Tabla de Contenidos
- Introducción
- Fundamentos de Fitness For Service (FFS)
- Normativas y Estándares API 579-1 y ASME FFS-1clave en FFS
- Metodologías de evaluación en FFS
- Implementación de FFS en Activos Petroleros
- Beneficios de implementar FFS
- Desafíos y soluciones en la implementación de FFS
- Futuro de FFS en la industria del petróleo y gas
- Innovaciones tecnológicas
Introducción
En la industria del petróleo y gas, la seguridad y eficiencia operativa son prioridades fundamentales. El concepto de «Fitness For Service» (FFS) se refiere a la evaluación de la capacidad operativa de los equipos y componentes industriales bajo condiciones específicas, asegurando que puedan operar de manera segura y efectiva a lo largo de su vida útil. La Gestión de Integridad de Activos (AIM) complementa este enfoque al monitorear y mantener la condición de los activos, garantizando su rendimiento óptimo y minimizando riesgos.
La relevancia de este artículo radica en la necesidad crítica de implementar estrategias FFS en el sector petrolero, donde los activos están expuestos a condiciones extremas y demandas operativas rigurosas. Entender y aplicar FFS no solo mejora la seguridad y confiabilidad de las operaciones, sino que también optimiza los costos y la eficiencia a largo plazo, proporcionando una ventaja competitiva en un mercado altamente regulado y competitivo.
Fundamentos de Fitness For Service (FFS)
Fitness for service (FFS) es un proceso de evaluación técnica que determina si un equipo o componente industrial puede continuar en servicio bajo condiciones operativas específicas sin comprometer la seguridad. Los principales objetivos de FFS incluyen la identificación de defectos y daños, la evaluación de su impacto en la integridad estructural, y la recomendación de acciones correctivas o de mitigación para asegurar la operatividad segura del equipo.
El concepto de FFS ha evolucionado significativamente desde su introducción en la industria. Inicialmente, se centraba en la evaluación de daños visibles y superficiales. Con el tiempo, se han desarrollado normas y metodologías más sofisticadas, como el API 579-1/ASME FFS-1, proporciona un marco integral para la evaluación de defectos y daños en equipos presurizados. Este estándar incorpora avances en tecnología de materiales, técnicas de inspección no destructiva (NDT) y análisis de tensiones, permitiendo evaluaciones más precisas y detalladas.
En el siguiente video se resumen aspectos esenciales de la metodología FFS mediante API 579-1 y ASME FFS-1, para la comprensión de los principios que garantizan la seguridad y eficiencia de equipos y estructuras. Fuente:
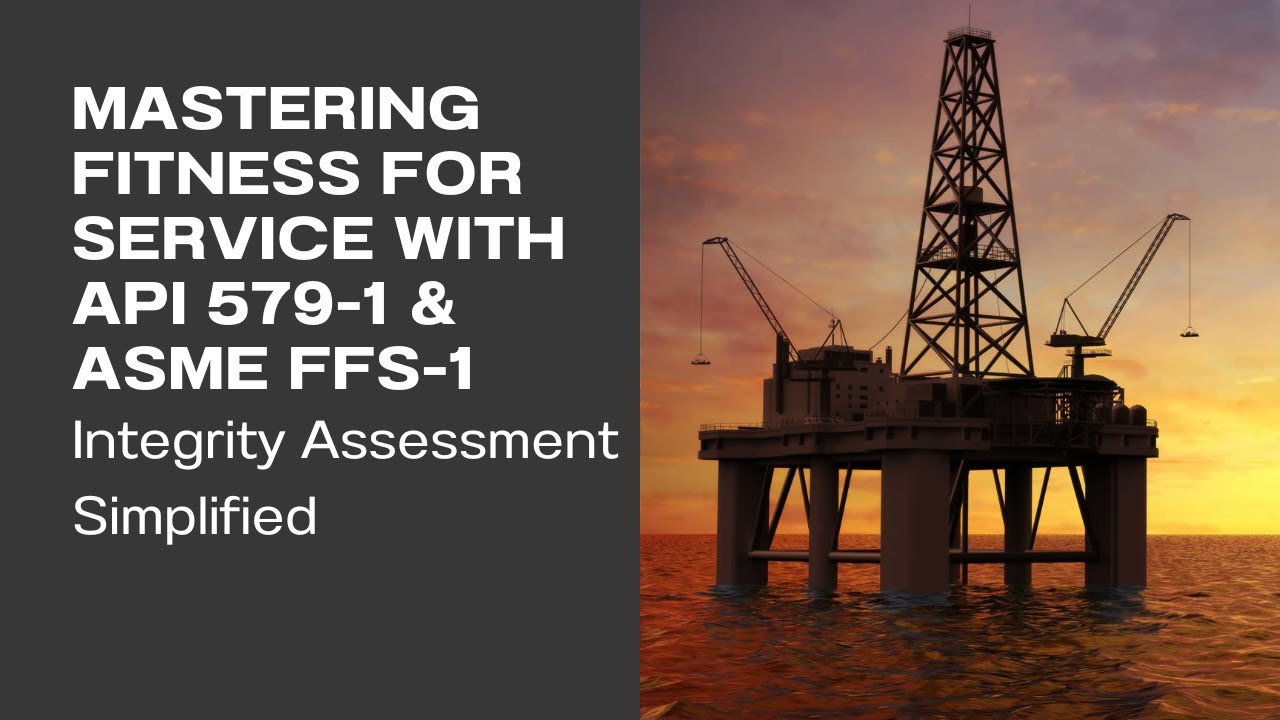
Control de Fitness For Service con API 579-1 y ASME FFS-1.
La evolución de FFS refleja la creciente complejidad de los equipos industriales y la necesidad de métodos de evaluación más rigurosos y precisos. Hoy en día, FFS es una disciplina esencial en la gestión de integridad de activos, ayudando a las empresas a maximizar la vida útil de sus activos, mejorar la seguridad operativa y cumplir con regulaciones cada vez más estrictas en la industria del petróleo y gas.
Normativas y Estándares API 579-1 y ASME FFS-1clave en FFS
El estándar API 579-1/ASME FFS-1, desarrollado conjuntamente por el American Petroleum Institute (API) y la American Society of Mechanical Engineers (ASME), es una guía comprensiva para la evaluación de la integridad estructural y operativa de equipos presurizados. Este estándar se aplica a una variedad de situaciones, incluyendo corrosión, grietas, deformaciones y otros tipos de daño en componentes como recipientes a presión, tuberías y tanques de almacenamiento. La norma está dividida en múltiples niveles de evaluación, permitiendo a los ingenieros realizar análisis cualitativos y cuantitativos, desde evaluaciones básicas hasta análisis avanzados utilizando métodos de elementos finitos.
Mientras que API 579-1/ASME FFS-1 es ampliamente utilizado en América del Norte, existen otros estándares internacionales que también regulan la evaluación de Fitness For Service. Por ejemplo, la norma BS 7910 del British Standards Institution (BSI) en el Reino Unido proporciona directrices para la evaluación de la integridad estructural de estructuras metálicas con defectos. Así mismo, el estándar europeo EN 13445-4 incluye procedimientos para la evaluación de equipos a presión. Aunque estos estándares comparten objetivos similares con API 579-1/ASME FFS-1, existen diferencias en los enfoques metodológicos y los requisitos específicos de cada uno. API 579-1/ASME FFS-1 es conocido por su enfoque detallado y estructurado, mientras que otros estándares pueden ofrecer más flexibilidad en ciertos aspectos de la evaluación.
Metodologías de evaluación en FFS
En el ámbito de Fitness For Service, se emplean diversas metodologías para evaluar la integridad de los equipos. Los métodos más comunes incluyen:
- Análisis de tensiones: Este método evalúa la capacidad de un componente para soportar cargas operativas sin fallar. Utiliza modelos matemáticos y simulaciones para determinar las tensiones internas y externas que afectan la estructura.
- Evaluación de corrosión: Implica la inspección y cuantificación del daño causado por la corrosión. Se utilizan técnicas como la ultrasonografía y la inspección visual para identificar áreas afectadas y medir el espesor residual del material.
- Análisis de fatiga: Este método examina la capacidad del material para resistir cargas cíclicas repetidas. Se enfoca en la propagación de grietas y la vida útil del componente bajo condiciones de operación fluctuantes.
Las evaluaciones de FFS se apoyan en tecnologías avanzadas y herramientas especializadas:
- Software de simulación: Herramientas como ANSYS y ABAQUS permiten realizar análisis detallados de elementos finitos, simulando el comportamiento de los materiales bajo diversas condiciones de carga y daño.
- Técnicas de Ensayos No Destructiva (NDT): Métodos como la ultrasonografía, radiografía, inspección por partículas magnéticas y corrientes de Eddy son esenciales para detectar y evaluar defectos internos y superficiales sin dañar el equipo. Estas técnicas proporcionan datos precisos sobre la integridad del material, facilitando decisiones informadas sobre la idoneidad para el servicio.
La integración de estas metodologías y tecnologías en un programa de FFS robusto permite a los ingenieros garantizar la seguridad y eficiencia operativa de los activos en la industria del petróleo y gas, optimizando tanto el rendimiento como la vida útil de los componentes críticos.
Implementación de FFS en Activos Petroleros
La implementación de FFSen activos petroleros es un proceso estructurado y meticuloso que involucra varios pasos clave:
Evaluación Inicial
- Identificación de los activos críticos y evaluación preliminar de sus condiciones actuales.
- Recolección de datos históricos de operación, mantenimiento y fallos.
Inspección y recolección de datos
- Uso de técnicas de inspección no destructiva (NDT) como ultrasonidos, radiografía, y corrientes de Eddy para recolectar datos precisos sobre el estado de los activos.
- Evaluación de la integridad estructural a través de mediciones detalladas.
Análisis y evaluación
- Aplicación de modelos de análisis de tensiones, corrosión y fatiga utilizando software avanzado como ANSYS o ABAQUS.
- Determinación de la capacidad residual del activo para continuar en servicio bajo las condiciones operativas actuales.
Desarrollo de estrategias de mitigación
- Definición de acciones correctivas y preventivas para mitigar riesgos identificados.
- Planificación de reparaciones, reemplazos o modificaciones necesarias.
Integración con sistemas existentes
- Integración de los resultados de FFS con sistemas de gestión de integridad de activos (AIM) y programas de mantenimiento predictivo.
- Actualización de bases de datos y sistemas de gestión de activos para reflejar las evaluaciones FFS.
Estudios de caso y ejemplos prácticos
Un ejemplo destacado de implementación exitosa de FFS es en la gestión de tuberías submarinas de una plataforma petrolera en el Mar del Norte. Se utilizó una combinación de inspección visual remota y ultrasonidos para evaluar la integridad de las tuberías que mostraban signos de corrosión. Mediante el análisis detallado de los datos recolectados, se identificaron segmentos críticos que requerían atención inmediata. La aplicación de FFS permitió priorizar las reparaciones, evitando así un posible fallo catastrófico y optimizando los recursos destinados al mantenimiento.
Otro caso relevante es el de una refinería en el Golfo de México, donde la implementación de FFS en los reactores de hidroprocesamiento ayudó a identificar grietas incipientes causadas por la fatiga térmica. Esto permitió la planificación de intervenciones durante paradas programadas, evitando costosos tiempos de inactividad no planificados.
Beneficios de implementar FFS
La implementación de FFS mejora significativamente la seguridad operativa al identificar y mitigar riesgos antes de que se conviertan en fallos críticos. Al detectar problemas estructurales en etapas tempranas, se pueden tomar acciones preventivas, reduciendo la probabilidad de accidentes y protegiendo a los trabajadores y el medio ambiente.
FFS permite una gestión más eficiente de los recursos destinados al mantenimiento. Al enfocarse en la integridad real de los activos, se pueden priorizar reparaciones y reemplazos basados en datos precisos, evitando gastos innecesarios en componentes que aún tienen una vida útil considerable. Esto resulta en una reducción de los costos operativos a largo plazo.
La aplicación de FFS asegura que los activos operen en condiciones óptimas, aumentando la eficiencia y confiabilidad de las operaciones. La identificación y corrección de defectos antes de que causen interrupciones permite mantener la producción constante, minimizando los tiempos de inactividad no planificados. Además, la mejora en la confiabilidad de los equipos incrementa la confianza en las operaciones, favoreciendo la planificación y ejecución de proyectos a gran escala.
La implementación de FFS no solo mejora la seguridad y eficiencia operativa, sino que también optimiza el uso de recursos y asegura la continuidad de las operaciones, proporcionando un valor significativo para las empresas del sector petróleo y gas.
Desafíos y soluciones en la implementación de FFS
Principales desafíos
1. Tecnológicos
- La implementación de FFS requiere tecnología avanzada de inspección y análisis, que puede ser costosa y difícil de integrar en sistemas existentes.
- La precisión y confiabilidad de las técnicas de inspección no destructiva (NDT) pueden variar, lo que afecta la calidad de los datos obtenidos para las evaluaciones FFS.
2. Operativos
- La interrupción de operaciones para realizar inspecciones puede ser costosa y puede impactar la producción.
- La integración de los resultados de FFS en las operaciones diarias requiere una coordinación eficiente entre diferentes departamentos.
3. Organizativos
- La resistencia al cambio dentro de las organizaciones puede dificultar la adopción de nuevas metodologías y tecnologías.
- La falta de personal capacitado en técnicas FFS y en el uso de herramientas avanzadas puede ser un obstáculo significativo.

Soluciones y mejores prácticas
1. Estrategias
- Integración Gradual: Implementar FFS de manera gradual, comenzando con activos críticos y expandiéndose a otros equipos con el tiempo.
- Automatización: Utilizar herramientas de software para automatizar el análisis de datos y facilitar la integración con sistemas de gestión de integridad de activos.
2. Capacitación
- Programas de Formación: Desarrollar programas de capacitación especializados para ingenieros y técnicos en técnicas FFS y el uso de tecnologías NDT.
- Certificación: Fomentar la certificación profesional en normas y estándares relevantes, como API 579-1/ASME FFS-1, para asegurar el conocimiento y la competencia en la implementación de FFS.
Futuro de FFS en la industria del petróleo y gas
Tendencias emergentes
1. Inteligencia Artificial (IA)
- La IA está revolucionando la capacidad de analizar grandes volúmenes de datos de inspección, mejorando la precisión y eficiencia en la detección de defectos y predicción de fallos.
- Algoritmos de aprendizaje automático pueden identificar patrones y anomalías que los métodos tradicionales pueden pasar por alto.
2. Internet de las Cosas (IoT)
- Sensores conectados a IoT permiten el monitoreo continuo de la salud de los activos, proporcionando datos en tiempo real sobre su estado y rendimiento.
- La integración de IoT con sistemas FFS facilita la implementación de mantenimiento predictivo y proactivo, reduciendo el riesgo de fallos inesperados.
3. Digitalización
- La digitalización de registros y datos de inspección mejora la accesibilidad y el análisis de la información histórica, apoyando decisiones más informadas y rápidas.
- Plataformas digitales y gemelos digitales permiten la simulación y evaluación virtual de activos, optimizando la planificación y ejecución de estrategias de mantenimiento.
Innovaciones tecnológicas
1. Nuevas técnicas de inspección
- Tomografía Computarizada Industrial: Ofrece imágenes detalladas del interior de los componentes, permitiendo la detección precisa de defectos internos.
- Termografía Infrarroja: Identifica variaciones térmicas que pueden indicar problemas estructurales o de aislamiento.
2. Metodologías avanzadas
- Análisis de Elementos Finitos (FEA): Mejora la precisión en la evaluación de tensiones y deformaciones en componentes complejos.
- Modelado Predictivo: Utiliza datos históricos y algoritmos avanzados para predecir la vida útil restante de los activos y planificar intervenciones de mantenimiento de manera más efectiva.
La adopción de estas tendencias y tecnologías emergentes está transformando el campo de FFS, mejorando la seguridad, eficiencia y rentabilidad en la industria del petróleo y gas, y asegurando que los activos críticos puedan operar de manera confiable y segura a lo largo de su vida útil.
Conclusiones
La implementación de Fitness For Service (FFS) en la industria del petróleo y gas ofrece una amplia gama de beneficios críticos. Primero, mejora la seguridad operativa al permitir la detección temprana de defectos y fallos potenciales, reduciendo así el riesgo de accidentes y protegiendo tanto a los trabajadores como al medio ambiente. Segundo, optimiza los costos y el mantenimiento, permitiendo a las empresas priorizar las reparaciones y el reemplazo de componentes basados en datos precisos y detallados, evitando gastos innecesarios. Finalmente, aumenta la eficiencia y confiabilidad de las operaciones, asegurando que los activos funcionen en condiciones óptimas y minimizando los tiempos de inactividad no planificados.
La adopción de FFS no es solo una recomendación; es una necesidad imperativa para cualquier empresa que busque mantenerse competitiva y segura en el sector industrial. Invitamos a todos los profesionales y organizaciones en la industria del petróleo y gas a colaborar y compartir conocimientos en la implementación de FFS. Esta colaboración puede llevar a innovaciones más rápidas y eficaces, mejorando aún más la seguridad y eficiencia de nuestras operaciones.
No subestimes el poder de FFS en la transformación de tus operaciones industriales. Actúa ahora para integrar estas metodologías avanzadas en tu estrategia de gestión de activos.
Referencias
Fuente propia