Tabla de Contenidos
- ¿Qué es la confiabilidad operacional en mantenimiento?
- Beneficios de la confiabilidad operacional en mantenimiento
- Estrategias de mantenimiento efectivas para las mejoras de la confiabilidad operacional
- ¿Cómo hacer un plan de mantenimiento centrado en la confiabilidad?
- Gestión de mantenimiento efectiva
- Gestión de Mantenimiento Asistido por Computadora (CMMS)
- Conclusión
- Referencias
En el ámbito empresarial contemporáneo, particularmente en el sector energético industrial, las mejoras de la confiabilidad operacional surgen como un pilar fundamental para asegurar la eficiencia, la seguridad y competitividad. Esta confiabilidad se alcanza a través de estrategias de mantenimiento efectivas que no solo evitan fallos imprevistos, sino que también optimizan los recursos y extienden la vida útil de los equipos.
Este artículo se enfoca en el concepto de mejoras de la confiabilidad operacional, utilizando las estrategias de mantenimiento más efectivas, haciendo uso de las mejores prácticas de mantenimiento industrial y tecnologías disponibles.
¿Qué es la confiabilidad operacional en mantenimiento?
Es la capacidad de una organización para desempeñar sus funciones de forma óptima en un lapso y bajo un entorno operacional específico. Se trata de la probabilidad de que los equipos, procesos y sistemas funcionen correctamente durante un periodo de tiempo determinado.
La confiabilidad operacional en mantenimiento define la probabilidad de que un sistema o componente ejecute sus funciones requeridas, bajo condiciones específicas, por un periodo determinado. En mantenimiento, esto implica asegurar que las máquinas y sistemas estén siempre listos, operen eficientemente y sin fallos inesperados durante el ciclo de producción. A continuación se presentan los objetivos principales de la Confiabilidad Operacional en Mantenimiento:
- Minimizar el tiempo de inactividad de los equipos y procesos.
- Reducir los costos de mantenimiento y reparación.
- Aumentar la productividad y la eficiencia.
- Mejorar la seguridad en el trabajo.
Para lograr efectivas mejoras de la confiabilidad operacional, es necesario:
- Implementar estrategias de gestión de mantenimiento efectivas: Mantenimiento preventivo, predictivo, centrado en la confiabilidad, etc.
- Contar con una cultura de seguridad y prevención: Capacitación del personal, identificación de riesgos, implementación de medidas de control.
- Utilizar herramientas y tecnologías adecuadas: Software de mantenimiento, monitoreo de condición, análisis de datos, gestión de mantenimiento asistido por computadora.
- Gestionar los riesgos de forma eficaz: Análisis de riesgos, planes de contingencia, gestión de cambios.
Beneficios de la confiabilidad operacional en mantenimiento
- Rentabilidad: Reducción de costos, aumento de la productividad.
- Seguridad: Menor riesgo de accidentes.
- Satisfacción del cliente: Mayor disponibilidad de productos y servicios.
- Mejor la imagen de la empresa: Mayor confianza de los clientes e inversores.
Estrategias de mantenimiento efectivas para las mejoras de la confiabilidad operacional
Para obtener mejoras en la confiabilidad operacional en las industrias, es fundamental implementar en mantenimiento estrategias de gestiones efectivas. Estas estrategias no solo buscan prevenir fallas y reducir tiempos de inactividad, sino también optimizar el rendimiento de los equipos y prolongar su vida útil. A continuación, se presentan algunas de las estrategias efectivas:
Mantenimiento Preventivo (MP)
- Descripción: Implica realizar intervenciones de gestión de mantenimiento planificadas basadas en horarios establecidos o condiciones operativas predeterminadas, con el objetivo de prevenir fallos antes de que ocurran.
- Ventajas: Reduce el tiempo de inactividad, prolonga la vida útil del equipo, minimiza los costos de reparación, mejora la seguridad.
- Desventajas: Puede resultar costoso si se realizan tareas innecesarias, no siempre es efectivo para prevenir todos los fallos, requiere un plan de mantenimiento bien definido.
- Ejemplo: Cambiar el aceite de un motor cada 5,000 kilómetros, realizar inspecciones periódicas de maquinaria industrial.
- Efectividad: Reducción del tiempo de inactividad hasta un 30%, reducción de los costos de mantenimiento hasta un 15%, aumento de la vida útil del equipo hasta un 20%.
El Mantenimiento Preventivo (PM) destaca como una estrategia esencial y efectiva para la mayoría de los equipos industriales. La clave radica en un plan flexible y adaptable a las condiciones operativas cambiantes. El éxito de esta herramienta se basa en la ejecución precisa de tareas programadas, garantizando la confiabilidad y eficiencia del equipo a lo largo del tiempo.
Mantenimiento Predictivo (PdM)
- Descripción: El software de gestión de mantenimiento computarizado (CMMS) se basa en el monitoreo del estado del equipo para determinar cuándo se necesita mantenimiento. Utiliza tecnologías de monitoreo en tiempo real y herramientas de diagnóstico para predecir posibles fallos en el equipo. Esto incluye análisis de vibraciones, termografía, análisis de aceite y otros. Se basa en monitorear la condición del equipo para determinar cuándo se necesita mantenimiento.
- Ventajas: Minimiza el tiempo de inactividad, optimiza el mantenimiento, mejora la confiabilidad, aumenta la seguridad.
- Desventajas: Requiere una inversión inicial en tecnología de monitoreo, necesita personal capacitado para usar la tecnología e interpretar los datos, desarrollar un proceso de gestión de datos puede ser complejo, la integración con sistemas de gestión existentes puede ser desafiante.
- Ejemplo: Monitoreo de vibraciones del motor para detectar desgaste del rodamiento: Análisis de aceite para detectar contaminación del aceite y desgaste de componentes. Análisis de vibraciones con equipos de medición. A continuación, se muestra una imagen representativa del monitoreo de vibraciones utilizando un sensor.
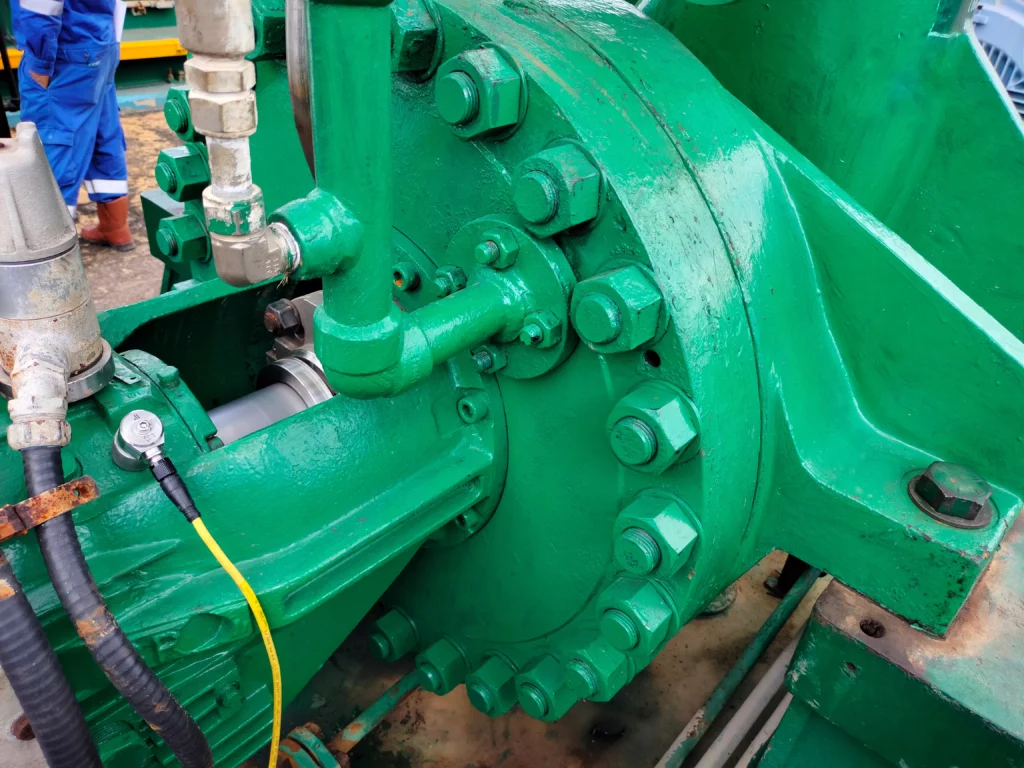
- Efectividad: Reducción del tiempo de inactividad hasta en un 40%, reducción de los costos de mantenimiento hasta en un 25%, aumento de la confiabilidad hasta en un 50%.
El Mantenimiento Predictivo (PdM) es óptimo para equipos críticos, costosos o con alta tasa de fallos. Su implementación exige una inversión inicial y un compromiso sostenido. En el sector energético, industrial y afines, el PdM se destaca como una herramienta poderosa para alcanzar la excelencia operacional.
Mantenimiento Centrado en Confiabilidad (RCM)
- Descripción: El Mantenimiento Basado en la Confiabilidad (RCM) es una estrategia de mantenimiento que se basa en un análisis exhaustivo de los equipos para determinar las fallas más críticas y determinar las estrategias de mantenimiento más efectivas. Este enfoque se centra en comprender y gestionar los modos de falla de los equipos críticos para mejorar la confiabilidad operacional. Implica la evaluación de las funciones de los equipos, la identificación de los modos de falla, y la implementación de estrategias de mantenimiento específicas para cada tipo de falla.
- Ventajas: Maximiza la confiabilidad, reduce costos, mejora la seguridad, optimiza la gestión de activos.
- Desventajas: Requiere un análisis complejo y detallado, necesita personal altamente capacitado, el éxito del RCM depende de la calidad de los datos, el RCM puede ser inflexible.
- Ejemplo: Implementar un programa RCM para una flota de aviones, analizar las causas de falla de un equipo crítico para determinar las mejores estrategias de mantenimiento.
- Efectividad: Reducción del tiempo de inactividad hasta en un 50%, reducción de los costos de mantenimiento hasta en un 30%, aumento de la confiabilidad hasta en un 60%.
El Mantenimiento Centrado en la Confiabilidad (RCM) es la clave para empresas con equipos críticos, el RCM garantiza la excelencia operacional al optimizar el mantenimiento y la confiabilidad de los equipos.
¿Cómo hacer un plan de mantenimiento centrado en la confiabilidad?
- Definir los objetivos: Establecer los objetivos específicos del plan de mantenimiento, como la reducción del tiempo de inactividad, la mejora de la seguridad o la disminución de los costos.
- Identificar los equipos críticos: Analizar los equipos y determinar cuáles son críticos para la operación. Se debe considerar la frecuencia de fallas, el impacto en la producción y el costo de reparación
- Analizar los modos de falla: Identificar las fallas más comunes de los equipos críticos y determinar las causas raíz.
- Desarrollar estrategias de mantenimiento: Seleccionar las estrategias de mantenimiento más adecuadas para cada equipo crítico, como mantenimiento preventivo, predictivo o RCM.
- Implementar el plan de mantenimiento: Establecer un plan de acción para la implementación del plan de mantenimiento, incluyendo la asignación de responsabilidades, recursos y presupuesto.
- Monitorear y evaluar el plan: Medir y evaluar el desempeño del plan de mantenimiento y realizar ajustes cuando sea necesario.
Gestión de mantenimiento efectiva
Constituye el primer paso hacia el fortalecimiento de la confiabilidad operacional, implicando una planificación, programación y ejecución de actividades de mantenimiento dirijidas a minimizar interrupciones y maximicen la vida útil de los equipos. La adopción de mejores prácticas de mantenimiento industrial es fundamental en la deficnicion de metodologías específicas para cada equipo o sistema.
Gestión de Mantenimiento Asistido por Computadora (CMMS)
El Sistema de Gestión de Mantenimiento Asistido por Computadora (CMMS) proporciona una serie de beneficios clave:
- Programación de mantenimiento: A través de uso se logra planificar y programar las actividades de mantenimiento de manera eficiente, asegurando que se realicen en el momento oportuno para evitar interrupciones no planificadas en la producción.
- Gestión de activos: Facilita el seguimiento y la gestión de todos los activos de la empresa, incluidos equipos, maquinaria e instalaciones, lo que ayuda a optimizar su rendimiento y prolongar su vida útil.
- Registro de historial de mantenimiento: Se puede llevar un registro detallado de todas las actividades de mantenimiento realizadas en cada equipo, lo que facilita el análisis de tendencias, la identificación de problemas recurrentes y la toma de decisiones informadas.
- Control de inventario y compras: Ayuda a gestionar el inventario de piezas de repuesto y materiales necesarios para el mantenimiento, optimizando los niveles de stock y facilitando la realización de pedidos de manera oportuna.
- Seguimiento de costos: Mediante el uso de este software se puede realizar un seguimiento preciso de los costos asociados con el mantenimiento de activos, lo que ayuda a identificar áreas de mejora y a optimizar el presupuesto de mantenimiento.
- Cumplimiento normativo: Regula el cumplimiento de los requisitos reglamentarios y normativos relacionados con el mantenimiento de activos, al proporcionar documentación y registros precisos de las actividades realizadas.
En general, un CMMS ayuda a mejorar la eficiencia, la confiabilidad y la rentabilidad de las operaciones de mantenimiento al proporcionar una plataforma centralizada para la gestión y el seguimiento de todas las actividades relacionadas con el mantenimiento de activos.
Conclusión
La confiabilidad operacional y la adopción de estrategias de mantenimiento eficaces, junto con tecnologías avanzadas, no solo mejora la competitividad y fortalecen la confianza en el mercado, sino que también garantizan operaciones seguras y rentables. Estas mejoras representan una inversión inteligente hacia la sostenibilidad y el éxito a largo plazo del sector empresarial.
«Impulsa tu eficiencia ahora»
Referencias
Fuente propia