Introducción
En la dinámica del sector energético, las paradas de planta en la industria petrolera representan uno de los eventos más críticos para sus operadoras, ya que pueden afectar tanto la operatividad como la rentabilidad de las operaciones en sus instalaciones de producción. La gestión eficaz de estas paradas no es solo una cuestión de mantenimiento, sino una estrategia económica que puede determinar el éxito financiero a largo plazo de una empresa.
En este artículo se analiza el impacto económico de las paradas de planta en la industria petrolera, abarcando tanto las paradas programadas como las no programadas y la importancia estratégica en la dirección de proyectos de paradas de planta y programas de mantenimiento.
¿Qué son las paradas de planta en la industria petrolera?
Una parada industrial, también conocida como parada de planta, es un proceso planificado y programado en el cual se detiene completamente la producción de una instalación industrial con el objetivo de llevar a cabo labores de mantenimiento, reparación, inspección, modificación o mejoras en los equipos, maquinarias y sistemas de plantas..
Tipos de paradas de plantas
Paradas no programadas
En la industria, especialmente en la petrolera, son situaciones críticas que pueden tener un impacto significativo en la producción, la seguridad y la rentabilidad. Este tipo de interrupciones ocurren de forma inesperada y pueden ser provocadas por una variedad de razones, tales como:
- Fallas mecánicas: (deterioro de una bomba en una instalación de refinación que cause el cierre automático del sistema)
- Errores humanos: Los errores humanos, como la manipulación incorrecta de herramientas o equipos por parte de un operador, pueden ocasionar acciones de cierre de emergencia en una planta.
- Fallas de software: Problemas en los programas de computadora o sistemas de software que desencadena un resultado indeseado en el control operativo del proceso.
- Desastres naturales: Eventos naturales como huracanes y terremotos
Paradas programadas
A diferencia de las emergencias, las paradas programadas se planifican con anticipación y forman parte de las planificaciones para mantenimientos regulares. Estas paradas permiten a la planta realizar actualizaciones esenciales y mantenimiento preventivo sin comprometer la seguridad y la producción continua, tales como:
- Actualización tecnológica: Programación para instalar nuevas tecnologías y mejorar la eficiencia de la planta. A continuación se presenta el siguiente video donde se muestra el reemplazo de los tambores de coque en la refinería Petrobrazi. Cortesía de OMV Petrom el mayor productor integrado de energía del sudeste de Europa.
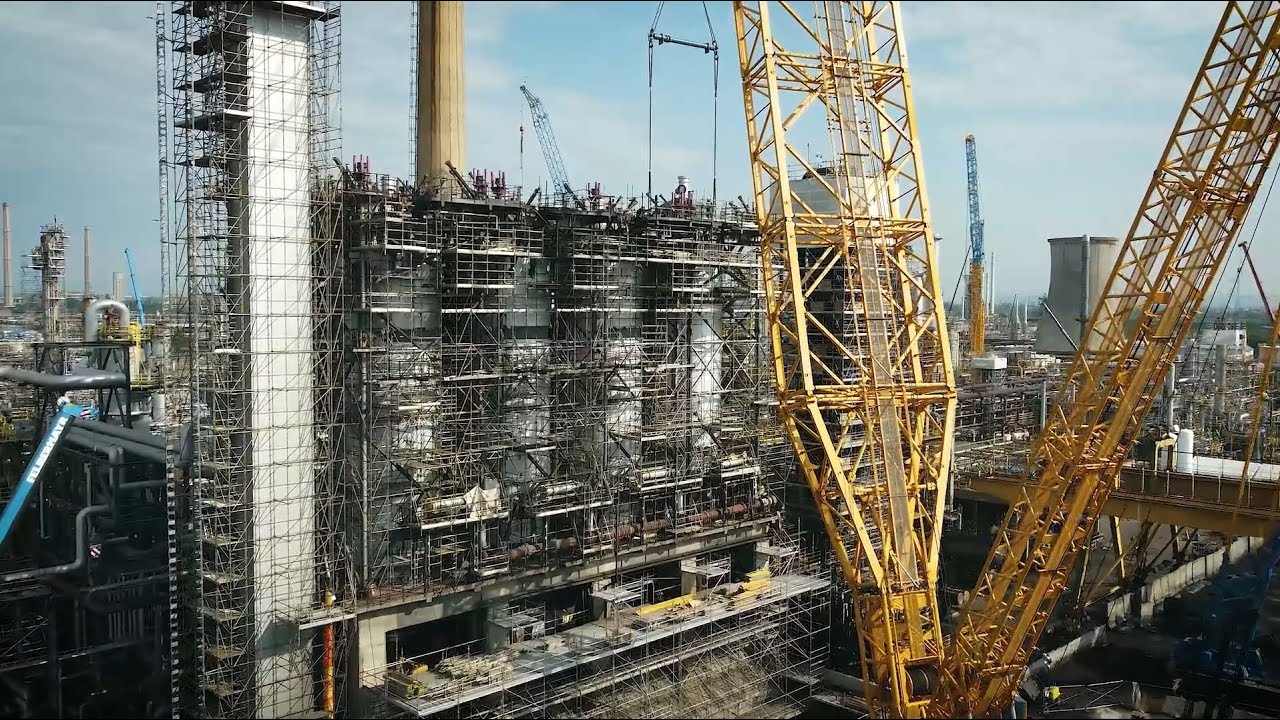
Reemplazo de tambores de coque en Refinería de Petrobrazi.
- Mantenimiento preventivo: Organizaciónpara la inspección y reparación de calderas, lo que ayuda a prevenir fallas inesperadas y garantizar una operación continua y estable.
- Revisión completa: Programación de paradas para realizar revisiones completas.
Impacto económico de las paradas de planta
El impacto económico de las paradas de planta en la industria, particularmente en sectores críticos como el petrolero, es un aspecto fundamental que requiere una atención meticulosa tanto en la planificación como en la ejecución. Estas paradas, ya sean programadas o no programadas, incurren en costos significativos, pero son esenciales para la operatividad segura y eficiente de las instalaciones.
A continuación, exploramos en detalle el impacto económico de ambas y por qué, a pesar de sus costos, son cruciales para la industria.
Impacto de las paradas no programadas
Son típicamente resultado de fallos imprevistos o accidentes y representan un riesgo económico considerable para cualquier operación industrial. Los costos asociados con estas interrupciones son múltiples y pueden ser exorbitantes:
- Pérdida de producción: Cuando una planta detiene su producción inesperadamente, cada hora de inactividad significa una pérdida directa de ingresos. En la industria petrolera, donde la producción puede valorarse en millones por día, estas pérdidas se acumulan rápidamente. Se estima que el sector de petróleo y gas enfrenta alrededor de 27 paradas no programadas al año, y cada incidente puede costar entre $10 millones y $50 millones en pérdidas directas e indirectas.
- Costos operativos adicionales: Las reparaciones de emergencia generalmente son más costosas que los mantenimientos programados debido a la necesidad de respuesta rápida. Esto puede incluir costos de mano de obra de emergencia, piezas de repuesto a precios Premium y, en algunos casos, multas por incumplimiento de regulaciones ambientales o de seguridad. Una encuesta de líderes en la industria reveló que el 70% de las plantas no tienen un plan efectivo para responder rápidamente a una parada no programada, lo que agrava el costo y la duración del tiempo de inactividad.
- Impacto a largo plazo: Los fallas que causan estas paradas pueden también tener repercusiones a largo plazo en la maquinaria, reduciendo su vida útil o comprometiendo su eficiencia futura, lo que lleva a más gastos en mantenimientos y posibles nuevas interrupciones.
Las nuevas tecnologías, como el análisis predictivo y el mantenimiento basado en la condición, están comenzando a utilizarse para anticipar fallos antes de que ocurran y, por lo tanto, reducir la frecuencia de estas paradas.
Impacto de las paradas programadas
Las paradas programadas, aunque también costosas, son inversiones calculadas que tienen como objetivo prevenir los incidentes costosos y disruptivos que pueden resultar de negligencias en el mantenimiento.
Los costos y beneficios incluyen:
Inversión en mantenimiento y mejoras: Las paradas programadas requieren inversión en recursos humanos y materiales para llevar a cabo mantenimientos, actualizaciones y reparaciones planeadas. Estos costos son significativos pero necesarios para la optimización de la planta.
Prevención de problemas mayores: El costo de no realizar paradas programadas puede ser devastador. Fallas catastróficas en equipos críticos no solo son más costosos de reparar, sino que también pueden resultar en accidentes, lesiones o daños ambientales severos, llevando a responsabilidades legales y daños a la reputación de la empresa. Las plantas que implementan gestión de mantenimiento preventivo rigurosos experimentan hasta un 30% menos interrupciones en sus operaciones en comparación con aquellas que reaccionan sólo a fallas.
Beneficios a largo plazo: Aunque el inicio de una parada de planta requiere una inversión considerable, las mejoras implementadas y la prevención de averías contribuyen a un mejor funcionamiento de los equipos y a una mayor eficiencia en los procesos. Esto se traduce en una reducción de los costos operativos y en un aumento sostenido de la producción a lo largo del tiempo. A continuación se detallan algunos de estos beneficios:
- Mejora de la eficiencia operativa: Una de las ventajas más significativas de las paradas programadas es la oportunidad de mejorar la eficiencia operativa de la planta. Durante estas paradas, se pueden realizar ajustes y mejoras en los equipos y sistemas que no serían posibles durante las operaciones normales. Esto incluye la calibración de instrumentos, la actualización de sistemas de software, y la instalación de nuevas tecnologías más eficientes. La siguiente imagen muestra el mantenimiento o sustitución del aislamiento térmico de las tuberías e intercambiadores de calor, mejorando la eficiencia de estos equipos en la transferencia de calor mediante la realización de una parada de planta.
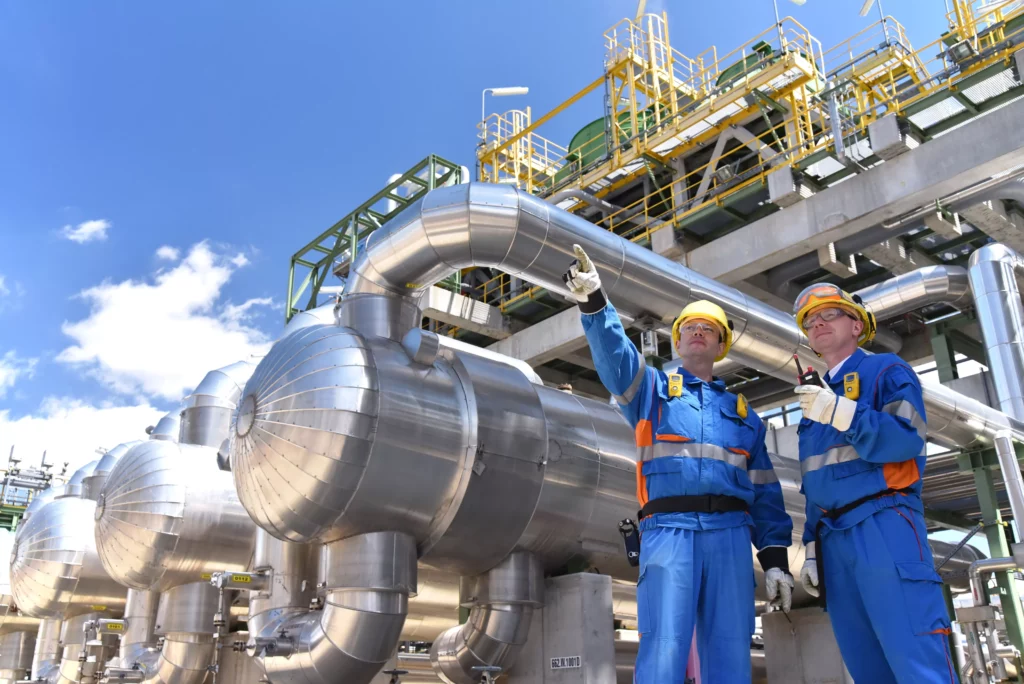
- Prolongación de la vida útil del equipo: El mantenimiento regular y las reparaciones programadas durante las paradas de planta ayudan a prolongar la vida útil de los equipos críticos. La revisión y reparación de componentes clave previenen el deterioro acelerado que puede resultar de operar continuamente sin mantenimiento adecuado. Esto no solo ayuda a evitar costosas sustituciones de equipos, sino que también asegura que la planta pueda operar a plena capacidad sin riesgo de fallos imprevistos.
- Reducción de las paradas no programadas: Al identificar y abordar proactivamente los problemas potenciales durante una parada programada, se puede reducir significativamente la incidencia de estas paradas, que son mucho más disruptivas y costosas. El mantenimiento preventivo y las inspecciones detalladas permiten a los técnicos detectar señales tempranas de desgaste o falla, que pueden ser rectificadas antes de que se conviertan en problemas mayores. Esta proactividad en el mantenimiento reduce el tiempo de inactividad no planeado y mejora la confiabilidad general de la planta.
- Mayor rentabilidad a largo plazo: Aunque las paradas programadas requieren una inversión inicial en términos de tiempo y recursos, los beneficios a largo plazo en la rentabilidad son claros. Con equipos que funcionan de manera más eficiente y confiable, y con menos interrupciones imprevistas, la planta puede maximizar su producción. Además, al reducir la frecuencia y severidad de las paradas no programadas, se ahorran costos significativos asociados con reparaciones de emergencia y pérdidas de producción. La estabilidad operativa aumentada también permite planificar mejor y optimizar las operaciones, contribuyendo a un flujo de ingresos más predecible y robusto.
Estrategias para minimizar el impacto económico de las paradas de planta en la industria petrolera
La relevancia de la dirección de proyectos de paradas de planta y programas de mantenimiento en la industria petrolera no puede ser subestimada. Estos eventos planificados son esenciales para mantener la funcionalidad, seguridad y eficiencia de las instalaciones, y tienen un impacto directo en la rentabilidad y sostenibilidad económica a largo plazo de las empresas.
Dirección eficaz de proyectos de paradas de planta
- Planificación estratégica: Estos planes deben deben estar alineados a las necesidades operativas inmediatas con las estrategias a largo plazo, utilizando herramientas como el software Primavera P6 o el método CPM para optimizar los tiempos y recursos.
- Coordinación y ejecución: La planificacio efectiva durante la ejecución de una parada de planta es crucial. Esto implica gestionar equipos multidisciplinarios, asegurar la disponibilidad de materiales y herramientas, y cumplir con los cronogramas establecidos. La comunicación continua entre todos los niveles de la organización ayuda a anticipar problemas y ajustar los planes en tiempo real.
- Evaluación y mejora continua: Después de cada parada de planta, se debe realizar una evaluación exhaustiva para identificar áreas de mejora. Este análisis ayuda a perfeccionar los procesos futuros, maximizar la eficiencia y reducir los costos. Las lecciones aprendidas son vitales para la mejora continua, permitiendo que la empresa se adapte mejor a las cambiantes condiciones del mercado y tecnológicas.
Programas de mantenimiento efectivos
- Los programas preventivo y predictivo bien diseñados pueden ayudar a reducir la frecuencia y la duración de las paradas de planta no planificadas.
- Estos programas pueden ayudar a extender la vida útil de los activos y reducir los costos de mantenimiento a largo plazo.
- Empresas como ExxonMobil y Petrobras han implementado con éxito programas de mantenimiento que han resultado en una reducción significativa del tiempo de inactividad y en mejoras en la eficiencia operativa.
Al implementar estrategias efectivas de dirección de proyectos de paradas de planta y programas de mantenimiento, las empresas petroleras pueden minimizar el impacto económico de las paradas de planta, mejorar la eficiencia operativa y aumentar la rentabilidad a largo plazo
Conclusión
Las paradas de planta en la industria petrolera son una herramienta doble filo: esenciales para el mantenimiento y la seguridad, pero costosas y disruptivas. Su gestión efectiva no solo es una cuestión de mantenimiento, sino una estrategia económica compleja que debe ser manejada con habilidad y previsión. Al planificar adecuadamente y ejecutar eficientemente estas paradas, las empresas no solo protegen su infraestructura y personal, sino que maximizan su eficiencia económica y operativa.
El manejo adecuado de las paradas de planta tiene un impacto directo en la rentabilidad a largo plazo. Al maximizar la eficiencia operativa y reducir las interrupciones, las empresas pueden mejorar su flujo de ingresos y su posición en el mercado.
La dirección de proyectos de paradas de planta y programas de mantenimiento bien diseñados son fundamentales. Incluyen planificación estratégica, coordinación eficaz durante la ejecución y evaluación post-parada para mejora continua. El uso de tecnologías avanzadas como el análisis predictivo y el mantenimiento basado en la condición también puede reducir la frecuencia de paradas no programadas.
¡Descubre cómo optimizar las paradas de planta hoy!
Referencias
Fuente propia