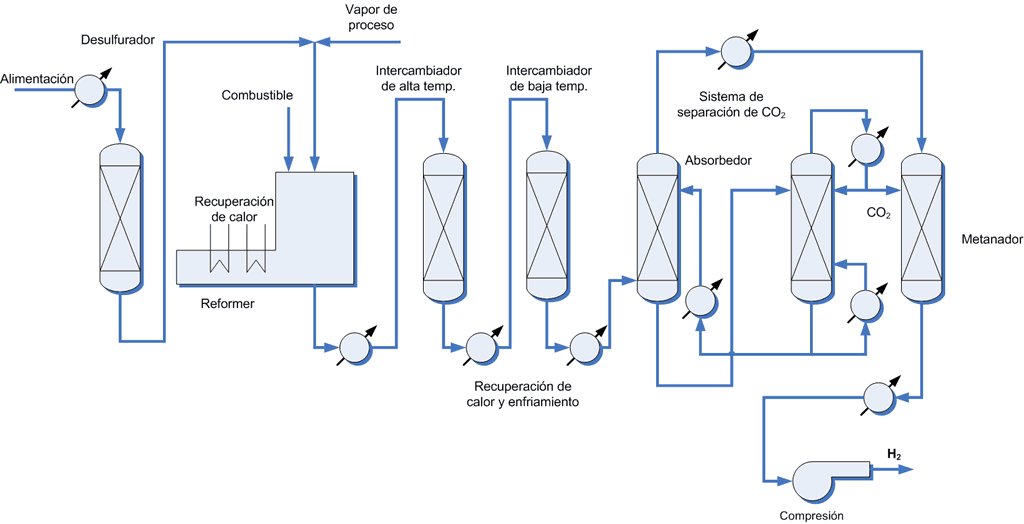
Una vez limpio, el gas natural se mezcla con vapor de agua, se incrementa la temperatura a unos 700-900 °C y se introduce en un lecho catalítico en base níquel. Las altas temperaturas requeridas en el reformador se consiguen con la quema de un combustible externo, ya sea una parte del gas natural u otro hidrocarburo. Cabe destacar que las instalaciones modernas han permitido aumentar la eficiencia energética del proceso de reformado entre un 10-20 %. Una vez se consigue la mezcla de gas de síntesis (CO e H2), se pasa a la unidad de desplazamiento para convertir el monóxido de carbono (CO) a dióxido de carbono (CO2) e incrementar la cantidad de hidrógeno final. Los catalizadores utilizados en la unidad de desplazamiento se basan en hierro, cromo y cobalto. Esta unidad consiste en dos reactores en serie: un primero a alta temperatura y un segundo a más baja temperatura.
Independientemente del proceso de oxidación el producto obtenido a partir del reformado es una mezcla de dióxido de carbono (CO2) e hidrógeno (H2), con trazas de metano (CH4) y monóxido de carbono (CO). Para obtener una corriente de hidrógeno puro se debe proceder a una etapa final de purificación, es decir, de separación de los otros compuestos del gas de síntesis. Esta etapa puede constar de varias unidades en función de la tecnología utilizada con el objetivo de suministrar hidrógeno de elevada pureza al final del proceso.
- Tecnología SMR: Reformado de Metano con Vapor con (PSA) para la producción de hidrógeno
La SMR es un método rentable y energéticamente eficiente de producción hidrógeno. Gracias a la tecnología interna de purificación mediante adsorción por oscilación de presión (PSA), pueden alcanzarse altos niveles de pureza 1.
En el proceso de reformado con vapor, un hidrocarburo desulfurado (gas natural, efluente gaseoso de la refinería, gas licuado de petróleo o nafta), materia prima, es sometida previamente a un tratamiento térmico y mezclado con vapor. Opcionalmente, se puede reformar previamente antes de pasar por un catalizador en un reformador a vapor exclusivo con quemadores en la parte superior, para producir hidrógeno, monóxido de carbono (CO) y dióxido de carbono (CO₂).
El CO, mediante desplazamiento por vapor se convierte en hidrógeno y CO₂ adicional. Luego el hidrógeno es separado usando la adsorción por oscilación de presión.
-Adsorción por oscilación de presión (PSA)
La adsorción por oscilación de presión es un proceso en el cual se separan gases individuales de una mezcla de gases. Se utiliza principalmente en los procesos químicos y petroquímicos, así como en la industria siderúrgica, por ejemplo, para recuperar el hidrógeno (H2) de los gases de coque o de conversión, o para separar el oxígeno (O2) y el nitrógeno (N2) del aire.
El proceso de adsorción se basa en la unión de las moléculas de gas a un material adsorbente. El lecho de adsorbente se selecciona especialmente en función del gas a absorber. Lo ideal es que solo se adsorba el gas que se va a separar, mientras que todos los demás pasen por el lecho de adsorción sin quedar atrapados. A menudo se utilizan adsorbentes que contienen carbono activo o tamices moleculares de carbón y adsorbentes de óxido como zeolita. La pureza del gas adsorbido no solo depende del adsorbente utilizado, sino que también son importantes la temperatura y la presión durante el proceso.
El proceso de adsorción por oscilación de presión se divide en cuatro etapas (Figura 2), que suceden en ciclos:
Adsorción: La adsorción tiene lugar a alta presión (hasta 40 bares). La mezcla de gases pasa por un lecho de adsorbente. El adsorbente atrapa las moléculas de gas fácilmente adsorbibles, mientras que las moléculas de gas que no son fácilmente adsorbibles o no son adsorbibles en absoluto pasan a través del lecho. El lecho adsorbente sigue adsorbiendo moléculas de gas hasta que alcanza su capacidad máxima.
Despresurización: La despresurización es el primer paso de la regeneración (desorción) del lecho adsorbente. A medida que la presión desciende, las moléculas de gas del lecho adsorbente se liberan y el gas objetivo se descarga del depósito de adsorción.
Purga: El lecho adsorbente se purga con el gas objetivo para regenerarlo completamente.
Represurización: Se hace con la mezcla de gases o con el gas objetivo hasta que se restablecen las condiciones del proceso de adsorción.
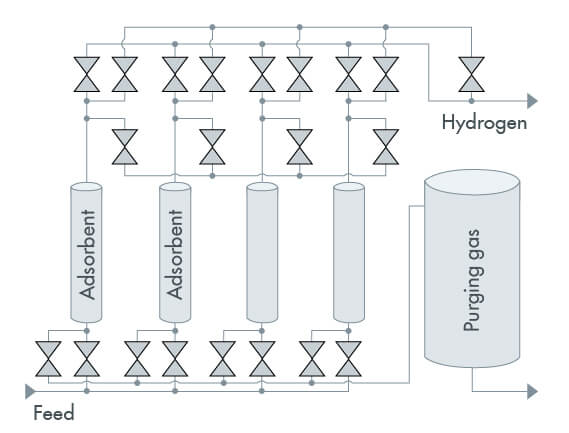
Proceso de pirolisis para la producción de hidrogeno
La pirólisis del gas metano es una tecnología incipiente que permite la descomposición del metano en hidrógeno y carbón (ver Figura 3). Este proceso también es conocido como craqueo térmico del metano o descomposición del metano, y ciertos autores denominan el hidrógeno producido como turquesa. En el proceso de pirólisis del gas, se produce en forma sólida mediante la siguiente reacción:
CH4 (g) → 2H2 (g) + C (s)
A diferencia del reformado, este proceso no requiere de ningún agente oxidante como el agua o el oxígeno. De este modo, no se añade ningún compuesto químico que contenga oxígeno en su estructura y que favorezca la producción de óxidos de carbono (CO2 o CO). Es importante mencionar que esta tecnología está todavía en fase de desarrollo.
- La tecnología de pirólisis asistida por plasma por microondas
El craqueo térmico del metano puede realizarse mediante la aplicación de la energía de una fuente de microondas. Por esta vía se ha conseguido descomponer de forma eficiente una corriente de CH4 en H2 puro y filamentos carbonosos, obviamente en ausencia de cualquier óxido de carbono (no existe oxígeno en el medio de reacción). Se debe reseñar el hecho de que los residuos de carbono, subproductos de la reacción, proporcionan un valor agregado al H2 producido ya que tienen excelentes propiedades de adsorción.
Una forma de llevar a cabo la descomposición del CH4 en sus componentes (H2 y C) de forma más suave que la propia pirólisis es mediante incorporación de catalizadores al reactor (Figuras 3). Los catalizadores disminuyen la energía de activación del proceso de pirólisis y aumentan, por lo tanto, la velocidad del proceso de generación de hidrógeno. Los catalizadores más idóneos para realizar este proceso están constituidos por partículas de níquel y hierro, finamente dispersas sobre soportes inorgánicos de naturaleza mesoporosa, por ej. Al2O3 y SiO2. Este tipo de sistemas producen H2, exento de óxidos de carbono, y filamentos de carbono que terminan desactivando el catalizador. El procedimiento usual de restaurar la actividad del catalizador desactivado consiste en gasificar el residuo carbonoso por tratamiento en aire o en vapor de agua; de estas opciones, el tratamiento con vapor de agua resulta particularmente atractiva ya que el níquel permanece en el estado metálico y no se requiere ningún tratamiento de reducción posterior antes de utilizarlo nuevamente.
Producción de Hidrógeno por electrólisis del agua
La electrolisis de agua es una tecnología fiable, con muchos años de experiencia acumulada en la Industria, y con numerosos proveedores de equipos y componentes (Figura 4). Como tecnología de obtención de hidrógeno, permite obtenerlo de gran pureza. El costo está determinado por el de la electricidad que se utilice. Y en todo caso, es importante recordar que el costo final del hidrógeno en un lugar determinado estará condicionado por los gastos de transporte y almacenamiento, así como los beneficios de los intermediarios.
Cuando el volúmen de hidrógeno requerido en alguna aplicación es moderado, el hidrógeno se obtiene mediante electrolisis de agua. La reacción electrolítica se realiza en medio alcalino debido a que en este medio se incrementa la conductividad eléctrica. El hidrógeno producido en el cátodo se debe purificar ya que contiene impurezas de oxígeno y un cierto nivel de humedad. La corriente de hidrógeno se seca con ayuda de un adsorbente y las impurezas de oxígeno se eliminan con un convertidor DeOxo. Además, en el ánodo del electrolizador se produce oxígeno, cuyo volumen es la mitad del volumen de hidrógeno, tal como corresponde a la composición de la molécula de agua. La mayor parte de los electrolizadores son de tipo tanque con los electrodos dispuestos en paralelo. El calor liberado en el proceso se elimina recirculando agua alrededor de las celdas.
El hidrógeno permite el acceso a un amplio grupo de precursores primarios tales como combustibles fósiles, energía nuclear y con una penetración cada vez mayor de las energías renovables (eólica, solar, biomasa). Conviene señalar el hecho de que el hidrógeno producido por electrolisis es del orden de 4.9-5.6 kWh por cada m3 de hidrógeno producido, lo que resulta al menos dos veces más caro que el hidrógeno obtenido por reformado del gas natural.
Puesto que los electrolizadores convencionales proporcionan H2 con un costo elevado, se han desarrollado otros procesos electrolíticos.
Uno de ellos es la electrolisis en fase de vapor. El potencial reversible de la celda decrece al aumentar la temperatura. Puesto que el costo de electricidad requerida en la electrolisis para producir H2 a partir de H2O es proporcional a la fuerza electromotriz de la celda, el costo disminuye con la temperatura. La celda se enfría debido a que el proceso es endotérmico y se mantiene a temperatura constante aportando calor desde el exterior. Esto significa que el calor se convierte por vía electroquímica en H2 sin pasar por un ciclo de Carnot. Así, a 1.500 ºK la cantidad de energía térmica que se utiliza en la descomposición termo-electroquímica es del 50% del total. Bajo estas condiciones, el costo de producción es 50% más bajo que en el proceso convencional.
Otra alternativa económica de producción de H2 la proporcionan nuevos tipos de electro-catalizadores que son capaces de disminuir el sobrevoltaje, lo que supone una reducción del coste.
Ecuaciones:
En el agua pura, en el cátodo cargado negativamente, se lleva a cabo una reacción de reducción, con los electrones (e-) desde el cátodo dando a los cationes de hidrógeno para formar gas de hidrógeno (el medio de reacción equilibrada con ácido):
Reducción en el cátodo: 2 H+(aq) + 2e- → H2 (g)
En el ánodo cargado positivamente, se produce una reacción de oxidación, la generación de oxígeno gas y que da electrones al ánodo para completar el circuito.
Oxidación en el ánodo: 2 H2O (l) → O2 (g) + 4 H+(ac) + 4e-
Reducción en el cátodo: 2 H+(aq) + 2e- → H2 (g)
En el ánodo cargado positivamente, se produce una reacción de oxidación, la generación de oxígeno gas y que da electrones al ánodo para completar el circuito.
Oxidación en el ánodo: 2 H2O (l) → O2 (g) + 4 H+(ac) + 4e-
Las mismas medias reacciones también pueden equilibrarse con la base que se enumeran a continuación. No todas las medias reacciones se deben equilibrar con ácido o base. Muchos lo hacen, como la oxidación o reducción del agua que
aparece aquí. Para añadir la mitad de las reacciones de éstos debe estar equilibrado con ácido o base.
Cátodo (reducción): 2 H2O (l) + 2e- → H2 (g) + 2 OH- (ac)
Ánodo (oxidación): 4 OH- (ac) → O2 (g) + 2 H2O (l) + 4 e-
La combinación de ambas reacciones da la misma descomposición total del agua en oxígeno e hidrógeno:
Reacción general: 2 H2O (l) → 2 H2 (g) + O2 (g)
El número de moléculas de hidrógeno producido de este modo es el doble del número de moléculas de oxígeno. Suponiendo igual presión y temperatura para ambos gases, el gas de hidrógeno producido tiene, por tanto, el doble de volumen del gas oxígeno producido. El número de electrones transportado a través del agua es dos veces el número de moléculas de hidrógeno generado y cuatro veces el número de moléculas de oxígeno generadas.
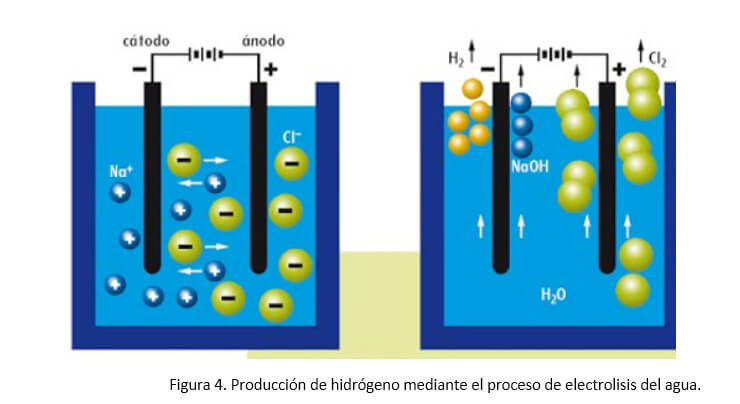