La corrosión en tuberías representa uno de los principales retos en la industria de petróleo y gas, debido a que estas estructuras conforman los sistemas de transporte de los flujos de procesos. A diario, miles de kilómetros de ductos trasladan hidrocarburos y sus derivados entre instalaciones de extracción, refinación y distribución. Sin embargo, estas tuberías están expuestas a entornos agresivos que favorecen la corrosión, comprometiendo su integridad y eficiencia operativa.
Actualmente, mediante el uso de tecnologías y prácticas de mantenimiento adecuadas, este problema puede ser controlado, prolongando significativamente la vida útil de sus activos.
Mecanismos de corrosión en tuberías
La corrosión es un proceso natural en el que los metales se deterioran con el tiempo debido a reacciones electroquímicas con el medio. Sin un mantenimiento adecuado y supervisión periódica, este proceso puede provocar fugas o incluso la rotura de tuberías, con graves consecuencias para el medio ambiente, la seguridad pública y los resultados financieros de las empresas. En la siguiente imagen se puede apreciar la corrosión del hierro en una tubería de acero.
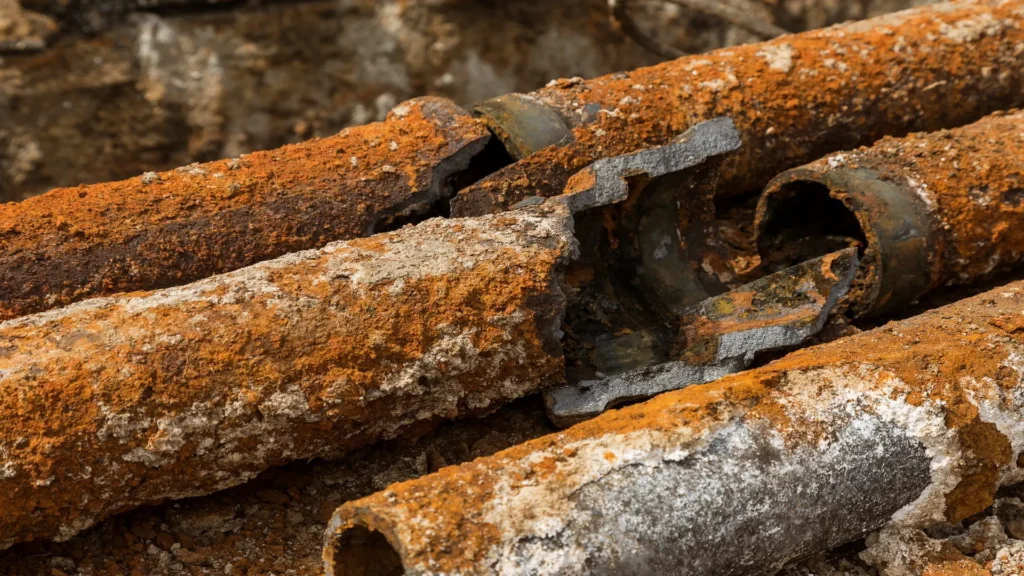
Tipos de corrosión en sistemas de transporte
- Corrosión galvánica: Ocurre cuando dos metales diferentes están en contacto en presencia de un electrolito. El metal menos noble (ánodo) se corroe mientras el más noble (cátodo) permanece intacto.
- Corrosión por picaduras: Es un tipo de ataque localizado que produce pequeños agujeros en la superficie del metal. Particularmente peligrosa porque es difícil de detectar y puede progresar rápidamente.
- Corrosión Influenciada Microbiológicamente (MIC): Causada por la actividad metabólica de microorganismos como por ej. Bacterias Reductoras de Sulfato (SRB).
- Corrosión Bajo Tensión (SCC): Combinación de tensiones mecánicas y ambiente corrosivo que produce grietas en el metal.
- Corrosión por CO₂ (Sweet Corrosion): Común en la industria petrolera, ocurre cuando el dióxido de carbono disuelto forma ácido carbónico.
- Corrosión por H₂S (Sour Corrosion): Causada por el sulfuro de hidrógeno presente en crudos y gas natural, particularmente agresiva y puede causar fragilización por hidrógeno.
Factores que Influyen en la velocidad de corrosión
- Composición del fluido transportado: Presencia de agua, CO₂, H₂S, oxígeno, cloruros, etc.
- Altas Temperaturas y presiones.
- Velocidad de flujo: Erosión-corrosión en zonas de alta velocidad.
- pH del medio.
- Propiedades metalúrgicas de la tubería.
- Condiciones del suelo (para tuberías enterradas).
- Interfaces aire-agua-suelo (zonas de triple interfaz).
Métodos de prevención y control de la corrosión
Selección de materiales
La primera línea de defensa contra la corrosión comienza con la selección apropiada de materiales, entre los que se incluyen:
- Aceros de baja aleación y alta resistencia (HSLA).
- Aceros inoxidables para ambientes particularmente corrosivos.
- Aleaciones resistentes a la corrosión (CRAs) como Inconel, Hastelloy, etc.
- Materiales compuestos para aplicaciones específicas.
Recubrimientos de protección contra la corrosión
Son un tipo especial de revestimiento que se aplica a las superficies metálicas para proteger la superficie subyacente de posibles daños corrosivos causados por el agua, el oxígeno o los electrolitos, actúan como una barrera física entre el metal y el ambiente corrosivo.
Las innovaciones en recubrimientos superficiales incluyen nuevas formulaciones, aplicaciones avanzadas y mejoras en el curado. Destaca el uso de resinas termoestables o termoplásticas en recubrimientos en polvo, que se aplican electrostáticamente sobre superficies metálicas y se curan térmicamente para lograr una capa uniforme, duradera y resistente. Entre los más utilizados se incluyen:
- Revestimientos epóxicos FBE (Fusion Bonded Epoxy).
- Sistemas de tres capas (3LPE/3LPP): Epoxy + adhesivo + polietileno/polipropileno.
- Revestimientos internos para protección contra fluidos corrosivos.
- Pinturas especializadas para instalaciones superficiales.
Protección Catódica (PC)
La protección catódica es una técnica para el control de la corrosión electrolítica en componentes metálicos expuestos a medios conductores. Su implementación es fundamental para extender la vida útil de estructuras metálicas críticas, como tuberías, tanques y plataformas marinas. Esta técnica de protección se realiza a través de dos métodos principales:
- Protección catódica por ánodos de sacrificio: Se conecta un metal más activo (el ánodo, como zinc o aluminio) a la estructura que se quiere proteger (el cátodo). El ánodo se corroe en lugar de la estructura, protegiéndola.
- Protección catódica por corriente impresa: Se utiliza una fuente de corriente externa (como un rectificador) para suministrar corriente a la estructura, convirtiéndola en el cátodo de la celda electroquímica.
El monitoreo es significativo para prevenir el deterioro de estas estructuras, asegurando su mantenimiento, integridad estructural y eficiencia operativa. La efectividad se valida mediante la comprobación de los criterios de protección catódica. La correcta aplicación de técnicas adecuadas y el uso de modernos sistemas de videovigilancia simplifican las operaciones de control, garantizando así la eficacia del sistema de protección catódica a lo largo del tiempo.
Inhibidores de corrosión
Los inhibidores de corrosión son utilizados para prevenir la degradación de los metales, al ser añadido en pequeñas concentraciones a un ambiente agresivo, ejercen un control de las reacciones electroquímicas, disminuyendo así la velocidad de la reacción de oxidación. Su mecanismo de acción incluye la formación de una película protectora sobre la superficie del metal, que puede lograrse mediante la pasivación del metal, la neutralización de agentes corrosivos o la alteración de las reacciones electroquímicas responsables de la corrosión.
Estos compuestos son necesarios en aplicaciones industriales, como oleoductos, maquinaria, tanques de almacenamiento, para garantizar la durabilidad y fiabilidad de los componentes metálicos. A continuación se presentan los tipos de Inhibidores de corrosión más utilizados.
- Inhibidores de película: Forman una capa protectora sobre la superficie metálica.
- Inhibidores anódicos y catódicos: Interfieren con las reacciones electroquímicas.
- Inhibidores volátiles: Para espacios confinados y sistemas fuera de servicio.
- Biocidas: Controlan la corrosión microbiológica.
Tecnologías avanzadas para el control de corrosión
Las tecnologías avanzadas para el control de la corrosión en tuberías están transformando la forma en que las industrias gestionan la protección y mantenimiento de sus activos. Gracias a la digitalización, el monitoreo remoto se ha convertido en una herramienta fundamental para detectar y prevenir daños antes de que se conviertan en problemas mayores.
Los sensores IoT permiten la supervisión continua de parámetros críticos como la humedad, temperatura y concentración de agentes corrosivos, proporcionando datos en tiempo real que facilitan una respuesta rápida y eficiente.
Además, el uso de gemelos digitales ha abierto un nuevo horizonte para la modelación y predicción del comportamiento corrosivo, permitiendo simular escenarios y optimizar estrategias de mantenimiento basadas en datos precisos y actualizados.
La inteligencia artificial complementa estos avances al analizar grandes volúmenes de información, identificando patrones y recomendando acciones preventivas que maximizan la vida útil de los materiales.
Marco regulatorio
Para garantizar la integridad y seguridad en sistemas industriales sujetos a corrosión, es fundamental cumplir con normativas técnicas y regulaciones reconocidas internacionalmente. Entre las más relevantes se encuentran los estándares NACE/AMPP, las normas del American Petroleum Institute (API), así como las regulaciones específicas de cada región y las certificaciones del personal involucrado en inspección y control de corrosión.
Conclusiones
La corrosión en tuberías de petróleo y gas es un desafío técnico controlable mediante estrategias integradas como la selección adecuada de materiales, protección catódica, recubrimientos avanzados, inhibidores químicos y monitoreo continuo. La adopción de tecnologías emergentes, como recubrimientos inteligentes y autorreparables, mejora la resistencia a la degradación, optimiza la operación y reduce costos de mantenimiento.
En un mundo cada vez más digitalizado, las nuevas tecnologías ofrecen oportunidades sin precedentes para optimizar la gestión de la corrosión, permitiendo transitar de un enfoque reactivo a uno predictivo y finalmente a uno prescriptivo, donde los sistemas inteligentes pueden recomendar acciones específicas antes de que los problemas se materialicen.
Referencias
- NACE/AMPP International: www.ampp.org
- American Petroleum Institute: www.api.org
- Pipeline and Hazardous Materials Safety Administration: www.phmsa.dot.gov